Individuelle Maßanfertigung von Induktoren
Für die perfekte induktive Erwärmung
Die induktive Erwärmung ist ein Wachstumsfeld – nicht ohne Grund: Das Verfahren ist einerseits energieeffizient, prozesssicher, reproduzierbar und sehr schnell. Andererseits sind seine Einsatzmöglichkeiten fast unbegrenzt. Mithilfe der Induktion lassen sich Bauteile zum Beispiel vorwärmen und fügen, löten, härten oder sogar aufschmelzen. Eine entscheidende Komponente bei diesen Prozessen ist der Induktor. Sein Design bestimmt entscheidend mit darüber, wie präzise ein Bauteil erwärmt wird. Deshalb wird das zentrale Werkzeug im Rahmen von aufwändigen Manufaktur-Prozessen auf Zehntel-Millimeter genau gefertigt – eine Aufgabe für die Experten von eldec mit Sitz in Dornstetten bei Freudenstadt. Die Mitarbeiter der EMAG Tochter kennen die unterschiedlichen Anwendungen des induktiven Erwärmens genau. Seit mehr als 30 Jahren entwickeln sie die dazugehörigen Induktoren – angepasst mit höchster Maßhaltigkeit an die Geometrie des Werkstücks.
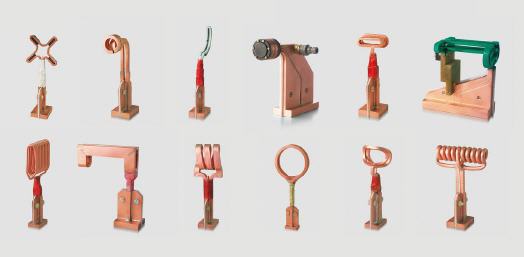
Die entscheidende Qualität des induktiven Erwärmens lässt sich unter dem Schlagwort „Präzision“ am besten zusammenfassen. Die Technologie kommt überall dort zum Einsatz, wo innerhalb kürzester Zeit viel Energie beziehungsweise Wärme in ein Werkstück eingebracht werden muss. Die Temperaturgenauigkeit spielt hierbei eine große Rolle und ist oft auch prozessrelevant – und nur im Zusammenspiel von Induktor-Geometrie, Frequenz, Leistung und Feldcharakterisierung ist eine präzise Erwärmung möglich. Zudem sorgt die induktive Energieeinbringung für schnelle Produktionsprozesse, einen minimalen Werkstückverzug und einen sparsamen Energieverbrauch.
Dabei kommt es neben dem eingesetzten Generator (als Stromquelle) vor allem auf den Induktor an, denn die Form dieses Werkzeugs bestimmt entscheidend darüber, welche Bereiche des Werkstücks erwärmt werden. Folglich kann es nicht überraschen, dass die verwendeten Induktoren so unterschiedlich sind wie die dazugehörigen Bauteile oder Komponenten. eldec produziert zum Beispiel Ring- oder Forminduktoren, die das zu erwärmende Bauteil millimetergenau umschließen. Stabinduktoren befinden sich während des Prozesses innerhalb des Bauteils und erwärmen das Metall somit von innen heraus. Häufig zum Einsatz – etwa beim induktiven Löten – kommen auch Flächeninduktoren. Sie erwärmen größere Flächen eines Bauteils gleichzeitig und gleichmäßig.
Erfahrungswissen ist entscheidend
„Insgesamt produzieren wir bis zu 1.000 Induktoren pro Jahr – Tendenz steigend“, stellt Stefan Tzschupke, Head of Business Development Generators bei eldec, heraus. „Die entscheidende Qualität, auf die viele Kunden vertrauen, ist das Erfahrungswissen unserer Monteure und Ingenieure. Schließlich ist der Induktorenbau ein anspruchsvoller Manufakturprozess, der nicht automatisiert ablaufen kann, denn es kommt auf viele hochgenaue Details an. Jeder Handgriff beim Löten oder Montieren des Induktors muss sitzen.“
Die Kunden von eldec profitieren letztlich vom ersten Moment an: Sie legen zum Beispiel eine Bauteilzeichnung oder einen Rohling des Bauteils vor. Anwendungstechniker von eldec schlagen anschließend einen Produktionsablauf vor: Wie vollzieht sich der induktive Prozess im Detail? Was für Temperaturen müssen erreicht werden und wie groß ist die Leistungsstärke des Generators? Und welche Form und Größe hat der Induktor? „Wenn diese Fragen geklärt sind, starten wir mit der Konstruktion des Induktors mithilfe moderner 3D-CAD-Software und CNC-Werkzeugmaschinen“, erklärt Tzschupke. „Das Endergebnis testen wir am echten Bauteil. Wenn uns die gefertigte Bauteilqualtät nicht zu 100 Prozent überzeugt, werden Änderungen vorgenommen und der Induktor – zum Beispiel auf der Fräsmaschine – nachbearbeitet. Bei hochkomplexen Induktoren, wie sie etwa beim induktiven Härten zum Einsatz kommen, geht es hier mitunter um wenige Zehntelmillimeter.“
Aktuell erproben die Spezialisten zudem eine neue Simulations-Software, mit der sie die Wirkungsweise eines virtuellen Induktor-Modells am Computer überprüfen. In Kürze startet der praktische Einsatz dieser Anwendung. „Wir gehen damit den nächsten Schritt“, erklärt Tzschupke. „Die Anwender profitieren letztlich von noch schnelleren Prozessen in der Entwicklung und noch präziseren Induktionsprozessen.“ Eine weitere Neuheit bei eldec ist die Herstellung der Windungen mithilfe des Sinterns. Hierdurch lassen sich besonders komplexe Induktor-Geometrien realisieren.
Wachstumsfeld im Unternehmen
Nicht zuletzt bietet eldec ein Höchstmaß an Flexibilität bei der Induktor-Konstruktion und -Produktion. So können Kunden, die eine bestimmte Anzahl von Werkzeugen pro Jahr benötigen, einen Rahmenvertrag mit dem Schwarzwälder Unternehmen abschließen. Den neuen Induktor stellt eldec dann „just in time“ bereit. Möglich ist natürlich auch, dass Anwender weitere Induktoren selber produzieren. Insgesamt stellt der Induktorenbau für eldec aber ein überaus wichtiges Wachstumsfeld dar.
Die Gründe dafür liegen auf der Hand: Zum einen entdecken immer mehr Unternehmen in Branchen wie dem Automobilbau oder der Luft- und Raumfahrt die großen Möglichkeiten des induktiven Erwärmens. Dabei werden immer komplexere Bauteile erwärmt, gehärtet oder zum Glühen gebracht. Zum anderen verlangt genau diese Entwicklung nach einem besonderen Know-how beim Induktorenbau. „Auf diese Entwicklung ist eldec in idealer Weise vorbereitet“, betont Tzschupke abschließend. „Wir bringen unser Erfahrungswissen umfassend ein und garantieren am Ende hocheffiziente beziehungsweise sichere Produktionsprozesse.“
Mehr Informationen zur EMAG eldec Induction GmbH:
![]() |
EMAG eldec Induction GmbH |
![]() |
Otto-Hahn-Strasse 14 |
![]() |
72280 Dornstetten |
![]() |
Tel.: +49-7443-9649-0 |
![]() |
Fax : +49-7443-9649-6931 |
![]() |
E-Mail: info@eldec.de |
![]() |
www.eldec.net |
War dieser Artikel für Sie hilfreich?
![]() |
![]() |
![]() |
![]() |
![]() |
Bitte bewerten Sie diese Seite durch Klick auf die Symbole.
Zugriffe heute: 3 - gesamt: 5321.