Hardinge setzt neuen Massstab
Markteinführung des Hochleistungs-Drehzentrum T 42
Mit der Markteinführung des Hardinge SUPER-PRECISION T-42 Drehzentrums gelingt Hardinge im Hartdrehen und im Fräsen ein weiterer Schritt zur Steigerung der Produktionskapazität im Genauigkeitsbereich von weit unter einem Mikrometer.
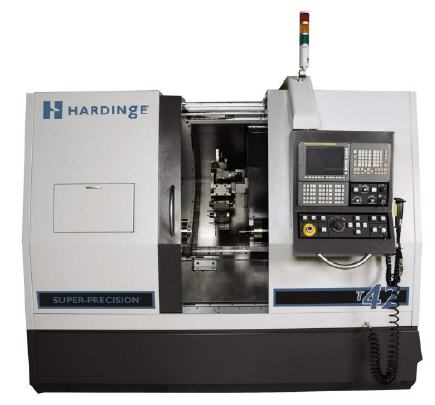
Hochleistungs-Drehzentrum T 42 von Hardinge
(Bild: Hardinge)
Die vom Hardinge-Konzern bei der AMB 2010 in Stuttgart vorgestellte Maschine setzt mit einer Achswiederholgenauigkeit von 0,76 µm, Rundheit von 0,25 µm, Prozessfähigkeit innerhalb von 3 µm bei feinster Oberflächengüte von 0,15 µm, einen neuen Maßstab in der "Nano"-Präzisionsbearbeitung.
Die T 42 wurde mit dem Ziel Einsparungen in Bezug auf Kosten und Durchlaufzeit bei der Herstellung komplexer Bauteile entwickelt, die für die hoch anspruchsvollen Bereiche der Luftfahrt, der Verteidigung, der Medizin und der Automobilherstellung typisch sind. Wichtigster Aspekt bei der Entwicklung war jedoch, ein Drehzentrum zu konzipieren, das Konstanz und Qualität dadurch erhöht, dass Arbeitsgänge kombiniert und insbesondere Hartdrehen und Fräsen in einem Zyklus zusammengefasst werden.
Die Leistungsfähigkeit der Hardinge T-42 liegt hier in ihrer modularen Bauweise, die es dem Maschinenhersteller ermöglicht, sie vorab für den jeweiligen Einsatz und auf die kundenspezifische Anwendung zu konfigurieren. Von der einfachen Zweiachsen-Version mit Reitstock bis hin zu einer genau zweckbestimmen Mehrachsen-Ausführung mit zwei Spindeln, C- und Y-Achse sowie bis zu 16 angetriebenen Werkzeugen mit Drehzahlen bis zu 16.000 U/min ist jede Ausstattung möglich. Spezielle Werkzeughalter in Verbindung mit der Revolverkopfschaltung auf Zwischenstationen ermöglichen bis zu 32 verschiedene Werkzeugpositionen. Verschiedenste automatische Entladesysteme stellen sicher, dass die Bauteile beim Verlassen der Maschine nicht beschädigt werden.
Hardinge verfügt über langjährige Erfahrung im Hochge-nauigkeitsdrehen, wenn es um die Einhaltung engster Toleranzen, bei der Arbeit mit Superlegierungen, Aluminiumsonderlegierungen und gehärteten Materialien geht, die sich von der speziellen Auslegung des Maschinenbettes her ergeben. Und das nicht nur bei der Erstfertigung von Präzisionswerkstücken, sondern auch langfristig durch die Gewährleistung von Konstanz bei jedem einzelnen Teil und mit guten und vorhersagbaren Standzeiten.
Die Hardinge SUPER-PRECISION T-42 bringt diese Technologie gewaltig voran: 45° Schrägbettanordnung, rippenverstärkter, in einem Stück gegossener Fuß, armiert mit Hardinges HARCRETE Polymerbeton. Das Maschinenbett absorbiert durch diese Art der Konstruktion Schwingungen und Verformungen. Durch ein Gewicht von weit über sechs Tonnen bietet es eine höchst stabile und unnachgiebige Plattform für äußerst lange Haltbarkeit. Unsere Erfahrung zeigt, dass dadurch die Lebensdauer der Schneidwerkzeuge bis zu 30 Prozent mehr betragen kann, als bei einem normalen Maschinenbett.
Hochleistungs-Rollenführungen auf der E-Achse verbessern die Steifheit und Unnachgiebigkeit zusätzlich, während sich Peripheriegeräte wie Kühlmittelpumpen, Filterung, Schaltschrank und Hydraulikversorgung auf einer etwa 50mm vom Maschinenbett entfernt installierten Einheit befinden. So wird verhindert, dass sich Hitze und Schwingungen auf das Maschinenbett und den eigentlichen Arbeitsraum übertragen. Großzügig dimensionierte Kugelrollspindeln mit 32 mm Durchmesser beschleunigen die X-Achse auf bis zu 24 m/min, die Z- und E-Achse auf 30,5 m/min und die Y-Achse auf 6 m/min. Lineare Glasmaßstäbe von Heidenhain mit 0,1µ Auflösung gehören zur Grundausstattung.
Hardinges eigene BMT-45 Werkzeugplatte erlaubt den Einsatz von angetriebenen Werkzeuge auf allen 16 Revolverstationen. Sie verfügt über einen Zapfenantrieb und spezielle Werkzeughalter, die die Aufnahme modular einsetzbarer angetriebener und statischer Werkzeuge ermöglichen. Der Revolverkopf kann auch auf halber Station arretiert werden, was die Anzahl der Werkzeugplätze auf 32 erhöht und so größtmögliche Flexibilität bietet und Einschränkungen bei komplexen Anforderungen durch kombinierte Betriebsvorgänge in einem Zyklus verhindert.
Der Riementrieb zu den drehenden Werkzeugen erfolgt über einen 3,7 kW-Motor mit 33 Nm Drehmoment. Die Standardgeschwindigkeit beträgt 8.000 U/min. Für Kleinstwerkzeuge sowie Diamant- und CBN-Werkzeuge kann sie durch Übersetzungsveränderungen auf bis zu 16.000 U/min erhöht werden. Die BMT-45 macht es auch möglich, Werkzeuge mit verbessertem Rundlauf innerhalb von 3 µm einzusetzen und gehört somit zur Besten ihrer Klasse. Hierdurch wird nicht nur die Zahnbelastung am Schneidwerkzeug ausgeglichen und somit dessen Lebensdauer verlängert, sondern gleichzeitig auch eine stets ausgezeichnete Oberflächengüte erzielt. Die Indexierung erfolgt schnell innerhalb 1 Sek. (geklemmt), Hochdruckkühlung durch das Werkzeug von bis zu 80 bar ist verfügbar.
Für die BMT-45 ist eine Reihe von speziellen angetriebenen Werkzeughaltern verfügbar, so dass eine Radialbearbeitung mit interner oder externer Kühlung, 90 Grad-Angriffswinkel, beidseitige axiale Enden-Bearbeitung und ein unter einem um ± 90 Grad einstellbarer Winkel möglich werden.
Der Einsatz einer unabhängigen Y-Achse mit einem Verfahrweg von 84 mm (+50 mm, -35 mm) erleichtert die Feineinstellung für punktgenaue Werkzeuganordnung, sie ist ein weiterer Faktor für eine konstante Bearbeitung. Die Minimierung des Achsversatzes, im Gegensatz zu Maschinen mit der konventionellen "Keil"-Variante, ist ein wichtiger Pluspunkt.
Die Leistungsfähigkeit der Spindeln war schon immer eine von Hardinge´s starken Seiten. Bezieht man die Vorteile der Spannzangen-Spindel mit ein, so trägt diese wesentlich zur Erhöhung der Steifheit,
Dämpfung und zur Verbesserung der Präzision bei. Dies gelingt nicht zuletzt dadurch, dass durch den konstruktiven Aufbau eine Bearbeitung nah an oder sogar im Bereich der Spindellagerung möglich ist. Sowohl die Hauptspindel als auch die Gegenspindel sind gleichermaßen mit Motorspindeln versehen, die 11 kW Leistung, 101 Nm Drehmoment bei 6.000 U/min liefern.
Die so konstruierte Spindel ermöglicht ein schnelleres Beschleunigen und Anhalten, ein integrierter Kühler trägt zusätzlich zur thermischen Stabilität bei. Die Spannfuttergröße beträgt 150 mm, die Stangenkapazität 42 mm und der maximale Bearbeitungsdurchmesser beläuft sich auf 315 mm bei 368 mm Drehlänge. Die Spindelbohrung hat einen Durchmesser von 48 mm.
Aufgrund der Anforderung der zu produzierenden Komponenten hat Hardinge ein eigenes System zur Teileentnahme entwickelt, wodurch Kratzer oder Beschädigungen am Werkstück vermieden werden. Der Teilegreifer verfügt über Nylon-Einlagen, die ein "sanftes" Entnehmen und Positionieren auf dem integrierten Teileförderer ermöglichen. Die Teile werden dann zur linken Seite der Maschine transportiert, wo sie manuell entnommen oder an einen Einlege- und Entnahmeroboter weitergeleitet werden können, was den unbeaufsichtigten Betrieb mit Stangenvorschub erlaubt. Eine Automation über eine Portallösung ist alternativ ebenfalls möglich.
Mehr Informationen zur HARDINGE GmbH:
![]() |
HARDINGE GmbH |
![]() |
Fichtenhain A 13 c |
![]() |
47807 Krefeld |
![]() |
Tel.: (49) 2151 496490 |
![]() |
Fax: (49) 2151 4964999 |
![]() |
www.hardinge.com |
Bitte bewerten Sie diesen Artikel.
![]() |
![]() |
![]() |
![]() |
![]() |
Bitte bewerten Sie diese Seite durch Klick auf die Symbole.