Pfleghar: Eine starke Kombination
High-Speed-Fräsmaschine mit FCS-NP-Spannsystem
Geld wird nur verdient, wenn Späne fliegen. Kaum eine Branche weiß dies besser, als mittelständische Modellbaubetriebe. Dort gilt es, anspruchsvolle Fräsarbeiten in bester Qualität in kürzester Zeit fertigzustellen. Wohl dem, der wie die Helmut Pauser GmbH über ein innovatives Nullpunktspannsystem einen Weg gefunden hat, den Rüstaufwand weitgehend zu minimieren und dank moderner Maschinentechnik gleichzeitig die Bearbeitungszeiten zu reduzieren.
Es mag schon vielen Betrachtern bei den ersten ,Zusammentreffen‘ mit dem FCS Nullpunktspannsystem ähnlich ergangen sein, wie Helmut Pauser, Geschäftsführer der gleichnamigen GmbH. Er erinnert sich: „Als ich das System das erste Mal auf der Euromold gesehen habe, hätte ich mir nicht einmal im Traum vorstellen können, dass ich später einmal zu einem echten Fan des FCS-Systems werden könnte. Auf den ersten Blick war für mich kein echter Vorteil erkennbar.“ Das hat sich grundlegend geändert. Für den Geschäftsführer eines mittelständischen Modell- und Formenbau-Unternehmen gibt es für das FCS-Nullpunktspannsystem nur ein Prädikat: „Einfach clever.“
Doch einmal der Reihe nach. Vor rund 25 Jahren machte sich Helmut Pauser in der sprichwörtlichen Garage selbstständig. Dem Modellbaumeister gelang es relativ schnell, sich einen kleinen Kundenkreis zu erarbeiten, für den er auch Elektroden fräste. Schon in den Anfängen seiner Selbstständigkeit setzte er dabei Spannsysteme (die allerdings noch von Erowa) ein. Als sein ehemaliger Betrieb dann in eine Insolvenz schlitterte, übernahm er einen Teil der Belegschaft, mietete eine Halle und schon bald war vor allem im Umfeld Modellbau der Name Pauser kein unbekannter mehr.
Helmut Pauser: „In den Anfangsjahren dominierte der Modellbau bei weitem. Heute sind wir ganz klar in erster Linie ein Formenbauer mit einem kleinen Rest Modellbau. Wobei unsere Formen vorzugsweise nicht in den Volumenbereich gehen, sondern für den Kleinstserienbereich wie beispielsweise Lamborghini, Rolls Royce oder bestimmte Porsche-Modelle genutzt werden. Da bei den kleinen Stückzahlen keine exorbitanten Standzeiten nötig sind, arbeiten wir in aller Regel mit Aluminiumlegierungen. Wobei, um keine Missverständnisse aufkommen zu lassen, hier die absolut gleichen Qualitätsanforderungen einzuhalten sind, wie bei Formen für die Großserienfertigung.“
Wie gut das Unternehmen aus Straßdorf ist, lässt sich auch und vor allem daran ablesen, dass Helmut Pauser von den Anfangsjahren einmal abgesehen, nie aktiv Aufträge akquirieren musste, die Kunden kommen tatsächlich ,von alleine‘ zu ihm. Ein Großteil davon sind inzwischen sowieso Stammkunden und Neukunden kommen vor allem über Mund-zu-Mund-Propaganda zu ihm. Warum? Helmut Pauser: „Mit rund 20 hochqualifizierten Mitarbeitern, darunter sieben Konstrukteure allein für die Werkzeug-Konstruktion und die NC-Programmierung, und vier Großbearbeitungszentren sind wir so flexibel aufgestellt, dass wir sehr schnell auf Kundenanfragen reagieren können.“
Wobei die Konstrukteure von Guideline, einer zum Breyl-System zugehörigen Software unterstützt werden. Andreas Krieg, technischer Vertrieb beim FCS-Handelspartner Pfleghar erläutert: „Guideline ermöglicht bereits in der Konstruktionsphase mit realistischen Daten die Spannlagen zu simulieren. Die Software analysiert die 3D-Daten des Werkstücks und unterstützt den Konstrukteur beim Festlegen der Spannpunkte. Dabei wird ein Raster über das Bauteil gelegt und die Software schlägt darauf aufbauend die idealen Spannpunkte vor. Durch die Erstellung der Spannlage in der CAD/CAM-Abteilung wird der Maschinenstillstand deutlich verringert. “
Sein Kollege Kim Fleck, erklärt: „Das FCS-Nullpunktspannsystem Brey-Line beruht auf einem Baukastenprinzip, das aus Säulen, Ringen und Bolzen besteht. Gespannt wird auf Rasterplatten oder Paletten, die direkt auf dem Maschinentisch oder in Handling-Systemen installiert werden. Zentrierringe im Bauteil und der Rasterplatte übernehmen die Positionierung des Werkstücks.“ Andreas Krieg: „Wir sind ja nun nicht der einzige Anbieter von Nullpunktspannsystemen und ich sage ganz bewusst: Alle unsere Markbegleiter haben hervorragende Produkte. Aber alle arbeiten mit den beiden Komponenten Palette und Spanntöpfen und ich behaupte, es gibt außer FCS niemand, der etwas Vergleichbares wie Breyl-Line im Programm hat.
Die grundsätzlichen Vorteile des FCS-Systems, das eine Wiederholgenauigkeit von 4 µm erreicht, liegen vor allem in der hohen Stabilität, den Freiheitsgraden der Bearbeitung sowie in der Durchgängigkeit. Durch die erhöhte Position des Werkstücks ist eine echte 5-Seiten-Bearbeitung realisierbar. Es können kleine und große Werkstücke gespannt werden – auf Fräs-, Erodier-, Tiefbohr- und Messmaschinen. Die Aufspannung eignet sich sowohl für Schlicht- als auch für schwere Schruppbearbeitung. Zudem ermöglichen die permanenten Bezugspunkte im Bauteil, das Werkstück bei Bedarf abzuspannen und auf Paletten oder anderen Maschinen neu zu spannen, ohne das der Nullpunkt verloren geht.“
Kim Fleck ergänzt: „Ein weiterer Pluspunkt ist, dass die Spannposition auf dem Maschinentisch nahezu frei gewählt werden kann, um beispielsweise eine optimale Späneabfuhr sicherzustellen. Hinzu kommt, dass durch die Vielzahl der zur Verfügung stehenden Komponenten die Aufspannung aufgabenspezifisch aus dem Baukasten konfiguriert und auf jegliche zusätzliche konventionelle Spannmittel verzichtet werden kann. Gleichzeitig aber besteht die Möglichkeit, diese konventionellen Spannmittel mit einzubeziehen.“
Und wie sieht das in der Praxis aus? Helmut Pauser: „Ich bin ein Fan des FCS-Systems, denn ich kann ein beliebiges Teil räumlich nahezu unabhängig an jeder günstigen Position innerhalb des Bearbeitungsraumes einer Maschine spannen. Wir haben derzeit auf unseren vier Bearbeitungszentren rund zehntausend Bohrungen die wir für Spannaufgaben nutzen können. Wir können unsere Teile damit quasi wo immer wir wollen aufspannen. Das eröffnet für uns eine Flexibilität, die mit Spanntöpfen nie und nimmer erreichbar ist.“
Ausschlaggebend für den Kauf war ein Auftrag für ein Getriebegehäuse für ein Militärfahrzeug. Helmut Pauser: „Das Teil war mit normalen Vorrichtungen fast nicht zu spannen. Da habe ich mich an das FCS-System erinnert, denn auf den Messen waren immer die abenteuerlichsten Teile aufgespannt. Also haben uns eine Grundplatte und vier Spanner gekauft und siehe da, wir hatten absolut kein Problem mit dem Aufspannen. Es war für uns alle hier ein echtes Schlüsselerlebnis und seitdem haben wir uns ein reichhaltiges Sortiment mit unterschiedlichen Komponenten von FCS angeschafft und profitieren von den Pluspunkten.“
Andreas Krieg: „3.000 bis 4.000 Spindel-Stunden in der Einzelteilfertigung sind schon mehr als ordentlich, mit unserem System kann sich das um bis zu 50 Prozent nach oben bewegen.“ Helmut Pauser: „Wir haben noch keine belastbaren Zahlen vorliegen, aber wir gehen davon aus, dass wir durch den Einsatz der FCS-Elemente unsere Maschinenlaufzeiten vier- bis fünfhundert Stunden pro Jahr und Maschine gesteigert haben.“
Bei allen Vorteilen der FCS-Spannphilosophie, letzten Endes braucht es aber auf jeden Fall ein Maschinenkonzept, das diese Pluspunkte auch in handfeste Ergebnisse umsetzt. Helmut Pauser: „Auf der EMO vor sechs Jahren habe ich, ohne einen konkreten Bedarf im Hintergrund, alle bei einer anstehenden Investition in Frage kommenden Maschinen einmal genauer angeschaut. Schon damals sind uns die Bearbeitungszentren von Parpas positiv aufgefallen. Zum einen war die Zugänglichkeit besser geregelt als bei vielen Wettbewerbern und auch die Sicht in den Arbeitsraum war um einiges günstiger. Dazu kamen deutliche Vorteile bei den Dynamikwerten und bei der zur Verfügung stehenden Drehzahl. Vor allem aber überzeugte mich der stabile Maschinenbau.“
Christoph Klumpp, Geschäftsführer der Parpas Deutschland GmbH: „Schon bei den ersten Gesprächen mit Helmut Pauser wurde deutlich, dass wir mit der Shark genau die richtige Maschine für sein Anforderungsprofil im Portfolio haben. Auf Kundenwunsch mit einem Zwei-Achs direktangetriebenen Orthogonalkopf und Drehzahlen bis 18.000 1/min hochgerüstet, konnten wir Herrn Pauser fast so etwas wie seine Wunschmaschine offerieren.“ Dem muss auch so gewesen sein, denn Helmut Pauser bestellte gleich zwei absolut identische Maschinen. „Mit den beiden Sharks haben wir zum einen drei ältere Maschinen auf einen Schlag ersetzt und zum anderen bieten zwei baugleiche Maschinen interessante Möglichkeiten sowohl bei der Planung wie auch im Fertigungsalltag.“ Und: „Das ganze Maschinenkonzept ist wie auf die Belange des Modellbaus hin ausgerichtet. Das reicht hin bis zum 5-Achs-Ausweichfräsen, da der Kopf auch nach hinten schwenken kann.“
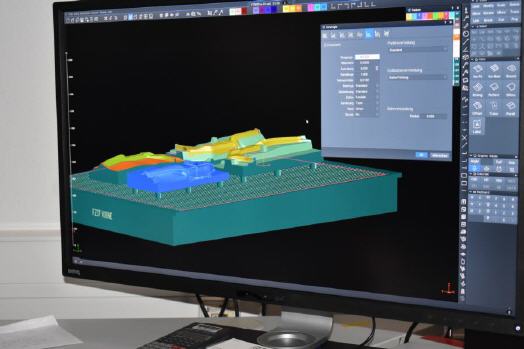
Simulation der Spannlage mit ›Guideline‹
Christoph Klumpp: „Die Shark ist eine High-Speed- Fräsmaschine in Starrbettbauweise. Die Maschine eignet sich für das Schruppen, das Vorschlichten und das Schlichten gleichermaßen. Möglich wurde das durch die konsequente Finite-Elemente-Methode, mit der sich eine Maschinenstruktur realisieren ließ, die allen auftretenden statischen, dynamischen und thermischen Beanspruchungen optimal entspricht. Dieses führt zu einer hohen Stabilität und einem hohen Eigen-Frequenzbereich, der durch die Bearbeitung nicht angeregt wird. Somit sind hervorragende dynamische Eigenschaften gegeben. Und last not least: Der symmetrische Aufbau des RAM-Kreuzschieber-Ständer ermöglicht eine optimale Kraftaufnahme und ein gleichmäßiges thermisches Wachstum. Hierdurch sind eine optimale Steifigkeit der Maschine und eine sehr hohe Genauigkeit im gesamten Verfahrbereich gegeben. Zudem werden durch Wärmesensoren die erwärmten Maschinenteile konstant thermisch vermessen, abhängig von der Umgebungstemperatur. Die nicht vermeidbare Materialausdehnung wird elektronisch kompensiert.“
Auch in Sachen Leistung macht die Shark ihrem Namen alle Ehre. Standardmäßig steht eine 22 kW Motorspindel mit einem Drehmoment von 400 Nm zur Verfügung. Kraft genug, um alle 30 Werkzeuge (wobei Magazinlösungen bis 500 Werkzeugplätze optional möglich sind) optimal anzusteuern.
Ein besonderes Highlight ist der Fräskopf in Orthogonal-Bauweise. Durch seine schlanke Form und die geringe Störkontur zwischen Spindelmitte und Außenkontur in einem Bereich von 180 Grad, ermöglicht er den Einsatz sehr kurzer Werkzeuge, was wiederum eine hohe Performance beim Fräsen ermöglicht und gleichzeitig die Werkzeugkosten stark reduziert. Zudem sind zahlreiche Features wie ein hydraulisch betätigter Gewichtsausgleich der Vertikalachse, die CNC gesteuerte Kompensation für die Wärmeausdehnung, ein Kühlmittelsystem mit einer Förderleistung von 25 l/min und einem Druck von 6 bar sowie optische direkte Messsysteme der Fa. Heidenhain bereits im Standard enthalten.
Für Helmut Pauser sind die beiden Parpas-Zentren jedenfalls die Arbeitspferde in der Produktion. Da kann es schon mal vorkommen, dass der Chef persönlich nach Schichtende oder am Wochenende noch einmal nachsieht, ob denn alles ,am Laufen‘ ist. Bislang haben ihn speziell die beiden Sharks hier noch nicht oft im Stich gelassen.
Trotzdem: „Wenn ich vier Maschinen und einen Auftragsbestand habe, der eine weitere Maschine nötig machen würde, kann ich jedem nur raten, erst einmal in ein FCS-Spannsystem zu investieren. Der Rüstanteil sinkt und die Spanzeiten nehmen zu und noch immer gilt ,Verdient wird nur wenn Späne fliegen.‘ Auf der anderen Seite ist es aber schon so, dass die ,richtige‘ Werkzeugmaschine letztendlich über den wirtschaftlichen Erfolg eines Modellbauers entscheidet. Am besten, man hat beides.“
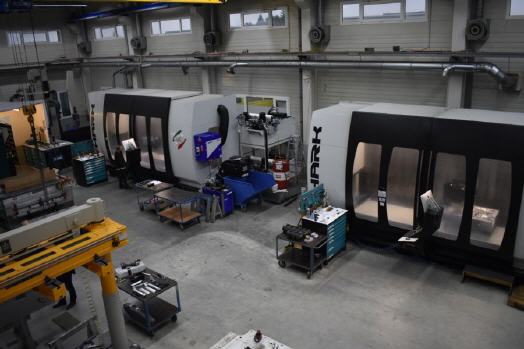
Zwei Sharks ersetzten fünf ältere Maschinen
Mehr Informationen zur Pfleghar GmbH & Co. KG:
![]() |
Pfleghar GmbH & Co. KG |
![]() |
Kartonstraße 2 |
![]() |
88255 Baienfurt |
![]() |
Tel.: +49 (0) 751 / 560 50-0 |
![]() |
Fax: +49 (0) 751 / 560 50-11 |
![]() |
E-Mail: info@pfleghar.de |
![]() |
www.pfleghar.de |
War dieser Artikel für Sie hilfreich?
![]() |
![]() |
![]() |
![]() |
![]() |
Bitte bewerten Sie diese Seite durch Klick auf die Symbole.
Zugriffe heute: 1 - gesamt: 2339.