Blitzschneller Filterbau
Verarbeitung von bis zu 200 Blechrahmen pro Minute
Bis zu 200 Blechrahmen pro Minute verarbeitet eine neue Automationszelle von MartinMechanic, die in der Umweltindustrie zum Einsatz kommt. 15 bis 75 solcher perforierten Bleche, die die Anlage übereinanderstapelt, bilden je nach Anforderung einen Filter. Mit seiner Hilfe kann Altöl aufbereitet werden.
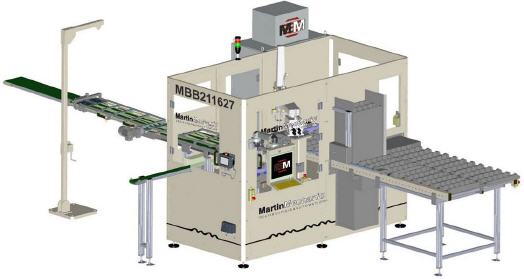
In diesem Fall werden durch die Anlage MBB211627 zunächst immer die Zubehörteile für zwei Filter mit den Außenmaßen 20 mal 14 Zentimeter in Blistern parallel aufeinandergeschichtet. Die Größe der Filter und die Abstände der Blechrahmen hängen von der Viskosität des zu reinigenden Mediums und davon ab, wie dicht der Filter sein muss. Über die SPS-Steuerung S7-1500 lassen sich Chargenanzahl und die jeweilige Variante anwählen.
Dafür wurde ein 19 Zoll großes Komfort-Touchpanel an einem Kragarm fest montiert, damit die optimale Zugänglichkeit stets gegeben ist. Für die Produktion der Filtermodule ist der Scara-Roboter XG1000 vom Typ Omron-Yamaha im Einsatz, der über eine Reichweite von 1000 Millimeter verfügt und eine maximale Traglast von 20 Kilogramm hat.
Schon die Zuführung erfolgt mit sehr hoher Geschwindigkeit. Mit drei Meter pro Sekunde bewegt sich das Pressenauslaufband, auf dem die Blechrahmen zur Weiterverarbeitung Richtung Automationszelle geschoben werden. Dort treffen die Bauteile auf eine Wendeeinheit. Der Stopper über dem Laufband wird durch einen Zylinder angesteuert, der synchron zur Noppensteuerung der Presse läuft.
Jeder Rahmen wird in einem 90-Grad-Winkel abgewendet. Allerdings hat jeder zweite die exakt entgegengesetzte Orientierung, damit die Rahmen anschließend passend übereinandergesetzt werden können. Wegen der hohen Geschwindigkeit werden die Blechrahmen durch eine Einlaufkurve geführt, damit sie ordnungsgemäß im Stapelschacht ankommen. Ein Sensor erkennt die jeweiligen Teile, so dass sich der Schacht immer automatisch um die Höhe des Blechrahmens, in diesem Fall vier Millimeter, absenkt.
Ist ein Stapel voll, nimmt eine Hubeinheit das Filtermodul auf und legt es auf dem darunterliegenden Taktband ab. Das Taktband schiebt das Filtermodul zur Prüfstation. Anhand der Bildverarbeitung werden die Stapelhöhe, die Anzahl der übereinanderliegenden Blechrahmen und ihre alternierende Anordnung erkannt. Die wechselnde Laufrichtung ist später für das optimale Filtern wichtig.
Ist ein Stapel eventuell nicht ganz korrekt angeordnet, gibt es dafür zwei mögliche Szenarien. Der Werker entscheidet sich vorab per SPS-Steuerung und Touchpanel, welche Variante ausgeführt werden soll: Entweder die Anlage geht bei einer eventuellen Fehlproduktion in einen geplanten Stopp oder der Roboter greift automatisch nach dem unfertigen Modul und legt es auf ein spezielles Austrageband.
Die Filtermodule, die in Ordnung sind, legt der Roboter in einem Blister ab. Dafür werden die leeren Blisterstapel auf dem Zutrageband in der Depalettierstation vereinzelt und dem Roboter nacheinander an der Beladestation zugeführt. Jeder einzelne Blister wird mit 12 übereinandergestapelten Filtermodulen bestückt.
Das Austrageband befördert die gefüllten Blister in Längsrichtung bis zur Palettiereinheit, die sie nach dem FiFo-Prinzip (First In – First Out) von unten nach oben übereinanderstapelt. Immer das zweitunterste Tray wird in die Höhe gehoben, damit ein neues nachgeschoben werden kann. Je nach Filtervariante kann die Anlage bis zu zehn Blister schichten. Der komplette Stapel fährt schließlich auf einem Transportband aus der Anlage. Er wird vom Werker manuell auf einen Transportwagen gezogen und arretiert. Anschließend werden die fertigen Filtermodule an die Logistik übergeben.
Die MBB211627 ist bereits die dritte Anlage ihrer Art. Entsprechend konnte die Konstruktionszeit auf sieben Monate verkürzt werden. Ihr Vorgängermodell wurde hinsichtlich der Zugänglichkeit und einer deutlich höheren Leistung verbessert. Außerdem konnte die Stellfläche der Anlage, ohne die Transportbänder gerechnet, platzsparend auf 15 Quadratmeter verkleinert werden. Die autarke Laufzeit wurde auf 15 Minuten erhöht.
Mehr Informationen zur Friedrich Martin GmbH:
![]() |
Friedrich Martin GmbH & Co KG |
![]() |
Hauptstrasse. 25 |
![]() |
72202 Nagold |
![]() |
Tel.: +49(0) 74 52-84 66-0 |
![]() |
Fax: +49(0) 74 52-84 66-5 66 |
![]() |
E-Mail: info@MartinMechanic.com |
![]() |
www.martinmechanic.com |
War dieser Artikel für Sie hilfreich?
![]() |
![]() |
![]() |
![]() |
![]() |
Bitte bewerten Sie diese Seite durch Klick auf die Symbole.
Zugriffe heute: 1 - gesamt: 2133.