Automatisierung trifft flexible Fertigung
Deutliche Effizienzsteigerung in der Produktion
Zuidberg in den Niederlanden macht dank Toyoda Machinery Europe seine Zerspanung für Serienteile und Prototypen effizienter.
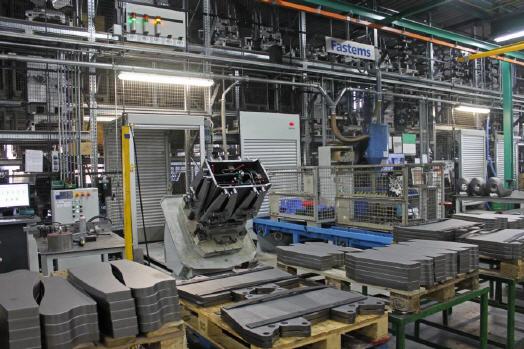
Eigentlich passen Automatisierung und kleine Stückzahlen nur schwer zusammen. Doch Zuidberg, ein niederländischer Hersteller von Frontkrafthebern und verschiedenen Traktorenkomponenten, konnte mithilfe von Toyoda Machinery Europe eine flexible Fertigung automatisieren. Das Ergebnis ist eine deutliche Effizienzsteigerung in der Produktion, und gleichzeitig konnte Zuidberg auch im Kampf gegen den Fachkräftemangel entscheidend punkten.
In Ens, nahe dem IJsselmeer, produziert Zuidberg neben den Frontkrafthebern auch landwirtschaftliche Raupenlaufwerke sowie Getriebe und Antriebslösungen und setzt mit 320 Mitarbeitern rund 50 Millionen Euro im Jahr um. Die Fertigungs-Tochter Zuidberg Machining B.V. ist eine wichtige Säule des gesamten Unternehmens. 65 Mitarbeiter sind hier im Bereich Zerspanung beschäftigt.
Erwin Stremmelaar ist seit mehr als 10 Jahren Produktionsleiter bei Zuidberg Machining, „und in der Zeit ist viel passiert“. Das neueste Projekt ist eine flexible Automatisierungslinie, in der Bearbeitungszentren von Toyoda in ein „Flexible Manufacturing System“ von Fastems integriert wurden. Auf rund 50 Metern Länge streckt sich die haushohe Linie quer durch die Fertigungshalle.
Bis zu 400 kg schwere Gussteile Vor drei Jahren entstand das Projekt – „Auslöser war die Anfrage eines Traktorenherstellers, für den wir bis zu 400 Kilogramm schwere Gussteile bearbeiten sollten“, erinnert sich Stremmelaar. Diese Teile waren für eine bereits bestehende automatisierte Fertigungslinie zu groß, so dass Zuidberg in eine zweite Anlage investierte.
Diese verfügt nun über 800 mm große Paletten, die jeweils mit bis zu vier schweren Gussteilen gleichzeitig bestückt werden können. Die Bauteile werden hydraulisch mit 500 bar gespannt und in ein Lager „gefahren“, wo sie auch nach Wochen noch mit mindestens 400 bar fest sitzen. Dies wird automatisch geprüft und überwacht. Je nach Produktionsablauf bewegen sich die bis zu 2,5 Tonnen schweren Paletten zu einer der beiden Toyoda FH800SX-i Bearbeitungszentren, in denen die Gussteile zerspant werden.
„Die Toyoda FH800SX-i ist sehr stabil und kann die schweren Paletten gut aufnehmen“, erklärt Stremmelaar. Dass sich Zuidberg für die Bearbeitungszentren von Toyoda entschieden hat, lag neben dem technischen Anspruch auch an der guten Erfahrung mit der Qualität aus Japan. „Wir haben bereits seit 2008 auf einer anderen automatisierten Strecke Toyoda (Mitsui Seiki)Maschinen sehr erfolgreich im Einsatz“, erklärt Stremmelaar. „Selbst ein Bearbeitungszentrum aus dem Jahre 2001 ist noch voll in der Produktion.“ Auch in die Integration der Bearbeitungszentren mit dem Fastems-System hat ohne Probleme funktioniert. Und auch im Bereiche Servicequalität ist Stremmelaar sehr zufrieden: „Wenn wir Toyoda brauchen, ist immer jemand verfügbar.“
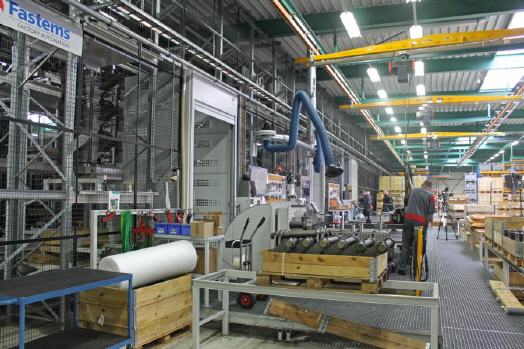
Bis zu 75 Werkzeuge pro Bauteil
Für eine noch effizientere Zerspanung sind die Bearbeitungszentren mit einem Cellro Werkzeug-Magazin (Toolchanger) ausgestattet. „Auf wenig Fläche stehen hier zusätzlich 304 Werkzeuge zu Verfügung“, so Peter Hellmond, Manager Sales & Marketing bei Toyoda Machinery Europe.
Die rotierenden Werkzeugtürme versorgen mit einem Roboter die Maschinen mit den benötigten Fräsern und Bohren deutlich schneller als ein herkömmliches Kettenmagazin. „Mit Cellro erreichen wir einen Werkzeugwechsel in 6 bis 20 Sekunden.“ Ein entsprechend großes Kettenmagazin liege mit 35 bis 40 Sekunden deutlich darüber. „Für uns ist das eine deutliche Zeiteinsparung“, freut sich Stremmelaar, denn im Schnitt werden bei Zuidberg rund 20 bis 30 Werkzeuge pro Bauteil benötigt, „bei manchen sogar bis zu 75.“ Gerade bei einer Automatisierung, die für viele verschiedene Teile ausgelegtet ist, entfalte das System so deutliche Vorteile. Zudem können auch Schwesterwerkzeuge vorrätig gehalten werden.
Die Zeiteinsparung durch die automatisierte Zerspanung hat die Produktion bei Zuidberg so effizient gemacht, dass immer mehr Bauteile auch von externen Kunden bearbeitet werden. „Denn unser Ziel ist, Geld zu verdienen, so einfach ist das“, schmunzelt Stremmelaar. „Und das schafft man eben nur wenn sich die Spindel bewegt“, ergänzt Hellmond.
Auf der automatisierten Anlage werden neben den schweren Gussteilen auch Biege- und Schweißteile für eigene Produktion gefertigt. Das umfasst sowohl Serien mit bis zu 3000 Teilen wie auch Einzelteile und Prototypen. „Um uns hierfür die nötige Flexibilität zu schaffen, haben wir in die Anlage auch eine zweite Toyoda FH800SX-i integriert“, sagt Stremmelaar. „Aufgrund der vielseitigen Anforderungen erreichen wir damit eine höhere Prozesssicherheit und können die Prototypen parallel zu Serienproduktion fertigen.“
Vorteile beim Fachkräftemangel Die gesamte Anlage ist soweit automatisiert, dass nur beim Bestücken sowie bei Werkzeugkontrolle und -wechsel Mitarbeiter im Einsatz sind. Das schafft für Zuidberg ein weiteres Plus: Die relativ schnelle Mitarbeiterqualifikation ermöglicht eine flexiblere Auswahl neuer Mitarbeiter.
Gleichzeitig kann Zuidberg dank der hohen Automatisierung den Mitarbeitern in der Fertigung eine 4-Tage-Woche anbieten. Ein Trumpf für das dynamisch wachsende Unternehmen, denn auch in den Niederlanden werden Fachkräfte immer knapper und mittelständische Unternehmen müssen sich mit cleveren Ideen auf dem Markt um die besten Köpfe beweisen.
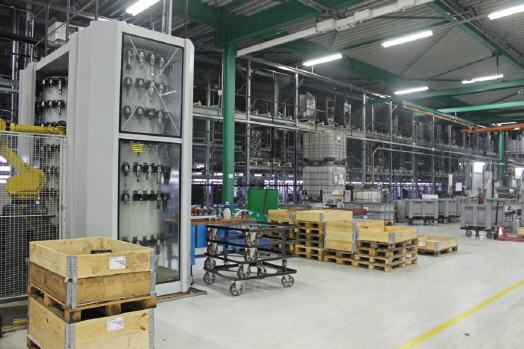
Mehr Informationen zu Lerinc:
![]() |
Lerinc Werkzeugmaschinen & Automation GmbH |
![]() |
Carl-Zeiss-Strasse 22 |
![]() |
42589 Heiligenhaus |
![]() |
Tel.: +49-(0)-20 56-9856-0 |
![]() |
Fax: +49-(0)-20 56-9856-25 |
![]() |
E-Mail: info@lerinc.de |
![]() |
www.lerinc.de |
War dieser Artikel für Sie hilfreich?
![]() |
![]() |
![]() |
![]() |
![]() |
Bitte bewerten Sie diese Seite durch Klick auf die Symbole.
Zugriffe heute: 1 - gesamt: 2521.