Zirkondioxid für Dentalprodukte
Kopp Schleiftechnik und TU Darmstadt forschen
Zirkondioxid für die Dentalindustrie möglichst wirtschaftlich zerspanen, und zwar mit besten Resultaten – dies war das Forschungsziel eines gemeinsamen Projekts der Kopp Schleiftechnik GmbH und der TU Darmstadt. Im Rahmen der Initiative „Zentrales Innovationsprogramm Mittelstand“, gefördert vom Bundesministerium für Wirtschaft und Energie, wurden Kugelfräser entwickelt und mit unterschiedlichen Parametern bei der Zerspanung von Grünlingen der anspruchsvollen Keramik getestet – mit überraschenden Ergebnissen.
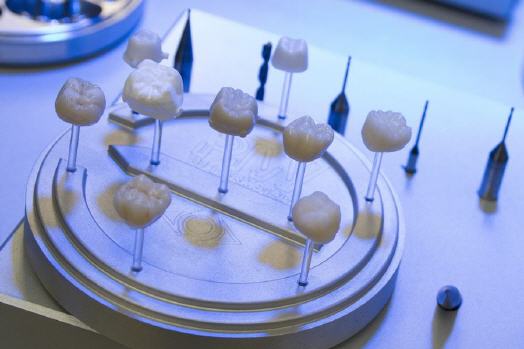
Bei Zirkondioxid (ZrO2) mit einer Härte von 1.200 HV handelt es sich um eine Keramik, die aufgrund ihrer Biegefestigkeit, Bruchzähigkeit und Verschleißfestigkeit häufig in der Industrie eingesetzt wird – die Anwendungsmöglichkeiten reichen von Ventilen, Sensorkörpern, Gleitlagern und Wasserpumpen bis hin zu Rohren und Werkzeugschneiden. Auch in der Medizintechnik, beispielweise der Dentalindustrie, ist ZrO2 aufgrund seiner Biokompatibilität, hoher Abrasionsstabilität sowie geringer Plaqueaffinität äußerst beliebt.
Daher wird erwartet, dass auch in Zukunft sein Einsatz als Material für Stifte, Implantate, Kronen und Brückenversorgungen zunehmend ansteigt. Das stellt allerdings den Zerspaner vor große Herausforderungen, denen sich der Werkzeughersteller Kopp Schleiftechnik GmbH aus Lindenfels/Winterkasten und die Technische Universität (TU) Darmstadt im Rahmen gemeinsamer Forschungen gestellt haben.
Zu klären war, wie sich die Werkzeugkosten, die 7 bis 15 Prozent der Herstellungskosten betragen, senken lassen, um so die Produktivität zu steigern. Die Projektpartner berücksichtigten dabei die Schwerpunkte Referenz, Standweg, Werkzeugoptimierung, Substrate und Beschichtung, Prozessoptimierung sowie Maschinenvermessung. Auch spielt die mit den verschiedenen Bearbeitungsstrategien erreichbare Oberflächenqualität eine maßgebliche Rolle, stellt doch der Nachbearbeitungsprozess ebenfalls einen erheblichen Kostenfaktor dar.
„Zunächst einmal lässt sich feststellen, dass es bei der erfolgreichen Bearbeitung von Zirkondioxid auf eine optimale Kombination aus Werkzeuggeometrie, Beschichtung und Bearbeitungsstrategie ankommt“, erklärt Achim Kopp, Geschäftsführer der Kopp Schleiftechnik GmbH. „Selbstverständlich müssen die Fräser auch so konzipiert sein, dass das Werkstück nicht beschädigt wird. Materialchipping gilt es unbedingt zu vermeiden.“
Es gibt drei Möglichkeiten, ZrO2 zu bearbeiten: Im Grünlingszustand, also als Pressling ohne Wärmebehandlung, im vorgesinterten Weißlingszustand oder in seiner durchgesinterten, endfesten Form. Im Rahmen ihrer Forschungsarbeiten fertigte die Kopp Schleiftechnik GmbH zweischneidige Kugelkopffräser mit einem Durchmesser von 1 mm zum Schlichten von Zirkondioxid im Grünlingszustand. „Denn in dieser Form hat sich die Zerspanung im Allgemeinen am meisten bewährt, da die Härte und somit auch die Widerstandsfähigkeit von Zirkondioxid hierbei geringer ist“, erläutert Vitali Dejkun, wissenschaftlicher Mitarbeiter bei der TU Darmstadt.
Zerspant wurde in ebenen Spiralbahnen auf Kleinstbearbeitungs- bzw. Desktopfräsmaschinen, wie sie im Dentallabor üblich sind. Dabei wurde mit unterschiedlichen Hartmetallsubstraten und Geometrien gearbeitet, und es kamen sowohl unbeschichtete Fräser als auch 6 bis 8 µm dicke Diamantbeschichtungen zum Einsatz. Gefräst wurde dabei mit verschiedenen Schnittgeschwindigkeiten, ausgehend von den vom Hersteller empfohlenen Parametern vc = 100 m/min, fz = 0,02 mm und ae = 0,3 mm.
Alle untersuchten Werkzeuge wiesen – unabhängig von den gewählten Parametern – aufgrund der Zerrüttung des Werkstoffs und der induzierten Druckspannungen einen abrasiven Freiflächenverschleiß auf. Darüber hinaus wurden die Werkzeuge durch das abgetragene Material in den Eingriffszonen zusätzlich belastet, und durch die hohe Reibung verringerten sich auch die Standzeiten.
„Dagegen haben wir im Versuch festgestellt, dass die Standzeit durch Luftzufuhr in die Eingriffszone gleich um den Faktor 2 erhöht werden konnte“, so Achim Kopp. „Mit der Diamantbeschichtung wurde die Standzeit im Vergleich zu unbeschichteten Werkzeugen sogar zusätzlich um den Faktor 10 erhöht.“
Um eine wirtschaftliche Zerspanung von Zirkondioxid zu ermöglichen, sind allerdings zusätzlich die Werkzeugeinsatzzeiten zu beachten. Wurden die Fräser regulär alle fünf Stunden gewechselt, war der Einsatz von unbeschichteten, aber gekühlten Kugelfräsern am lohnendsten, da auch deren Standzeit bei ungefähr fünf Stunden lag. Vitali Dejkun: „Die diamantbeschichteten Fräser hielten zwar wesentlich länger durch, doch wäre mit ihnen bei einem Werkzeugwechsel alle fünf Stunden eindeutig Potenzial vergeudet worden – und Geld, denn die Beschichtung macht immerhin 50 Prozent der Werkzeugkosten aus!“ Die Zerspanung mit diamantbeschichteten Fräsern wäre erst bei einem Werkzeugwechsel alle sieben Stunden wieder rentabel gewesen, ermittelten die Wissenschaftler.
Auch die Oberflächenrauheit des Werkstücks wurde untersucht, da sie den anschließenden Polieraufwand und damit die Wirtschaftlichkeit des Herstellungsprozesses maßgeblich mitbestimmt. Vitali Dejkun: „Heraus kam, dass anfänglich größere Rauheiten durch Ausbrüche an den radialen Fräsgrenzen im Laufe der Werkzeugstandzeit weniger werden. Grund: Sowohl bei den unbeschichteten als auch bei den beschichteten Werkzeugen stellten sich nach kurzer Zeit Kantenverrundungen ein, die zu besseren Rauheitswerten führten.“
Von der Frässtrategie waren die Flächengenauigkeiten ebenso abhängig: Zirkondioxid ist sehr spröde, weshalb bei der kombinierten Fräsbearbeitung wechselseitig Mikrorisse in das Werkstück eingebracht werden. Beste Ergebnisse erzielte der Gleichlauf und mittlere der Gegenlauf, wohingegen die kombinierte Strategie zu einer 64 Prozent höheren Rauheit durch Chipping führte. Das Hartmetall, aus dem das Werkzeug besteht, hatte nur einen sehr geringen Einfluss auf die Oberflächengüte.
„Insgesamt lässt sich sagen, dass wir im Rahmen des Projekts mit unseren Werkzeugen Standzeitoptimierungen von 80 Prozent im Vergleich zu Standardwerkzeugen realisieren konnten. Gerade für eine so um Wirtschaftlichkeit ringende Branche wie die Dentalindustrie sind solche Margengewinne von enormer Bedeutung“, resümiert Achim Kopp.
Mehr Informationen zur Kopp Schleiftechnik GmbH:
![]() |
Kopp Schleiftechnik GmbH |
![]() |
Am Raupenstein 21 |
![]() |
64678 Lindenfels/Winterkasten |
![]() |
Tel.: +49 (0) 62 55/95 95-0 |
![]() |
Fax: +49 (0) 62 55/95 95-139 |
![]() |
E-Mail: info@kopp-schleiftechnik.de |
![]() |
www.kopp-schleiftechnik.de |
War dieser Artikel für Sie hilfreich?
![]() |
![]() |
![]() |
![]() |
![]() |
Bitte bewerten Sie diese Seite durch Klick auf die Symbole.
Zugriffe heute: 2 - gesamt: 6369.