Die Planung ist entscheidend
Expertengespräch rund um Graphitbearbeitung
In vielen Bereichen hat Graphit Kupfer als Werkstoff zur Elektrodenfertigung im Werkzeug- und Formenbau ersetzt. Doch wer Graphitelektroden erfolgreich und wirtschaftlich einsetzen will, muss die gesamte Prozesskette betrachten – angefangen von der Konstruktion und der Planung, über den passenden Maschinenpark und ausgefeilte Werkzeuge mit leistungsstarken Beschichtungen bis hin zur Messtechnik für die Qualitätskontrolle und die Ausbildung der Mitarbeiter. Darin sind sich die Experten der Zecha Hartmetall-Werkzeugfabrikation GmbH, der CemeCon AG, der GF Machining Solutions GmbH sowie der CIMTRODE GmbH einig.
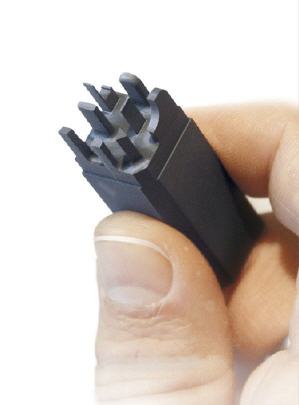
„Weniger Abbrand, thermisch stabil, höhere Abtragsraten nahezu ohne Verschleiß – es ist kaum verwunderlich, dass heute Graphit an so vielen Stellen der Vorzug gegenüber Kupfer zur Elektrodenfertigung gegeben wird. Der Werkstoff bietet vielfältige Vorteile, die sich direkt positiv auf die Wirtschaftlichkeit auswirken“, so Arndt Fielen, Vertriebsleiter bei der Zecha Hartmetall-Werkzeugfabrikation GmbH, Spezialist für hochpräzise Werkzeuge in kleinsten Dimensionen.
„Einer der wohl bedeutendsten Vorteile ist, dass man mit Graphit eine erodierfertige Elektrode aus der Fräsmaschine erhält. So ist Erodieren ohne jegliche manuelle Nacharbeit möglich“, konkretisiert Daniel Gruber, Inhaber der CIMTRODE GmbH, Experte rund um Graphitbearbeitung zum Beispiel bei hochwertiger Messtechnik für den Werkzeug- und Formenbau. Das hat für viele Anwender ein enormes Einsparungspotential und erhöht zudem im Regelfall auch die Maßhaltigkeit und am Ende die Qualität der herzustellenden Produkte.
Ein weiterer großer Vorteil von Graphit sind die Möglichkeiten bei der Elektrodengestaltung. Mussten Werkzeug und Formenbauer früher hunderte einzelne Kupferelektroden fertigen, so können sie heute dank Graphit die Elektrodenanzahl radikal reduzieren. Denn durch die etablierte HSC-Frästechnologie ist die Zerspanung von Graphit unendlich variabel und ermöglicht die Herstellung von Elektrodengeometrien, die mit Kupfer nicht möglich wären. „Es gibt Beispiele, wo die Elektrodengeometrien von über 100 Kupferelektroden auf vier Geometrien in Graphit zusammengefasst wurden“, teilt Benjamin Sendler, Leiter Anwendungstechnik bei GF Machining Solutions GmbH, Hersteller von hochwertigen Maschinen zur Fräsbearbeitung und Funkenerosion, seine Erfahrungen.
Abstimmung für beste Ergebnisse
Um die Vorteile auch in vollem Umfang zu nutzen, ist die richtige Planung und die Abstimmung der Parameter das A und O. Arndt Fielen: „Bei der Zerspanung von Graphit etwa sind deutlich höhere Abtragsraten und filigranere Formen möglich. Dafür muss aber auch die Qualität der Werkzeuge stimmen. Ausgefeilte Geometrien, wie etwa bei der SEAGULL-Serie sind dabei nur ein wichtiger Faktor für hohe Präzision.“ Durch die außergewöhnlich kurze Schneidengeometrie gepaart mit engsten Fräser-Toleranzen, lassen sich mit SEAGULL-Fräsern feinste Rippen und filigranste Elektrodengeometrien problemlos herstellen.
Diamantbeschichtungen sind dabei ein entscheidender Faktor: Denn das Zerspanen von Graphit ist wegen der hohen Abrasivität des Werkstoffs ohne einen wirksamen Verschleißschutz wirtschaftlich kaum möglich. Damit die hohe Präzision der Werkzeuge aber auch nach der Beschichtung gewährleistet bleibt, darf sie auf keinen Fall die Mikrogeometrie beeinflussen. „Unsere Multilayer-Diamantbeschichtungen werden im Endmaß auf die Werkzeuge abgeschieden und behalten die Mikrogeometrie bei – und das jederzeit reproduzierbar. So entsteht eine unschlagbare Kombination aus perfekt geschliffenem Werkzeug und hochwertiger, extrem glatter Beschichtung, die für eine ausgezeichnete Oberflächenqualität der gefrästen Elektrode sorgt“, so Thomas Schaaff, Area Sales Manager bei der CemeCon AG, Experte für innovative Beschichtungslösungen für Zerspanwerkzeuge.
Qualität garantieren
Doch auch das beste Werkzeug kann keine Höchstleistungen bringen, wenn die Zerspanparameter sowie die Qualität der Bearbeitungsmaschinen nicht passen. Stimmen etwa die Einstellungen und die Programmierung nicht, arbeitet das System bestenfalls nicht wirtschaftlich, weil der Werkzeugverschleiß zu hoch oder die Abtragsraten zu niedrig liegen, aber auch Werkzeugbruch und Zerstörung der Elektrode sind denkbar. Benjamin Sendler: „Mit Lösungen sowohl für die Fräsbearbeitung als auch Funkenerosion sehen wir uns als Partner der Werkzeug- und Formenbauer und wissen, wie entscheidend die Abstimmung aller Faktoren aufeinander ist. Dafür müssen alle Beteiligten, also Maschinenhersteller, Fräserhersteller, Steuerungshersteller, Messinstrumentenhersteller und nicht zuletzt die Anwender gut zusammenarbeiten – von der Planung bis zur Ausführung. Dann können erstaunliche Ergebnisse erreicht werden.“
Gerade bei filigranen Elektroden mit Toleranzen im µm-Bereich müssen alle Einflussfaktoren perfekt aufeinander abgestimmt sein. Nur eine hervorragende Qualitätskontrolle kann Fehler schon frühzeitig aufzeigen und gegebenenfalls zur Anpassung der Parameter führen. CIMTRODE hat ein Mess- und Prüfsystem speziell für den Formen- und Werkzeugbau entwickelt: C-View ermöglicht zum Beispiel die Kontrolle und Beurteilung von Verschleiß an Fräs- oder Bohrwerkzeugen. Zudem lässt es eine exakte Beurteilung von Elektrodenoberflächen zu, bevor man damit erodiert. „Das bietet enorme Vorteile für den Anwender und es lassen sich signifikante Verbesserungen hinsichtlich Qualität und Prozesssicherheit erzielen“, so Daniel Gruber.
Um die hohe Qualität und Präzision, die beim Werkzeug- und Formenbau gefordert wird, möglichst wirtschaftlich umsetzen zu können, gehen immer mehr Firmen den Weg der Standardisierung und Automatisierung. Dadurch lassen sich Vorteile, die heute meist der Serienfertigung vorbehalten sind, auch bei der Einzelteilherstellung nutzen. Dazu Thomas Schaaff: „Prozesssicherheit ist gerade auch bei steigender Automatisierung enorm wichtig. Unsere Diamantbeschichtungen leisten dazu einen entscheidenden Beitrag. Durch die gleichbleibende Qualität und die herausragenden Eigenschaften der Mulitlayer erreichen die Werkzeuge hohe Standzeiten und können damit lange und problemlos eingesetzt werden.“ Das trägt zu einer hohen Prozesssicherheit und -stabilität bei, um so etwa die mannlose Fertigung übers Wochenende zu ermöglichen.
Neue Wege
Daneben sollen auch beispielsweise neue Bearbeitungsvarianten höhere Produktivität und Genauigkeit noch besser vereinen. „Eine Innovation der letzen Jahre ist, Graphit nass zu fräsen. Daraus ergeben sich viele neue Möglichkeiten. Es eröffnet mehr Flexibilität, Stahl, Kupfer und Graphit auf einer Maschine zu bearbeiten und dabei die Werkzeugkosten signifikant zu reduzieren. Es könnte die Lösung für all jene sein, die bislang die Vorteile aus dem Werkstoff Graphit noch nicht nutzen – etwa weil sich die Investition in eine dafür erforderliche Erodiermaschine und einer zusätzlichen neuen Fräsmaschine für die Trockenbearbeitung nicht rechnet“, zeigt Arndt Fielen einen neuen Weg für die Graphitbearbeitung.
Auch beim Senkerodieren bleibt die Entwicklung nicht stehen: „Moderne Generatortechnologien bringen etwa schon heute Zeitersparnisse von bis zu 40 Prozent bei gleicher Qualität sowie kleinere Untermaße an der Elektrode. Auch neue Erodier-Strategien sind vielversprechend: Dadurch entstehen spezielle Oberflächentexturen, die den Verschleiß von Spritz- und Druckgusswerkzeugen und die Entformungskräfte deutlich reduzieren“ ergänzt Benjamin Sendler.
Mehr Informationen zur ZECHA GmbH:
![]() |
ZECHA Hartmetall- Werkzeugfabrikation GmbH |
![]() |
Benzstraße 2 |
![]() |
75203 Königsbach-Stein |
![]() |
Tel.: +49 (0) 72 32 / 30 22-0 |
![]() |
Fax: +49 (0) 72 32 / 30 22-25 |
![]() |
E-Mail: info@zecha.de |
![]() |
www.zecha.de |
War dieser Artikel für Sie hilfreich?
![]() |
![]() |
![]() |
![]() |
![]() |
Bitte bewerten Sie diese Seite durch Klick auf die Symbole.
Zugriffe heute: 3 - gesamt: 1545.