In 120 Sekunden ist alles verschraubt
Automationszelle von MartinMechanic
Das komplette Gehäuse einer Pumpe verschraubt die neue Automationszelle MDG211556 von MartinMechanic in nur 120 Sekunden. Der Auftraggeber für die Anlage, die in das firmeneigene Netzwerk eingebunden ist, stammt aus der Elektroindustrie. 4.0-fähig kann die Wartung von jedem Ort aus direkt gestartet werden.
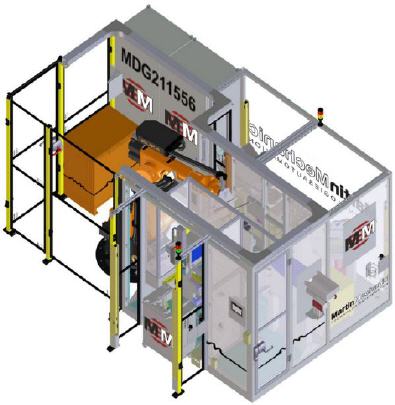
Dreh- und Angelpunkt für die Produktion ist der Kuka-Roboter KR30, der eine Reichweite von 2033 Millimeter hat und selbst bei einer Traglast von 30 Kilogramm nicht in die Knie geht. Er hält eine pneumatische Schraubspindel, die auf einem Zustellschlitten sitzt. Die 12 Schrauben, die er jeweils für die Verschraubung von Ober- und Unterseite des Gussgehäuses benötigt, werden ihm über einen Segmentförderer zugeführt und bereitgestellt. Der Roboter holt die Schrauben mit seinem Vakuumgreifer ab und dreht diese in das Gehäuse ein.
Zuvor legt der Werker die Gehäuseunterseite, den Dichtring und die Oberseite in den Einlegeplatz ein, auf dem sie fixiert und vorgespannt werden. Er scannt die Bauteile mit einem Handscanner ein. Die Steuerung erfasst die Teilenummern und überprüft, ob es sich um die zu montierende Variante handelt. Denn mit der Anlage können unterschiedliche Varianten bis zu einer Länge von 500 und einer Breite von 400 Millimeter verschraubt werden.
Der Sicherheitsbereich der Anlage ist durch eine Lichtschranke markiert. Erst wenn der Werker ihn verlassen hat, kann er manuell den Pendeltisch in Bewegung setzen. Dieser dreht sich um 180 Grad zum Roboter hin, der sofort seinen Auftrag ausführt. Mit der Schraube an seinem Greifer fährt der Roboter über das Gehäuse, um diese mit der Spindel einzudrehen. Der Vorgang wiederholt sich, bis sechs Schrauben mit einem Drehmoment von 30 Newtonmetern eingedreht und angezogen wurden. Der Pendeltisch verfügt über zwei zusätzliche Achsen. Dadurch wird es möglich, dass die Schrauben auch an der Stirnseite in einem Arbeitsgang eingedreht werden können. Die restlichen Schrauben werden an der Gehäuseunterseite festgezogen, wofür eine weitere Achse das Gehäuse um 180 Grad dreht.
In der Zeit, in der Ober- und Unterseite des Gehäuses bearbeitet werden, kann der Anlagenbediener schon die nächsten Gussteile einlegen. Bei Volllast wird die Automationszelle natürlich von zwei Werkern gleichzeitig bedient.
Der Pendeltisch dreht sich nun erneut und ein Querhub befördert das fertig montierte Bauteil auf den Entnahmeplatz, wo es wieder entspannt und aus der Fixation gelöst wird. Noch einmal wird es im Rahmen der Endkontrolle gescannt. Gehäuse ohne Beanstandung werden, da nach der Montage nun doppelt so schwer, direkt auf einen Transportwagen gezogen und zur nächsten Arbeitszelle befördert, wo weitere Montageschritte folgen.
Gehäuse, die nicht in Ordnung sind, werden mit einem roten Etikett versehen. Auf ihm ist das Fehlermerkmal ersichtlich, denn gegebenenfalls können die Gehäuse in einem zusätzlichen Arbeitsschritt manuell nachbearbeitet werden.
Neun Monate dauerten Entwicklungs- und Bauzeit der MDG211556, die mit der SPS-Steuerung S7-1500 von Siemens ausgerüstet ist. Das Touchpanel mit 19-Zoll-Bildschirm wurde fest angeordnet. Alle Prozessdaten werden in einer Datei erfasst und können jederzeit ausgegeben und ausgewertet werden. Dadurch lässt sich lückenlos dokumentieren, dass alle Produktionsvarianten ordnungsgemäß ausgeführt wurden.
Mehr Informationen zur Friedrich Martin GmbH:
![]() |
Friedrich Martin GmbH & Co KG |
![]() |
Hauptstrasse. 25 |
![]() |
72202 Nagold |
![]() |
Tel.: +49(0) 74 52-84 66-0 |
![]() |
Fax: +49(0) 74 52-84 66-5 66 |
![]() |
E-Mail: info@MartinMechanic.com |
![]() |
www.martinmechanic.com |
War dieser Artikel für Sie hilfreich?
![]() |
![]() |
![]() |
![]() |
![]() |
Bitte bewerten Sie diese Seite durch Klick auf die Symbole.
Zugriffe heute: 1 - gesamt: 1968.