Inovatools stellt Druckluftversorgung um
Werkzeughersteller senkt Energieverbrauch
Weil Luft teurer als Strom ist und dem Management die Umwelt am Herzen liegt, rüstet Inovatools die Druckluftversorgung in allen Werken weltweit um. Der Präzisionswerkzeughersteller setzt dabei auf die neuen drehzahlgeregelten Kompressoren der GA-VSD+-Baureihe von Atlas Copco. Allein mit dem jüngsten Kompressor in Kinding spart der Mittelständler 15.000 Euro im Jahr.
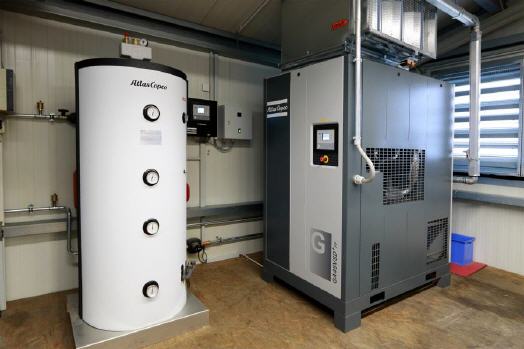
„Energie kostet nicht nur viel Geld, sondern verbraucht vor allem auch natürliche Ressourcen“, eröffnet Georg Eckerle das Gespräch. „Es ist unsere Verantwortung, damit sparsam umzugehen“, sagt der Geschäftsführer der Inovatools Eckerle & Ertel GmbH. Der Hersteller hochwertiger Hartmetall-Fräs- und Bohrwerkzeuge hat seinen Hauptsitz in Kinding-Haunstetten im Altmühltal. 1990 in Beilngries gegründet und 1992 mit acht Mitarbeitern nach Haunstetten in einen Neubau umgezogen, beschäftigt das Unternehmen heute 160 Mitarbeiter im Altmühltal, weltweit insgesamt 220 an neun Standorten.
Vom Hauptwerk aus steuert Eckerle auch die anderen Niederlassungen. Gefertigt wird noch in Weimar, im österreichischen Mieming, in Portugal und in der Türkei. Weil ihm die Verantwortung für die Umwelt am Herzen liegt und „Luft teurer als Strom“ ist, wie er betont, hat Georg Eckerle die Druckluftversorgung an allen Standorten unter die Lupe genommen. „Ich gehe dafür auch selbst auf Leckagesuche, und zwar am Wochenende, wenn die Fertigung leise ist“, berichtet der Inhaber. „Mir ist es einfach ein Bedürfnis, diese Leckagen sofort zu beheben. Und wenn es nur eine Schlauchklemme ist, die nicht richtig sitzt oder Druckluftverluste verursacht!“ Von ineffizienten Drucklufterzeugern gar nicht erst zu reden.
Das Ergebnis der Untersuchungen und Effizienz-Überlegungen: Nach und nach werden alle Standorte auf Atlas-Copco-Kompressoren umgestellt. „Unsere Vorgabe lautet, dass in jeder Station mindestens eine drehzahlgeregelte Maschine stehen muss, damit wir keine Energie verschwenden“, sagt Eckerle. Messungen hätten ergeben, dass reine Volllast-Leerlauf-Stationen zu hohe Anlauf- und Leerlaufverluste mit sich bringen. „Wir haben dann ein Energiekonzept erarbeitet: Überall soll mit Drehzahlregelung und auch Wärmerückgewinnung gearbeitet werden.“
Dezentrale Versorgung mit drei Druckluftstationen
Der Standort Haunstetten ist mit den Jahren gewachsen, es gibt mehrere Hallen mit dezentraler Energieversorgung. Das ist ein Grund dafür, dass Inovatools auch seine Druckluftversorgung dezentral organisiert hat: Sechs Kompressoren teilen sich die Arbeit in drei Stationen. In Station 1, die aufgrund einer Erweiterung des Werkes entstanden ist, steht ein drehzahlgeregelter, öleingespritzter Schraubenkompressor des Typs GA 18 VSD+ FF von Atlas Copco mit 18 Kilowatt (kW) installierter Leistung. „Hier stand früher eine Volllast-Leerlauf-Maschine“, erklärt Eckerle. „Die Station ist mit der Drehzahlregelung nun um gut ein Drittel effizienter geworden.“
Zur Gesamteffizienz der GA-Kompressoren trägt auch bei, dass Kältetrockner sowie Druckluftfilter und Kondensatableiter von Atlas Copco bereits ab Werk in das Plug-and-play-Gehäuse des Kompressors integriert wurden. Darauf weist das Kürzel „FF“ (Full Feature) hin. Eingebaut ist zudem ein Plattenwärmetauscher, so dass sich eine Wärmerückgewinnung – wie etwa bei der dritten Station von Inovatools bereits geschehen – leicht umsetzen lässt. Laut Angaben von Atlas Copco sind mit der neuen GA-VSD+-Baureihe im Vergleich zu schlecht ausgelasteten Maschinen mit Volllast-Leerlauf-Regelung sogar Einsparungen von bis zu 50 Prozent möglich.
Sie resultieren in erster Linie aus der variablen Drehzahl: Durch die automatische Regulierung der Motordrehzahl wird die Druckluftversorgung im gesamten Druckluftnetz auf den jeweiligen Bedarf aller angeschlossenen Verbraucher abgestimmt. Hinzu kommt eine Konstruktion, die noch stärker auf Effizienz getrimmt wurde als bei der Vorgängergeneration. So weist der ölgekühlte interne Permanentmagnetmotor einen Wirkungsgrad gemäß IE4 („Super Premium Efficiency“) auf. Auch der Kühlluftventilator wurde neu entwickelt und ist sparsamer, und die vertikale Anordnung des Getriebestranges sowie die direkte Verbindung zwischen Motor und Verdichterstufe mit neuartigen Verdichtungselementen steigern die Effizienz zusätzlich.
An einer zweiten Station stehen noch zwei Kompressoren eines anderen Herstellers. Diese sind erst fünf Jahre alt, arbeiten aber auch nach dem Last-Leerlauf-Prinzip. Zwar steht dort ein großer Pufferbehälter, trotzdem ist Georg Eckerle unzufrieden. „Hier werden wir früher oder später auch auf eine Station mit Drehzahlregelung umstellen.“
15.000 Euro im Jahr gespart
Seine Lieblingsstation ist Station 3. Dort hat Inovatools vor einem Jahr, im Herbst 2016, einen GA 45 VSD+ FF hingestellt, ebenfalls drehzahlgeregelt und mit 45 kW Leistung der größte Kompressor am Standort. Eckerle sagt schlicht: „Diese Maschine ist mit ihrer Effizienz einfach der Knüller!“ Sie ersetzt zwei alte Kompressoren, die man aber derzeit noch in Reserve vorhält, angesichts des stetigen Wachstums, das das Unternehmen in den letzten Jahren gestemmt hat.
„Der Atlas-Copco-Berater hatte uns Berechnungen vorgeschlagen, mit denen wir die Effizienzsteigerungen gut prognostizieren konnten“, blickt der Geschäftsführer zurück. „Die Messungen mit anschließender Simulation ergaben, dass wir allein an dieser Station fast 15.000 Euro im Jahr würden sparen können. Da brauchten wir nicht zweimal zu überlegen.“ Überhaupt hätten Atlas-Copco-Kompressoren die höchste Qualität am Markt und die geringsten Ausfallquoten, findet Eckerle. „Und wir erhalten selbst hier im Altmühltal einen guten lokalen Service.“
Bei den Prognosen für den Bedarf der umzurüstenden Station 3 legte Atlas Copco einen aus der Vergangenheit bekannten Verbrauch von knapp 300000 kWh im Jahr zugrunde. Bei Kosten von 0,18 Euro pro Kilowattstunde belief sich die Stromrechnung bis dato auf rund 54.000 Euro. „Mit der neuen GA 45 VSD+ FF sollen wir bei gleichem Verbrauch nur noch auf 38.743 Euro kommen“, rechnet Eckerle. Außerdem habe man noch die BAFA-Förderung in Höhe von 30 % in Anspruch genommen. „Zusammen mit der Wärmerückgewinnung ergibt sich eine unfassbare Ressourcenersparnis“, freut er sich.
Denn in der Station wird die Verdichtungswärme aus dem Kompressor abgezogen und über Wärmetauscher an einen Warmwasserspeicher abgegeben. Der ist bei Atlas Copco unter der Bezeichnung „Thermo-Kit“ in zwei Größen erhältlich: als Thermo-Kit 400 und 800 mit 400- beziehungsweise 800-l-Speicher. Bei Inovatools steht ein 400er. Das Paket besteht aus Wärmespeicher, Pumpe, Steuerung und Installationszubehör. Es eignet sich für Anwender mit Zentralheizung, die Bedarf an 50 bis 70 °C warmem Wasser haben. Mit dem Thermo-Kit lässt sich die Energie von einer Stunde Volllastbetrieb des Kompressors aufnehmen und speichern.
Sperrluft sichert Qualität der Positionsmessungen in den CNC-Maschinen
Der Maschinenpark in Haunstetten umfasst 120 Maschinen, die allesamt Druckluft benötigen. Eckerle hebt die Steuerung der pneumatisch betriebenen Funktionen hervor sowie die sieben Ölfilteranlagen, die immer dann laufen, wenn die Werkzeuge beschliffen werden und der Ölschlamm ausgetragen werden muss. Die Rückspülung der sich regelmäßig zusetzenden Filter geschieht von innen mit Öl und Druckluft.
Die wichtigste Funktion der Druckluft ist jedoch diejenige als Sperrluft an den 80 CNC-Maschinen. Die an den Achsen eingebauten Glasmaßstäbe müssen mit einem Überdruck von 1,5 bar beaufschlagt werden, um von innen sauber zu bleiben und die Position der jeweiligen Achsschlitten exakt messen zu können. Sprich: Sie sind für die Qualität der erzeugten Produkte maßgeblich. Ein optischer Sensor am Schlitten erfasst die Position der Achse anhand eines „Lineals“ im Glasmaßstab, dessen Markierungen er abtastet, und gibt die Werte an die Steuerung weiter. Der Glasmaßstab könnte verdrecken, der Sensor von Öl beschädigt werden. „Deshalb benötigen wir hierfür trockene, sehr saubere und ölfreie Druckluft“, erklärt Georg Eckerle. „Die wird von den GA-Kompressoren sicher erzeugt.“
Die Erfahrungen mit den neuen drehzahlgeregelten GA-Kompressoren in den Stationen 1 und 3 seien „nur positiv“. Der Lärmpegel ist im ganzen Werk gesunken – was sich vor allem deshalb bemerkbar mache, weil alle drei Druckluftstationen sehr nah an den Fertigungsbereichen verortet sind. Die Kompressoren arbeiten laut Eckerle allesamt so leise wie prozesssicher. „Auch die Wärme können wir zurückgewinnen“, sagt er. Im Winter unterstütze das Unternehmen mit der abermals genutzten Verdichtungswärme die Heizung in den Fertigungshallen und der Verwaltung. „Leider haben wir in unseren Fertigungsprozessen keinen Bedarf für diese Wärme, sonst wären wir in diese Richtung natürlich auch längst aktiv geworden.“
Mehr Informationen zu Atlas Copco:
![]() |
Atlas Copco Deutschland |
![]() |
Langemarckstr. 35 |
![]() |
D-45141 Essen |
![]() |
Tel.: +49 (0)201 21 77 0 |
![]() |
Fax: +49 (0)201-2177-100 |
![]() |
E-Mail: atlascopco.deutschland@de.atlascopco.com |
![]() |
www.atlascopco.de |
![]() |
------------------------------------------------------ |
![]() |
Handwerkzeuge: |
![]() |
Atlas Copco Tools Central Europe GmbH |
![]() |
Langemarckstr. 35 |
![]() |
D-45141 Essen |
![]() |
Tel.: +49 (0)201 21 77 0 |
![]() |
E-Mail: tools.de@atlascopco.com |
![]() |
www.atlascopco.com/de-de/itba |
War dieser Artikel für Sie hilfreich?
![]() |
![]() |
![]() |
![]() |
![]() |
Bitte bewerten Sie diese Seite durch Klick auf die Symbole.
Zugriffe heute: 1 - gesamt: 2124.