Besser, schneller und mobiler WIG-Schweißen
Invertertechnik von Rehm
Der Brauerei-Anlagenbauer Kaspar Schulz schweißt in Produktion und Montage ausschließlich mit der WIG-Schweißtechnik. Das Traditionsunternehmen aus Bamberg setzt dabei auf die neueste Generation von Rehm-Schweißgeräten mit Invertergesteuerter Prozesstechnik.
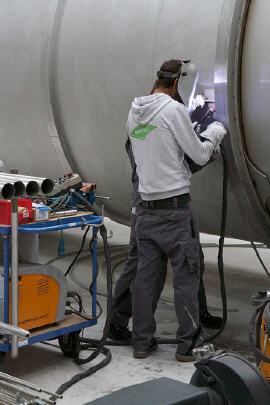
Die Firma KASPAR SCHULZ baut schlüsselfertige Brau-und Mälzungsanlagen, Gär-und Lagertanks sowie Spezialbehälter. Gegründet 1677, ist das in Bamberg angesiedelte Familienunternehmen in zehnter Generation der älteste Brauereimasch inenhersteller der Welt. Im Bereich Anlagenbau für Gasthaus- und Regionalbrauereien sowie dem stark gewachsenen Markt an Craft-Bier Brauereien ist die Firma KASPAR SCHULZ Marktführer. Eine Position, die das Ergebnis eines stetigen Optimierungsprozesses in der Fertigung ist.
Bei der Produktion der Tanks stellt das Schweißen von unterschiedlichen Materialien einen entscheidenden Produktionsschritt dar. Deshalb hat das Unternehmen bei der Ausbildung neuer Fachkräfte auch einen gesonderten Block zum Thema Schweißen eingeführt. Die Facharbeiter im Anlagen- und Behälterbau arbeiten hauptsächlich mit dem Wolfram-Inertgas (WIG)-Schweißverfahren und vertrauen dabei schon seit einem viertel Jahrhundert auf REHM Schweißgeräte.
KASPAR SCHULZ vertraut auf REHM
Dabei kommt seit Jahren die Schweißtechnologie von einem Marktführer im WIG-Bereich zum Einsatz, der Firma REHM mit Sitz nahe Stuttgart. Gründe für diese Entscheidung gibt es viele. Zum einen ist die partnerschaftliche Zusammenarbeit auf Basis einer guten Kommunikation für das Traditionsunternehmen ein wichtiger Punkt. Zum anderen arbeiten die Schweißstromquellen absolut zuverlässig, sind äußerst robust und bieten optimale Schweißeigenschaften. In der Produktionshalle arbeitet das KASPAR SCHULZ-Team mit der stationären WIG-Anlage INVERTIG.PRO digital. Aufgrund der Größe der Behälter kommen die Schweißgeräte aber oft auch vor Ort beim Kunden zum Einsatz. Hier setzt KASPAR SCHULZ auf den Weltmeister im Fliegengewicht, den WIG-Inverter TIGER ULTRA.
Neues WIG-Schweißgerät: mobil und robust
2015 war das Montage- und Serviceteam auf der Suche nach einer neuen Schweißgerätegeneration mit integrierter Wasserkühleinheit, die mobil und robust ist, aber gleichzeitig auch absolut zuverlässig arbeitet. Man entschied sich für den TIGER 230 AC/DC ULTRA von REHM, dem mit (oder auch ohne) Wasserkühleinheit kleinsten und leichtesten Gerät in der Profi-Klasse. Neben der Mobilität war für den Anlagenbauer KASPAR SCHULZ aber vor allem Unempfindlichkeit ein entscheidendes Auswahlkriterium. Bei Montageeinsätzen ist die Belastung um ein Vielfaches höher als im Werkstatteinsatz.
Der neue TIGER verfügt über ein Kühlsystem, das eindringende Schmutzpartikel sicher durch den integrierten Kühlkanal ableitet. Das robuste Kunststoffgehäuse fängt selbst massive Schläge sicher ab. Auch Stürze aus bis zu 90 cm Fallhöhe hält das Trägersystem problemlos aus. Damit ist die Elektronik im Inneren bestens geschützt. Die übersichtliche und intuitive Bedienung erleichtert die Arbeit des Montageteams zusätzlich.
Modernste Inverter-Prozesstechnik spart Zeit und sichert Produktqualität
In der Schweißpraxis der Firma KASPAR SCHULZ müssen vor allem Kehl- und Stumpfnähte bei V2A/V4A-Werkstoffgruppen wie 1.4571 oder 1.4404 bzw. 1.4435 mit meist über 3 mm dicken Blechdicken waagerecht fallend oder stehend mit Zusatzwerkstoff verschweißt werden. Schon nach einer kurzen Testphase hat sich das Einsatzteam auf den neuen WIG-Inverter TIGER konzentriert. Die hohe Taktfrequenz des Primärinverters ermöglicht sehr spezifische Prozessvarianten. Diese vorprogrammierten Prozesstechniken hatten bei KASPAR SCHULZ schneller zum gewünschten Schweißergebnis geführt.
Um ein besseres Abschmelzen des Zusatzwerkstoffs und ein besseres Ausfließen an den Flanken zu erreichen, nutzt das Montageteam z. B. bei dünneren Blechdicken die DC HYPER.PULS-Technik bzw. bei größeren Blechdicken ab 5mm die AC HYPER.PULS-Technik, jeweils mit/ohne DUAL.WAVE. Im DUAL.WAVE Betrieb wird zwischen konventionellem AC-Schweißen und einer Gleichstromphase umgeschaltet.
Optimale Ergebnisse dank HYPER.PULS-Technik
Pulsprozesse werden auch von anderen Geräteherstellern angeboten. Doch nur der Inverter von REHM bietet eine HYPER.PULS-Technik mit bis zu 17,5 kHz. Erst bei dieser Pulsfrequenz spielt der Pulslichtbogen seine physikalischen Vorteile voll aus. Auch beim Verschweißen von 1 mm Bauteilen aus Kupfer kann mit HYPER.PULS viel schneller mit weniger Wärmeausdehnung gearbeitet werden. Die Praxiserfahrungen bei KASPAR SCHULZ zeigten, dass die HYPER.PULS-Technik einen sehr stark fokussierten, stabilen Lichtbogen erzeugt. Mit ihm konnte der Schweißer den Wärmeeintrag besser kontrollieren. Bessere Fließeigenschaften waren die Folge. Das sind optimale Bedingungen für eine schmale, gleichmäßige Naht. „Gerade in unserer Branche ist die Optik ein entscheidender Faktor. Die Schweißnähte bleiben am Ende oftmals sichtbar. Die müssen sitzen“, so Fabian Schwab, Ausbilder bei KASPAR SCHULZ.
Weil rund zehnProzent weniger elektrische Leistung zugeführt werden muss, ist das Schweißen in Zwangslagen zudem einfacher. Mit der Kombination DUAL.WAVE & HYPER.PULS ist dank der Prozessumschaltung auch die Schuppung gleichmäßiger. Außerdem entstehen weniger Poren, weil das Schmelzbad während der DC-Phase besser ausgasen kann. Das bedeutet wiederum mehr Sicherheit beim Schweißen von Tanks, die zu 100 Prozent dicht sein müssen.
Dank des sinusförmigen Stromverlaufs folgt der Lichtbogen exakt der Schweißnaht. Schnelleres Schweißen ist die Folge. Die Firma KASPAR SCHULZ erzielte dadurch eine zweistellige Steigerungsrate bei der Produktivität. Ein Ergebnis, das KASPAR SCHULZ überrascht hat, wie Jürgen Hofmann, Schweißwerkmeister SLV betont: „Dass das Schweißen noch besser als mit dem Vorgänger geht, hätten wir nicht erwartet. Das ist für uns ein weiterer Schritt nach vorne.“
Mehr Informationen zur REHM GmbH u. Co. KG:
![]() |
REHM GmbH u. Co. KG Schweißtechnik |
![]() |
Ottostraße 2 |
![]() |
73066 Uhingen |
![]() |
Tel.: (07161) 30 07-0 |
![]() |
Fax: (07161) 30 07-20 |
![]() |
E-Mail: rehm@rehm-online.de |
![]() |
www.rehm-online.de |
War dieser Artikel für Sie hilfreich?
![]() |
![]() |
![]() |
![]() |
![]() |
Bitte bewerten Sie diese Seite durch Klick auf die Symbole.
Zugriffe heute: 1 - gesamt: 2136.