Der Weg zum Top-Werkzeug
Umfassend testen, Fehler vermeiden
Gerade im Zerspanungsbereich sind Innovationen extrem wichtig, um auch künftig wirtschaftlich zu fertigen und wettbewerbsfähig zu bleiben. Insbesondere bei den Schneidwerkzeugen ist die Innovationskraft enorm. Hersteller wie Dormer Pramet beschäftigen sich permanent mit der Entwicklung von neuen Werkzeugen, WSP-Geometrien und Schneidstoffen: von dem breiten Produktprogramm mit über 35.000 kataloghaltigen Artikeln, sind z. B. beim Drehen 70 Prozent in den letzten fünf Jahren entstanden. Wie so ein neues Schneidwerkzeug konkret entwickelt wird, soll an den SBN10-Fräsern und BNGX-Wendeschneidplatten von Dormer Pramet gezeigt werden.
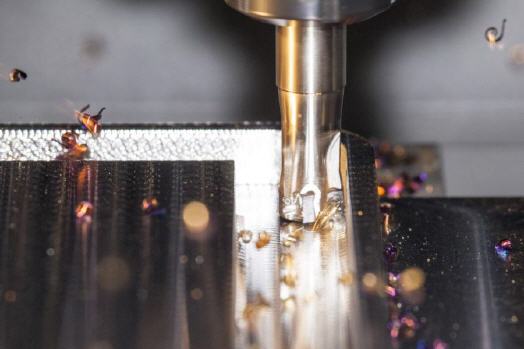
Die Abteilung für Produktmanagement und -entwicklung wird jedes Jahr marktnah und kundenspezifisch mit der Entwicklung neuer Werkzeuge beauftragt. Als im Januar 2015 Jan Bittner als Produkt- und Entwicklungsingenieur neu ins Team im Tschechischen Šumperk kam, war seine erste Aufgabe, die Entwicklung eines Sortiments von HochleistungsFräswerkzeugen. Es brauchte knapp drei Jahre, bis eine komplett neue Produktreihe von SBN10-Fräsern und BNGXWendeschneidplatten am Zerspanungsmarkt lanciert werden konnte. An der Produktentwicklungszeit lässt sich auch ablesen, wie hoch die Investitionen eines Herstellers waren.
Grundsätzlich startet das Produktmanagement den Prozess für die Erstellung eines neuen Werkzeugs mit der Ermittlung der Marktbedürfnisse sowie den Lücken im eigenen, aktuellen Sortiment. Karel Tiefenbach, Produktmanager für das Fräsen mit Wendeschneidplatten, hatte dafür ein spezielles Konzept mit klaren Zielvorgaben für das Entwicklungsteam erstellt. Die Herausforderung: das Team sollte ein Sortiment an Werkzeugen für Doppelt-Negative-Schneidwerkzeuge entwickeln, um den Kunden durch höhere Vorschubgeschwindigkeiten einen zusätzlichen Produktivitätsschub zu ermöglichen.
Das Werkzeugdesign sollte für die doppelseitigen WSP-Einsätze passend sein, um den wirtschaftlichen Aspekt der vier Schneidkanten werkzeugseitig zu maximieren und zudem mit einem höheren Rampwinkel eine optimale Spankontrolle bieten. Mit einem vielseitigen Fräsersortiment fokussierte das Entwicklerteam vor allem auch den Werkzeug- und Formenbau an, um hochproduktive und prozesssichere Werkzeuge für die Schrupp- bis Fertigbearbeitung vorzuhalten.
Entwicklungsingenieur Jan Bittner setzte sich anfangs mit Jan Vlcek von der Produktdesign- und Informationsabteilung zusammen. Sie sondierten den Markt der Mitbewerber nach gleichwertigen Fräsern, ermittelten den Kundenbedarf und erweiterte Anforderungen an das geplante HochvorschubFräsersortiment – später als SBN10 bekannt. Jan Bittner erinnert sich zurück: "Wir haben mit Vorstudien und ersten Prototypen begonnen und eine Reihe von Ideen vorgestellt, bevor wir erste Muster fertigten. Bei einer neuen Entwicklung heißt es immer, Schwierigkeiten und Herausforderungen zu überwinden, doch können einige kleine Änderungen in diesem frühen Entwicklungsstadium später große Auswirkungen haben.“ So habe man bspw. bei einem ersten Muster auch festgestellt, dass ein Konflikt mit dem Patent eines Wettbewerbers besteht.
Da viele Unternehmen ständig neue WSP entwickeln, ist der Markt überfüllt. "Wir haben jedoch mit dem Designer eng zusammengearbeitet, um unser Konzept schließlich so zu verändern, dass es einzigartig ist und gleichzeitig die ursprüngliche Aufgabe erfüllt“, erklärt der Entwicklungsingenieur. Zudem waren die Kollegen in Schweden und Nordamerika eng eingebunden, zusammenzuarbeiten, um auch wirklich sicherzustellen, dass das neue WSP-Design nicht mit irgendwelchen Patenten kollidiert. "Wir haben zudem mit Kollegen aus dem Bereich IP (Intellectual Property, geistiges Eigentum) darüber gesprochen, wie wir unser Design einzigartig machen können, und dies war eine ganz neue Erfahrung für mich.“ So habe das Entwicklerteam um Jan Bittner in jeder Phase mit der IP über das Design diskutiert und geringfügige Änderungen vorgenommen. „Wir mussten bestätigen, dass wir in jeder Entwicklungsstufe zum Patent angemeldet waren und nicht im Widerspruch zu anderen bereits eingereichten Dokumenten standen. Schließlich bekamen wir das Okay, weiterzumachen.“
Als das Projekt 2015 startete, war die Zeitvorgabe bis mit den neuen BNGX-Einsätzen bis November 2017 auf den Markt zu kommen. „Wir hatten jedoch Druck von unseren Vertriebsteams, die die Wendeschneidplatten früher wollten! Unser Ziel war es, den Prozess so schnell wie möglich voranzutreiben und wir haben den Zeitplan eingehalten“, freut sich Werkzeugentwicklungsingenieur Jan Bittner. Bis Mitte 2016 lief die Testphase. Wichtig dabei waren umfasste Feldversuche mit Kunden. „Nur so können wir die Praxistauglichkeit überprüfen. Zwar waren wir zuversichtlich, dass es ein gutes Produkt ist, aber keine Tests in unserem eigenen Entwicklungscenter in Šumperk können praxisnahe Anwendungsfälle beim Kunden ersetzen.“ Schließlich habe man aus den Praxistests so viel gelernt, dass weitere Produktverbesserungen identifiziert werden konnten.
Ein Beispiel war der Test bei einem Kunden in Frankreich, bei dem ein titanhaltiger, austenitischer, Chrom-Nickel-Edelstahl bearbeitet wurde – ein extrem zähes und duktiles Material. Der Zerspanungsprozess erfordert eine leistungsstarke Maschine, die zu hohen Vorschüben bei langsamen Spindeldrehzahlen fähig ist. "Wir haben es mit einem HochvorschubFräswerkzeug eines Wettbewerbers verglichen, das ähnliche Eigenschaften wie unser SBN10 aufweist.“
Und das Ergebnis konnte sich sehen lassen: Nach der Bearbeitung von drei Teilen war die Schneidkante der Mitbewerber-WSP verschlissen, was den Bediener zwingt, die Schneidkante zu prüfen und zu wechseln, um die Produktion fortzusetzen. Nach der Bearbeitung von acht Teilen mit den Schneidplatten SBN10 und BNGX zeigte die Schneidkante nur einen geringen Flankenverschleiß und war noch in einem guten Zustand, um weiter zu zerspanen.
Jan Bittner präzisiert: "Neben deutlich längeren Standzeiten war die Zerspanungsrate um 20 Prozent höher. Der Kunde war so beeindruckt, dass er sofort einen der neuen Fräser kaufte und Anfang 2018 sieben weitere vorbestellte.“ Am Ende hatte das Entwicklerteam über 20 Praxistests mit Kunden in Frankreich, Brasilien, Polen, China, Italien, Tschechien und Deutschland durchgeführt. Insgesamt erfüllten fünf dieser Tests nicht die Erwartungen, halfen aber dem Team bei der weiteren Produktverbesserung. „Die Tests sind für uns ein wichtiger Prozess, denn schließlich tragen sie unmittelbar dazu bei, die Produktleistung zu verbessern und Einschränkungen zu reduzieren.“
Entscheidend sei dabei, so schnell als möglich während des Testprozesses zu reagieren, Probleme zu beseitigen und das Design des Werkzeugs zeitnah zu verbessern, bevor es für weitere Tests wieder eingesetzt wird. "Im Juli 2017 sind wir nach Deutschland zu einem Kunden zurückgekehrt, bei dem einer der Tests nicht so gut lief. Wenn wir zum selben Ort zurückkehren, können wir genau die gleichen Prüfbedingungen herstellen. Dies ist wichtig, um zu überprüfen, ob die Verbesserungen, die wir vorgenommen haben auch Wirkung zeigen. Der Anwendungsfall lief sehr erfolgreich und es war großartig, dem Kunden die neue und verbesserte Version zu präsentieren.“
Das war dann auch der Zeitpunkt, um das neue Produkt auf den Markt zu bringen. Zuvor wurde nochmals mit der IP geklärt, dass das Patent vorliegt und alles für den Markteintritt vorbereitet ist. Mit der Produktion wurde sichergestellt, dass auch genügend Wendeschneidplatten für den Zeitpunkt der Einführung produziert werden können. Darüber hinaus unterstützte das Produktmanagementteam Marketing- und Kommunikation bei der Erstellung des gesamten Informationsmaterials mit Broschüren, Bildern, Videos, Pressemitteilungen und Internet-Content.
Schließlich konnte Dormer Pramet seine Produktpalette an BNGX-Wendeschneidplatten und SBN10-Fräsern pünktlich im November 2017 präsentieren, sprich fast drei Jahre nach der ersten Konstruktionsvorbereitung. Bis Ende 2018 produziert das Werk im Tschechischen Šumperk mehr als 30.000 BNGXWendeschneidplatten in verschiedenen Größen und Spanbrechern sowie 450 Fräser in drei verschiedenen Varianten: Schaftfräser mit Gewindeschaft, Schaftfräser mit Zylinderschaft sowie Aufsteckfräser.
Jan Bittner resümiert: "Produktentwicklung ist sehr viel Teamarbeit. Es sind viele Kollegen auf der ganzen Welt, die an der Entwicklung unserer neuen Schneidwerkzeuge beteiligt sind. Vom Produktmanagement über das Design, die Technologieteams, Produktion, Testphasen bis hin zu Vertrieb und Marketing. Keine Abteilung ist unabhängig von den anderen. Wir sind alle miteinander verbunden, kein Bereich kann ohne die Unterstützung der anderen erfolgreich sein. Alle müssen zusammen an einem Strang ziehen, um ein Produkt erfolgreich am Markt lancieren zu können. Unsere Aufgabe im Produktmanagement eines Präzisionswerkzeugherstellers ist es, in die Zukunft zu blicken, was benötigen die Kunden, was wird in fünf bis zehn Jahren wichtig sein."
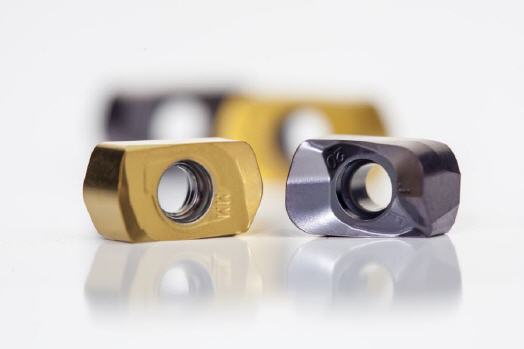
Mehr Informationen zu Dormer Pramet:
![]() |
Dormer Pramet |
![]() |
Am Weichselgarten 34 |
![]() |
91058 Erlangen |
![]() |
Tel.: +49 (0)9131 9330874-0 |
![]() |
E-Mail: isabel.hagen@dormerpramet.com |
![]() |
E-Mail 2: info.de@dormerpramet.com |
![]() |
www.dormerpramet.com |
War dieser Artikel für Sie hilfreich?
![]() |
![]() |
![]() |
![]() |
![]() |
Bitte bewerten Sie diese Seite durch Klick auf die Symbole.
Zugriffe heute: 1 - gesamt: 2298.