Smarte Prozessgestaltung beim Kegelradfräsen
Intelligente Nutzung von Antriebsinformationen
Hochproduktive Fräsprozesse bei extrem hoher und reproduzierbarer Verzahnungsqualität – das ist das Ergebnis des optimalen Zusammenspiels von innovativen Verzahn-Werkzeugen und leistungsfähigen Klingelnberg Kegelrad-Fräsmaschinen. Verknüpft werden beide Elemente durch den Verzahnprozess.
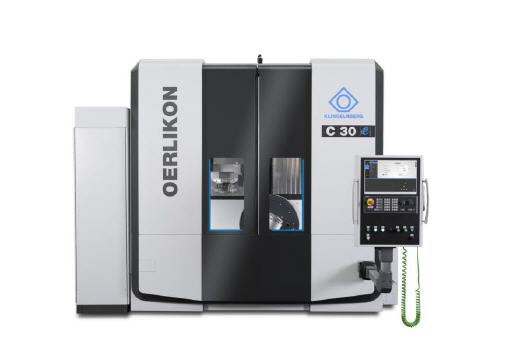
Wachsender Wettbewerb und der damit verbundene Druck, vor allem in der Automobilindustrie, verlangen eine immer kostengünstigere Produktion bei steigenden Qualitätsanforderungen. Hiervon ist die spanende Fertigung von Kegelrad-Verzahnungen ebenfalls in großem Maße einbezogen. Gerade deshalb ist es wichtig, das volle Potenzial aller am Prozess beteiligten Komponenten auszuschöpfen,um die Maschinenleistung und die eingesetzten Werkzeuge bestmöglich auszunutzen und so die Zykluszeit zu reduzieren.
Das Fräsen von Kegelrädern ist durch ständig variierende Schnittverhältnisse gekennzeichnet, deshalb ist eine „einfache“ Regelung des Vorschubs allein nach der Spindelauslastung und ohne hinreichende Analyse und Kenntnis der Prozessabläufe auf keinen Fall optimal. Durch die fortlaufende Entwicklung der Klingelnberg Maschinen-Bediensoftware wird jetzt dem Anwender ein Einblick in den Prozessablauf ermöglicht. Dieser Einblick über das Softwaremodul Klingelnberg Smart Process Control befähigt den Technologen, in einem ersten Schritt, die Maschinenbelastung aufzuzeichnen und den jeweiligen Prozesssequenzen exakt zuzuordnen. In einem zweiten Schritt kann die Maschinenreaktion auf Prozessänderungen präzise analysiert und nachverfolgt werden. Eine neue Basis zur Optimierung hochproduktiver Verzahnprozesse ist hiermit geschaffen.
Klingelnberg Smart Process Control unterstützt das Zusammenspiel von innovativen Fräs-Werkzeugen und der leistungsfähigen Klingelnberg Kegelrad-Fräsmaschine C 30. Hochproduktive Fräsprozesse bei extrem guter und reproduzierbarer Verzahnungsqualität sind das Ergebnis.
Kriterien für einen optimalen Verzahnprozess:
- Die Bauteil-Qualität entspricht exakt den Anforderungen.
- Die Bearbeitungszeit ist möglichst kurz.
- Das eingesetzte Verzahn-Werkzeug kann möglichst lang im Einsatz bleiben.
- Ein Optimum aus Maschinenkosten und Werkzeugkosten ist gefunden.
Auf den ersten Blick ist das eine sehr einfache „Checkliste“. Allerdings ergeben sich bei der Optimierung des Kegelrad-Fräsprozesses Konflikte zwischen Zielsetzung und technischer Umsetzung. Wer den Prozess verbessern will, für den stehen zwei Ziele klar im Fokus: eine gesteigerte Produktivität sowie eine verbesserte Prozesssicherheit, um die hohen Anforderungen an die geometrische Bauteil-Genauigkeit (Teilung und Topografie) reproduzierbar und sicher zu erfüllen – und das ohne Einbußen in der Oberflächenbeschaffenheit der Zahnflanke, welche als Messoberfläche dient.
Eine Steigerung der Produktivität erfordert jedoch eine Erhöhung der Bearbeitungsparameter, und genau darin besteht der Konflikt. Denn gesteigerte Bearbeitungsparameter führen tendenziell zu einem schlechteren Verschleißverhalten der Werkzeuge. Hierdurch erhöht sich die Gefahr einer Schädigung der Flankenoberfläche durch Oberflächendefekte wie Kratzer oder sogar Aufschweißungen. Diese sind zwingend zu vermeiden.
Die Möglichkeiten einen Kegelrad-Fräsprozess zu optimieren, sind durch verschiedene Elemente eingeschränkt. Welche davon als erste eine Grenze setzen, hängt immer vom Bauteil-Typ und den damit verbundenen unterschiedlichen Prozessmerkmalen ab: Bei formverzahnten Bauteilen – das sind exklusiv Tellerräder – ist es das Werkzeug hinsichtlich seines Verschleißes. Bei gewälzten Bauteilen – das sind immer Ritzel und oft auch Tellerräder – legt häufig die Entstehung von Oberflächendefekten die Grenze fest. Die Kegelrad-Fräsmaschine spielt hingegen in den meisten Fällen eine untergeordnete Rolle.
Unterstützung für den Technologen
Die Steuerungen von modernen CNC-Maschinen ermöglichen eine präzise Aufzeichnung von Signalen. So ist es möglich, zu allen Zeitpunkten eines Prozesses unterschiedliche Informationen zu erfassen und abzuspeichern. Die Aufgabe des Technologen ist es, festzulegen, über welche maßgeblichen Kriterien ein Prozess als optimal zu definieren ist. Während beispielsweise das Kriterium „Bearbeitungszeit“ am Ende des Prozesses leicht abzulesen ist, lässt sich das Kriterium „Schädigung der Flankenoberfläche durch Oberflächendefekte“ schon schwerer ab- und einschätzen. Denn der Verschleiß des Werkzeugs ändert sich mit dessen Einsatzdauer, zusätzlich spielen hier Chargeneinflüsse des Materials eine Rolle. Am schwierigsten zu bewerten ist die Werkzeug-Belastung und der sich daraus ergebende Schneidenverschleiß.
Entgegen vieler anderer Zerspanprozesse verändert sich beim Kegelrad-Fräsprozess ständig die Eingriffssituation der Werkzeug- Schneiden während des Prozessablaufs. Die Belastung der Verzahnmaschine variiert ebenfalls entsprechend. Das Besondere ist, dass sich der entstehende Werkzeug-Verschleiß aufgrund der lokalen Belastungen entlang der gesamten Schneide unterschiedlich ausbildet. Möchte der Technologe die Informationen der Maschinensteuerung als Basis für die Bewertung der lokalen Werkzeugbelastung heranziehen, müssen die am Schneidprozess beteiligten Schneidkanten-Länge berücksichtigt werden.
Klingelnberg Smart Process Control
Die Aufzeichnung der Auslastung der Werkzeug-Spindel hilft sowohl bei der Optimierung als auch bei der Überwachung von Prozessabläufen. In der Kegelrad-Zerspanung werden die Prozesse durch Stützpunkte aus Arbeitsposition und Vorschub definiert. Eine Variation dieser Parameter bewirkt eine Änderung der Auslastung der Werkzeug-Spindel. Die für den Anwender direkt an der Maschine nutzbare Klingelnberg Smart Process Control Software ermöglicht für jede Bearbeitungssituation eine präzise Visualisierung der Maschinenbelastung. So ist der Prozessablauf auf einen Blick zu erfassen und gut zu verstehen. Nach einer kurzen Schulung durch einen erfahrenen Klingelnberg Technologen ist der Maschinenanwender in der Lage, seine Prozesse eigenständig mit Klingelnberg Smart Process Control zu analysieren und anschließend zu optimieren.
Das automatische Mitschreiben der Spindelauslastung – für eine sinnvolle Werkstück-Anzahl – ermöglicht eine kontinuierliche Prozessüberwachung über einen frei definierbaren Zeitraum. Die über diesen Zeitraum erfassten Daten lassen sich bequem mit den gängigen MS-Office-Programmen auswerten. Der Einfluss von Änderungen am Prozess kann über diese Langzeitbetrachtung gut aufgezeigt werden.
Die Langzeitüberwachung dient ebenfalls zur Erkennung von Materialunregelmäßigkeiten oder veränderten Verschleißcharakteristiken des Werkzeugs.
Einsatz in der Praxis:
Die Herstellung von Kegelrad-Verzahnungen erfolgt meist durch einen mehrstufigen Prozess. Bei den meisten Bauteilen wird die Flankenform durch eine wälzende Bewegung der Verzahnmaschine erzeugt. Das Schlichtwälzen bildet hierbei – nach dem anfänglichen Tauchprozess und dem darauffolgenden Schruppwälzen – den abschließenden Arbeitsschritt beim Verzahnen einer Kegelrad-Verzahnung. Abbildung 1 zeigt die aufgezeichnete Auslastungskurve (blau) der Werkzeug-Spindel eines solchen Schlichtwälz-Prozesses. Da es sich bei dem Beispiel um einen Radsatz handelt, der im Anschluss an die Wärmebehandlung durch Läppen seine endgültige Qualität erhält, steht die Bauteil-Genauigkeit bei der Bearbeitung besonders im Fokus. Der zu optimierende Prozess – siehe Abbildung 1 – startet mit einem Tauchvorgang (I) bei einer Arbeitsposition Lambda von ca. 312°.
Hat das Werkzeug seine Arbeitstiefe erreicht, wälzt es einen ersten Bereich der Zahnflanke vor (Schruppwälzen, II von Lambda 312° bis 321°). Im Anschluss daran erfolgt nach einer kurzen Tiefenzustellung (III) das Schlichtwälzen der Verzahnung mit der aufgezeigten Werkzeugauslastung (WA [%]). Das Werkzeug startet das Schlichtwälzen (IV) bei einem Wälzwinkel Lambda von 321° und endet bei einem Wälzwinkel Lambda von ca. 301°. Hierbei durchwälzt es den schruppgewälzten Bereich. Deutlich sichtbar ist der Lastanstieg bzw. Laststoß um den Wälzwinkel von 312°, der aus dem Übergang des schruppgewälzten Bereichs in den nicht gewälzten Bereich resultiert.
Eine Messung des betrachteten Bauteils zeigte Auffälligkeiten in der Flankentopografie, die genau im Bereich des Lastanstiegs, also bei 312°, lagen. Der Klingelnberg Technologe kann hieraus erkennen, dass eine Prozessmodifikation anzustreben ist. Als Modifikation hin zu einem optimierten Gesamt- und Schlichtwälzprozess analog Abbildung 3 wurde die Arbeitsposition des Tauchvorgangs von Lambda 312° auf Lambda 308° verlagert, um den schruppgewälzten Bereich zu vergrößern. Außerdem fand an den Stützpunkten P1 bis P4 eine Anpassung durch Eingabe geeigneter Spanstärken (SW [mm]) statt. Resultat ist eine deutlich gleichmäßigere Spindelauslastung beim Schlichtwälzen ohne lokalen Lastanstieg im Bereich der Tauchposition Lambda 308° und eine unauffällige Flankentopografie.
Auf dieser Basis besteht jetzt die Möglichkeit, das gleichmäßige Lastniveau über eine Verlagerung der Stützpunkte P1 bis P4 parallel anzuheben, um so eine Verkürzung der Bearbeitungszeit zu erzielen. Die Nutzung von Klingelnberg Smart Process Control ermöglicht für den Tauch- und Schruppwälz-Bereich ebenfalls eine kontrollierte Anhebung der Vorschübe. In Summe konnte, wie Abbildung 2 veranschaulicht, eine Verkürzung der Hauptzeit dieses Beispielprozesses um sieben Prozent erreicht werden.
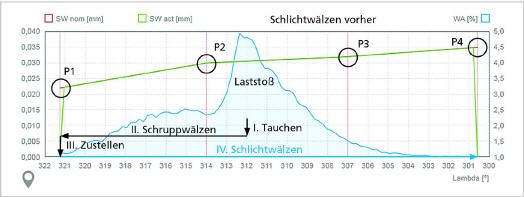
Bild1: Auslastungskurve vor Optimierung

Bild 2: Bearbeitungszeit
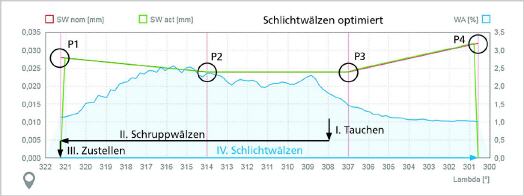
Bild 3: Auslastungskurve nach Optimierung
Mehr Informationen zur Klingelnberg GmbH:
![]() |
KLINGELNBERG GmbH |
![]() |
Peterstraße 45 |
![]() |
42499 Hückeswagen |
![]() |
Tel.: +49-2192-81 0 |
![]() |
Fax: +49-2192-81 200 |
![]() |
E-Mail: info@klingelnberg.com |
![]() |
www.klingelnberg.com |
War dieser Artikel für Sie hilfreich?
![]() |
![]() |
![]() |
![]() |
![]() |
Bitte bewerten Sie diese Seite durch Klick auf die Symbole.
Zugriffe heute: 3 - gesamt: 5587.