Trumpf-Laser machen mobil
Laser hilft bei der Fahrzeug-Effizienzsteigerung
Mobilität ist zu einem Grundbedürfnis industrialisierter Gesellschaften geworden. Das betrifft die Zunahme des weltweiten Güterverkehrs genauso wie die vielfältigen individualisierten Mobilitätsanforderungen. Dem gegenüber stehen regulierende Maßnahmen der Energiepolitik zur Reduzierung des CO2-Ausstoßes. Hier sind die Automobilhersteller in der Pflicht. Sie steigern die Effizienz von neuen Fahrzeugmodellen, indem sie beispielsweise Gewicht reduzieren oder in gänzlich neue Antriebskonzepte wie Elektromobilität investieren. Die Lasertechnik ist in beiden Fallen eine Schlüsseltechnologie, da sie eine präzise und effiziente Bearbeitung garantiert und manche Produktionsverfahren überhaupt erst ermöglicht.
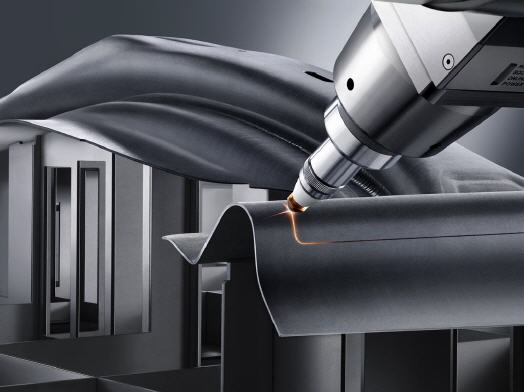
Laserschneiden von hochfestem Stahl
Durch den Einsatz pressgehärteter Stähle kann das Gewicht einer Karosse deutlich reduziert werden. Diese Stähle haben eine sehr hohe Festigkeit und ermöglichen einen geringeren Materialeinsatz im Vergleich zu herkömmlichen Bauweisen. Dadurch reduziert sich nicht nur der Kraftstoffverbrauch, auch die Sicherheit erhöht sich.
Maschinen und Laser von TRUMPF kommen in zahlreichen Prozessschritten bei der Verarbeitung hochfester Stähle zum Einsatz. Auf der EMO illustrierte TRUMPF diese Prozesskette anhand eines Golf GTI.
Die meisten pressgehärteten Karosserieteile werden aus Aluminium-Silizium beschichtetem, borlegiertem Stahl gefertigt. Dieser wird normalerweise vom Coil in einer Platinenschneidpresse bearbeitet. Das Beschneiden der flachen Platinen kann auch von einer 2-D-Laserschneidmaschine erledigt werden. Diese bietet den Vorteil, dass die Bauteile jederzeit flexibel verändert werden können ohne teures Schneidwerkzeug zu tauschen. Die Laserbearbeitung lässt das Schachteln der Bauteile zu, sodass sich die Ausnutzung des Materials erhöht.
Die Platinen werden anschließend in einer Ofenstrecke erwärmt, um das Material plastisch und damit gut formbar zu machen. Hier können TruHeat-Generatoren zur Induktionserwärmung Einsatz finden. Die Produkte von HÜTTINGER Elektronik weisen eine höhere Energieeffizienz auf und können damit die Betriebskosten im Vergleich zu herkömmlichen Gasfeuerungstechnologien reduzieren.
Die erwärmten Teile werden in einer Formpresse abgeschreckt und erreichen dadurch eine Zugfestigkeit von rund 1500 MPa. Das hochfeste Material erhöht die Sicherheit der Fahrgastzelle entscheidend und lässt sich durch konventionelle Verfahren kaum mehr wirtschaftlich bearbeiten. Aus diesem Grund kommen 3-D-Laserschneidanlagen für das Zuschneiden der pressgehärteten Karosseriebauteile zum Einsatz. Hier hat TRUMPF mit der TruLaser Cell 8030 mit Scheibenlaser eine spezielle Maschine entwickelt, die für diese Anwendung optimiert ist.
Die Strukturbauteile werden danach weiterverarbeitet und zu Karosseriebaugruppen zusammengeschweißt. Hier können 3-D-Schweisszellen mit TruDisk-Lasern und Remote-Schweissoptiken eingesetzt werden. Eine Nachverfolgbarkeit der gefertigten Teile stellen lasermarkierte Barcodes sicher. Die Laserkennzeichnung bietet den Vorteil der langfristigen Beständigkeit und hohen Qualität.
40 Prozent Zeitersparnis bei Nutzfahrzeugachse
Neben dem Golf GTI zeigte TRUMPF als weiteres Beispiel für den Einsatz des Lasers in der Automobilfertigung auf der EMO eine Nutzfahrzeugachse. Die Herausforderung bei der Achsenfertigung ist der hohe Kohlenstoffgehalt des Werkstoffs. Dieser lässt sich mit konventionellen Methoden nicht schweißen, das Material wird schnell rissig und spröde. Durch Vorwärmen mit TruHeat-Generatoren und speziellen Induktoren werden die Achsenbauteile für den nachfolgenden Schweißprozess optimal vorbereitet. Rissbildung und Versprödung werden verhindert.
Die Tiefschweißnähte an den Achsrändern schweißt der Laser. Dies bietet bei dem anspruchsvollen Werkstoff den Vorteil einer geringeren Wärmeeinbringung und damit eines reduzierten Verzugs. Die geringere thermische Belastung des Materials und eine gesteuerte Abkühlung nach dem Schweißprozess vermeiden Risse und erhöhen die Belastbarkeit des Achsbauteils. Zusätzliche Arbeitsschritte wie mechanische Nacharbeiten entfallen aufgrund der Qualität der Schweißnähte. Insgesamt lassen sich Nutzfahrzeugachsen durch Laserschweißen in 40 Prozent weniger Zeit herstellen.
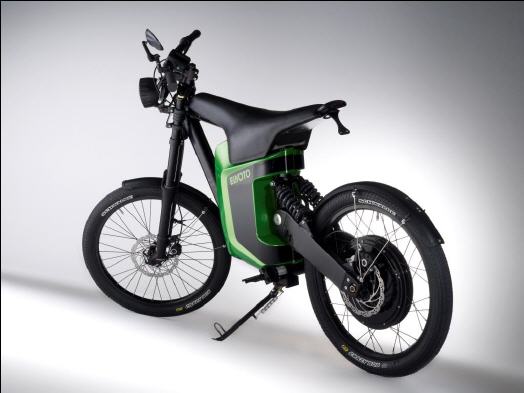
E-Bike Elmoto
Laserfertigung als Grundlage für E-Mobility
Eine der größten Herausforderungen bei der Realisierung einer flächendeckenden Elektromobilität ist die Herstellung von schnellaufladbaren, leistungsstarken und langlebigen Batterien für Elektromotoren. Diese Engergiespeicher sind mit den für Alltagsanwendungen eingesetzten Lithium-Ionen-Akkus nicht vergleichbar, da sie während eines normalen Beschleunigungsvorgangs eine sehr hohe Leistungsdichte in sehr kurzer Zeit zur Verfügung stellen müssen. Diese Stromspitzen stellen hohe Anforderungen an das Batteriemanagement im Hinblick auf Leistungshöhe und Leistungsdauer. Gleichzeitig muss die Wiederaufladung schnell erfolgen, da die Verfügbarkeit eines der Erfolgskriterien für die Praktikabilität von Elektromotoren ist.
Auch in punkto Lebenszyklusdauer müssen künftige Batterien für Elektromobile wesentlich robuster sein als dies bisher bei Lithium-Ionen-Akkus der Fall ist. Derzeitige Batterien in Elektromobilen haben eine Ladezeit von rund drei bis vier Stunden und eine Reichweite von bis zu 200 Kilometern. Um die Effizienz und Leistungsstärke dieser Speicher zu erhöhen, wird versucht durch die Kombination mehrer Batteriezellen leistungsstarke Gesamtakkus zu schaffen.
Alltagstaugliche Batterien sind derzeit für Elektrofahrräder realisiert. Als Beispiel hierfür zeigte TRUMPF auf der EMO das ELMOTO. Die an diesem E-Bike eingesetzte Batterie besteht aus einer einzelnen Zelle, die rund 2,2 Ampere liefert. Der geschätzte weltweite Markt für diese Fahrräder hat ein Volumen von rund 50 Millionen Euro.
Für die Fertigung leistungsstarker Energiespeicher ist die Lasertechnik ein mehr als geeignetes Fertigungsverfahren. Denn beim Schneiden und Schweißen von Batteriebauteilen wie Gehäuse oder Zellverbinder kann der Laser seine ganzen Vorteile ausspielen. Die berührungslose Bearbeitung sorgt für eine geringe mechanische Belastung des Materials. Die lokal begrenzte, geringe Wärmeeinwirkung beim Schweißen ergibt verzugsfreie Nähte.
Das Ziel, immer kleinere und leistungsstärkere Zellen in einen Batterieblock zu integrieren unterstützt die Lasertechnik durch die hohe Bearbeitungsqualität und Präzision bei der Fertigung und Feinbearbeitung kleiner Bauteile. Die effiziente Fertigung auf Lasermaschinen mit hoher Produktivität und niedrigen Teilekosten ermöglicht die Herstellung großer Volumen zu günstigen Preisen, wie es der Automobilmarkt erfordert.
Mehr Informationen zur TRUMPF Lasertechnik:
![]() |
TRUMPF Laser- und Systemtechnik GmbH |
![]() |
Postfach 1450 |
![]() |
71252 Ditzingen |
![]() |
Johann-Maus-Straße 2 |
![]() |
71254 Ditzingen |
![]() |
Telefon +49 (0) 7156-303-0 |
![]() |
Telefax: +49 (0) 7156-303-670 |
![]() |
E-Mail: info@trumpf-laser.com |
![]() |
www.trumpf-laser.com |
War dieser Artikel für Sie hilfreich?
![]() |
![]() |
![]() |
![]() |
![]() |
Bitte bewerten Sie diese Seite durch Klick auf die Symbole.
Zugriffe heute: 3 - gesamt: 6704.