Schnaithmanns Werkzeugmaschinen-Automation
Einwandfreie Qualität ist garantiert
Schnaithmann Maschinenbau GmbH, Hersteller für Transfer- und Montageanlagen für Automations-, Montage-, Materialfluss- und Handhabungsaufgaben, hat eine Doppelroboter-Automationsanlage an den CNC-Zerspanungsspezialisten Wesa GmbH geliefert. Die Anlage dient der automatisierten Be- und Entladung von Werkzeugmaschinen inklusive hundertprozentiger Qualitätsprüfung der fertigen Werkstücke.
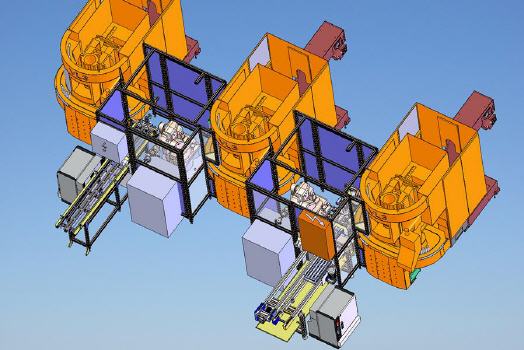
Wesa mit Sitz in Waldstetten in der Nähe von Schwäbisch Gmünd im Großraum Stuttgart bietet mit rund 70 Mitarbeitern CNC-Präzisionszerspanung an. Das Unternehmen versteht sich als Technologiepartner und Systemlieferant, das CNC-Präzisonsteile für Kunden aus unterschiedlichen Branchen fertigt, darunter die Automobilindustrie, für die Wesa mehrfacher A-Lieferant ist. Das Leistungsspektrum für Prototypen wie auch für die Serienfertigung umfasst Drehteile, Frästeile, Oberflächentechnik, Messtechnik sowie Komplettbearbeitung.
Der umfangreiche Maschinenpark des schwäbischen Zerspanungsspezialisten lässt keine Wünsche offen: er besteht aus CNC-Drehzentren, Bearbeitungszentren, Vertikal-Drehmaschinen, CNC-Wälzfräsmaschinen, Rundschleifmaschinen, Tiefbohrmaschinen, Kreissägeautomaten sowie der gesamten Palette konventioneller Bearbeitungsmaschinen mit bestens ausgestatteter Werkzeugvorhaltung.
Bei der von Schnaithmann gelieferten Doppelroboter-Automationsanlage handelt es sich um zwei Roboterzellen zur Be- und Entladung dreier Vertikaldrehmaschinen. Die Zuführung der Rohlinge beziehungsweise Sägeabschnitte erfolgt über eine zweibahnige Schwerkraftrinne, wobei die Werkstücke mit Hilfe der Schwerkraft an das Ende der Rinne rollen und dort vereinzelt werden.
Der Roboter 1 holt ein Werkstück ab und stellt es in die bereitstehende leere Aufnahme der ersten Vertikaldrehmaschine. Dort werden die Rohteile über Schleppkettensysteme in die Maschinen hinein der Spindel zugeführt, wo eine erste Bearbeitungsoperation erfolgt (OP 10, erster Operationsschritt). Anschließend werden die Halbfertigteile aus der Maschine heraus transportiert. Der Roboter 1 holt dann das Halbfertigteil, bläst es ab und führt es der Spänekontrolle zu, wo mit Hilfe einer Kamera Späne innerhalb eines Gewindegangs entdeckt werden und NIO-Teile (Nicht-in-Ordnung-Teile) ausgeschleust werden.
Anschließend belädt der Roboter 1 eine Messstation, wo kritische Merkmale zu 100 Prozent vermessen werden. Die Messstation ist mit der Bearbeitungsmaschine gekoppelt und korrigiert automatisch die betreffenden Merkmale; NIO-Teile werden separat ausgeschleust. Nachfolgend entlädt und wendet der Roboter 1 das Halbfertigteil und belädt die zweite Maschine, wo der nächste Bearbeitungsschritt erfolgt (OP 20). Der Roboter 2 holt das Halbfertigteil aus der zweiten Maschine, bläst es ab und führt das Werkstück einer zweiten Messvorrichtung zu, wo wie zuvor kritische Merkmale zu 100 Prozent gemessen, automatisch korrigiert und fehlerhafte Teile ausgeschieden werden.
Im Anschluss führt der Roboter 2 die Werkstücke der dritten Maschine (OP 30) zu, ebenfalls nach demselben Ablauf wie bei den vorherigen Be- und Entladevorgängen. Danach holt der Roboter 2 das Fertigteil aus OP 30 ab und führt es einer separaten Bürst- und Entgratstation sowie einer weiteren Abblasstation zu. Dann transportiert der Roboter 2 das Fertigteil zu einer Prüfstation, wo wiederum mehrere Qualitätsmerkmale sichergestellt werden und NIO-Teile gegebenenfalls ausgeschleust werden.
Leere Mehrfachladungsträger werden nun der Roboterzelle über ein Schnaithmann-Staurollenketten-Bandsystem zugeführt, wo die fertigen Teile in die Träger eingelegt werden. Das Bandsystem transportiert die nun vollen Ladungsträger zum Werker, der sie manuell entlädt. Durch die durchgängig integrierten Messsysteme sind Auswertungen mittels SPC (statistical process control, statistische Prozessregelung) und CAQ (computer-aided quality assurance, rechnerunterstützte Qualitätssicherung) möglich.
Trotzdem kann nach jedem Fertigungsschritt auf Anforderung des Werkers ein Teil zur weiteren Prüfung angefordert und ausgeschleust werden. Die vollen Ladungsträger mit den fertigen Teilen werden direkt an den Endkunden, der die Werkstücke verbaut, verschickt – dies erfordert, dass alle Qualitätskriterien innerhalb des automatisierten Verarbeitungsprozesses zu 100 Prozent erfüllt sind.
Die hundertprozentige Prüfung aller qualitätsrelevanten Merkmale ist nur eines der Vorteile der von Schnaithmann realisierten Automationsanlage. Die Systemlösung zeichnet sich durch eine kompakte Bauweise aus, bei der Schnaithmann-Standardkomponenten der Reihen MTS (modulare Transfersysteme) und FPS (flexible Profilsysteme) mit kundenspezifischen Sonderlösungen kombiniert wurden. Von Engineering und Konstruktion über Montage, Elektrik, Steuerung, Roboterprogrammierung und Inbetriebnahme bis zur weiteren Betreuung vor Ort und After-Sales-Service bietet Schnaithmann alle Leistungen aus einer Hand.
Neben der kurzen Realisierungszeit spielen auch die räumliche Nähe zu Schnaithmann mit Sitz in Remshalden in der Nähe von Stuttgart und der gute persönliche Draht zu Schnaithmanns Bereichsleiter für Materialfluss- und Handhabung, Marc Burkhardt, eine Rolle. „Durch die sehr enge und vertrauensvolle Zusammenarbeit bereits bei der Konzeption des Gesamtsystems wie auch in der Hochlaufphase konnte hier gemeinsam eine optimale und uneingeschränkt prozesssichere Lösung gefunden werden, die maximale Verfügbarkeit bei gleichzeitiger hundertprozentiger Prüfung aller qualitätsrelevanter Kriterien in der geforderten Taktzeit ermöglicht,“ erklärt Marc Burkhardt, der das Projekt bei Schnaithmann verantwortet. „Wesa kann sich somit darauf verlassen, dass nur einwandfreie Teile in der gewünschten Stückzahl verschickt werden.“ Wesa hat bereits mehrere Schnaithmann-Anlagen dieser Art im Einsatz, weitere befinden sich im Bau beziehungsweise sind in Planung.
Das Erfolgsrezept des von Karl Schnaithmann 1985 gegründeten Unternehmens mit heute 190 Mitarbeitern ist die Entwicklung der beiden Systeme MTS und FPS, die nach dem Baukastenprinzip verbaut werden: die modularen Transfersysteme bieten eine große Auswahl an Bandsystemen für unterschiedlichste Anwendungen, während die flexiblen Profilsysteme ein komplettes Baukastensystem an Komponenten für Zuführung und Handhabungstechnik umfassen.
Durch die Kombination beider Systeme und die Einbindung von Sonderteilen wie Linear- und Greiftechnik, Roboter oder Bearbeitungskomponenten entstehen maßgeschneiderte kundenspezifische Lösungen, die Schnaithmann an eine Vielzahl von Branchen in alle Welt liefert, darunter die Automobilproduktion, der Sondermaschinenbau, der Werkzeugmaschinenbau und die Hausgeräteherstellung. Die Systeme lassen sich in jedes bestehende Fertigungs- und Montagekonzept integrieren und können auch zu einem späteren Zeitpunkt an die jeweiligen Anforderungen der Produktion und den gewünschten Automatisierungsgrad angepasst werden.
Mehr Informationen zu Schnaithmann Maschinenbau:
![]() |
Schnaithmann Maschinenbau GmbH |
![]() |
Fellbacher Straße 49 |
![]() |
73630 Remshalden-Grunbach |
![]() |
Tel.: +49 (0) 71 51-97 32-0 |
![]() |
Fax: +49 (0) 71 51-97 32-190 |
![]() |
E-Mail: info@schnaithmann.de |
![]() |
www.schnaithmann.de |
War dieser Artikel für Sie hilfreich?
![]() |
![]() |
![]() |
![]() |
![]() |
Bitte bewerten Sie diese Seite durch Klick auf die Symbole.
Zugriffe heute: 3 - gesamt: 6552.