Kugelzapfen für Fahrwerke effizient produziert
Niro statt Vergütungsstahl
Die ZF Friedrichshafen AG hat Kugelzapfen aus nichtrostendem Stahl entwickelt. Als Alternative zu konventionell eingesetzten nitrierten Kugelzapfen aus Vergütungsstahl sind diese per se korrosionsgeschützt. Die Fertigung erfolgt effizient durch Kaltfließpressen – zeit- und energieaufwendige Wärmebehandlungs- und Beschichtungsverfahren entfallen. Anwender profitieren von geringeren Herstellungskosten und einer längeren Lebensdauer des Bauteils. Die Entwicklung der Spezialstahllösung erfolgte gemeinsam mit der Swiss Steel AG, einem Unternehmen der Schmolz + Bickenbach-Gruppe.
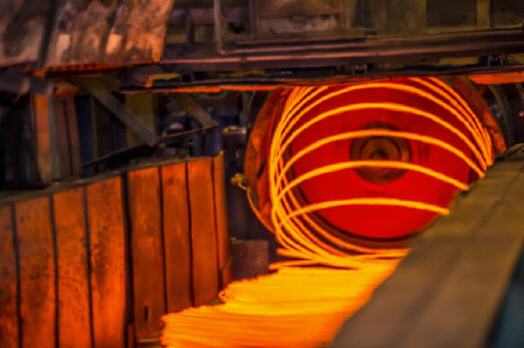
Die ZF Friedrichshafen AG zählt mit rund 72.600 Mitarbeitern und 122 Produktionsgesellschaften in 26 Ländern zu den weltweit führenden Technologiekonzernen in der Antriebs- und Fahrwerktechnik. Das Produktportfolio umfasst Getriebe, Lenkungen, Dämpfungsmodule, elektronische Systeme, Fahrwerkkomponenten sowie komplette Achssysteme und -module. Rund fünf Prozent des jährlichen Umsatzes investiert der Konzern in Forschung und Entwicklung.
„Wir verstehen uns als innovatives Unternehmen und arbeiten stets an der Wettbewerbsfähigkeit unserer Produkte“, erklärt Dr. Jochen Kruse, Projektingenieur im Center of Competence für Strukturbauteile der ZF Friedrichshafen AG. „Dafür investieren wir unter anderem in die Erprobung neuer Werkstofflösungen, wie zum Beispiel die Fertigung von Kugelzapfen aus nichtrostendem Stahl.“
Diese Kugelzapfen sind ein wesentlicher Bestandteil von Kugelgelenken, die unter anderem in Spurstangen, Winkelgelenken und Koppelstangen zum Einsatz kommen. Sie übertragen Lenk- und Federbewegungen. Dementsprechend hoch sind die Anforderungen an die mechanisch-technologischen Eigenschaften des eingesetzten Stahls.
Im Mittelpunkt stehen eine hohe Dauerfestigkeit und Zähigkeit sowie ein gutes Reibungsverhalten (Tribologie) und Korrosionsbeständigkeit. Sie sind ausschlaggebend für die Belastbarkeit, Verschleißbeständigkeit und Lebensdauer des Bauteils in der Anwendung.
„Zapfenstreich“ für den Vergütungsstahl
Als Standard greift ZF auf gezogenen Walzdraht aus Vergütungsstahl, wie 41Cr4 oder 42CrMo4, zurück. Um die Kaltumformbarkeit zu verbessern, wird der Vergütungsstahl vor dem Kaltfließpressen weichgeglüht. In mehreren Umformstufen wird der Draht nach den Vorgaben von ZF zum Kugelzapfen gepresst. Die erforderliche Festigkeit erhält das Bauteil durch eine Vergütungsbehandlung. Anschließend dreht ZF den Kugelzapfen auf Endkontur, glättet ihn auf einer Rolliermaschine und transportiert ihn zu einem externen Beschichter.
Um den erforderlichen Korrosionsschutz sicherzustellen, nitriert dieser das Bauteil nach Kundenvorgabe per Gas, Plasma oder im Salzbad und lässt ihn kontrolliert abkühlen. Dieser Prozessschritt kann, einschließlich Transport, bis zu drei Wochen dauern. Wird die Beschichtung vor der Montage des Zapfens beschädigt, ist der Korrosionsschutz des Kugelzapfens nicht mehr vollständig gegeben. Folglich sinkt die Korrosionsbeständigkeit des Bauteils.
„Durchlaufzeit, Energieverbrauch und Transportwege sind mit dem Einsatz von Vergütungsstahl vergleichsweise ineffizient“, so Kruse. „Deswegen haben wir mit unserem langjährigen Partner Swiss Steel eine ökologisch und ökonomisch sinnvolle Alternative entwickelt.“ Ziel war es, einen preisgünstigen und nichtrostenden Stahl zu finden, um die kostenintensiven Prozessschritte Glühen, Vergüten und Nitrieren zu vermeiden.
Wirtschaftliche Alternative: nichtrostender Stahl
„Um die optimale Stahlzusammensetzung in Kombination mit den idealen Prozessparametern zur Erzielung der geforderten Werkstoffeigenschaften zu bestimmen, haben wir zahlreiche Laboruntersuchungen und großtechnische Walzversuche durchgeführt“, erläutert Dr. Ulrich Urlau, Leiter Unternehmensentwicklung bei Swiss Steel.
In Bezug auf die mechanischen Eigenschaften legten Swiss Steel und ZF Wert auf ein feinkörniges Gefüge. Es vereint eine hohe Dauerfestigkeit und Duktilität, ohne die Zähigkeit zu mindern, und ist dadurch besonders belastbar. Außerdem spielten ein gutes Kaltverfestigungsverhalten und eine ausreichende Kaltumformbarkeit eine wichtige Rolle. „Der nichtrostende Stahl 1.4003 bringt alle geforderten Grundvoraussetzungen mit“, betont Stephan Hasler, Manager Research & Development bei Swiss Steel. „Der Stahl zeichnet sich durch eine für diese Anwendung ideale Kombination aus Korrosionsbeständigkeit und mechanischen Eigenschaften aus sowie einen verhältnismäßig moderaten Preis.“
Das Know-how von Swiss Steel steckt in der Optimierung des Werkstoffes und der Walzparameter hinsichtlich der Anforderungen von ZF. Bei der Stahlherstellung bildet Stahlschrott die Basis. Diesen schmilzt die Deutsche Edelstahlwerke GmbH, ein Schwesterunternehmen der Swiss Steel, im Elektroofen. Nach dem Legieren entkohlt der Edelstahlspezialist das Material per Vakuumverfahren (VOD), um die Korrosionsbeständigkeit weiter zu erhöhen, und gießt den flüssigen Stahl zu Knüppeln.
Durch gezielte Steuerung von Temperatur und Abkühlung beim Walzen beeinflusst Swiss Steel die mechanisch-technologischen Eigenschaften und das Gefüge des Stahls. Das Ergebnis ist ein niedrigst gekohlter ferritisch-martensitischer Edelstahldraht mit der ZF-internen Bezeichnung X1CrNi12.
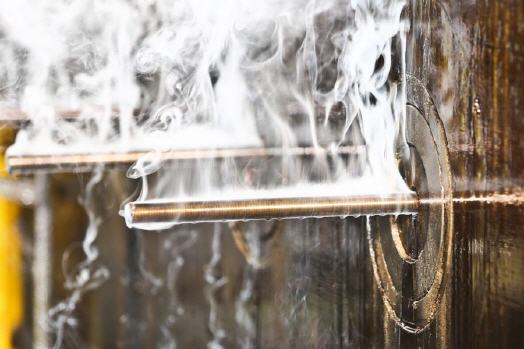
Weiterverarbeitung des Stahls zum fertigen Bauteil
Ein Kugelzapfen mit Halshinterschnitt und Innensechskant war das Testobjekt in der Entwicklungsphase. Um unter anderem das geforderte Festigkeitsniveau von 800–1.000 MPa zu erreichen, standen der Drahtabzug beim Ziehprozess vor der Kaltumformung sowie die Umformstufen beim Kaltfließpressen im Blickpunkt. Sie haben unmittelbare Auswirkung auf die örtlichen mechanisch-technologischen Eigenschaften am Kugelzapfen und müssen aufeinander abgestimmt sein.
Dafür definierten ZF und Swiss Steel gemeinsam mit dem Kaltumformer, der Fuchs Schraubenwerk GmbH, die erforderlichen Prozessparameter. Da der Walzdraht aus X1CrNi12 eine hohe Ausgangsfestigkeit mitbringt, galt es zudem, eine leistungsfähigere Presse und ein stabiles Abschersystem beim Kaltfließpressen einzusetzen. Der Mehraufwand in der Fertigung wird durch eine vergleichsweise kurze Durchlaufzeit kompensiert. Die Qualität des Bauteils aus X1CrNi12 entspricht den Anforderungen in vollem Umfang.
Das belegen die ZF-internen Versuche am gepressten Kugelzapfen: Auch nach längerem Stillstand ist er leichtgängig im Gelenk. Er bringt die erforderliche Festigkeit im Gewinde mit und hält schlagartiger mechanischer Beanspruchung auch bei tiefen Temperaturen stand. Abhängig vom Bauteildesign variieren die Kostenvorteile durch den Einsatz des X1CrNi12. Bei Kugelzapfen mit einem Kugeldurchmesser bis zu 30 mm zeigt sich die Rentabilität des Edelstahls am deutlichsten.
„Die gut funktionierende interdisziplinäre Zusammenarbeit mit Swiss Steel und Fuchs Schraubenwerk war die Voraussetzung für die Entwicklung des Stahls bis zur Marktreife“, so Dr. Kruse. „Unser Ziel ist es, die nitrierten Vergütungsstahlsorten sukzessive gegen den X1CrNi12 auszutauschen.“
Testphase bestanden, Serienreife erreicht
Die Modifikation des 1.4003 für das Kaltfließpressen des Kugelzapfens überzeugte ZF: Die Eigenschaften des Stahls sind vergleichbar mit denen konventionell hergestellter Teile aus Vergütungsstahl. Eine deutliche Verbesserung erreicht der nichtrostende Stahl X1CrNi12 hinsichtlich der Korrosionsbeständigkeit in der Anwendung. Auch die Ökobilanz wird verbessert: Mit X1CrNi12 entfallen schadstoffbelastete Prozessschritte wie das Nitrieren sowie zusätzliche Transportwege. Die Durchlaufzeit in der Fertigung ist spürbar verkürzt, ergo steigt die Flexibilität im Fall von Produktionsschwankungen. Der Anwender erhält ein modernes, effizientes Material und kann gleichzeitig die Gesamtkosten senken.
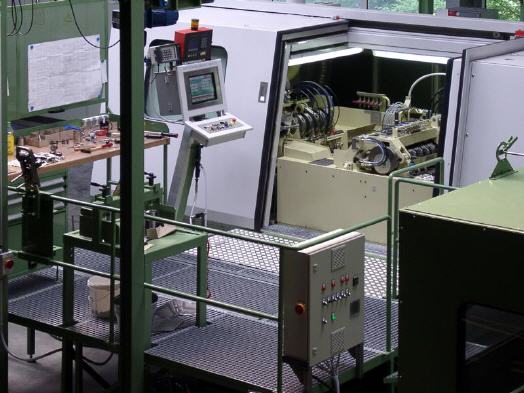
Mehr Informationen zur SCHMOLZ + BICKENBACH AG:
![]() |
Swiss Steel Holding AG |
![]() |
Landenbergstrasse 11 |
![]() |
CH - 6005 Luzern |
![]() |
Tel.: +41 41 581 40 00 |
![]() |
Fax: +41 (0) 41 209 51 04 |
![]() |
www.swisssteel-group.com |
War dieser Artikel für Sie hilfreich?
![]() |
![]() |
![]() |
![]() |
![]() |
Bitte bewerten Sie diese Seite durch Klick auf die Symbole.
Zugriffe heute: 4 - gesamt: 1654.