Sicher und effizient spannen
Auszugssicherung Safe-Lock wird zum Standard
Das Haimer Safe-Lock-System sorgt für sichere Werkzeugspannung. Durch Mitnehmerelemente im Futter, die in spiralförmige Nuten im Werkzeugschaft eingreifen, wird zusätzlich zu den reibschlüssigen Klemmkräften ein Formschluss erzeugt. Der verhindert wirksam, dass Schaftfräser aus dem Futter gezogen werden. Dadurch lassen sich höhere Schnittwerte fahren. Auch die Werkzeugstandzeiten verlängern sich.
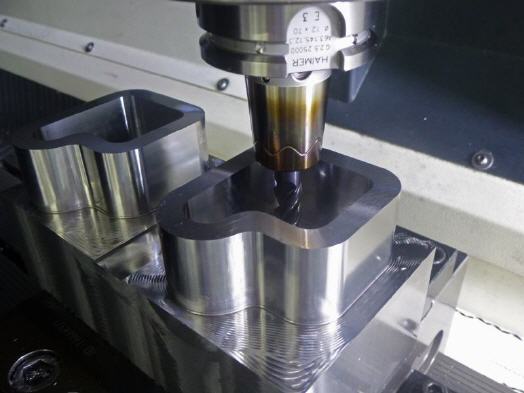
Safe-Lock ist mittlerweile zu einem de-facto Standard in der Werkzeugspannung für die Fräsbearbeitung geworden. Dass diese Form der Werkzeugspannung in vielen Fällen herkömmlichen Kraftspannfuttern und Weldon-Schäften deutlich überlegen ist, hat sich in den zehn Jahren seit der Einführung des Safe-Lock-Systems vielfach bestätigt.
Bestes Zeichen dafür ist die große Anzahl der Lizenznehmer, zu denen mittlerweile nahezu alle führenden Werkzeug- und Aufnahmenhersteller gehören –zum Beispiel Walter, Widia, Sandvik, Coromant, Seco Tools, Sumitomo, Kennametal, Helical, Emuge Franken, Data Flute, Niagara, OSG und Mapal. Im Jahr 2017 entschlossen sich auch Iscar und Ingersoll, Werkzeuge mit Safe-Lock-Schaft anzubieten. Zudem ist das futterseitige Angebot auf Schrumpf-, Spannzangen- und Hydrodehnspannfutter angewachsen. Neben den bereits verfügbaren Safe-Lock Hydrodehnspannfuttern von Kennametal arbeitet Mapal bereits daran ein eigenes Safe-Lock Sortiment in Hydrodehnspanntechnik auf den Markt zu bringen.
Andreas Haimer, Geschäftsführer der HAIMER GmbH, erklärt: „Wir sind stolz darauf, dass sich Safe-Lock in der Schwer- und Schruppzerspanung gewissermaßen als Standard etabliert hat, und breite neue Einsatzfelder wie das trochoidale Fräsen erobert. Wir freuen uns außerdem über unsere neuen Lizenzpartner, die das Safe-Lock-Angebot erweitern und noch mehr Anwendern zugänglich machen.“
Erfolgreich in der Luft- und Raumfahrt-Industrie Entstanden ist Safe-Lock aus den Anforderungen der Schwerzerspanung, wie sie in der Luft- und Raumfahrt-Industrie sowie bei Energieerzeugern an der Tagesordnung ist. Innovative Werkstoffe wie zum Beispiel diverse Titanlegierungen sind nicht nur leicht, sondern auch hochfest, korrosionsbeständig – und schwer zu bearbeiten. Das betrifft nicht nur Maschinenkonzepte und Prozesse, sondern auch die eingesetzten Werkzeuge und Spannfutter.
Viele Werkstücke werden aus dem Vollen gefräst, wobei oftmals bis zu 90 Prozent des Materials zerspant werden. Um den Prozess wirtschaftlich und qualitativ zu optimieren und ein hohes Zeitspanvolumen zu erreichen, werden meist hohe Drehmomente und Vorschubkräfte sowie niedrige Drehzahlen gewählt. Bei diesem Hochleistungsfräsen (High Performance Cutting, HPC) treten jedoch hohe Zugkräfte auf. In Verbindung mit hohen Schnitt- und Vorschubkräften führen sie zu einer Walkbewegung des Werkzeuges im Futter. Es besteht die Gefahr, dass der Fräser aus dem Futter gezogen wird. Das betrifft insbesondere all die Werkzeugaufnahmen, die eine genaue Spannung mit guter Rundlaufgenauigkeit bieten, wie zum Beispiel Schrumpf-, Hydrodehn- oder auch Kraftspannfutter.
Daher ist Safe-Lock in der Luft- und Raumfahrt-Industrie inzwischen weit verbreitet. Alexander Steurer, Leiter CNC–Programmierung Stator-Bauteile bei der MTU Aero Engines AG in München, erklärt die Entscheidung seines Bereichs für das Haimer-System: „Durch die Einführung der Safe-Lock-Technologie und Schrumpftechnik von Haimer können wir die Prozesssicherheit bei kritischen Fräsbearbeitungen von hochwarmfesten Werkstoffen gewährleisten. Dies ist eine Grundvoraussetzung, um bei dem in unserer Gehäusefertigung umgesetzten Automatisierungsgrad reibungslose Abläufe zu gewährleisten.“
Die Kombination von Auszugsicherheit und hoher Rundlaufgenauigkeit führt zu einer schwingungsarmen und dadurch sehr effizienten Zerspanung: Durch gesteigerte Schnitttiefen und Vorschübe kann das Zeitspanvolumen teils deutlich erhöht werden. Der Werkzeugverschleiß verringert sich durch die exzellenten Rundlaufeigenschaften auf bis zu 50 Prozent.
Die Argumente des optimalen Rundlaufs von weniger als 3 µm, das symmetrische Safe-Lock-Design und die Möglichkeit für eine einfache Längeneinstellung waren für die MTU gewichtige Gründe, um auf das Haimer-System umzusteigen, anstatt weiterhin mit Whistle Notch bzw. Weldon-Werkzeugen zu arbeiten. Diese verhindern zwar den Werkzeugauszug ebenso wirkungsvoll, sind allerdings hinsichtlich Rundlauf und Wuchtgüte bereits durch die unsymmetrische Flächenverteilung ungenügend. Mit Safe-Lock zu höherer Produktivität Doch nicht nur in der Luft- und Raumfahrt hat Safe-Lock™ begeisterte Anhänger gefunden.
Daniel Rautenbach bewegt sich mit der Glätzer GmbH im harten Geschäftsumfeld der Automobilindustrie. Der geschäftsführende Gesellschafter des Spezialisten für CNC-Bearbeitung in Solingen erläutert: „Perfekte Qualität und absolute Liefertreue sind Grundvoraussetzungen, um überhaupt ein Angebot abgeben zu können – letztlich entscheidet der Preis.“ Dementsprechend gilt in seiner Produktion: Qualität ohne Abstriche ist ein Muss – die Effizienz macht letztlich den Unterschied zwischen Gewinn und Verlust.
Über einen Auftrag zur Bearbeitung einer Lkw-Scheibenbremse aus Gusseisen Typ EN-GJS-800-2 mit zu fräsenden konkaven Konturen kamen die Produktionsverantwortlichen Mitte 2013 zum HAIMER Safe-Lock-System. Betriebsleiter Ingo Schulten erklärt: „Bei dieser Bearbeitung hat der Fräser nicht nur punktuellen Kontakt zum Werkstück, sondern er wird zu 30 oder 40 Prozent umschlungen. Die dabei wirkenden extrem hohen Kräfte drohen das Werkzeug aus der Aufnahme zu ziehen.“ Die eingesetzten Weldon-Spannfutter hielten zwar das Werkzeug fest in der Aufnahme. Aber die seitliche Schraube verhindert einen guten Rundlauf des Werkzeugs. „Wir hatten extrem schwankende Standzeiten der Werkzeuge, und es kam sogar zu Fräserbrüchen“, berichtet der Betriebsleiter.
Fräsversuche mit Safe-Lock überzeugten ihn und die anderen Produktionsmitarbeiter bei Glätzer. „Der Wechsel zu dieser Auszugsicherung kam uns vor wie der Sprung von der Kurbel zum elektrischen Anlasser“, zeigt sich Schulten begeistert. „Wir können damit jetzt produktive Schnittwerte fahren, und erfreulicherweise liegen die Werkzeug-Standzeiten nun um 40 Prozent höher als zuvor.“
Vorteile beim High Speed Cutting Safe-Lock setzt sich auch branchenübergreifend immer mehr in der HSC-Bearbeitung mit hochspiralisierten Fräswerkzeugen sowie beim trochoidalen Fräsen durch. Bei letzterem werden Werkzeugeingriffswinkel und Schnittgeschwindigkeit über die gesamte Bearbeitung hinweg durch das CAM-System berechnet und optimiert. Dadurch kann bis zu dreimal schneller und tiefer gefräst werden, auch in harten und schwer zerspanbaren Werkstoffen.
Allerdings steigt dabei die Gefahr des Werkzeugauszugs. Auch wenn beim trochoidalen Fräsen meist nur ein dünner Span abgetragen wird, ist jedoch die Werkzeugschneide oft mit ihrer gesamten Länge im Eingriff. So entstehen hohe Axialkräfte, die den Anwender dazu zwingen für eine sichere Werkzeugspannung zu sorgen. Ein Schrumpffutter mit Safe-Lock ist hierfür eine ideale Lösung, da es eine bessere Sicherheit als eine Weldon-Aufnahme bietet, leichter zu montieren ist und darüber hinaus noch hochgenau spannen kann. Durch die guten Wucht- und Rundlaufeigenschaften in Verbindung mit der Spannsicherheit lassen sich optimale Werkzeugstandzeiten bei zugleich hohen Zerspanraten erzielen.
Mehr Informationen zur Haimer GmbH:
![]() |
Haimer GmbH |
![]() |
Weiherstraße 21 |
![]() |
86568 Igenhausen |
![]() |
Tel.: +49 (0) 82 57 / 99 88-0 |
![]() |
Fax: +49 (0) 82 57 / 18 50 |
![]() |
E-Mail: haimer@haimer.de |
![]() |
www.haimer.com |
War dieser Artikel für Sie hilfreich?
![]() |
![]() |
![]() |
![]() |
![]() |
Bitte bewerten Sie diese Seite durch Klick auf die Symbole.
Zugriffe heute: 1 - gesamt: 1811.