Montage hydrodynamischer Gleitlager
Servopresse der aiPRESS-Baureihe im Einsatz
Die Montage hydrodynamischer Gleitlager in einen Rotor ist äußerst diffizil. Damit im Einsatz eine optimale Funktion gegeben ist, müssen die positionsbestimmenden Lagerelemente des Rotors auf den Mikrometer genau zueinander positioniert sein. Beim Fügen entstehen jedoch Kräfte, die sich negativ auf den Pressprozess auswirken und so reproduzierbare Ergebnisse oft nicht ermöglichen. Erforderlich ist deshalb eine Presse, die besonders steif ist und intelligent auf die auftretenden Kräfte reagieren kann. Die Precision Motors Deutsche Minebea GmbH (PM DM) setzt deshalb auf die innovativen Präzisionspressen der Baureihe aiPRESS von IEF-Werner.
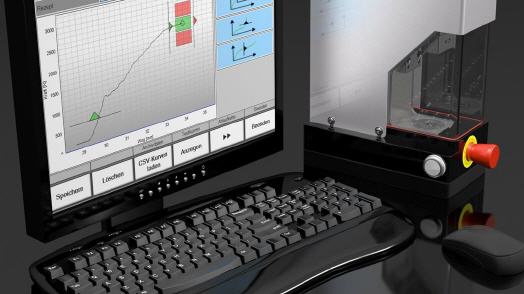
Hydrodynamische Gleitlager stellen selbst unter hohen Belastungen sowie bei hohen Drehzahlen einen verschleißfreien Dauerbetrieb sicher. Aufgrund dieser positiven Eigenschaft setzen Konstrukteure hydrodynamische Gleitlager häufig in Verbrennungsmotoren ein, um Kurbelwellen zu lagern. Sie eignen sich zudem sehr gut für extrem schnelldrehende Läufer – beispielsweise in Turboladern.
Ein weiteres großes Anwendungsfeld sind Antriebsmotoren von Festplatten-Laufwerken. Diese rotieren in der Regel mit Geschwindigkeiten von 5.400 bis 10.000, in Hochleistungsrechnern und Servern bis 15.000 Umdrehungen in der Minute. Die Herstellung solcher Motoren gehört zum Kerngeschäft der Precision Motors Deutsche Minebea GmbH (PM DM). Das Unternehmen mit Sitz in Villingen-Schwenningen ist das größte Motorenentwicklungszentrum im internationalen Verbund der japanischen Minebea Co. LTD., Tokyo.
Der Konzern beschäftigt weltweit mehr als 53.000 Mitarbeiter und zählt zu den führenden Herstellern mechanischer und elektronischer Bauteile. „Für die Herstellung der Antriebsmotoren für Festplatten eignen sich hydrodynamische Gleitlager besonders gut. Denn neben ihrer außergewöhnlichen Standfestigkeit verursachen sie nur geringe Laufgeräusche und lassen sich relativ günstig herstellen“, erklärt Andreas Meyer, Entwicklungsleiter bei der IEF-Werner GmbH in Furtwangen. Um diese Lager effizient und vor allem mit konstant hoher Qualität montieren zu können, wandte sich PM DM an den Automatisierungsspezialisten IEF-Werner.
Auf den Abstand kommt es an
Ein hydrodynamisches Gleitlager besteht aus einem Stator und einem Rotor, sowie zwei konischen Lagerelementen. Der Rotor wird über die beiden Lagerelemente in Position gehalten. Die konischen Lager werden auf den Stator (Welle) gepresst, dürfen aber den Rotor nicht berühren. „Für die Funktion ist der richtige Abstand ausschlaggebend. Stimmt dieser, gleitet das Lager optimal auf einem hauchdünnen Ölfilm mit minimaler Reibung“, erläutert Meyer. Der Abstand der doppelkonischen Lager zueinander darf hierbei eine Toleranz von zwei Mikrometern weder unter- noch überschreiten. Ist der Abstand zu groß, flattert das Lager und der Ölfilm reißt ab. Ist der Abstand zu klein, sitzt das Lager zu fest und läuft heiß.
„Damit waren besondere Herausforderungen an uns gestellt“, sagt Meyer. Die doppelkonischen Lager müssen nach dem Fügen im Rotor sicher halten. Dies wird über eine Presspassung sichergestellt. Dementsprechend wirken hohe Kräfte, welche sich auf Systembauteile wie Servomotor, Kupplungssystem, Axiallager, C-Gestell sowie auf die Bauteile selbst auswirken. Variieren die Maßtoleranzen innerhalb einer Bauteilcharge, entstehen sogar unterschiedlich hohe Deformationen. „Jeder Pressprozess erzeugt somit individuelle Störgrößen, die zu verschieden großen Abweichungen von der Soll-Einpressposition führen. Erforderlich ist deshalb ein besonders steifes und präzises System, das mit den dynamischen Kräften intelligent umgehen kann“, erläutert Meyer.
Die Lösung: Präzisionspressen von IEF-Werner
IEF-Werner hat mit der aiPRESS-Baureihe Systeme im Programm, die flexibel aufgebaut sind und sich sowohl in Fertigungslinien als auch in Handarbeitsplätze integrieren lassen. Die Basis der Presse bildet ein massives und verwindungssteifes C-Gestell aus Werkzeugstahl. Der Antriebsstrang besteht aus einer Präzisionsspindel und einem Servomotor. Eine Präzisionsführung, die die Querkräfte vollständig aufnehmen kann, hält den Antriebsstrang über den gesamten Arbeitsweg präzise in der Spur.
Ein Konfigurationssystem sorgt dafür, dass sich der Antriebsstrang exakt an den benötigten Kraftbereich anpassen lässt. Der Servoantrieb arbeitet somit immer unter optimalen Betriebsbedingungen. Für eine hohe Steifigkeit sorgen zudem zwei Seitenplatten, die rechts und links am C-Gestell befestigt sind. Während die eine fest verschraubt ist, ist die andere Seitenplatte lose gelagert. Damit ist diese gegenüber dem C-Gestell frei beweglich. „Hier haben wir ein Wegmesssystem integriert“, erläutert Meyer. Durch diese unterschiedliche Befestigung der Seitenplatten können wir die Eigenverformung des Systems jederzeit präzise messen und entsprechend kompensieren.
In der Reinraum-Fertigung von PM DM bestückt ein Mitarbeiter das Werkzeug mit den Einzelteilen, die später das fertige Gleitlager bilden. Zunächst muss der Stator mit dem darauf vormontierten unteren konischen Lagerelement in das Werkzeug eingesetzt werden. Danach folgen der Rotor sowie das obere konische Lagerelement. Die Presspinole tastet die Baugruppe an und beginnt mit dem Fügeprozess. Es baut sich eine kontinuierliche Kraft auf, die die Komponenten der Presse staucht sowie die zu fügenden Bauteile verformt.
Der Betrag dieser Verformung kann mit einem Kraftsensor und einem Wegmesssystem - vom Antasten bis zum Losbrechen - exakt ermittelt werden. „Diesen Betrag können wir vergleichsweise einfach mit unseren Messinstrumenten erfassen und mit Presswegvorgaben automatisch verrechnen. Nach der Setzphase wird es jedoch knifflig. Denn nun wirkt die eingeleitete Kraft direkt auf das doppelkonische Lager, das exakt in Position gebracht werden muss. Um das konische Lagerelement in Bewegung zu setzen, muss die Losbrechkraft (Maximalkraft) überwunden werden.
Der entscheidende Faktor
Was passiert, wenn die Losbrechkraft überschritten wird? „Das ist ein extrem kurzer Moment, bei dem das Bauteil unkontrolliert losbricht und für den Bruchteil einer Sekunde dem Pressstempel vorauseilt. Die Vorspannung im System bricht schlagartig ein“, berichtet Meyer. Das Bauteil führt eine Relativbewegung aus, die vom Messsystem nicht erfasst wird. „Die Relativbewegung addiert sich zur vorgegebenen Einpresstiefe hinzu. Eine reproduzierbare Positionierung des Bauteils ist mit herkömmlicher Presstechnik nicht möglich“, sagt der IEF-Ingenieur. Die Techniker von IEF-Werner haben nun eine Methode entwickelt, mit der die aiPRESS die erforderlichen Korrekturfaktoren intelligent und eigenständig ermitteln kann und damit die geforderte hohe Genauigkeit reproduzierbar erreicht. Das Verfahren haben die Schwarzwälder aiTUNING getauft. Es ist zum Patent angemeldet.
Im Testlabor pressten die Ingenieure dazu ein doppelkonisches Lager auf eine Welle und zeichneten dabei die Kraft-Weg-Kennlinie auf. Zum Einsatz kam dabei eine spezielle Werkstückaufnahme mit integrierter Messvorrichtung, welche in der Lage ist, das axiale Spiel zwischen den doppelkonischen Lagern und dem Rotor zu messen. Nun wurde das konische Lagerelement schrittweise um wenige Mikrometer weitergeschoben.
„Aus den Positionswerten konnten wir den tatsächlich zurückgelegten Weg ermitteln“, sagt Meyer. Dieser Vorversuch ergab: Der effektiv zurückgelegte Weg des doppelkonischen Lagers ist immer minimal größer als der vorgegebene Weg. Diese Differenz entspricht der Relativbewegung des Bauteils während des Losbrechmoments. „Aus diesen Verpressungen ermittelten wir die entsprechenden Kenngrößen“, beschreibt Meyer das Testverfahren. „Mit den Kenngrößen konnte eine mathematische Methode entwickelt werden, aus der sich wiederum dynamische Korrekturfaktoren berechnen lassen.“
Auf dem Weg zur optimalen Verpressung
„Wir erreichen absolut überzeugende Ergebnisse“, resümiert der IEF-Ingenieur. Zuerst erfolgt das Vorpressen: Dazu wird das doppelkonische Lager auf die Welle an eine strategisch richtige Position gepresst. Damit ist es nur wenig von der idealen Position entfernt. Die Presse bestimmt mittels der speziellen Werkstückaufnahme das vorhandene Axialspiel und somit den restlichen Weg für die Endpressung. Nach dem Zielpressen misst die Anlage erneut das Axialspiel.
Befindet sich die Position des doppelkonischen Lagers noch nicht innerhalb der Toleranz, erfolgen weitere Pressprozesse. Bei diesem sogenannten „Finishing“-Prozess zieht die Presse die dynamisch ermittelten Korrekturfaktoren der vorausgegangenen Pressvorgänge heran, um die Relativbewegung selbstständig zu kontrollieren. „Es sind dabei höchstens drei weitere Pressvorgänge nötig. Die Prozesssicherheit liegt jetzt bei 99 Prozent“, sagt Meyer. Das Presssystem ist nun im Motorenentwicklungszentrum in Villingen-Schwenningen erfolgreich im Einsatz.
Mehr Informationen zur IEF Werner GmbH:
![]() |
IEF Werner GmbH |
![]() |
Wendelhofstr. 6 |
![]() |
78120 Furtwangen |
![]() |
Tel: +49 (0) 7723 925-0 |
![]() |
E-Mail: info@IEF-Werner.de |
![]() |
www.ief-werner.de |
War dieser Artikel für Sie hilfreich?
![]() |
![]() |
![]() |
![]() |
![]() |
Bitte bewerten Sie diese Seite durch Klick auf die Symbole.
Zugriffe heute: 3 - gesamt: 6187.