Gleichmäßige Fasen für perfekte Schweißnähte
Bessere Qualität in der halben Zeit
Für die Schweißnahtvorbereitung an Aluminium-Bauteilen für Waggons und Triebwagen nutzt die Stadler Altenrhein AG Anfasmaschinen von Atlas Copco Tools. Die Qualität der Schweißnähte hat sich so verbessert, dass kaum mehr Nacharbeit nötig ist. Zudem schaffen die Werker die Arbeit mit diesen Werkzeugen in der Hälfte der Zeit.
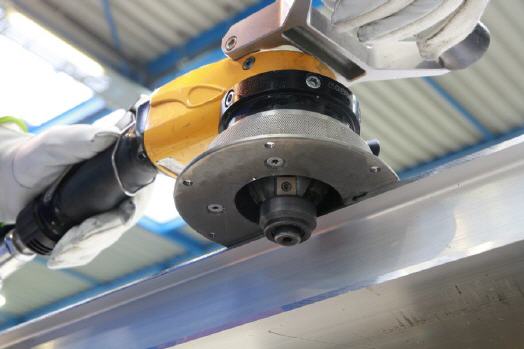
Beim Besuch der Stadler Altenrhein AG fällt der Blick gleich auf eine bunte Explosionszeichnung an der Wand. Das Fertigungskonzept illustriert die Einzelteile eines Schienenfahrzeugs: Stirn- und Seitenwände, Vorbauten und Mittelteil des Untergestells, Oberdeck, Zwischenböden, Türportale. In den Fertigungshallen liegen sie in unterschiedlichen Bearbeitungszuständen vor, um sich später zu einem Doppelstockwagen für zwei- bis mehrteilige Züge zu fügen. Auch kundenindividuelle Züge und Straßenbahnen bauen die 1000 Mitarbeiter hier.
Allein 35 Beschäftigte am Standort arbeiten in der sogenannten Kastendetailfertigung. Einer der wesentlichen Schritte ist die Vorbereitung der Alu-Rohprofile für das anschließende Fügen. „Für dieses Kopfstück wurden drei Rohprofile zusammengeschweißt“, sagt Manfred Reibnegger, der in Altenrhein für die Kastendetailfertigung verantwortlich ist. Er zeigt auf ein etwa 4 bis 5 m langes Bauteil, das später als Kopfstück des Wagen-Vorbaus dienen und Puffer sowie Kupplung aufnehmen wird.
Die Kopfstücke bestehen aus drei bis sechs Profilen. Diese werden miteinander verschweißt, mit einem hartmetallbestückten 700-mm-Sägeblatt in einer CNC-Maschine auf die gewünschte Länge und Breite gebracht und dann in dem Bearbeitungszentrum mit Bohrungen und Aussparungen für Anbauteile versehen. „Im nächsten Arbeitsschritt werden sie manuell entgratet“, erklärt Reibnegger weiter. „Und um sie optimal für die späteren Schweißprozesse vorzubereiten, fasen wir alle Kanten an.“ Dabei spiele die Qualität der Fasen eine wichtige Rolle; denn die Werkstücke müssten in verschiedenen Winkeln zueinander zusammengeschweißt werden. Hohe Maßhaltigkeit der Fasen sei die Voraussetzung dafür, dass die Materialkanten leicht positioniert werden können – und dass die Schweißnähte perfekt halten.
Fasen auf bis zu 25 m Länge
Stadler setzt daher seit einiger Zeit auf druckluftbetriebene Turbinen-Anfasmaschinen von Atlas Copco: „Mit der GTB 25 bearbeiten wir die breiteren Kanten über längere Strecken“, sagt Reibnegger. Dazu gehören die 6 bis 11 m langen Seitenwände, die später auf das Untergestell geschweißt werden. Oder die Oberdeckprofile, die auf der gesamten Länge von 25 m angefast und dann aneinander beziehungsweise an die Seitenwände geschweißt werden müssen. 6 bis 7 m lang wiederum sind die Bodenplatten, die sich an die Kopfstücke anschließen. Und so weiter. „Im Niederflurwagen gibt es 24 oder 25 Platten, die eine Fase benötigen“, erklärt Reibnegger.
Atlas Copco bietet die GTB 25 mit verschiedenen Schneidköpfen zur Vorbereitung für die gängigsten Schweißprozesse an, um die Kanten im richtigen Winkel anzuschrägen. Das von Stadler verwendete Werkzeug hat einen Schneidkopf für 30-Grad-Fasen. „Der Werker braucht die Maschine im Prinzip einfach nur noch an der Kante entlangzuführen, der Winkel stimmt dann automatisch“, macht Reibnegger klar. Bis vor einiger Zeit wurde dieser Arbeitsschritt noch mit einem gewöhnlichen Winkelschleifer erledigt. Mit der Erfahrung der Produktionsmitarbeiter bei Stadler ging dies zwar auch, aber eben nicht ganz so sauber. „Und es dauerte deutlich länger“, gibt Werker Steffen Zwanzig zu.
Auch probehalber eingesetzte Akkumaschinen brachten wesentlich weniger Leistung als die druckluftbetriebene GTB 25, die Atlas Copco auf der Basis seiner GTG-Turbinenschleifer entwickelt hat. „Und die Verwendung von Elektrowerkzeugen vermeiden wir aus Sicherheitsgründen weitestgehend“, ergänzt Reibnegger. Kabel könnten durch Aluspäne aufscheuern; zudem drehten die Maschinen zu lange nach. Für das Kopfstück, das Steffen Zwanzig mit der GTB 25 bearbeitet, braucht er jetzt etwa zwei Stunden. „Früher habe ich ungefähr vier Stunden an einem Bauteil dieser Größe gearbeitet“, sagt er. Neben der Zeitersparnis von durchschnittlich 50 % pro Werkstück profitiert Stadler vor allem von der gestiegenen und nun immer konstanten Qualität der Fasen.
Gleichmäßige Spalte
„Als wir noch mit normalen Schleifmaschinen gearbeitet haben, schwankte der Winkel der Fase schon mal stärker“, sagt Reibnegger. „Doch für den Schweißprozess ist ein gleichmäßiger Spalt sehr wichtig, vor allem angesichts der hohen Anforderungen an die Belastbarkeit einzelner Komponenten!“ Aus der Hand, mit dem Winkelschleifer, lasse sich die genaue Gradzahl selbst von den erfahrenen Stadler-Mitarbeitern nicht auf der gesamten Länge durchhalten.
Das Führungslager der GTB 25 macht die exakte Bearbeitung der Kanten dagegen einfach. Für die Kopfstücke und Bodenplatten setzt Stadler einen 30°-Schneidkopf ein, mit dem Fasen von 30° oder 60° gefräst werden können – je nachdem, ob der Werker die Maschine horizontal oder vertikal am Werkstück ansetzt. Durch ihren ergonomischen Zusatzhandgriff lässt sich die Turbinen-Anfasmaschine komfortabel bedienen und sicher am Bauteil entlangführen.
Vor dem Fräsvorgang wird die Oberfläche lediglich noch mit einem Kühlschmierstoff behandelt. Das dient dazu, dass die Wendeschneidplatten sich nicht mit Aluminiumspänen zusetzen, was aufgrund des weichen Materials bei der Hitze sonst leicht geschehen könnte. „Anders als bei Stahl kann man Aluminium nicht an der Farbe ansehen, wann es heiß wird“, erklärt Reibnegger. Der Schmierstoff muss nach der Bearbeitung entfernt werden, damit er den Schweißvorgang nicht ungünstig beeinflusst.
Nacharbeit überflüssig
„Auch unsere Qualitätskontrollen zeigen, wie sich der Prozess durch die Atlas-Copco-Maschine verbessert hat“, sagt Reibnegger. „Vorher waren die Schweißnähte oft nicht in Ordnung und mussten nachgearbeitet werden.“ Bei ungleichmäßigen Fasen konnte es dazu kommen, dass die Durchschweißung zu gering war oder die Naht durchbrannte. Das wurde dann bei der Zwischenkontrolle festgestellt und kostete viel Nacharbeit, um die Nähte wieder aufzuschleifen und zu reparieren. „Jetzt genügt es, dass wir stichprobenartig nur etwa zehn Prozent der Bauteile röntgen“, erklärt Reibnegger weiter. „Das machen wir ausschließlich bei den hochbelasteten Teilen.“ Wenn Nacharbeit nötig sei, betreffe das heute nur noch Übergangsfehler an den Schweißansätzen. An den Fasen gebe es keine Probleme mehr.
Auch die Werker sind mit der Maschine sehr zufrieden. Während es mit dem Winkelschleifer nötig war, ständig die Einhaltung des Winkels zu kontrollieren, stellen die Mitarbeiter jetzt nur noch die Höhe der Fase ein – und bestimmen damit auch ihre Breite. „Wichtig ist, dass immer ein Fasensteg von mindestens ein bis zwei Millimetern verbleibt“, erklärt Steffen Zwanzig und stellt die Höhe ein, indem er einfach die Werkzeugführungsplatte dreht. Er korrigiert die Einstellung, bis die Vorgaben erfüllt sind. „Wenn der Steg zu dünn wird, könnte sich die Maschine ins Material schneiden“, sagt er. Das Führungslager limitiere die Eintauchtiefe der Anfasmaschine.
Ein Sicherheitshebel vermeidet unbeabsichtigtes Starten, und der 360°-Luftauslass lässt sich so einstellen, dass er die Abluft direkt vom Bediener wegleitet. Auch sonst zeigt sich die GTB 25 pflegeleicht, da die Wendeplatten mit ihren acht Schneiden sehr leicht gewechselt oder gedreht werden können; das übernimmt Christian Feig im Haus, der sämtliche Werkzeuge am Standort betreut und regelmäßig wartet. „Alle vier Monate wird außerdem ein Ölwechsel gemacht, damit das Getriebe keinen Schaden nimmt“, sagt der Maschinenmechaniker, der an einer Wartungsschulung von Atlas Copco Tools in Studen teilgenommen hat.
LSB 38 für Fensteröffnungen
Unter den 180 Schleifwerkzeugen in Feigs Obhut sind auch zwei kleinere Lamellen-Anfasmaschinen von Atlas Copco. Die beiden LSB 38 wurden angeschafft, weil die GTB für Fräsarbeiten im Winkel von 45° bei 4 mm Radius etwas zu unhandlich war. „Wir nutzen die wendigeren LSBs zum Beispiel zum Fräsen der Radien an den Fensteröffnungen“, erklärt Manfred Reibnegger. Mit einem Fenster sind die Mitarbeiter bei Stadler mit der LSB 38 in weniger als einer Minute fertig. „Vorher haben wir dafür etwa fünf Minuten benötigt“, sagt Steffen Zwanzig: „Die Krümmungen sind ziemlich knifflig, da musste man mit einem Winkelschleifer sehr aufpassen.“
Auch mit den Lamellenwerkzeugen hat Christian Feig, der jede Wartung und Reparatur in einer Datenbank hinterlegt, nicht viel Arbeit; denn die Lamellen arbeiten ölfrei, so dass sie auch mit ölfreier Druckluft betrieben werden können. Damit ist beim Arbeiten mit der LSB eine Kontaminierung von Oberflächen vor dem Schweißvorgang ausgeschlossen. Nur das hermetisch gekapselte Getriebe muss im Rahmen der Wartungsroutine geschmiert werden. Zur regelmäßigen Wartung gehört neben Ölwechsel und Schneidmittelüberprüfung auch die Kontrolle der Drehzahl. „Insgesamt sind die Druckluftmaschinen wesentlich robuster als die Elektro- und Akkuwerkzeuge“, betont Feig. „Im Prinzip kann die LSB gar nicht so kaputt sein, dass man sie nicht reparieren könnte.“
Mehr Informationen zu Atlas Copco:
![]() |
Atlas Copco Deutschland |
![]() |
Langemarckstr. 35 |
![]() |
D-45141 Essen |
![]() |
Tel.: +49 (0)201 21 77 0 |
![]() |
Fax: +49 (0)201-2177-100 |
![]() |
E-Mail: atlascopco.deutschland@de.atlascopco.com |
![]() |
www.atlascopco.de |
![]() |
------------------------------------------------------ |
![]() |
Handwerkzeuge: |
![]() |
Atlas Copco Tools Central Europe GmbH |
![]() |
Langemarckstr. 35 |
![]() |
D-45141 Essen |
![]() |
Tel.: +49 (0)201 21 77 0 |
![]() |
E-Mail: tools.de@atlascopco.com |
![]() |
www.atlascopco.com/de-de/itba |
War dieser Artikel für Sie hilfreich?
![]() |
![]() |
![]() |
![]() |
![]() |
Bitte bewerten Sie diese Seite durch Klick auf die Symbole.
Zugriffe heute: 1 - gesamt: 2313.