Vom Rohr-Halbzeug bis zum Türgriff
Laserschweißen mit Anspruch
Tür auf, Tür zu – unzählige Male öffnet oder schließt jeder von uns tagtäglich Türen mit einem Griff. Wie jedoch ein Türgriff produziert wird und dass in der Herstellungskette gleich mehrfach ein Laser zum Einsatz kommt, lernt man bei dem führenden Beschlag-Hersteller Hoppe im hessischen Stadtallendorf. Dort ist ein Faserlaser integriert worden. Hier im Edelstahl-Kompetenzzentrum Werk 1 verschweißt er Türgriffe mit Vierkant-Stahleinsätzen.
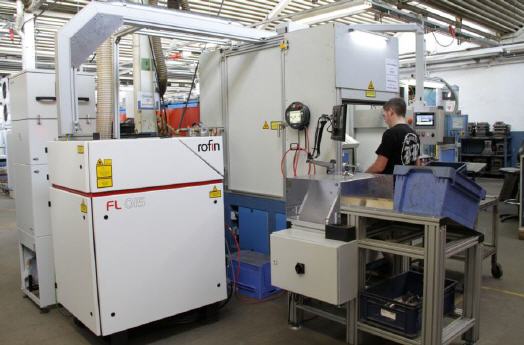
Als europäischer Marktführer in seiner Branche kennt sich HOPPE mit Innovationen sowohl bei den Produkten als auch in den Fertigungsabläufen aus. Der werkseigene Sondermaschinenbau ist an wesentlichen Prozessschritten in der Produktion beteiligt. Reinhold Reitz ist der Verantwortliche im Werk 1 über alle in Eigenregie gebauten Sondermaschinen. Ob Sägen, Biegen, Schweißen, Schleifen oder die vollautomatisierte „Griffe- Autobahn“, in der Türgriffe in großen Stückzahlen hergestellt werden: die meisten Maschinen hat man in der hauseigenen Konstruktion geplant und in der Werkstatt gebaut. „Wir als Mitarbeiter von HOPPE kennen die Anforderungen an die Maschinen und Abläufe einfach am besten und wissen genau, worauf es ankommt. Das gesamte Know- how ist und bleibt so in unserem Unternehmen“, erklärt Reitz.
Als Herr über so viele Produktionsschritte ist man stets auf der Suche nach Optimierungen in den Abläufen und Prozessen. Der Laser als Werkzeug ist dabei natürlich eine interessante Option, bietet er doch höchste Präzision, ermöglicht sehr hohe Taktzeiten und verringert die notwendige Nachbearbeitung in vielen Anwendungen erheblich. Ein möglicher Ansatzpunkt war das Verschweißen von Vierkant-Stahleinsätzen mit Edelstahlgriffen, die bisher mit WIG-Schweißen gefügt wurden. Hier entsteht jedoch eine breite Schweißnaht, die anschließend aufwendig nachgearbeitet werden muss. Der Laser mit seiner feinen Schweißnaht und den hohen Taktzeiten versprach eine hohe Effektivität und Kosteneinsparung, so dass man sich im Markt nach Erfahrungen mit dem Laserschweißen umhörte.
Mit dem Nordrhein-Westfälischen Zulieferer Esta Rohr GmbH, der die Rohr-Halbzeuge an HOPPE liefert, ist man schon viele Jahre bekannt und hat deren Umstellung der Produktion von WIG- auf CO2-Slab-Laserschweißen aufmerksam verfolgt. „Die lasergeschweißten Rohre sind qualitativ so hochwertig, dass unsere sehr hohen Anforderungen an die Festigkeit und Toleranzen problemlos erfüllt werden“, so Reitz. Dass sie dabei günstiger sind als konventionell geschweißte Rohre ist ein erfreulicher Nebeneffekt. Mit den eigenen Überlegungen, Laser in der Produktion einzusetzen, wandte man sich an Sven Pitzer, Technischer Leiter bei Esta Rohr, um von seinen Erfahrungen zu profitieren.
Bei Esta Rohr stellte man schon 2005 die erste Rohrschweißanlage von WIG auf Laserschweißen um und hat seit einigen Jahren komplett umgesattelt. Unterstützt wurde und wird Esta Rohr dabei vom Hamburger Laserspezialisten ROFIN, der sowohl die CO2-Slab-Laserstrahlquellen als auch die Rohrschweißsysteme mit integrierter Prozesssensorik (Profile Welding System PWS) lieferte. Bereits seit mehr als 10 Jahren verbindet Esta Rohr mit ROFIN eine sehr gute und von partnerschaftlicher Zusammenarbeit geprägte Geschäftsbeziehung. „Das alles haben wir durch Herrn Pitzer natürlich gehört und uns dann ebenfalls an die Hamburger gewendet“, berichtet Reinhold Reitz. „Die ersten Kontakte waren direkt sehr positiv, so dass wir erste Versuche zur Machbarkeit in Auftrag gegeben haben“, fügt er hinzu. Darüber hinaus war ROFIN im Werk Stadtallendorf bereits bekannt, denn drei Beschriftungslaser sind seit vielen Jahren in der Produktion im Einsatz.
Die ersten Versuche zum Verschweißen von Vierkant-Stahleinsätzen mit Edelstahlgriffen im Hamburger Applikationslabor lieferten vielversprechende Ergebnisse, so dass schon bald das erste Grobkonzept der neuen Anlage im hauseigenen Sondermaschinenbau von HOPPE erstellt wurde. Von der ersten Idee bis hin zur Umsetzung und Inbetriebnahme der Laseranlage vergingen nur knapp sechs Monate, in denen Reinhold Reitz und sein Kollege und Projektleiter Manfred Ludwig insgesamt dreimal das Hamburger Applikationslabor besuchten. Versuche mit und ohne Prozessgas wurden gefahren, verschiedene Schweißparameter ausprobiert, bis schließlich die Entscheidung für einen Faserlaser ROFIN FL 015 mit 1,5 kW Ausgangsleistung gefallen war.
„Unser Ziel war die deutliche Reduzierung der Nacharbeiten an der Schweißnaht und das Ergebnis mit dem Laser hat uns hier mehr als überzeugt“, berichtet Manfred Ludwig und weiter: „Auch die vorgegebene Taktzeit von 10 Sekunden pro Schweißung war von Laserseite kein Problem.“ Reinhold Reitz ergänzt: „Das alles lief wirklich sehr reibungslos. Unsere Konstruktion hat parallel zu den Versuchen die Detailkonzepte der neuen Anlage angepasst und dann in die Realisierung weitergegeben. Die anschließende Inbetriebnahme des Lasers durch ROFIN verlief sehr angenehm und schnell“, ergänzt Reinhold Reitz.
Inzwischen ist die Anlage in die Serienfertigung eingebunden und überzeugt bis in die Geschäftsleitung hinauf mit der Kosten-Nutzen-Analyse. „Wir sind durchweg zufrieden mit unserer neuen Anlage. Und wenn ich mich hier so umschaue, habe ich noch ein paar mehr Ideen, wo uns der Laser gute Dienste erweisen könnte“, sagt Reinhold Reitz lächelnd und blickt sich in der Fertigungshalle um: die nächsten Bauteile sind bereits auf dem Weg ins Hamburger Applikationslabor.
Mehr Informationen zur Rofin-Sinar Laser GmbH:
![]() |
Rofin-Sinar Laser GmbH |
![]() |
Berzeliusstr. 87 |
![]() |
22113 Hamburg |
![]() |
Tel.: 040-73363-4380 |
![]() |
Fax: 040-73363-4138 |
![]() |
E-Mail: info@rofin.com |
![]() |
www.rofin.com |
War dieser Artikel für Sie hilfreich?
![]() |
![]() |
![]() |
![]() |
![]() |
Bitte bewerten Sie diese Seite durch Klick auf die Symbole.
Zugriffe heute: 1 - gesamt: 1847.