Siemens steigert Patenterstanmeldungen
Zwölf Forscher ausgezeichnet
Siemens meldete im Geschäftsjahr 2014 rund 4.300 Patente an – neun Prozent mehr als 2013. Zum Erfolg beigetragen haben zwölf Siemens-Forscher und -Entwickler, die zusammen für über 900 Erfindungen und 842 erteilte Einzelpatente verantwortlich sind. Sie wurden von Siemens in München als „Erfinder des Jahres 2014“ ausgezeichnet.
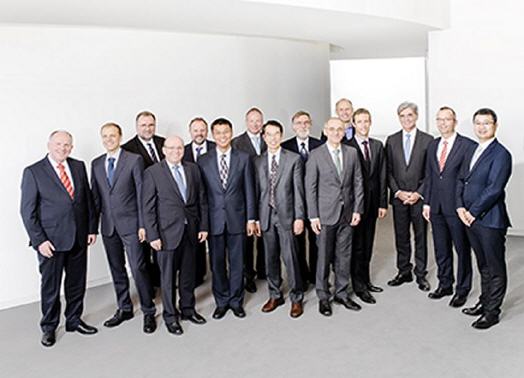
„Innovation ist einer der tragenden Säulen der Siemens Vision 2020“, sagt Joe Kaeser, CEO der Siemens AG. „Grundlage unserer Innovationen sind kreative und wertvolle Ideen. Mit diesen Ideen und ihrem Streben nach neuen technologischen Lösungen haben diese zwölf Erfinder und ihre 30.000 Kollegen weltweit entscheidend dazu beigetragen, die technologische Zukunft und den Markterfolg unseres Unternehmens zu sichern.“ Acht der ausgezeichneten Siemens-Forscher kommen aus Deutschland, die Übrigen aus USA, Dänemark und China.
Ihre Erfindungen reichen von drahtlos funkenden Sensoren, die an Bahngleisen Züge überwachen, über ein neues Kühlsystem, das Windkraftanlagen mehr Strom produzieren lässt, bis hin zu einer Gasturbine, deren Komponenten neu kombiniert wurden – und damit die Herstellung der Turbine wesentlich günstiger machen als bislang.
Die Auszeichnung zum „Erfinder des Jahres“ vergibt Siemens seit 1995 jährlich an herausragende Forscher und Entwickler des Hauses, deren Erfindungen in erheblichem Maße zum Unternehmenserfolg beitragen.
Die Erfinder 2014 waren:
Ralf Beyer
Virtueller Bohrer für Schienenfahrzeuge
Als Ralf Beyer seine Idee zum ersten Mal vor internationalem Fachpublikum präsentierte, war die Reaktion verhalten. Von manchem Skeptiker sei er sogar belächelt worden, erzählt der 47-jährige Systemarchitekt der Siemens Mobility in Erlangen. Der Mann, der „neue Ideen in Schienenfahrzeuge bringt“, wie er seine Tätigkeit selbst beschreibt, hatte im Jahr 2007 auf einem Kongress in Großbritannien prognostiziert, „dass die Wartung von Schienenfahrzeugen eines Tages komplett drahtlos auf Tablet und Smartphone laufen“ würde.
Damals habe sich das kaum jemand vorstellen können, erinnert sich der Diplomingenieur. Doch er war klug genug, seine Idee über die Anmeldung eines Patentes zu sichern. Denn heute, so der Erfinder, „will das jeder haben“. Zukünftige Anforderungen berücksichtigen, vor dem Kunden wissen, was er in Zukunft wollen wird, das sei seine Aufgabe, beschreibt Ralf Beyer seine Tätigkeit. Der Automatisierungstechniker kann der bereits 29 Erfindungen und 50 Patente sein eigen nennt, hat einen webbasierten Service für Schienenfahrzeuge entwickelt, der in den Flotten des britischen „Thameslink“, im deutschen „ICx“ sowie im österreichischen „Desiro ÖBB“ zum Einsatz kommen wird.
„In unseren Schienenfahrzeugen sind um die 200 Steuergeräte miteinander vernetzt. Die will man bei der Wartung gezielt anwählen können“, beschreibt Ralf Beyer die Herausforderung, der er sich angenommen hatte. Im Allgemeinen geht es darum, Probleme in Zügen zu diagnostizieren und Ausfälle zu prognostizieren, bevor es dazu kommt. Im Besonderen geht es darum, die Techniker genau dorthin zu leiten, wo die Ursache eines Fehlers liegt und die Technik selbst gleichzeitig so gut zu verbergen, dass jeder denkbare Zentimeter im Innenraum des Fahrzeugs für den Komfort der Insassen genutzt werden kann. Wo Sitze und Haltestangen den Raum einnehmen, darf die Technik nicht in voluminösen Schaltschränken sitzen. Sie muss dezent in die Wand integriert sein.
„Der eigentliche Gag ist: Ich muss keine Klappen im Fahrzeug öffnen, um in das Fahrzeug hineinzukommen“, erklärt Beyer den praktischen Nutzen seiner Erfindung. Bisher mussten die Techniker seinen Angaben zufolge bei Regulierungsbedarf – etwa der Temperatur der Klimaanlage oder der Öffnungs- und Schließzeiten von Türen – diverse Arbeitsschritte ausüben: Sie mussten die Klappe öffnen, hinter der sich die Technik verbirgt, Zugangspunkte suchen, Kabel anstecken.
„Für die Wartung musste man bis zu 20 verschiedene Kabel dabei haben“, erzählt der Siemens-Ingenieur. Die unterschiedlichen Komponenten darin benötigten außerdem unterschiedliche Service-Softwares der Hersteller. Pro Fahrzeug waren das bis zu 60 verschiedene. Dafür wurde auch bisher ein Notebook verwendet. Es genügte jedoch, dass dessen Betriebssystem wechselte, schon konnte es passieren, dass die Software einzelner Hersteller nicht mehr lief.
Ralf Beyer brachte das auf die Idee, die Software direkt in die Komponenten hineinzubringen. Das zog eine ganze Reihe von Vorteilen nach sich. Die Software jeder Komponente ist auf dem aktuellen Stand. Kabel sind nicht mehr notwendig, denn der Techniker klinkt sich einfach von Tablet oder Handy aus in das Netzwerk des Fahrzeugs ein. Das funktioniert sogar unabhängig vom Endgerät: Mit jedem Computer mit Web- Browser kann der Techniker – die Zugangsdaten vorausgesetzt – sich in die Unterebenen der Service-Applikationen einklinken und dort nach Fehlern suchen und diese beheben. Sogar die Dokumentation relevanter Informationen kann direkt dort hinterlegt werden, wie auch die zugehörige Ortsinformation.
Die Anzeige greift auf geographische Karteninformationen zu und speichert Fehlermeldungen gemeinsam mit dem jeweiligen Ort. Das Ganze trägt den Namen: „Web Based Diagnostics“. Und so funktioniert es: Wer die IP-Adresse des betreffenden Fahrzeugs in den Web-Browser eingibt, landet zunächst auf einer Übersichtsseite, die das Fahrzeug als Gesamtsystem abbildet. Von dort kann er sich via Klick oder durch Tippen und Wischen auf einem Touchscreen immer weiter in die verschiedenen Ebenen der Fahrzeugsteuerung hineinbegeben, in dessen Beleuchtung, Belüftung, kurz: in jegliche Komponente.
Die Entwickler haben diesem Prinzip einen englischen Namen gegeben: „drill-down diagnostics“. Denn die Plattform erlaubt, sich immer tiefer in das Fahrzeug „hineinzubohren“. Doch es ging den Entwicklern nicht nur darum, die Arbeit der Techniker effizienter und angenehmer zu gestalten. Sie hatten auch besseren Service für den Fahrer im Visier. Auch er benötigt einen visuellen Überblick über sein Fahrzeug, schließlich trägt er die Verantwortung. Er muss sofort erfahren, wenn es irgendwo ein Problem gibt oder geben könnte.
Seine Bedürfnisse sind jedoch anders gelagert als die des Technikers: Während Letzterer auf der Suche nach der Ursache eines Problems ist, benötigt der Fahrer eine Anweisung, wie er auf ein Problem reagieren soll. Eine neu gestaltete Nutzeroberfläche erfüllt genau diesen Zweck. Er nennt 29 Erfindungen und 16 Schutzrechtsfamilien sein eigen und ihm wurden bereits 50 Patente erteilt.
Jörg-Uwe Dahl
Ausgeklügelte Mechanik für geringen Energieverlust
Jörg-Uwe Dahl ist ein klassischer Konstrukteur. „Die meiste Zeit zerbreche ich mir den Kopf, wie ich Material und Anordnung so kombiniere, dass bessere Lösungen entstehen“, erklärt er. Wenn er beispielsweise einen neuen Schalter für ein Niederspannungsnetz konstruiert, sind seine Ausgangsbasis die Anforderungen, die in einem Pflichtenheft beschrieben sind, und der vorgegebene Bauraum. „Der ist natürlich immer zu klein, sonst wäre es ja keine Herausforderung“, sagt der Erfinder. Dann beginnt die Tüftelei. „Seit es 3D-Drucker gibt, macht das noch mehr Spaß als zuvor, denn jetzt kann ich viele Teile einfach ausdrucken und gleich in meine Konstruktion einbauen, um zu sehen, ob das funktioniert.“
Früher diente beispielsweise Knete als Material für 3D-Versuche, aber diese Teile konnten natürlich nicht auf die spätere Funktionalität getestet werden. Besonders nützlich war das 3D-Drucken für die Konstruktion des Rotorsystems, in dem die Kontakte eines Leistungsschalters im Niederspannungsbereich angebracht sind. „Die Anforderungen an elektrische Anlagen werden immer höher und gleichzeitig wird immer mehr Leistung übertragen“, erklärt Dahl. Deswegen müssen auch die Schalter ständig verbessert werden. „Die Herausforderung liegt darin, dass die Kontakte zuverlässig schließen und gleichzeitig möglichst wenig Wärme entsteht, denn das bedeutet Stress für das Material und Stromverlust“, sagt Dahl.
Sein Rotor funktioniert im Prinzip wie eine Kinderwippe auf dem Spielplatz, bei der beide Seiten der Wippe in Schwebe verharren sollen: Das gelingt nur, wenn die Kräfte auf beiden Seiten genau ausbalanciert sind „Das Problem sind hier zum Einen die Toleranzen und zum Anderen der im Betrieb des Schalters zu erwartende Verschleiß,“, erklärt Dahl. Denn einerseits muss der Rotor den Strom sicher unterbrechen, andererseits den Strom sicher führen. Dabei handelt es sich um ein klassisches Problem im Schalterbau.
„Es gibt bestimmt hundert Patente, die mögliche Lösungen beschreiben“, sagt Dahl. Seine Lösung hat die Produktverantwortlichen in der Siemens Division Energy Management jedenfalls überzeugt, weil sie zuverlässig funktioniert, platzsparend ist und weniger Energie verloren geht: Die Erfindung geht, wie auch viele andere aus Dahls Entwicklungsteam, in die Produktion. Da der Rotor bei Schaltern für verschiedene Leistungsklassen eingebaut wird, sind Dahl und seine Kollegen auch damit beschäftigt, die Konstruktion an die verschiedenen Baugrößen anzupassen. Die Schalter selbst werden in einem Siemens-Werk in Tschechien hergestellt.
Insgesamt hat Dahl 61 Erfindungen gemeldet, die in 113 Einzelpatenten in 50 Schutzrechtsfamilien geschützt sind. Den Zeitpunkt seines Eintritts bei Siemens kann sich der Konstrukteur und Erfinder gut merken: „Das war kurz nach der Wende 1989“. Dahl, in der damaligen DDR geboren und aufgewachsen, hatte an der Technischen Universität Magdeburg Maschinenbau studiert und sich dabei auf Strömungsmechanik spezialisiert.
Nach einer nur wenige Monate dauernden Tätigkeit bei einem Schaltgerätewerk, das später geschlossen wurde, entdeckte Dahl in der Berliner „Morgenpost“ eine Stellenanzeige von Siemens. Er bewarb sich und wurde sofort eingestellt. „Der Zeitpunkt der Wende war für mich ideal, weil ich meine Berufstätigkeit sozusagen gleich in der neuen Welt beginnen konnte“, sagt Dahl.
Uffe Eriksen
Bessere Kühlsysteme für Windkraftanlagen
„Ein erster Schritt zu einer höheren Leistungsfähigkeit des Hauptlagers ist, die Temperatur eines Hauptlagers mit Fettschmierung kontrollieren zu können“, erklärt Uffe Eriksen. Der 44-jährige Däne forscht seit zehn Jahren bei Siemens im mit Schmiermitteln Bereich Windenergie. Das Hauptlager einer Windkraftanlage ist hohen Belastungen ausgesetzt. Bislang war es nur möglich die Leistung durch eine Kühlung für Lager mit Ölschmierung zu kontrollieren, jetzt funktioniert das auch bei Lagern mit Fettschmierung.
„Bei meiner Arbeit hinterfrage ich den Status Quo, um unsere Produkte einfacher zu machen“, sagt Uffe Eriksen. „Ein einfacheres Produkt können wir günstiger anbieten und machen es damit für unsere Kunden attraktiver“, so der Ingenieur weiter. Deshalb hat Eriksen mit seinem Team im dänischen Brande eineinhalb Jahre lang daran gearbeitet, ein Luftkühlsystem für leistungsstarke Windturbinen zu entwickeln. Die neue Luftkühlung leitet die Außenluft durch die Gondel in den Generator. „Hohe Luftfeuchtigkeit oder Salz können zu Korrosion führen und Schäden an der Maschine verursachen“, erklärt Uffe Eriksen.
Deshalb wird die Luft zunächst gefiltert und entfeuchtet, bevor sie von einem Ventilator zu den temperaturempfindlichen Generatorteilen geblasen wird. Über einen Ausgangskanal strömt die Kühlluft wieder nach draußen, ohne dass zusätzliche Öffnungen im Gehäuse des Generators zur Außenseite hin notwendig sind. Im Vergleich zu einem konventionellen Luft-Wasser-Luft-Wärmetauscher ist die Wärmeübertragung bei der direkten Luftkühlung effizienter, außerdem ist die Konstruktion an sich deutlich einfacher.
„Der große Vorteil der Außenluftkühlung ist aber, dass der Generator durch die bessere Kühlung mehr Leistung produziert“, betont Eriksen. Ein Wärmetauscher arbeite nur mit Temperaturverlust, erklärt er. Das heißt, die niedrigste im Generator zu erreichende Temperatur liegt immer über der Außentemperatur. Deshalb ist die Luftkühlung konventionellen Kühlsystemen überlegen. Durch die niedrigere Temperatur kann der Generator unter höherer Last laufen und so mehr Energie erzeugen.
Uffe Eriksen versteht sich als Teamplayer. „Erfindungen entstehen nicht im stillen Kämmerchen“, sagt der Ingenieur. Und weiter: „Für mich ist es wichtig, mit Kollegen zusammenzuarbeiten, mit denen ich mich austauschen kann.“ Das sei der Vorteil davon, bei Siemens zu arbeiten, meint Eriksen. „Hier sind viele fachkundige Kollegen, mit denen ich diskutieren kann und die sehr gute Simulations-Tools haben“, sagt er.
Es scheint zu funktionieren: Eriksen hat 30 Erfindungen gemeldet, die in 50 Einzelpatenten und 25 Schutzrechtsfamilien geschützt sind.
Dr. Liexiang Fan
Scherwellen-Elastographie: Mit digitalem Tastsinn Tumore früher erkennen
Bei vielen medizinischen Untersuchungen ist es Standard, dass der Arzt den Patienten abtastet – etwa, um herauszufinden, ob sich in bestimmten Geweberegionen Verhärtungen gebildet haben, bei denen es sich um Tumore oder Fibrosen handeln könnte. Diese Art der Untersuchung ist aber nur in relativ oberflächlichem Gewebe möglich. Um auch innere Organe wie die Leber „abtasten“ zu können, entwickelte eine Forschergruppe von Siemens unter Leitung von Dr. Liexiang Fan die Methode der Scherwellen-Elastographie, die während einer Ultraschalluntersuchung angewandt wird.
„Um Scherwellen zu erzeugen, benutzen wir die Methode der Acoustic Radiation Force Impulse (ARFI) “, erklärte Fan. Dabei werden akustische Kurzimpulse ins untersuchte Gewebe ausgesandt, welche lokalisierte mikrometergroße Gewebeverschiebungen zur Folge haben. Fan begann im Jahr 2005 mit den Forschungen zum digitalen Abtasten. Seit Jahren arbeitet das Team rund um den aus China stammenden Wissenschaftler daran, diese Methode zu verbessern. Die Experten im US-amerikanischen Issaquah, dem Siemens-Standort für Ultraschall- Forschung, kooperieren dabei mit der Duke Universität in North Carolina, USA.
„Die Scherwellen-Elastographie wird seit 2008 in die Siemens-Ultraschallgeräte integriert“, sagt der Erfinder. Er ist stolz darauf, mit dieser Untersuchungsmethode einen großen Beitrag zur frühzeitigen Diagnose von Krebserkrankungen und zur Reduzierung von Biopsien zu leisten. „Jetzt ist es möglich, den Grad einer Verhärtung der Leber, also der Leberfibrose, genau in vier verschiedenen Stadien exakt zu messen“, sagt Fan. So gibt es die Möglichkeit, eine bessere Behandlung des Patienten auf ihn abzustimmen.
Die Scherwellen-Elastographie-Technologie nutzt die Tatsache, dass sich die Scherwellen im Gewebe wesentlich langsamer bewegen als Ultraschallwellen. „Erst untersucht der Arzt das Gewebe mit herkömmlichem Ultraschall“, erklärt Fan. „Wenn er auf dem Monitor verdächtige Stellen entdeckt, untersucht er mit Scherwellen- Elastographie in diesem Gebiet weiter.“
Die Scherwellen werden vom selben Ultraschallkopf erzeugt und detektiert. ARFI bewirkt in verhärtetem Gewebe eine geringere Verschiebung als in weichem Gewebe. Fan entwickelte Algorithmen, die aufgrund der Verschiebung und der Veränderung errechnen, wie elastisch das Gewebe ist. Dies ist möglich, weil die Geschwindigkeit, mit der sich die Scherwelle im Gewebe ausbreitet, in direktem Zusammenhang zur so genannten Gewebefestigkeit steht.
„In den ersten Anwendungen errechnete die Software im Ultraschallgerät die mittlere Geschwindigkeit der Scherwellen in einem kleinen Gebiet und gab die Ergebnisse als Zahlen aus“, erklärt Fan. „Seit letztem Jahr ist es uns gelungen, diese Werte auch im Bild darzustellen, was die Diagnose mit Siemens Ultraschall- Geräten noch einfacher macht.“ Verhärtetes Gewebe hat in der Bilddarstellung eine andere Farbe als elastisches Gewebe.
An Methoden der Signal- und Bildverarbeitung hat Fan bereits in China, seinem Geburtsland, gearbeitet. Dort hat er Elektrotechnik studiert und war bereits mehrere Jahre im Beruf, bevor er als 30jähriger in die USA immigrierte. Um zu promovieren, ging er noch einmal an die Universität: In Lake Forrest, North Carolina, nahm er an einem Studiengang zur Medizinischen Bildgebung teil und erhielt im Jahr 2000 seinen PhD.
Gleich im Anschluss begann er seine Forschungstätigkeit bei Siemens Healthcare in Issaquah. In nur zwölf Jahren meldete Fan 64 Erfindungen. Zwölf davon wurden als Einzelpatente in 37 Schutzrechtsfamilien geschützt. Seine Freizeit verbringt Fan mit seiner Frau und den beiden Töchtern. Erholung findet er beim Angeln an einem der zahlreichen Flüsse und Seen des US-Bundesstaats Washington.
Dr. Peter Faubel
Der Weichensteller
In großen Rangierarealen ist es nicht einfach, den Überblick zu behalten, welche Güterwagen sich gerade wo befindet. Da aber jeder Güterzug durch Achsenanzahl und -abstand seiner Wagen ein charakteristisches Profil hat, kann er mittels sogenannter Radsensoren, die an den Gleisen angebracht sind, relativ leicht identifiziert werden. Der Erfinder Dr. Peter Faubel hat diese Geräte so weiterentwickelt, dass sie die Messdaten der überfahrenden Züge drahtlos funken können.
Dank des extrem niedrigen Energiebedarfs des neuen Systems können die Geräte mehrere Jahre im Einsatz bleiben, ohne gewartet werden zu müssen. Die bisher notwendige und teure Verkabelung der Sensoren entfällt. Außerdem eignet sich diese Sensorik und Datenübertragung auch dafür, den Umstellschutz bei elektrisch ortsgestellten Weichen zu gewährleisten. Beide Anwendungen werden zurzeit auf dem Rangierbahnhof des Rheinhafens in Karlsruhe erfolgreich getestet.
Ein großer Rangierbahnhof, der es leicht auf zwei Quadratkilometer Fläche bringt, muss ständig überwacht werden, um zu wissen, welche Züge wo stehen und wie viele Wagen sie haben. Dazu sind bereits seit vielen Jahren so genannte Doppelkontakt- Radsensoren an den Gleisen angebracht. Die Sensoren registrieren, wann ein Rad über sie rollt. Aus dem Zeitabstand, der zwischen dem ersten und dem zweiten Kontakt liegt, errechnet der mitinstallierte Prozessor direkt am Gleis, ob der Zug von links oder rechts gekommen ist, wie viele Achsen und Wagen der Zug hat und – anhand der Achsabstände – um welche Wagentypen es sich handelt.
„In Europa haben wir einen sehr bunten Wagenpark mit recht unterschiedlicher Achsenanzahl und unterschiedlichen Achsenabständen. Darum kann man aus den Messergebnissen der Sensoren sehr gut den ‚Fingerabdruck’ des Zuges errechnen“, erklärt Erfinder Faubel. Für die Energieversorgung der Funkverbindung und der Sensoren werden die Geräte mit einer Batterie oder einem Solarpanel und Akku ausgestattet. „Der Energieverbrauch ist so gering, dass die Geräte nicht öfter gewartet werden müssen als die verkabelten herkömmlichen Radsensoren“, sagt Faubel.
Da die Funktechnik, mit der die Geräte ausgestattet sind, den speziellen Sicherheitsanforderungen für den Zugverkehr entspricht, können sie auch für die so genannte Freimeldung von elektrisch ortsgestellten Weichen eingesetzt werden. Dabei handelt es sich um Weichen, die früher per Hand während des Rangierbetriebs umgestellt wurden. Dafür mussten die Rangierer vom Wagen springen und buchstäblich Hand an die Weiche legen, was häufig zu Unfällen führte und außerdem viel Zeit kostete.
Jetzt stellt der Rangierer die Weichen um, indem er einen Schlagtaster am Gleis bedient, den er vom Fenster, aber auch von Rangiertritt oder vom Boden aus erreichen kann. Die Weiche darf aber nur dann passiert werden, wenn sichergestellt ist, dass sie sich nicht wieder umstellt, während der Zug über sie rollt. Dafür erfassen die Doppelradsensoren, wo sich die Achsen des Zuges befinden, und senden die Informationen über eine Kurzfunkstrecke an die Steuerung der Weiche.
Das Protokoll der Kurzfunkstrecke hat Faubel zusammen mit seinem Kollegen Wolfgang Windolf so entwickelt, dass es den Sicherheitsanforderungen im Rangierverkehr entspricht. Faubel, der im Herbst 2014 in den Vorruhestand gegangen ist, blickt auf eine sehr abwechslungsreiche Tätigkeit bei Siemens zurück. Er fing direkt nach dem Studium der Elektrotechnik an der Ruhr-Universität Bochum und Promotion an der Universität Dortmund bei Siemens an, damals im Bereich Automatisierungstechnik am Standort Nürnberg.
Viele Jahre war er für die Entwicklung von Software zuständig, die nur in Ausnahmefällen patentfähig ist. Umso erstaunlicher ist es, dass er auf die Zahl von 61 Erfindungsmeldungen blicken kann, die in 44 Einzelpatenten in 24 Schutzrechtsfamilien mündeten. „Ich habe an Workshops zur Förderung von Innovationen teilgenommen. In dieser Zeit entstanden in der kreativen Atmosphäre und dem lebendigen Austausch mit Kollegen sehr viele Ideen für neue Technologien“, klärt Faubel auf.
Arbeitsam wird es auch im Vorruhestand für Faubel: Mit seiner Frau will er etliche Projekte in Haus und Garten vorantreiben und sich wieder aktiv an der Arbeit im Kirchenvorstand seiner Gemeinde beteiligen. Die vier Kinder sind inzwischen groß und einige bereits aus dem Haus.
Dr. Christoph Lehmann
Ein neuer Dreh für Gas- und Dampfturbinen
Gas- und Dampfturbinen werden in ihrer Leistung ständig optimiert, um mehr Energie erzeugen zu können. Häufig sind neue Materialien oder Produktionsmethoden der Ansatz für solche Verbesserungen. Die Idee von Dr. Christoph Lehmann hingegen beruht ganz einfach darauf, bereits bestehende Komponenten des Turbinen-Generator-Wellenstranges anders zu nutzen. Lehmann arbeitet in der Division Power and Gas in Mülheim an der Ruhr, wo Siemens große Dampfturbinen und Generatoren entwickelt und herstellt.
„Vor einigen Jahren war ich an der Planung des weltgrößten Dampfturbinen-Generators für ein finnisches Atomkraftwerk beteiligt“, erklärt Lehmann. Dabei habe er sich häufig mit den Plänen beschäftigt und eines Tages eine Art Geistesblitz gehabt: Eine Gas- oder eine Dampfturbine hat am Anfang ihres Wellenstrangs einen öldruckbetriebenen Hydraulikmotor, der nur dazu dient, die Welle zu drehen, wenn die Turbine abgeschaltet wird. „Das langsame Drehen verhindert, dass sich die Welle während der Abkühlung von Betriebstemperatur von einigen 100 Grad Celsius auf Umgebungstemperatur von etwa 20 Grad Celsius durchbiegt“, erklärt Lehmann.
Am anderen Ende des Wellenstrangs haben viele Turbosätze für den Generator weitere Hilfsgeneratoren, die Haupterreger- und die Hilfserregermaschine, wobei letztere die Spannung für den Haupterregermaschine erzeugt, die den Generator erregt. „Ich habe geprüft, wie stark die Leistung der Hilfserregermaschine ist und berechnet, dass diese ausreichen würde, um den Wellenstrang zu drehen, wenn man sie als Motor einsetzt“, sagt Lehmann.
Bei der Hilfserregermaschine handelt es sich um eine permanenterregte Synchronmaschine. Für den Drehbetrieb muss sie an ein Drehstromspeisegerät angeschlossen werden, das mit variabler Spannung und Frequenz betrieben werden kann. So wird die Synchronmaschine zum Motor, der genau mit der Frequenz arbeitet, die für das langsame Drehen des Wellenstrangs notwendig ist. Damit kann der öldruckbetriebene Hydraulikmotor wegfallen, was eine erhebliche Einsparung bei den Herstellungskosten bedeuten würde.
„Zurzeit analysieren wir, welche Kosten das Umschalten von Generatorauf Motorbetrieb bei dem Hilfsgenerator verursacht, dann könnten wir bei einem Testbetrieb probieren, wie meine Idee funktioniert“, sagt Lehmann.
Lehmann hat Elektrotechnik an der RWTH Aachen studiert und an der Universität Duisburg mit einem Thema über Elektrische Maschinen promoviert. Bereits während der Doktorarbeit arbeitete er mit der Kraftwerksparte von Siemens in Mülheim an der Ruhr zusammen, wo er nach seinem Abschluss auch tätig wurde. Seine 30 Jahre bei Siemens waren immer geprägt von Entwicklungsarbeiten. Heute ist Lehmann Consultant Manager und berät seine Abteilung in allen technischen Fragen.
Er hat hundert Erfindungen gemeldet, die in 123 Einzelpatenten und 57 Schutzrechtsfamilien geschützt sind. Seine besten Ideen für Erfindungen hat Lehmann bei Spaziergängen am Wasser, die er gerne zusammen mit seiner Frau unternimmt. „Gerade wenn ich ungestört und ohne Druck meinen Gedanken nachhänge, fallen mir Lösungen ein“, erzählt er. Lehmann besucht häufig Trödelmärkte und sammelt neben altem Spielzeug auch Technikbücher über Kraftwerke und Generatoren. „Dort finde ich auch viele Anregungen“, sagt er.
Dieses Jahr plant Lehmann, in den Vorruhestand zu gehen und freut sich darauf, mehr Zeit für seine vielen Interessensgebiete zu haben. Dazu zählt auch das Singen in einem Gospelchor, Bassgitarre spielen und Lautsprecher zu entwickeln.
Joachim Lohmeyer
Rettungswege für Datenpakete
Die Energie, die ein Kraftwerk erzeugt, wird über automatisierte Stromnetze weiter transportiert und verteilt. Als Informationsübertragungsstandard für die Automatisierungssoftware setzen die Betreiber das industrielle Ethernet ein, das über Kupfer- oder Glasfaserkabel Daten überträgt. „Das industrielle Ethernet wird seit den 80er Jahren kontinuierlich weiterentwickelt und seit langem in der Stromverteilung eingesetzt. Hier verbindet es die Leitebene mit der Automatisierungsebene“, erklärt Joachim Lohmeyer.
Der studierte Informatiker befasst sich seit vielen Jahren mit Informationstechnologie im industriellen Bereich. Seit etwa zehn Jahren wird das Ethernet auch für die Informationsübertragung in den Schaltanlagen von Stromverteilungsnetzen eingesetzt. Die großen Umspannwerke, die den Strom auf untergeordnete Stromnetze weiter verteilen, entsprechen in ihrer Ausdehnung mehreren Fußballfeldern.
„Wenn hier alle Geräte Punktzu- Punkt miteinander per Kabel verbunden werden müssen, ist das aufwendig und teuer“, erklärt Lohmeyer. Bei Ethernet hingegen reicht eine Schnittstelle pro Gerät aus, um mit allen anderen Geräten Daten über das Ethernet austauschen zu können. Damit steigt jedoch die Gefahr, dass ein Ausfall im Kommunikationsnetz weite Teile eines Stromverteilungsnetzes betrifft. Eine Sicherheitsmaßnahme ist es daher, die Kommunikationsnetze redundant, also mit mehreren Übertragungswegen zwischen den Geräten, auszulegen.
Fällt ein Weg aus, gibt es noch weitere. Eine weitere Möglichkeit besteht darin, die Geräte ringförmig miteinander zu verbinden. Fällt ein Teil eines Rings aus, führt der Weg über den Rest des Rings zum Ziel. Große Anlagen werden in mehrere Subsysteme aufgeteilt, die parallele und ringförmige Kommunikationsnetze verwenden. Diese Subsysteme werden über mehrere Schnittstellen miteinander verbunden. So wird verhindert, dass mehrere Fehler in verschiedenen Subsystemen den gesamten Übertragungsweg lahm legen.
„Dabei muss man aber sicherstellen, dass sich die Informationen nicht in Endlos- Schleifen bewegen“, erklärt Lohmeyer. Die Schnittstellen zwischen den einzelnen Übertragungsebenen fungieren zugleich als Sender und als Empfänger der Datenpakete. Eine bisher angewandte Lösung sperrt die redundanten Übertragungswege und hebt sie nur auf, wenn ein Gerät ausfällt und damit die Übermittlung unterbrochen wird. Das führt allerdings zu Verzögerungen, denn der Ausfall muss erst erkannt und das Signal für die Freigabe der alternativen Übertragungswege gegeben werden, bevor dann das Datenpaket erneut auf dem alternativen Weg geschickt wird.
Lohmeyer hat dagegen eine Lösung entwickelt, bei der sich die Datenpakete gleichzeitig auf redundanten Übertragungswegen durch das Kommunikationsnetz bewegen. Anhand der Absenderadresse, die jedes Datenpaket trägt, ermittelt das von Lohmeyer mit entwickelte Gerät, eine so genannte Redundanz-Box an der Schnittstelle zwischen redundant gekoppelten Teilnetzen, in welche Richtung das Datenpaket geschickt werden muss, die entgegen gesetzte Übertragungsrichtung wird gesperrt. So werden Endlos-Schleifen, die letztlich zur Überlastung und damit zum Ausfall des Kommunikationsnetzes führen würde, verhindert.
Lohmeyers Erfindung wurde bereits in einem Siemens-Produkt umgesetzt, dem Industrial Ethernet Switch SCALANCE X204RNA, das auch bereits in einigen Stromnetzen im Einsatz ist.
Lohmeyer hat Informatik an der Technischen Universität Karlsruhe studiert und seine Berufstätigkeit vor 29 Jahren bei Siemens begonnen. „Auch in meiner Freizeit bin ich ein Tüftler und Bastler“, erzählt er. Zurzeit fasziniert ihn besonders die Technologie des 3D-Drucks. „Dabei geht es mir weniger um das gedruckte Endergebnis, sondern um den Aufbau und die Software“, erklärt er.
Der Erfinder ist verheiratet und lebt in Nürnberg. Er hat 33 Erfindungen gemeldet, die in 38 Einzelpatenten in 17 Schutzrechtsfamilien geschützt sind.
Dr. Hubert Schierling
Motorleistung auf den Punkt gebracht
Neueste Antriebstechnik ist für die „Digitale Fabrik“ von großer Bedeutung: Mit punktgenau arbeitenden Motoren lassen sich in der Fertigung viele Verbesserungen erreichen. Dr. Hubert Schierling von Siemens hat sein ganzes Berufsleben neuen Lösungen in der Antriebstechnik gewidmet. Einer seiner jüngsten Erfindungen ist eine neue Regelung, die die Drehzahleinstellung von Elektromotoren – und damit deren Leistung – verbessert. Das Ergebnis: Wo zuvor ein sehr großer Motor eingesetzt werden musste, reicht mit der zusätzlichen Software des Erfinders jetzt ein kleiner.
Seit der Erfindung der Dampfmaschine haben sich Motoren stetig weiterentwickelt. Einen großen Entwicklungsschub setzte die Erfindung der veränderbaren Drehzahleinstellung von Motoren seit den 70er Jahren in Gang, die ergänzt wurde von der ständigen Weiterentwicklung von leistungselektronischen Schaltern. Der Erfinder Schierling begann Mitte der 70er Jahre sein Studium der Elektrotechnik an der damaligen Technischen Hochschule Darmstadt, heute Technische Universität Darmstadt, und promovierte anschließend in der Antriebstechnik.
Gleich danach fing Schierling bei Siemens in Erlangen in der Entwicklung von drehzahlveränderbaren Antrieben an. Seit 27 Jahren ist das Tüfteln an neuen Lösungen sein beruflicher Alltag. „Langweilig wird das nie, denn jede technologische Weiterentwicklung bietet uns Ingenieuren die Möglichkeit, in unserem Gebiet neue Lösungen zu verwirklichen“, erklärt Schierling. Auch die neue Regelung für die Drehzahleinstellung von Motoren ist überhaupt erst realisierbar, seit sich die Rechenleistung von Prozessoren sprunghaft verbessert hat.
Bei der Erfindung handelt es sich um ein zusätzliches Softwareprogramm, das bereits in der neuesten Version von Antriebssteuerungen von Siemens enthalten ist. Es löst ein Problem, das bei einer ganz bestimmten Drehzahleinstellung von Elektromotoren auftritt.
Um die Drehzahl eines Motors einzustellen, muss man ihn mit einer Wechselspannung speisen, deren Frequenz zu der gewünschten Drehzahl passt. Dazu wird die Spannung aus dem Netz zunächst mit einem Gleichrichter in eine Gleichspannung gewandelt. Ein Wechselrichter formt dann diese Gleichspannung wieder in eine Wechselspannung um, indem er die Klemmen des Motors wechselweise mit einem der beiden Pole der Gleichspannung verbindet. Das Hin- und Herschalten geschieht mehr als 1000 Mal pro Sekunde. So entsteht im Mittel die Wechselspannung mit der gewünschten Frequenz.
Wenn der Motor allerdings mit hoher Drehzahl bei sehr hohen Frequenzen läuft, kommt es zusätzlich zu dieser gewünschten Frequenz zu weiteren Frequenzanteilen im Motor: Dieser läuft heiß und die Steuerung schaltet ihn schließlich ab. Für viele industrielle Anwendungen sind aber genau diese Drehzahlen nötig, beispielsweise um den Kompressor eine Druckluftanlage, einen Ventilator oder eine Pumpe mit hoher Leistung anzutreiben.
„Um diesen kritischen Wert trotzdem zu erreichen, musste man deshalb einen großen Motor einsetzen, obwohl rein von der Leistung her ein kleiner eigentlich ausreichen würde“, erklärt Schierling. Indem er genau analysierte, welche physikalischen Vorgänge die zusätzlichen, unerwünschten Frequenzen im Motor verursachen, fand Schierling die Lösung: „Die neue Software regelt das Hin- und Herschalten zwischen den beiden Polen der Gleichspannung genau so, dass die unerwünschte Frequenz nicht entsteht“, erklärt Schierling. Das Ergebnis: Der Motor kann nun auch in der geforderten Drehzahleinstellung laufen, ohne dass er zu heiß wird. Jetzt reicht der kleine Motor aus.
Diese Erfindung ist nur eine von 142, die Schierling im Laufe seiner Karriere gemacht hat. Seine Ideen sind in 321 Einzelpatenten in 109 Schutzrechtsfamilien geschützt. Die hohe Zahl seiner Patente ergibt sich für den Erfinder ganz von selbst: „Ich mache ja den ganzen Tag nichts anderes als Lösungen für Probleme zu suchen.“ Und er sucht eben so lange, bis er ein Erfolgserlebnis hat, „denn das ist es ja, was einen Ingenieur glücklich macht.“
Dem Familienhaushalt – seine beiden Söhne sind fast mit ihrem Studium fertig – kommt das sehr zugute. So musste die Ehefrau des Erfinders noch nie einen Handwerker rufen, um die Waschmaschine oder andere Dinge zu reparieren. Eine besondere Fertigkeit hat Schierling bereits im Reparieren von Fahrradbeleuchtungen erlangt, „das ist ja meist ganz schlechte Qualität und geht dauernd kaputt.“
Dr. Christian Schröter
Bessere CT-Bilder bei geringerer Strahlenbelastung
„Integrierende Detektoren messen über einen Zeitraum die einfallende Lichtintensität, ähnlich wie ein Fotofilm“, erklärt Dr. Christian Schröter. „Ein zählender Detektor hingegen macht es sich zu Nutze, dass Licht aus einzelnen Teilchen besteht und kann jedes einzelne Lichtteilchen messen“, fährt Schröter fort. Der Vorteil: Der zählende Detektor misst nicht nur die Intensität der einfallenden Lichtstrahlen, sondern zudem das energetische Spektrum der Röntgenquanten.
Die damit entstehenden spektral aufgelösten Bilder ermöglichen es unterschiedliche Gewebearten und Materialien zu differenzieren, was verbesserte Diagnosemöglichkeiten erschließt. Mit integrierenden Detektoren waren bisher beispielsweise Jod, das als Kontrastmittel genutzt wird, und Knochen nur schwer voneinander zu unterscheiden. Mit zählenden Detektoren in CTs wird das wesentlich besser möglich sein. Dabei gab es bislang ein Problem: Die neuartigen Detektormaterialien verändern sich unter Bestrahlung und verursachen deshalb Bildfehler.
„Das ist für unsere Kunden natürlich inakzeptabel“, sagt Dr. Christian Schröter. Der 37-jährige hat mit seinem Team eine Möglichkeit gefunden, ein elektronisch generiertes Signal zur Kalibrierung des Detektors zu nutzen. Die Veränderung der Detektormaterialien unter Bestrahlung wird damit erfasst und die Bildfehler korrigiert. „Wenn man weiß, was den Fehler verursacht, kann man ihn korrigieren“, fasst der Diplomphysiker das Prinzip zusammen, der sich seit sieben Jahren mit dem Thema Detektormaterialien beschäftigt.
Dabei verliert Schröter das Geschäft nicht aus dem Blick:„Es würde mich nicht kalt lassen, wenn unsere Konkurrenten in Führung gehen. Deswegen interessiert es mich nicht nur, technologisch Spitze zu sein. Wir dürfen den Kostenfaktor nicht vergessen. Nur, wenn wir Spitzentechnologie zu einem attraktiven Preis anbieten, kann sie auch vielen Menschen zugänglich gemacht werden.“
Die Passion und der Ansporn, besser zu sein als die anderen, das verstehe er als unternehmerisches Denken. Nach seinem Physikstudium an der TU Dresden hat Schröter den Weg in die Wirtschaft eingeschlagen. „Ich wollte an etwas arbeiten, das zum Einsatz kommt“. Deshalb entschied er sich für eine Promotionsarbeit bei Siemens Corporate Technology, der zentralen Forschungs- und Entwicklungsabteilung des Unternehmens. Aber auch in den Münchner Labors war er, für seinen Geschmack, noch nicht nahe genug dran am Geschäft.
„Bei einem Termin in Forchheim habe ich gesehen, dass dort die Computertomographen vor dem Fenster der Kollegen verladen werden. Da war mir klar: Hier will ich arbeiten“. Heute kann Schröter von seinem Fenster aus den Abtransport der neuen CTs beobachten: „Es ist ein tolles Gefühl das fertige Produkt zu sehen, an dem man selbst gearbeitet hat“.
Schröter hat 57 Erfindungen gemeldet, die in 13 Einzelpatenten in 29 Schutzrechtsfamilien mündeten.
Dr. Klaus Wendelberger
Leittechnik auf Knopfdruck
Leittechniken sind das Gehirn und die Nerven eines Kraftwerkes. Damit kann ein Anlagenfahrer in einer Leitzentrale das Kraftwerk einfach via Mausklick steuern und den Prozess über Bildschirme im Blick behalten. Doch die Rechnertechnik hat einen kürzeren Lebenszyklus als die Anlagentechnik, weshalb die Leittechnik nach rund 20 Jahren ausgetauscht und technisch auf den neuesten Stand gebracht werden muss. Ein solcher Austausch ist mit einem gewaltigen Aufwand verbunden.
Der Leittechnik- Lieferant muss das neue Leitsystem auf Basis des alten Systems aufwendig projektieren. Das geschieht mit Hilfe unzähliger Leittechnikunterlagen vom Kraftwerksbetreiber: Wie verlaufen die Kabelwege zwischen der Leittechnik- und der Kraftwerksanlage? Wie wurden bisher die Signale der einzelnen Kraftwerkskomponenten eingelesen und ausgewertet? Und: Wie können die bisherigen Funktionen und Automatismen von der alten Lösung ins neue System übersetzt und übertragen werden? Im Kraftwerksneubau, bei dem ein neues Leitsystem zu liefern ist, sind diese Fragen in äquivalenter Weise auf Basis der Planungsunterlagen für die neue Anlage zu beantworten.
Egal ob Austausch oder Neuinstallation: Beides geschah bisher mittels manuellen Auswertens der unzähligen Dokumente. „Ein irrsinnig zeitaufwendiges Unterfangen“, erinnert sich Dr. Klaus Wendelberger. „Das gilt vor allem für die Übersetzung und Übertragung der Funktionspläne, welche sämtliche programmierte Automatikfunktionen der installierten Leittechnik aufzeigen.“ Nicht selten handelt es sich dabei um mehrere zehntausend Pläne, deren Inhalte bisher mit einem Zeitaufwand von rund zehn Minuten pro Plan ausgewertet, übersetzt und in die Pläne des neuen Systems übertragen werden mussten.
Der promovierte Kybernetiker witterte hier ein großes Optimierungspotenzial und begann 2010 mit seinem Team, den aufwändigen Prozess auf Verbesserungsmöglichkeiten hin zu untersuchen. Die Idee war schnell geboren: „Das Ziel war es, den Projektierungsprozess so weit wie möglich und sinnvoll zu automatisieren“, so der gebürtige Schwabe. „So obliegen die Eingangsunterlagen ohnehin gewissen standardisierten Grundprinzipien. Zwar unterscheidet sich die Funktionssprache von Hersteller zu Hersteller. Aber hier ist es wie bei Fremdsprachen, die man über Jahre paukt: irgendwann beherrscht man diese und kann sie einfach übersetzen.“
In etwa dreieinhalb Jahren der Entwicklung wurde Schritt für Schritt die Idee in die Lösung umgesetzt: Ein computerbasiertes System nutzt nun dieses Wissen. Es liest die Texte und Bilder der vielen tausend Dokumente unter anderem dank semantischer Erkennung nicht nur automatisch aus oder interpretiert diese selbstständig. Es übersetzt diese auch sogleich in die Sprache einer Siemens- Leittechnik. Seit rund einem Jahr (und bisher in zehn Projekten) wird die automatische Übersetzung von Funktionsplänen eingesetzt.
„Wir müssen quasi nur noch die Randbedingungen eines Kraftwerkes in den Rechner eingeben“, erläutert der Ingenieur, der seit 1997 bei Siemens arbeitet. Solche Eingaben beziehen sich etwa auf den Typ des Kraftwerks und dessen Spezifikationen, zum Beispiel die Megawatt- Leistung. „Einfach ausgedrückt reicht dann ein simpler Knopfdruck, ehe das System die fertig projektierte Leittechnik ausgibt“, so der zweifache Familienvater.
Allein die automatische Übersetzung der zigtausend Funktionspläne kostet heute nur noch zwei bis drei Tage Rechenzeit – statt wie bisher ein ganzes Mann-Jahr. Und: „Dank unseres Systems haben wir im kompletten Leittechnik-Engineering bis zu 30 Prozent Kosteneinsparungen. Bei Gesamtkosten, die oft im sechsstelligen Bereich liegen, ist das nicht wenig.“ Gleichzeitig sinkt durch die Automatisierung des Projektierungsprozesses die Fehlerquote, während die Qualität der Leittechnikfunktionen erhöht, die Ressourcenzuordnung verbessert und die Projektlaufzeit drastisch verkürzt wird.
Klaus Wendelberger hat in den 17 Jahren bei Siemens 22 Erfindungen gemeldet. Seine 29 erteilten Einzelpatente sind in 19 Schutzrechtsfamilien geschützt. Der Ingenieur ist ein Kopfmensch, der sich gerne in der Theorie bewegt. Es gibt nur wenige Momente, wo er seinen Kopf abschalten und somit die Seele baumeln lassen kann. Beim Singen im Chor etwa. Oder beim Kitesurfen: „Auf einem Surfbrett zu stehen und sich von einem Drachen ziehen zu lassen und dabei die Kraft des Drachens und gleichzeitig das Brett auf dem Wasser zu beherrschen“, schwärmt er, „da kann ich den Kopf abschalten – das ist ein Riesenspaß.“ Doch auch hier stehen Privates und Berufliches nah beieinander: „Um loslassen zu können, muss ich mich auch hier auf eines besonders verlassen können: Die Automatismen.“
Dr. Kevin Zhou
Brustkorb in 2-D-Ansicht - Rippenbrüche und Metastasen schneller erkennen
Stellen Sie sich vor, ein medizinischer Scan wäre so umfassend und präzise, dass die Position und Funktion jeder einzelnen Körperzelle gespeichert und bewertet werden könnte. Obwohl die technischen Möglichkeiten dafür noch in ferner Zukunft liegen, nähert sich die Wissenschaft dieser Vision in bestimmten Körperregionen bereits an – wenngleich auf Voxel-Ebene, wobei jedes dieser 3-D-Pixel rund 100.000 Zellen repräsentiert. Genau in diese Richtung geht auch die Arbeit von Dr. S. Kevin Zhou und seinem Team.
Dr. Zhou ist Principal Key Expert für die Analyse von Ganzkörperaufnahmen bei Siemens Corporate Technology in Princeton, New Jersey. „Wir arbeiten darauf hin, dass jeder einzelne Voxel eines Scans automatisch gekennzeichnet werden kann“, erklärt Zhou. „Daraus könnten wir schließlich Dienste wie eine semantische Suche entwickeln. Ärzte wären dann in der Lage, unmittelbar auf alle verfügbaren Informationen zu einer bestimmten Körperregion zugreifen.“
Bevor eine solche Entwicklung möglich ist, muss das System sich jedoch zuerst orientieren. Dafür sucht es nach anatomischen Orientierungspunkten; im Brustkorb sind das zum Beispiel das obere Ende der Lunge und das untere Ende der Aorta. „Die Orientierungspunkte sorgen dafür, dass das System nicht durcheinanderkommt und sich zurechtfindet“, sagt Zhou. Hinter dieser Technik steckt die Entwicklung von Software, die lernen kann, Bildinhalte zu identifizieren. Dafür nutzt sie riesige Mengen an Klassifizierungsmerkmalen, die alle Beispiele eines Zielobjekts gemein haben.
Die Software wird über tausende Bilder – zum Beispiel der Leber – trainiert, von denen jedes von Experten kommentiert wurde. Sie hat so die dreidimensionale Form und das Aussehen des anatomischen Zielobjekts gespeichert und kann darüber dieses Objekt in jedem medizinischen Bild identifizieren und aus seiner Umgebung herauslösen – unabhängig von Verdeckungen, Blickwinkel, Bildgebungsverfahren oder Krankheitsbild. Die Methode lässt sich auf immer mehr Teile des Körpers anwenden, von Organen und Knochen bis zu den Umrissen eines Fötus oder einer Läsion. Eine der ersten Anwendungen des Konzepts ist die Entwicklung einer Software, die den Brustkorb und die Wirbelsäule eines Patienten automatisch auf einem CT-Bild erkennt und den Brustkorb virtuell „plattdrückt“, um die Befundung zu vereinfachen.
Das ist ein großer Schritt, denn in vielen Ländern sind Radiologen heute gesetzlich dazu verpflichtet, alle wichtigen Organe und den gesamten Brustkorb auf Anzeichen für Verletzungen oder Krankheiten zu untersuchen – unabhängig vom Grund des Scans. Das gilt auch für die innenliegenden Oberflächen. „Eine Untersuchung der Rippen ist besonders zeitaufwändig, weil die Betrachtung der ganzen gebogenen Oberflächen schwierig ist“, erklärt Zhou. „Das ist eine mühsame und fehleranfällige Prozedur.“ Wenn jedoch der Verdacht auf ein Thoraxtrauma besteht, müssen Rippen und Wirbelsäule unbedingt schnell untersucht werden. „Wichtig ist, die Rippen und Wirbelkörper vollständig und zuverlässig zu untersuchen, um eventuelle Verletzungen zu finden, bei denen eine sofortige medizinische Versorgung nötig ist“, sagt Zhou. „Durch die neue Visualisierungstechnik ist die Erkennungsempfindlichkeit höher, und Knochenbrüche können nicht nur besser, sondern auch schneller erkannt werden.“
Auch Krebstumore, die an den Innenseiten der Rippen entstehen, könnten so schneller entdeckt werden. „Durch die zweidimensionale Darstellung des Brustkorbs und der Wirbelsäule lassen sich auch Knochenmetastasen erkennen, die bei den herkömmlichen Methoden von den Radiologen übersehen werden könnten“, sagt Zhou. Mit der Software, die gemeinsam mit den Siemens-Geschäftseinheiten Computed Tomography und Syngo entwickelt wurde, lässt sich der Brustkorb automatisch vom Rest der Aufnahme segmentieren und „plattdrücken“, so dass der Prozess wesentlich beschleunigt wird. „Über maschinelles Lernen kann das Programm dann die einzelnen Rippen identifizieren und ihre Mittellinien lokalisieren. Dadurch ist es wiederum möglich, jede Rippe auf dem Bild mit einem einfachen Programm zweidimensional darzustellen“, fügt Zhou hinzu.
Die durch sechs Patente – darunter drei von Zhou – geschützte Technologie wurde von Siemens in die neue syngo.CT Bone Reading Software integriert, die seit 2013 auf dem Markt ist. Das Produkt identifiziert, „entfaltet“ und kennzeichnet alle 24 Rippen und auch alle 24 Wirbel automatisch.
Eine unabhängige klinische Untersuchung hat ergeben, dass sich die Befundungszeit durch das Produkt halbiert und die Erkennungsempfindlichkeit von Rippenbrüchen um zehn Prozent steigt. Das wiederum verbessert die Lebensqualität des Patienten und führt zu erheblichen Kosteneinsparungen. Und Einsparungen sind ein wesentlicher Faktor. Dank der Software, die bereits in 116 Krankenhäusern und Radiologie-Praxen in 23 Ländern eingesetzt wird, können pro Vorgang rund zwölf US-Dollar durch eine kürzere Befundungszeit in der Radiologie gespart werden.
Bisher wurden schon tausende Patienten mit der neuen Technik befundet, wobei die Nutzungsrate der Software alle sechs Monate um 50 Prozent ansteigt, sodass in den nächsten fünf Jahren mit Einsparungen von vielen Millionen US-Dollar zu rechnen ist. Darüber hinaus, so Zhou, gäbe es keine vergleichbaren Produkte auf dem Markt – ein Grund dafür, dass das R&D Magazine kürzlich bekanntgegeben hat, dass das Produkt mit dem renommierten R&D 100 Award ausgezeichnet wird. Der „Oscar der Erfindungen“ wird an die 100 innovativsten, neu eingeführten Technologien aus dem Jahr 2013 vergeben.
Für viele Erfinder wären drei Patente ein Grund zum Jubeln – für Zhou (41) dagegen sind sie nur ein Bruchteil seines Beitrags zum riesigen Siemens-Schatz an geistigem Eigentum. In seinen zehn Jahren bei Siemens wurden bereits 31 seiner Erfindungen patentiert. Insgesamt kann er auf 213 Erfindungen stolz sein. Sein Patent für regressionsbasierte Objekterkennung erhielt 2013 den Thomas Edison Patent Award des R&D Council von New Jersey.
Bei einer solchen Erfolgsbilanz kann man sich kaum vorstellen, wie Kevin Zhou noch Zeit für andere Dinge findet, und doch ist er nicht nur Erfinder und Wissenschaftler, sondern auch Ehemann und stolzer Vater eines kleinen Jungen. Lesen und Nachdenken genießt er genauso wie das Spielen mit seinem Sohn. „Das Leben ist eine unendliche Geschichte. Solange wir mitspielen, müssen wir es einfach genießen!“
Dr. Yue Zhuo
Smarter Schutz für Smart Grids
Stromnetze, die nur aus einer Energiequelle gespeist werden, sind bereits jetzt in vielen Regionen Vergangenheit. Energie aus Wind, Sonne und anderen erneuerbaren Quellen trägt immer mehr zur Stromversorgung bei. Daran müssen Stromverteilungsnetze angepasst werden. Sie werden zu so genannten Smart Grids. Sie vor Ausfällen zu schützen, erfordert neue Technologien. Dr. Yue Zhuo, von der zentralen Siemens-Forschung Corporate Technology in China hat einen Algorithmus entwickelt, der die Schutzschalter eines Smart Grids effektiv managt.
Dr. Yue Zhuo und sein Team, das in Peking und Schanghai arbeitet, sind spezialisiert auf die Erforschung von neuen Technologien für Niederspannungsnetze, die bei Siemens in der Geschäftseinheit Low Voltage zu neuen Produkten für Smart Grids weiterentwickelt werden. Das Forscherteam hat eine neue Lösung für den Schutz von Netzen mit mehreren Stromquellen erfunden. Damit sich im Falle eines Kurzschlusses nicht große Teile oder gar das gesamte Netz automatisch abschaltet, arbeitet die Vielzahl von Schaltern, die einzelne Netzstrecken miteinander koppeln, nach dem Prinzip der Selektivität.
Damit ist die automatische Abstimmung der Schalter untereinander gemeint: Welcher Schalter ist dem Kurzschluss am nächsten und muss das Netz auf seinem Abschnitt abschalten? Diese Technologie wird zonenselektiver Schutz (Zone Selectivity Interlocking, ZSI) genannt. Dieses System funktioniert allerdings nur, wenn die Elektronen wie bei einer Einbahnstraße immer in die gleiche Richtung fließen. In Netzen mit mehreren Energiequellen werden verschiedene Stromleitungen gekoppelt: Der Stromrichtung kann sich also in jedem dieser Abschnitte umdrehen, weil das Verteilnetz an immer mehr Stellen Strom ein- und ausspeisen muss.
Um bei einem Kurzschluss die richtigen Abschnitte abzuschalten, ist ein zonenselektiver Schutz mit Richtungsbestimmung (Directional Zone Selectivity Interlocking, DZSI) erforderlich, der in Echtzeit die Richtung des Stroms bestimmt. Bisher existierende DZSI-Systeme benötigen erheblich mehr Verkabelungen als der zonenselektive Schutz. Zhuo hat den ZSI mit Hilfe einer neuen Topologie und Stromfluss-Designs die Verkabelung für ein DZSI-System genauso einfach wie für einen zonenselektiven Schutz ohne Richtungsbestimmung gestaltet. Dadurch sinken die Kosten erheblich und die Wartung wird vereinfacht.
Die neue Technologie hat eine Steuerungseinheit für jeden Leistungsschalter und kann als Sender oder Empfänger fungieren und erfordert deswegen keine zusätzliche Verkabelung. Ein weiterer Vorteil der Erfindung besteht darin, dass die Steuerungseinheiten die gesamte Automatisierungseinrichtung des Netzes überwachen und defekte Teile schnell lokalisiert werden können. „Diese Technologie der Selbstüberwachung und -diagnose könnte man auch in Fabriken mit großen Automatisierungsanlagen einsetzen“, erklärt Zhuo.
Noch befindet sich der Algorithmus mitsamt den notwendigen Modulen im Stadium der Prototypentwicklung. Es bestehen jedoch gute Aussichten, dass die Technologie, die im Reich der Mitte erfunden wurde, in die Schalter für Niederspannungsnetze von Siemens implementiert wird. Zhuo hat an der Tsinghua Universität in Peking Steuerungstechnik studiert und nach einer kurzen Station bei einem lokalen chinesischen Unternehmen und einem internationalen Unternehmen vor neun Jahren bei Siemens angefangen.
„Ich war der erste Mitarbeiter des neuen Teams von Corporate Technology in Peking“, erzählt er. Seither ist das Team für die Entwicklung von neuen Technologien für Automatisierungs- und Steuerungssysteme stetig gewachsen. Heute ist Zhuo der Leiter einer 30-köpfigen Forschergruppe. In den neun Jahren hat Zhuo 123 Erfindungen gemeldet, von denen 21 Einzelpatente in 82 Schutzrechtsfamilien geschützt sind.
Mehr Informationen zu Siemens:
![]() |
Siemens Aktiengesellschaft |
![]() |
Wittelsbacherplatz 2 |
![]() |
80333 München |
![]() |
Tel. +49 89 636-00 |
![]() |
Fax +49 89 636-34242 |
![]() |
E-Mail: contact@siemens.com |
War dieser Artikel für Sie hilfreich?
![]() |
![]() |
![]() |
![]() |
![]() |
Bitte bewerten Sie diese Seite durch Klick auf die Symbole.
Zugriffe heute: 2 - gesamt: 9311.