Gewichtseinsparung durch Hybridverfahren
Der Laser im Automobilbau
Im März 2014 startete das BMBF-geförderte Verbundvorhaben »KLasse« zur Entwicklung eines Kombinationsverfahrens zum Laserschneiden und zur lokalen Laserentfestigung von Bauteilen aus hochfesten pressgehärteten Stählen. Gemeinsam mit Automobilherstellern und -zulieferern, Partnern aus dem Bereich Stahlherstellung sowie Laser- und Anlagenbau und dem Fraunhofer-Institut für Lasertechnik ILT soll das Konsortium neben verbesserter Crashperformance zur Reduzierung des Gewichts von Fahrzeugen und somit zur Erhöhung der Energieeffizienz im Automobilbereich beitragen.
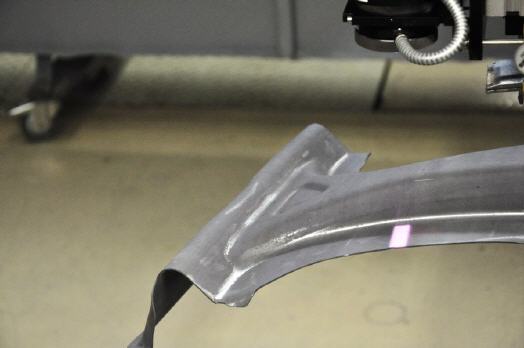
In der Automobilindustrie sind aufgrund ökonomischer, ökologischer wie auch politischer Zwänge Maßnahmen zum effizienteren Energieeinsatz gefordert. Eine wichtige Stellschraube ist die Reduzierung des Fahrzeuggewichts, wobei gleichzeitig die Anforderungen an die Fahrzeugsicherheit steigen. Um diesen Anforderungen gerecht zu werden, kommen zunehmend Bauteile aus pressgehärteten hochfesten Stählen zum Einsatz. Diese Stähle erreichen bei einer geringeren Blechstärke und damit geringerem Gewicht ein gleich gutes oder sogar verbessertes Crashverhalten von PKW-Strukturen wie zum Beispiel in B-Säulen oder im seitlichen Schweller. Die hohe Festigkeit dieser Werkstoffe hat jedoch auch zu notwendigen Änderungen bei der Weiterbearbeitung wie dem Beschneiden und dem Fügen geführt.
Als Beschnittverfahren hat sich das Laserschneiden etabliert, da mechanische Verfahren zu raschem Werkzeugverschleiß führen und bei neuen Güten mit einer weiter gestiegenen Festigkeit wie dem MBW-K1900 nicht mehr einsetzbar sind. Allerdings entstehen beim Laserschneiden Aufhärtungen in der Randzone der Schnittkante. Das Fügen erfolgt im Wesentlichen durch das weitverbreitete Punktschweißen. Beim Punktschweißen wiederum entsteht eine Wärmeeinflusszone mit deutlicher Härtereduzierung um den Schweißpunkt. Mechanische Verfahren für den Mischbau wie Clinchen oder Stanznieten sind aufgrund der hohen Festigkeit bei pressgehärteten Stählen kaum noch möglich.
Beide Effekte beeinträchtigen die Crasheigenschaften des Bauteils. Durch eine lokale Wärmebehandlung der Bauteile im Schnittkantenbereich und in den Fügezonen können die Eigenschaften des Werkstoffs lokal angepasst und somit seine Crasheigenschaften verbessert werden. Dieser zusätzliche Prozessschritt verursacht jedoch Mehrkosten. Aus ökonomischen Gründen ist es daher sinnvoll, die lokale Wärmebehandlung mit dem Schneidprozess zu kombinieren.
Für das Kombinationsverfahren wird eine hybride Laserstrahlquelle bestehend aus einem Diodenlaser für die Wärmebehandlung und einem Faserlaser für das Schneiden entwickelt. Weiterhin arbeitet das Konsortium an der Entwicklung eines hybriden Schneid-Wärmebehandlungs-Kopfes. Beide Komponenten werden in einem Anlagenkonzept für die 3D-Bearbeitung integriert. Das Projekt wird vom Bundesministerium für Bildung und Forschung (BMBF) gefördert und vom Projektträger VDI begleitet. Bis zum Jahr 2017 werden die Verfahrensgrundlagen erarbeitet sowie eine Demonstratoranlage aufgebaut und erprobt.
Mehr Informationen zum Fraunhofer ILT:
![]() |
Fraunhofer-Institut für Lasertechnik ILT |
![]() |
Steinbachstr. 15 |
![]() |
52074 Aachen |
![]() |
Telefon +49 241 8906-0 |
![]() |
www.ilt.fraunhofer.de |
War dieser Artikel für Sie hilfreich?
![]() |
![]() |
![]() |
![]() |
![]() |
Bitte bewerten Sie diese Seite durch Klick auf die Symbole.
Zugriffe heute: 3 - gesamt: 5970.