Hohe Steifigkeit für höchste Leistung
Walter Prototyp ConeFit-System
Die Leipold-Gruppe in Wolfach verbesserte mit Hilfe der Walter AG in nur wenigen Wochen ihre Performance beim Fräsen von Großserienteilen aus V2A-Stahl. Das Walter Prototyp ConeFit-System trug wesentlich zu diesem Erfolg bei.
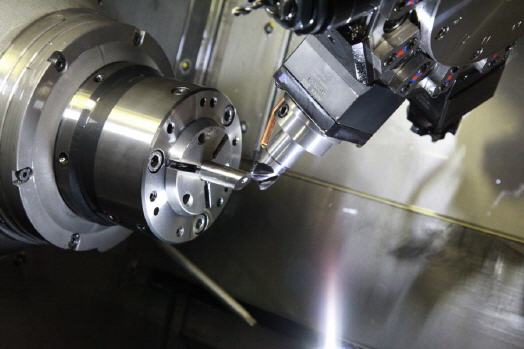
Die in der Schwarzwald-Gemeinde Wolfach beheimatete metallverarbeitende Leipold Gruppe hat sich auf die Herstellung von Präzisionsteilen für die Automobilindustrie, die Elektro- und Gebäudetechnik sowie die Industrietechnik spezialisiert. Mit rund 400 Mitarbeitern an vier Standorten in Deutschland und den USA zählt sie zu den größten in ihrer Branche.
Bei der Fertigung komplexer Dreh-, Fräs- und Schleifteile aus Edelstählen und nichteisenhaltigen Metallen ist die kontinuierliche Verbesserung ein wichtiger Bestandteil bei Leipold. „Besonders bei unseren Langläufern ist höchste Präzision und Effizienz erforderlich, weil sich hier kleinste Fehler auf die ganze Serie auswirken und wirtschaftliche Probleme verursachen können“, erklärt der Produktionsleiter Robert Kern.
Regelmäßig werden in der Leipold-Gruppe deshalb gerade diese Langläufer unter die „Lupe“ genommen, um, gemeinsam mit den Hauptwerkzeuglieferanten, die bestmöglichen Zerspanungsergebnisse zu erzielen. Mit Walter wurde der Fertigungsprozess für ein komplexes Drehteil für die Kraftstoffverteilung aus dem Werkstoff 1.4301 analysiert.
Gemeinsames Team setzt neuen Prozess auf
Mathias Scherer von der Walter Deutschland GmbH und technischer Berater für die Leipold Gruppe, schaute sich gemeinsam mit dem Team der Fa. Leipold im Wolfacher Werk die laufenden Prozesse an. Ziel war es, Optimierungspotenziale ausfindig zu machen. „Wir strebten eine hohe Reproduzierbarkeit mit geringerem Ausschuss an. Wenig gebundene Mitarbeiterkapazität, geringer Messaufwand und wenig Werkzeugwechsel waren weitere Faktoren“, fasst Florian Vollmer, Leiter des Technologiezentrums bei der Fa. Leipold, die Anforderungen zusammen. „Insgesamt wollten wir einen robusteren und stabileren Prozess mit einer wesentlichen Standzeitverbesserung erreichen.“
Sehr schnell war den Experten klar: Der bislang eingesetzte Wendeplattenfräser mit drei Schneiden schaffte nur rund 8.000 Teile aus rostfreiem V2A-Stahl (1.4301) und wurde dann unbrauchbar. Bei dem bemängelten Bauteil handelt es sich um einen konkav geformten Radius, der im Laufe der Produktion nicht mehr maßgenau ausgeführt wurde.
„Bei diesem Bauteil handelt es sich praktisch um einen „Dauerläufer“, der etwa zwei Jahre lang rund um die Uhr auf der eingesetzten Maschine gefertigt wird“, erklärt Roland Braunwarth, Leiter der CNC und Mehrspindlerfertigung bei Leipold. „Da geht es um höchste Präzision und Effizienz, deshalb muss der Prozess einwandfrei funktionieren.“
Der geringere Output in diesem Produktionsbereich führte zu Einschränkungen bei der Wirtschaftlichkeit. Deshalb entschied sich das Experten-Team rund um Mathias Scherer für den Einsatz eines Walter Prototyp ConeFit-Systems. Das Ergebnis überzeugte: „Mit ConeFit verbesserte sich der Output noch deutlicher als wir es erwartet hatten“, freut sich Roland Braunwarth. „Zusätzlich erreichten wir einen stabileren Prozess mit besserer Maßhaltigkeit.“
Hochproduktive Zerspanung dank höchster Steifigkeit
Das Walter Prototyp ConeFit-System ist modular aufgebaut und verfügt über unterschiedliche Schaftvarianten sowie Werkzeug-Geometrien. Somit kann es flexibel für jeden Bearbeitungsfall eingesetzt werden. Es erlaubt ein einfaches Handling durch genaueren und schnelleren Wechsel der Werkzeuge mit Hilfe der patentierten ConeFit-Schnittstelle. Dabei bleibt die Aufnahme in der Maschine, nur der ConeFit-Kopf wird gewechselt.
Das Vollhartmetallwechselkopfsystem besteht aus einem schneidenden Teil und einem konischen Gewinde. Die Plan- und Kurzkegelanlage sowie das selbstzentrierende Gewinde sorgen für höchste Stabilität und Genauigkeit. Dadurch wird nicht nur Vollhartmetall gegenüber normalen Schaftfräsern eingespart. Er ist dank seiner verschiedenen Verlängerungen und Haltervarianten universell einsetzbar. Außerdem schneiden die Werkzeuge in der Regel weicher als eine Wendeplattenlösung.
Wo vorher zwei Schnitte ausgeführt werden mussten, genügt mit dem ConeFit-System nur ein Schnitt. Zusätzlich garantiert die hohe Steifigkeit auch eine hohe Zerspanungsleistung.
Aufgrund der kurzfristig erreichten guten Ergebnisse prüft man bei Leipold derzeit weitere Einsatzgebiete für das ConeFit-System. „Wir verfügen über ein breites Maschinenspektrum auf denen die Werkzeuge eingesetzt werden können“, so Roland Braunwarth. „Dazu zählen unsere Einspindeldrehzentren, die Mehrspindeldrehautomaten und die Rundtaktmaschinen. Das ConeFit™-System ist maschinenübergreifend einsetzbar. Selbstverständlich müssen dabei immer die Kosten für solch moderne Werkzeuge mit den kaufmännischen Ergebnissen verglichen werden.“ Insgesamt ziehen die Verantwortlichen bei Leipold ein sehr positives Fazit. Das liegt nicht zuletzt auch daran, dass im Zuge der gemeinsamen Untersuchungen noch weitere Optimierungen mit zusätzlichen Werkzeugen aus den Sortimenten von Walter erreicht werden konnten. „Hierzu zählen unter anderem Erfolge beim Stechdrehen, beim Ein- und Abstechen sowie beim Fräsen. Erfolge, die nicht nur für ein Unternehmen im Hochlohnland Deutschland überlebenswichtig sind, sondern auch für die Lieferanten wie dem Werkzeugspezialisten Walter“, freut sich Produktionsleiter Robert Kern.
Mehr Informationen zur Walter AG:
![]() |
Walter AG |
![]() |
Derendinger Straße 53 |
![]() |
72072 Tübingen |
![]() |
Telefon 07071 70-10 |
![]() |
Fax 07071 70-1212 |
![]() |
E-Mail: info@walter-ag.de |
![]() |
www.walter-tools.de |
War dieser Artikel für Sie hilfreich?
![]() |
![]() |
![]() |
![]() |
![]() |
Bitte bewerten Sie diese Seite durch Klick auf die Symbole.
Zugriffe heute: 2 - gesamt: 6088.