Deutliche Vorteile bei der Elektrodenherstellung
Standardfräser mit optimierter Diamantbeschichtung
Seit mehr als 65 Jahren ist die Formenbau Sauter GmbH erfolgreich in der Metallverarbeitung tätig. Das Familienunternehmen mit Sitz im schwäbischen Hirrlingen fertigt Einzelteile aus verschiedenen Materialien nach Kundenwunsch. Um die Anforderungen nach Präzision und hoher Oberflächenqualität zu erfüllen, setzt Sauter Standardfräser mit optimierter Diamantbeschichtung der HAM Hartmetallwerkzeugfabrik Andreas Maier GmbH ein. Bei der Herstellung von Elektroden für die Senkerosion aus Graphit erzielt das Unternehmen damit deutliche Prozessvorteile. Darüber hinaus testen Experten von Hartmann den Einsatz der Fräser für die Hartmetallbearbeitung – mit sehr guten Ergebnissen.
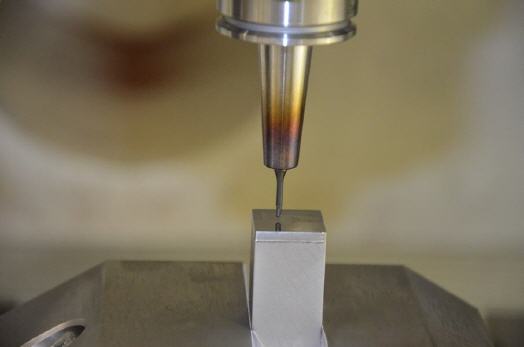
Von einer kleinen, 1948 gegründeten Schildermanufaktur hat sich Sauter zu einem hochpräzisen, zuverlässigen Werkzeug- und Formenbau entwickelt, der in dritter Generation in Familienbesitz ist. Sieben Mitarbeiter stellen im 2013 bezogenen, modernen Büro- und Produktionsgebäude Spritzgussformen, Biege-, Präge- und Stanzwerkzeuge sowie Elektroden her. Spezialisiert hat sich Sauter auch auf Draht- und Senkerosion, Fräsarbeiten und Industriegravuren in Aluminium, Stahl und Kunststoff. Spezialstempel und Sonderwerkzeuge runden das Portfolio ab.
Die Kunden kommen hauptsächlich aus der Automobilindustrie, dem Maschinenbau und der Medizintechnik. „Unsere Stärke ist die Einzelteilfertigung. Wir müssen Lösungen für die individuellen Kundenwünsche finden, bei denen das Preis-Leistungsverhältnis stimmt“, beschreibt Geschäftsführer Niko Sauter. Zu den Stärken des Werkzeug- und Formenbauers gehört die hohe Fertigungstiefe. Vom Rohblock bis zum fertig gefrästen, geschliffenen oder erodierten Werkstück wird alles im Hause produziert. „Das ist eine unserer Kompetenzen und die Kunden schätzen das“, sagt Sauter. Damit das so bleibt, investiere sein Unternehmen kontinuierlich in die Modernisierung des Maschinenparks. In der Produktionshalle stehen eine neue CNC-Flachschleifmaschine und eine HSC-Fräsmaschine mit 40.000er Spindel. Eine leistungsstarke CNC-Drehbank kam kürzlich hinzu.
Viel Erfahrung hat Sauter im Lauf der Jahre mit der Bearbeitung von Graphit gesammelt. Eine besondere Herausforderung bei der Herstellung von Elektroden für die Senkerosion ist die Miniaturisierung. „Die Teile werden immer kleiner und genauer. Das setzt eine hochpräzise Bearbeitung voraus. Wir realisieren beispielsweise Pins mit einem Durchmesser von lediglich 0,2 Millimeter in Graphit absolut zuverlässig“, beschreibt Sauter. Um die Herstellung der Elektroden weiter zu verbessern, greift der Werkzeug- und Formenbauer auf Standardfräser der Typen 40-5480, 40-5880 und 40-5600 von HAM mit modifizierter Diamantbeschichtung zurück.
Achim Schweikart, Leiter Außendienst der HAM Vertriebsgesellschaft Fritz Hartmann GmbH sowie seine Techniker-Kollegen unterstützen ihn bei der Wahl des geeigneten Werkzeugs. Bereits seit Jahren bestehen intensive Kontakte zwischen den Unternehmen. „Hartmann/HAM zeichnet sich durch kompetente Beratung aus. Wir schätzen auch die große Erfahrung und den sehr guten Service. Die Fachleute nehmen sich viel Zeit, Werkzeuge vor Ort einzufahren. Wenn wir neue benötigen, sind diese am nächsten Tag in der gewünschten Art und Weise verfügbar“, lobt Sauter.
Um die Elektrodenherstellung zu optimieren, schlug Schweikart die HAM-Lösung vor. „Der Fräser kommt aus unserem Standardprogramm und ist damit keine teure Sonderlösung. Neu ist die Beschichtung. Normalerweise erzeugen diamantbeschichtete Werkzeuge eher raue Oberflächen. Diesen Nachteil konnten wir durch unsere modifizierte Lösung verhindern“, beschreibt Schweikart. In der täglichen Praxis hat der Fräser überzeugt.
Niko Sauter: „Wir haben bei der Elektrodenbearbeitung mit der neuen Beschichtung schon nach den ersten Schruppgängen erkannt, dass die erzeugte Oberfläche deutlich besser ist als erwartet.“ Bei der Standzeit erzielt der HAM-Fräser einen um den Faktor fünf besseren Wert als ein vergleichbares Wettbewerbsprodukt. Das haben Tests ergeben. Sauter konnte damit die Prozesssicherheit signifikant erhöhen. Das Werkzeug bearbeitet heute fünf Elektroden ohne nennenswerten Verschleiß, wo bei früheren Lösungen bereits nach der zweiten Elektrode getauscht werden musste.
Auf Initiative von Hartmann wagte sich Niko Sauter an eine weitere, anspruchsvolle Bearbeitung: dem Fräsen von Hartmetall. „Wir haben dieses Material als Wachstumsmarkt erkannt und reagieren darauf“, sagt Schweikart und schlug vor, denselben Standard-Fräsertyp mit modifizierter Diamantbeschichtung auszuprobieren wie bei der Elektrodenherstellung. Gemeinsam mit seinen Kollegen Ulrich Czogalla und Jürgen Heiler, Technische Beratung und Verkauf bei Hartmann, fanden umfangreiche Versuche vor Ort an der neuen HSC-Fräsmaschine mit 40.000er Spindel statt. Versuchsobjekt war das Hartmetall-Substrat G 40 mit 18 Prozent Kobaltanteil und Härte 87 HRC.
Die ersten Ergebnisse der Fräsversuche bewerten die Hartmann/HAM-Experten wie auch Niko Sauter als „sehr positiv“. Die Werkzeuge haben die Anforderungen an die Standzeit erfüllt. Auch die Oberflächengüte überzeugte. „Es gibt keinerlei Ausbrüche am Werkstück“, sagt Ulrich Czogalla und legt die Kontroll-Lupe zur Seite. Wenn die Präzisionswerkzeuge in der Praxis zum Fräsen von Hartmetall eingesetzt werden können, entstehen damit Umformwerkzeuge wie Stempel und andere Komponenten für Alu-Fließpressen oder Sinterpressen, in denen Hartmetall zunehmend eingesetzt wird. „Dann schlagen wir ein neues Kapitel in unserer Bearbeitungsstrategie auf“, meint Niko Sauter.
Die Leistungsfähigkeit der HAM-Innovation hat den Geschäftsführer überzeugt. „Ich bin mit den Resultaten mehr als zufrieden. In der Elektroden-Herstellung konnten wir die Standzeiten deutlich verbessern und damit die Prozesssicherheit optimieren. Die Ergebnisse der Hartmetall-Fräsversuche sind vielversprechend und wir verfolgen den Ansatz konsequent weiter“, fasst er zusammen. Die Oberflächengüte entspreche den steigenden Anforderungen des Marktes. Sauter überzeugt auch der preisliche Aspekt. Das HAM-Werkzeug aus dem Standardprogramm liegt um ein Vielfaches niedriger als eine Sonderlösung. Für die Kosteneffizienz spricht auch die Tatsache, dass die Werkzeuge komplett in Baden-Württemberg produziert werden. Teure Outsourcing-Maßnahmen oder Zukäufe entfallen.
Mehr Informationen zur HAM GmbH:
![]() |
Hartmetallwerkzeugfabrik Andreas Maier GmbH |
![]() |
Stegwiesen 2 |
![]() |
88477 Schwendi-Hörenhausen |
![]() |
Tel.: 07347 / 61-0 |
![]() |
Fax: 07347 / 7307 |
![]() |
E-Mail: info@ham-tools com |
![]() |
www.ham-tools.com |
War dieser Artikel für Sie hilfreich?
![]() |
![]() |
![]() |
![]() |
![]() |
Bitte bewerten Sie diese Seite durch Klick auf die Symbole.
Zugriffe heute: 2 - gesamt: 6526.