Low-Frequency-Technologie von eldec
Low-Frequency-Technologie von eldec
Schneller, präziser, sparsamer –das induktive Erwärmen hat viele Anwendungsbereiche erobert. Die Experten von Emag eldec kennen diese Vorteile und haben das Portfolio um die Low-Frequency-Technik (LF) erweitert. Konkrete Anwendungsbeispiele machen deutlich, dass der gesamte Prozess von kürzeren Taktzeiten und einer höheren Reproduzierbarkeit profitiert.
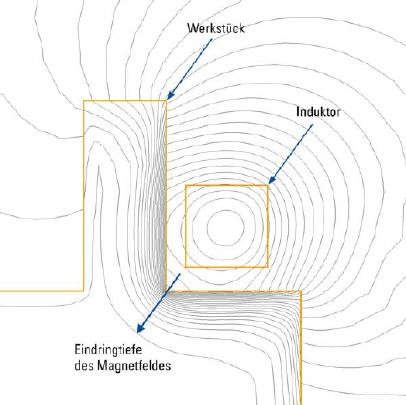
Schweiß- oder Fügeprozesse stellen gerade im Automobilbau eine besondere Herausforderung dar, denn es müssen riesige Stückzahlen mit minimaler Taktzeit und ohne unzulässige Veränderung im Werkstoffgefüge bearbeitet werden – die induktive Erwärmung ist deshalb häufig ein unverzichtbarer Bestandteil des verketteten Gesamtprozesses: Mithilfe der Technologie lässt sich das Bauteil sehr schnell auf die für den Prozess benötigte Bearbeitungstemperatur bringen. Unmittelbar danach startet der Hauptprozess. Allerdings darf es dabei nie zu einer Überhitzung am Bauteil kommen, die mit einer Härtereduktion, einer Oxidation oder einem unzulässigen Verzug einhergehen kann.
LF-Technologie punktet im Versuch
Welche Vorteile in diesem Zusammenhang die LF-Generatoren (Low Frequency) von EMAG eldec eröffnen, verdeutlicht ein aktuelles Anwendungsbeispiel aus dem eldec Technologiezentrum: Ziel war es hier, einen einfachen Kranz (ähnlich einem Gangrad) auf eine Temperatur von mindestens 200 und höchstens 370 Grad Celsius zu erwärmen – und das mit möglichst kleiner Taktzeit und hoher Prozesssicherheit. Dafür haben die Experten mithilfe einer numerischen Berechnung die induktive Erwärmung mit einer niedrigen Frequenz sowie mit einer typischen Mittelfrequenz vergleichend untersucht.
Die Ergebnisse sind eindeutig:
- Bei Einsatz einer niedrigen Frequenz von 2 kHz und einer Prozessdauer von fünf Sekunden zeigt sich das gewünschte Wärmebild von mindestens 200 Grad Celsius überall im Kranz (siehe Abbildung).
- Kommt eine Mittelfrequenz von 12,5 kHz zum Einsatz, muss die zulässige Maximaltemperatur auf 420 Grad Celsius ansteigen. Sonst wird innerhalb der angestrebten fünf Sekunden keine Mindesttemperatur von 200 Grad überall im Kranz erreicht. Die höhere Maximaltemperatur ist dabei unzulässig.
- Alternativ kann bei Einsatz von Mittelfrequenzen auch die Prozessdauer erhöht werden. Es ist dann allerdings eine Erwärmungszeit von 8,5 Sekunden nötig, um die gewünschte Temperaturverteilung (ohne Überschreiten der Maximaltemperatur) zu erreichen.
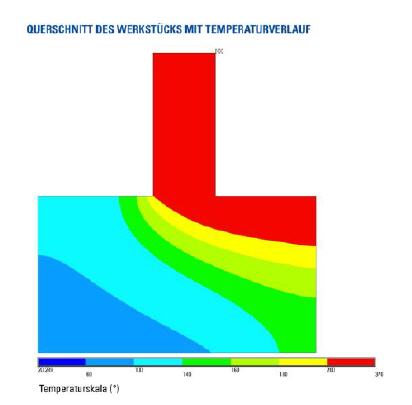
„Numerische Berechnungen nutzen wir, um Prozesse genauer und schneller auszulegen, als dies per ‚Trial-and-Error’ möglich wäre – also etwa zunächst einen Induktor bauen, testen, umbauen und so weiter. Die Ergebnisse lassen sich qualitativ sehr gut in die Praxis übertragen und machen hier auch sehr deutlich, welche Vorteile die LF-Technologie eröffnet“, erklärt Dr. Dirk Schlesselmann, stellvertretender Bereichsleiter F&E Anwendungstechnik bei eldec. „Die niedrigen Frequenzen erwärmen schneller im Volumen, weil das Magnetfeld tiefer in das Bauteil eindringt. Deswegen können wir die Taktzeit im Vergleich zur Mittelfrequenz deutlich reduzieren. Außerdem ist es leichter, im gewünschten Temperatur-Prozessfenster zu bleiben und die Gefahr von Überhitzungen geht zurück. Nicht zuletzt sind die auftretenden Temperaturgradienten kleiner. Und das bedeutet letztlich, dass die Gefahr einer Rissbildung am Bauteil kleiner ist.“
Vor diesem Hintergrund bieten die Induktionsspezialisten von EMAG eldec bereits ein breites Generatoren-Portfolio mit LF-Technologie an (Leistung: 50 bis 500 kW, Frequenzbereich: 2 bis 8 kHz). Ihr denkbarer Anwendungsbereich ist groß: Zum Beispiel beim Vorerwärmen für das Schweißen von Getrieberädern, Fügen von Statoren in Elektromotorengehäusen, Imprägnieren von Statoren oder Anlassen nach dem Härten sorgt die Technologie für große Anwendungsvorteile.
„Im Prinzip kann LF überall dort Sinn machen, wo eine Erwärmung im Volumen mit niedrigen Taktzeiten erfolgen soll. Unsere LF-Generatoren sorgen dann aber nicht nur für schnellere Abläufe, sondern operieren auch mit hoher Prozesssicherheit. Außerdem punkten die Geräte mit Spitzentechnologie. Sie nutzen die robuste und etablierte IGBT-Transistortechnik, haben einen Wirkungsgrad von mehr als 90 Prozent und ihre Energie wird präzise dosiert. Diese Vorteile wollen wir ab sofort auch im LF-Bereich gezielt in den Markt einbringen.“
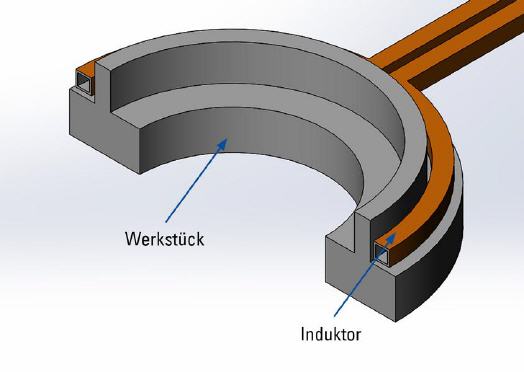
Mehr Informationen zur EMAG eldec Induction GmbH:
![]() |
EMAG eldec Induction GmbH |
![]() |
Otto-Hahn-Strasse 14 |
![]() |
72280 Dornstetten |
![]() |
Tel.: +49-7443-9649-0 |
![]() |
Fax : +49-7443-9649-6931 |
![]() |
E-Mail: info@eldec.de |
![]() |
www.eldec.net |
War dieser Artikel für Sie hilfreich?
![]() |
![]() |
![]() |
![]() |
![]() |
Bitte bewerten Sie diese Seite durch Klick auf die Symbole.
Zugriffe heute: 1 - gesamt: 2084.