Spitzenzeiten beim 3D-Druck
TruPrint 5000 mit Multilaserprinzip
Trumpf hat eine extrem schnelle und produktive 3D-Druck-Anlage im Mittelformat für Metallbauteile vorgestellt. Die ›TruPrint 5000‹ arbeitet im Multilaserprinzip und ist nicht nur mit einem, sondern mit drei scannergeführten und 500 Watt starken Trumpf-Faserlasern ausgestattet.
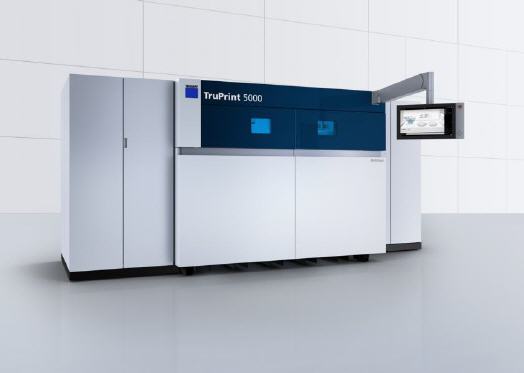
Die drei Laser der TruPrint 5000 sind mit einer von TRUMPF speziell konstruierten Optik so angebracht, dass sie gleichzeitig überall im gesamten Bauraum der Anlage arbeiten und so deutlich schneller und effizienter Bauteile erzeugen können - und das unabhängig von Anzahl und Geometrie der Bauteile.
Der Clou an der ganzen Sache: Anders als bei anderen Multilaserkonzepten ist die TRUMPF-Variante nicht auf definierte Bereiche in der Prozesskammer begrenzt - das macht den 3D-Drucker besonders schnell und produktiv.
Weiterer Faktor für die Geschwindigkeit sind die von TRUMPF entwickelten Belichtungsstrategien. Sie ermitteln automatisch die idealen Laserbahnen, sodass alle drei Laser immer teileübergreifend belichten können. Nahtstellen entstehen an den Bauteilen nicht, da sich die Außenkonturen nahtlos mit nur einem Laser erstellen lassen. Sind alle Prozessparameter optimal eingestellt, benötigt die TruPrint 5000 nur noch ein Drittel der Belichtungszeit pro Baujob.
Die Anlage basiert auf der Fertigungstechnologie Laser Metal Fusion (LMF) und erzeugt komplexe Bauteile per Laser Schicht für Schicht im Pulverbett. Die Bauteile können eine Größe von bis zu 300 Millimeter Durchmesser und 400 Millimeter Höhe haben und aus allen schweißbaren Werkstoffen bestehen, etwa Stähle, Nickelbasislegierungen, Titan oder Aluminium, sowie aus kohlenstoffreichen Warmarbeitsstählen. Die Vorheizung auf bis zu 500 Grad Celsius sichert insbesondere bei Warmarbeitsstählen und Titan eine hohe Bauteilqualität und sorgt bei allen Materialien für einen robusten Bauprozess.
Flexible Automatisierung
TRUMPF legt den Fokus bei seinen 3D-Druckern auch auf die Automatisierung der Anlagen. So ist die TruPrint 5000 in der Lage, automatisch den Fertigungsprozess zu starten - was zu einem robusten Prozess mit weniger Aufwand für den Bediener führt. Sobald der Bauzylinder in der Anlage platziert ist, fährt er automatisch auf seine Rüst- und Arbeitsposition. Das integrierte Nullpunktspannsystem ist die Basis für nachgelagerte Prozessschritte wie Erodieren, Fräsen oder Drehen. Es verbindet die Substratplatte automatisiert mit dem Kolben im Zylinder, sodass manuelle Arbeitsschritte (etwa Festschrauben) gänzlich entfallen. Anschließend bringt ein Fahrsystem in der Prozesskammer Bauraum- und Zylinderdeckel in eine Lagerposition und der Fertigungsprozess startet selbstständig.
Im nächsten Schritt kalibrieren sich die Laser, die Substratplatte richtet sich aus und der Bauprozess startet automatisch. Durch das integrierte Wechselzylinderprinzip lässt sich der Bauzylinder mit den fertig erzeugten Bauteilen ausfahren, während die Baukammer mit Schutzgas inert bleibt und direkt mit dem nächsten Baujob starten kann. Das senkt Stillstands- und Nebenzeiten und erhöht gleichzeitig die Produktivität des 3D-Druckers.
Automatisierte Peripherie erleichtert die Bearbeitung
Die TRUMPF-Siebstation reinigt mehrere Hundert Kilogramm Pulver pro Stunde und sichert so eine gleichbleibende Qualität des Pulvers. Auch die Entpackstation ist nahtlos in die Prozesskette integriert; der abgedeckte Bauzylinder lässt sich direkt in die Station fahren. Vorteil: Das externe Entpacken führt zu einer hohen Maschinenverfügbarkeit. Dank Schutzhandschuhen und Sichtschutz kommt der Anwender beim Entpacken und Reinigen nicht mit dem Pulver in Berührung. Das überschüssige Material landet am Ende wieder in der Siebstation. Dadurch ist ein sicherer und geschlossener Pulverkreislauf gewährleistet. Die Anlage ist somit bestens für einen industriereifen Serienfertigungsprozess ausgestattet.
Mit ihrer flexiblen Automatisierungsschnittstelle ist die Anlage kompatibel für unterschiedliche Industrie- und Fertigungsszenarien. So lässt sich die 3D-Druck-Anlage je nach Fabrikkonzept schnell und einfach beispielsweise an einer automatisierten Roboterlösung, einem Schienensystem oder einem autonomen Fahrzeug anbinden.
TRUMPF druckt optimierte Servoventile auf der Formnext
Dass die additive Fertigung Bauteile optimieren und neue Designfreiheiten eröffnen kann, zeigt einmal mehr das jüngste Gemeinschaftsprojekt zwischen Bosch Rexroth, Heraeus Additive Manufacturing und TRUMPF. In enger Zusammenarbeit haben die drei Unternehmen ein Servoventil neu gestaltet, Schwachstellen eliminiert und einen hybriden Fertigungsprozess entwickelt.
Der Technologiekonzern Heraeus hat hierfür das am besten geeignete Pulver hinsichtlich Fließverhalten und Partikelgrößenverteilung qualifiziert. TRUMPF hat mit seiner Technologiekompetenz das Herstellungsverfahren entscheidend geprägt. Im Rahmen des Projektes hat das Projektteam eine hybride Fertigung von Servoventilen für künftige Serienanwendungen entwickelt. Dabei werden konventionell hergestellte Preforms mit 3D-gedruckten und lasergeschnittenen Teilen für eine wirtschaftliche Fertigung der Ventile ergänzt. Die auf der TruPrint 5000 gedruckten Servoventile sind wesentlich leichter und kompakter, die optimierten Kanalführungen verringern die Drosselverluste und steigern die Energieeffizienz.
Mehr Informationen zur TRUMPF Lasertechnik:
![]() |
TRUMPF Laser- und Systemtechnik GmbH |
![]() |
Postfach 1450 |
![]() |
71252 Ditzingen |
![]() |
Johann-Maus-Straße 2 |
![]() |
71254 Ditzingen |
![]() |
Telefon +49 (0) 7156-303-0 |
![]() |
Telefax: +49 (0) 7156-303-670 |
![]() |
E-Mail: info@trumpf-laser.com |
![]() |
www.trumpf-laser.com |
War dieser Artikel für Sie hilfreich?
![]() |
![]() |
![]() |
![]() |
![]() |
Bitte bewerten Sie diese Seite durch Klick auf die Symbole.
Zugriffe heute: 1 - gesamt: 1948.