UTG: Der Roboter als Blechspezialist
Blechtreiben via Bit und Byte
Aktuell gibt es einen Hype bezüglich der generativen Fertigung, verbunden mit der Vorhersage, dass diese Technik die Herstellung von Produkten revolutionieren wird. Das ist zweifelsohne wahr, doch werden auch andere Fertigungsarten fit für die Zukunft gemacht. Ein Beispiel ist die automatisierte Blechbearbeitung durch Treiben, bei dem ein Roboter die menschliche Arbeitskraft ergänzt.
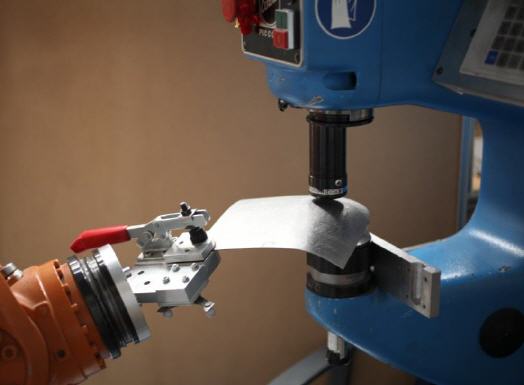
Handwerkliches Geschick kombiniert mit den Möglichkeiten der unmittelbaren Zustandskontrolle bei der Bearbeitung eines Werkstücks sind Fähigkeiten, die der Mensch dem Roboter noch voraus hat. Der Abstand schrumpft jedoch zusehends, wie der Lehrstuhl für Umformtechnik und Gießereiwesen (utg) der TU München zeigt. Dort haben sich Wissenschaftler zum Ziel gesetzt, die Technik der inkrementellen Blechumformung zu automatisieren.
Hauptaugenmerk war, ein flexibles Fertigungssystem zu entwickeln, das in der Lage ist, einzelne Blechkörper direkt aus einem CAD-System in ein reales Werkstück umzusetzen. Wenn dies gelingt, wären Einzelteile aus Blech, wie etwa Kunstwerke oder Prototypenteile, mit weit geringeren Stundensätzen herstellbar, als es derzeit möglich ist. Zur Anwendung soll ein spezieller Treibprozess kommen, das sogenannte ›Kraftformerverfahren‹ des Unternehmens Eckold. Dabei ist der Kraftformer eine Treibmaschine in Form einer C-Gestell-Presse.
Der Prozess erlaubt die Fertigung individueller Blechbauteile mit geometrieungebundenen Universalwerkzeugen und eröffnet im Bereich der Blechverarbeitung ganz neue Möglichkeiten. Ein erfahrener Werker kann mit dem Kraftformer durch geschickte Handhabung nahezu jede gewünschte Form inkrementell herstellen.
Was auf den ersten Blick zumindest für einfache Blechgeometrien nach einer recht simplen Aufgabe aussieht, entpuppt sich bei näherer Betrachtung als Feld mit zahlreichen Unbekannten und unvermuteten Hindernissen.Das beginnt damit, dass sich Blech beim Umformen bereits bei minimalsten Unterschieden in den einzelnen Blechchargen nicht identisch verhält. Geringe Abweichungen in der Blechdicke beispielsweise führen zu abweichenden Ergebnissen trotz gleicher Arbeitsabläufe in der Blechbearbeitung. Zudem hat der Fertigungsprozess großen Einfluss auf das Ergebnis durch sich ändernde Kontakteigenschaften des Werkzeugs, wie zum Beispiel Tribologie oder Verschleiß, die nicht vorab genau beschreibbar sind.
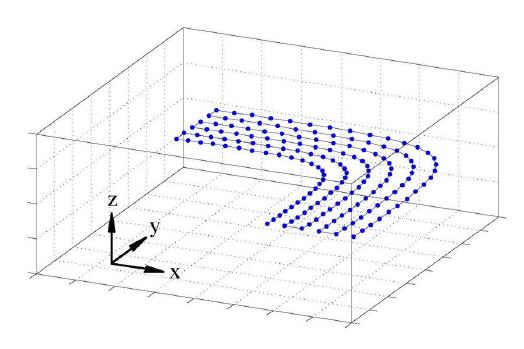
FEM ohne Chance
Die Simulation und Analyse etwa via FEM bietet hier nur bedingt Hilfestellung. Dass diese Techniken in der inkrementellen Blechumformung an ihre Grenzen kommen, ist auf den ersten Blick, insbesondere angesichts der mittlerweile zur Verfügung stehenden Großrechnerkapazität, sehr überraschend. Bei genauerer Betrachtung wird jedoch klar, warum diese Methoden sich schwer in diesem Bereich anwenden lassen.
Die Simulation eines Prozesses stellt eine Approximation des realen Prozessverlaufs dar.
Obwohl die erzielten Ergebnisse die Realität sehr genau widerspiegeln können, entstehen Abweichungen, wenn auch geringer Natur. Das Problem der inkrementellen Verfahren liegt darin, dass Bauteile in der Regel durch sehr viele Einzelschritte erzeugt werden. Will man nun einen Treibprozess simulieren, so ist jeder Schlag auf das Blech mit seinen Auswirkungen zu berechnen. Jeder Berechnungsschritt trägt einen Rundungsfehler. Die schrittweisen Fehler pflanzen sich fort, die Abweichung des Gesamtfertigungsprozesses kann nicht robust abgeschätzt werden und ist somit nicht für die Prozessauslegung nutzbar.
Die hohe Anzahl an inkrementellen Umformungen stellt also ein Problem für die Berechnungen dar. Der Prozess müsste schrittweise in Serie simuliert werden, um die Anzahl an Umformschritten abzubilden. Bedenkt man die enorme Anzahl der Schritte, die für einen praxisrelevanten Treibprozess nötig sind, mit einer jeweilig großen Rechenzeit, wird man verstehen, warum Simulation an dieser Stelle leider nicht sinnvoll weiterhelfen kann.
Diese Überlegungen werden aktuell am utg unter der Leitung von Prof. Dr. Wolfram Volk in verschiedenen Forschungsarbeiten berücksichtigt und untersucht. Es wurde bereits ein System entwickelt, mit dessen Hilfe der Werker einen optischen Soll/Ist-Abgleich zwischen dem Werkstück und der Zielgeometrie erhält. Durch die gezielte automatische Ausführung von Einzelschlägen in Abhängigkeit der Werkstückposition können wiederholgenau einfache Blechbauteile erzeugt werden.
Dieses Verfahren wurde durch eine kognitive Regelung der Schlagintensität sowie eine automatische Bauteilführung ergänzt.Weitere Schwerpunkte liegen in der Entwicklung der Grundlagen einer geschlossenen virtuellen Kette für die Fertigung von Blechbauteilen durch rechnergesteuertes Treiben. Aktuell wurde die Implementierung künstlicher neuronaler Netze abgeschlossen, um eine vollautomatisierte Fertigung einfacher Bauteile zu ermöglichen. Künftig soll dieses Konzept auf die Fertigung komplexer 3D-Geometrien erweitert werden. Andere Vorhaben zielen auf einen pragmatischeren Lösungsansatz und eine zeitnahe, industriell umsetzbare Lösung.
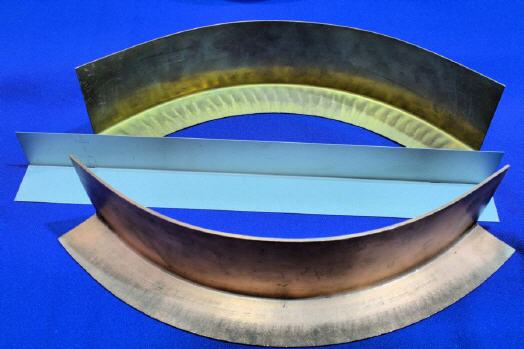
Lernen per Datenbank
Das am Institut entwickelte ›Kopiertreiben‹ ermöglicht die Realisierung von 3D-Umformungen. Ein Trackingsystem zeichnet dazu Bahnkurven aus Abschnitten der manuellen Fertigung sowie die zugehörigen Maschinenparameter auf. Im Anschluss bildet das Fertigungssystem bestehend aus Kraftformer und Roboter diese automatisiert und reproduzierbar nach. Darauf aufbauend wurde die Idee des ›automatisierten Kopiertreibens‹ verwirklicht.
Unter Verwendung einer Bauteil-Datenbank ist es anschließend möglich, automatisiert neue Bauteilgeometrien aus den Elementen des Katalogs zusammenzusetzen und somit segmentweise herzustellen. Dazu wurden Algorithmen entworfen, die an neuen Bauteilen Abschnitte mit Ähnlichkeiten zu bereits produzierten Geometrien identifizieren. Methoden und Konzepte der automatisierten Variation der Katalogelemente ermöglichen ein breites Bauteilspektrum mit wenigen, bekannten Geometrien abzudecken.
Auf diese Weise wird der vorhandene Erfahrungsschatz genutzt und zugleich der weitere Ausbau möglich, um im Laufe der Zeit sukzessive das Bauteilspektrum zu erweitern. Wie gut das bereits funktioniert, kann man in Garching bei München in Erfahrung bringen.
Universelle, kostengünstige Treibmaschinen und -werkzeuge in Verbindung mit Robotern zur Bauteilführung benötigen weniger Kapitaleinsatz in der Anschaffung und geringeren Energieeinsatz im Betrieb bei gleichzeitiger Erweiterung der Produktpalette. Automatisierte Verfahren verbessern zudem die Reproduzierbarkeit und steigern die Bauteilqualität sowie die Prozesssicherheit.
Nicht unerheblich ist auch der Beitrag zum Abfedern des Fachkräftemangels. Spezialisten mit der Erfahrung, aus einer Blechtafel ein Bauteil zu hämmern, sind bereits rar. Ein Einsatz solcher Verfahren wird dem Fachkräftemangel entgegenwirken und in der Einzel- und Kleinserienfertigung eine gewaltige Umwälzung einleiten.
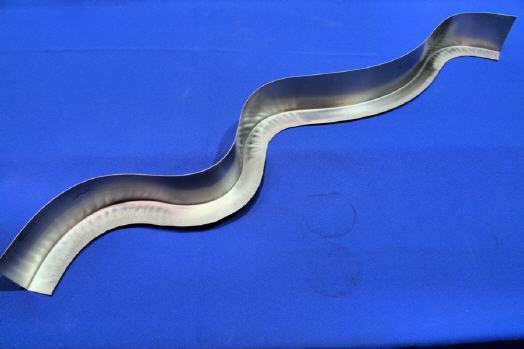
Mehr Informationen zur TU München Umformt.:
![]() |
Technische Universität München |
![]() |
Lehrstuhl für Umformtechnik und Gießereiwesen |
![]() |
Walther-Meißner-Straße 4 |
![]() |
85748 Garching |
![]() |
Tel.: +49 (0)89 / 2 89 - 1 37 91 |
![]() |
Fax: +49 (0)89 / 2 89 - 1 37 38 |
![]() |
E-Mail: info@utg.de |
![]() |
www.utg.de |
Zugriffe heute: 3 - gesamt: 7974.