Schwer zerspanbare Materialien sicher bearbeiten
Technologie für Verbrennungsmotoren
Energieeffizienz und Ressourcenschonung erfordern neue Werkstoffe. Die meisten dieser Leichtbau-Materialien eint eines: sie sind schwer zu zerspanen und stellen hohe Anforderungen an Maschine, Werkzeug und Prozess. Die Erarbeitung wirtschaftlicher und prozesssicherer Werkzeugkonzepte für ihre Bearbeitung erfordert großes Prozess-Know-how, wie es Mapal besitzt.
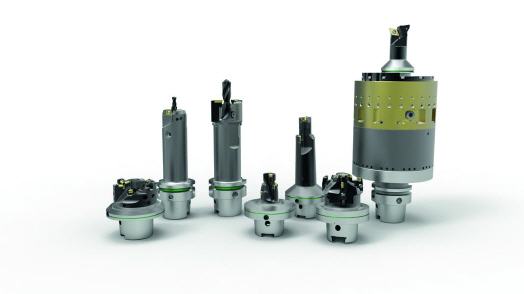
Bei Zylinderkurbelgehäusen aus Aluminium stellt der Aufbau der Zylinderlaufflächen aus eingegossenen beziehungsweise eingeschrumpften Graugussbuchsen den Stand der Technik dar. Um zukünftig Motorblöcke aus Aluminium noch dünnwandiger und leichter bauen zu können, werden die eingegossenen Buchsen durch thermisch aufgespritzte eisenmetallische Schichten ersetzt. Diese können dünner ausgeführt werden und die Reibleistung zwischen Kolbenring und Zylinderlauffläche wird verringert.
Für diese neue Technologie im Motorenbau sind spezielle Werkzeuge für die Konditionierung der Zylinderfläche vor dem thermischen Spritzen nötig, um eine optimale Schichthaftung zu erzielen. Dabei wird mit der MAPAL-Werkzeuglösung durch PKD-Konturschneiden eine definierte Strukturierung auf der Zylinderlauffläche erzeugt, in der sich die Spritzschicht optimal verkrallt und haftet. Nach dem Aufspritzen der Schicht werden die Zylinderlaufflächen mit Feinbearbeitungswerkzeugen mit sechsschneidigen PcBN-Schneiden bearbeitet. Die Geometrie der Lauffläche wird so für das abschließende Feinhonen vorbereitet. Die Feinbearbeitungswerkzeuge sind mit kühlmittelgesteuerten Aussteuermechanismen und einer Schneidenkompensation ausgestattet, um die Standzeiten weiter zu erhöhen.
Komplettbearbeitung von hochfesten Stahlsorten im Turbolader
Downsizing und Abgasturbolader treiben die moderne Motorenentwicklung. Für die Produktion der Turbinen- und Verdichtergehäuse des Turboladers waren oftmals sowohl Bearbeitungszentren als auch Drehmaschinen erforderlich. Die geometrisch komplexe Bearbeitung insbesondere beim Turbinengehäuse wird weiter erschwert, da hier hochfeste und temperaturbeständige Stahlgusssorten zum Einsatz kommen. Diese dürfen ihr Gefüge in einem Temperaturkorridor von -40° bis +1.050 Grad Celsius nicht verändern. Die Belastungen auf die Schneiden sind entsprechend hoch.
Moderne Fertigungsverfahren ermöglichen die komplette Bearbeitung auf einer Maschine. Mit mechatronischen Werkzeugsystemen und durch Interpolationsdrehen werden Konturen und Einstiche bearbeitet. Komplettbearbeitungswerkzeuge fassen darüber hinaus viele Bearbeitungsschritte zusammen. Die Tangentialtechnologie bettet die Schneidkörper stabil im Werkzeugkörper ein. Neben der Stabilität ermöglicht die Tangentialtechnologie die Umsetzung hochpositiver Schneidengeometrien, was für die Zerspanung des hochfesten Stahls Vorteile bringt.
Sinterwerkstoffe am Zylinderkopf prozesssicher und wirtschaftlich reiben
Das Downsizing hat in den letzten Jahren auch den Ventiltrieb im Zylinderkopf verändert. So wurden die Abmessungen des Ventilsitzes und der –führung von einer Motorengeneration zur nächsten immer kleiner. Dem Prinzip des Downsizing folgend, aus kleineren Motoren mehr Leistung zu holen, müssen die verwendeten Materialien der Ventilsitzringe starken Belastungen und Temperaturen standhalten. Verbesserte Materialien mit höherer Härte jedoch erschweren die Zerspanung. Als Schneidstoff wird meistens PcBN verwendet, um die Standzeiten in vernünftige Größen zu bringen.
Die Auswahl der optimalen PcBN-Sorte und der richtigen Kantenpräparation sind von entscheidender Bedeutung. Ebenso ist es essentiell, dass die Schneide absolut vibrationsfrei und robust im Werkzeugkörper aufgenommen ist. Hierzu liegt bei der MAPAL Lösung zur Bearbeitung der Ventilsitzringe die Schneide in einer Prismenauflage, um auch kleinste Vibrationen zu vermeiden, die sich negativ auf Qualität und Standzeit auswirken würden. Die Prismenaufnahme ist dabei als Festplattensitz so exakt in den Werkzeugkörper integriert, dass ein Einstellen der Schneide nicht mehr erforderlich ist.
Aufgrund der extremen Belastungen, denen Ventilführungen ausgesetzt sind, spielen die Gleit- und Wärmeleiteigenschaften der eingesetzten Werkstoffe eine große Rolle. In der Praxis werden zunehmend Sintermetalle verwendet, da sie im Vergleich zu anderen Werkstoffen kostengünstiger sind und eine höhere Verschleißfestigkeit aufweisen. Letztere jedoch stellt hohe Anforderungen an die für die Ventilführungsbearbeitung eingesetzten Reibwerkzeuge. Grundsätzlich stehen mehrere Werkzeuglösungen von MAPAL zur Verfügung, wobei Führungsleistenwerkzeuge bis zu Durchmessern um 6 mm erste Wahl sind.
Für kleinere Durchmesser kommt die PKD-Vollkopf-Technologie zum Einsatz, bei der durch einen speziellen Lötprozess ein Werkzeugkopf aus Voll-PKD stirnseitig auf einen Vollhartmetall-Grundkörper aufgebracht wird. Durch den innovativen Herstellungsprozess können die Werkzeuge mit sehr vielen Schneiden ausgestattet werden. So hat in einem aktuellen Anwendungsbeispiel eine Ventilführungsreibahle mit Durchmesser 5 mm sechs Schneiden. Die mit dem Werkzeug erreichten Zylinderformwerte sind hervorragend; zusätzlich konnte die Standzeit im Vergleich zum herkömmlich bestückten Werkzeug um das Dreifache gesteigert werden.
Fräsen von Aluminiumhybridbauteilen
Der Motorblock als schwerstes Einzelbauteil wird im Zusammenhang mit Gewichtsoptimierungsmaßnahmen besonders stark unter die Lupe genommen. Die Umstellung von Grauguss auf Aluminiumwerkstoffe brachte Gewichtseinsparungen von 40 bis 50 Prozent. Jedoch zeigt Aluminium Schwächen im Wärmedehnungskoeffizient, wodurch sich Lageraufweitungen ergeben würden. Durch Eisenwerkstoffe im Hauptlagerbereich lässt sich dies beherrschen.
Heute werden im Serienbetrieb die Vorteile beider Werkstoffe verbunden, indem Grauguss-Inlets in das Aluminiumgehäuse eingegossen werden. Diese Kombination stellt für beide Materialien betreffende Zerspanungsoperationen eine echte Herausforderung dar, erfordern sie doch grundsätzlich unterschiedliche Schneidstoffe und auch verschiedene Schnittgeschwindigkeiten. Dieser Konflikt führt im Regelfall bei der Bearbeitung zu ungenügenden Standzeiten, insbesondere wenn bestimmte Oberflächenwerte erreicht werden müssen.
Ein Lösungsansatz für die Planbearbeitung des Zylinderkurbelgehäuses ist der monolithische PKD-Planfräser HP-FaceMill mit fest gelöteten PKD-Schneiden und einem soliden Stahlgrundkörper. Der Durchbruch bei der Bearbeitung gelang durch den Einsatz des Fräsers mit den für Grauguss gängigen Schnittgeschwindigkeiten. Selbst in einem für PKD-Werkzeuge niedrigen Drehzahlbereich lassen sich aufgrund der hohen Schneidenanzahl im Werkzeug respektable Vorschubwerte erzielen.
Alternative Bearbeitungsstrategien für Inconel und Titan
Neben der Anpassung der Werkzeugtechnik an die spezifischen Anforderungen neuer Werkstoffe kann auch der Einsatz einer neuen Bearbeitungsstrategie zum Erfolg führen. Ein Beispiel ist hier das trochoide Fräsen von Titan oder Inconel. Durch die hohe Festigkeit dieser Werkstoffe ist die Belastung der Schneiden bei normalen Frässtrategien sehr hoch. Insbesondere die hohen Temperaturen führen zu schnellem Verschleiß. Um dem entgegenzuwirken, muss mit geringen Schnittwerten und Eingriffstiefen gearbeitet werden, was zu langen Bearbeitungszeiten insbesondere in der Volumenzerspanung führt.
Anders beim trochoiden Fräsen, bei dem der Fräser hochdynamisch auf einer trochoiden Bahn geführt wird. Dabei wird je nach Werkstoff der maximale Eingriffswinkel definiert. Bei Superlegierungen liegt er beispielsweise nur bei circa 40 Grad. Dadurch sind die Eingriffszeit des Fräsers sehr kurz und die thermische Belastung stark reduziert. Geringe Schnittbreiten und damit kleinere Schnittkräfte erlauben höhere axiale Schnitttiefen, sodass hohe Zerspanungsvolumina erzielt werden können. Beim dynamischen trochoiden Fräsen wird entlang der trochoiden Bahn die Vorschubgeschwindigkeit moduliert, sodass die Spanmittendicke konstant ist und eine gleichmäßige Belastung auf die Schneide wirkt.
Für das trochoide Fräsen sind eine geeignete Maschine mit hochdynamischen Achsen und schneller Steuerung und eine geeignete CAM-Software Grundvoraussetzungen. Speziell optimierte Fräser bringen zusätzlich weitere Vorteile. Da bei dem Verfahren mit sehr hohen Drehzahlen gearbeitet wird, besteht bei herkömmlichen Fräsern die Gefahr von Schwingungen. Um dies zu vermeiden, setzt MAPAL auf optimierte Vollhartmetall-Fräser des OptiMill® Programms mit ungleicher Schneidenteilung und variablem Drallwinkel, die auch bei hohen Schnittdaten weniger zum Schwingen neigen.
Mehr Informationen zur MAPAL Dr. Kress KG:
![]() |
MAPAL Dr. Kress KG |
![]() |
Obere Bahnstr. 13 |
![]() |
73431 Aalen |
![]() |
Tel.: 0 73 61 / 5 85 - 0 |
![]() |
Fax.: 0 73 61 / 5 85 - 1 50 |
![]() |
E-Mail: info@de.mapal.com |
![]() |
www.mapal.com |
War dieser Artikel für Sie hilfreich?
![]() |
![]() |
![]() |
![]() |
![]() |
Bitte bewerten Sie diese Seite durch Klick auf die Symbole.
Zugriffe heute: 3 - gesamt: 7219.