Bionik und Leichtbau bei Airbus
Flugzeugteile aus dem 3D-Drucker
Laserschmelzen mit Metallen gewinnt im Flugzeugbau an Bedeutung: Schnellere Durchlaufzeiten, günstigere Bauteile und eine bislang unbekannte Freiheit in der Formgebung sind auch hier klassische Argumente. Neue Aspekte sind aber auch Leichtbau, Bionik und verändertes, konstruktives Denken. Drei Experten erläutern, was noch zu erwarten ist.
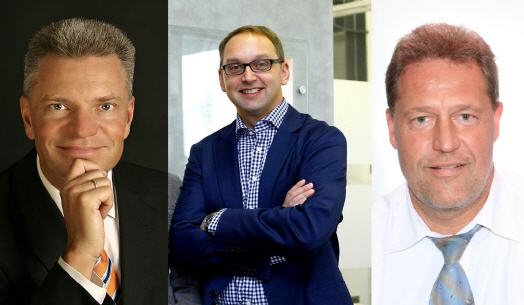
Bislang haben wir von ›Composite-Flugzeugen‹ gehört und nun kommen generative Fertigungstechniken, wie Laserschmelzen von Metallen oder Kunststoffsintern, im Flugzeugbau auf. Wie verändert dies die Konstruktion von Flugzeugstrukturelementen?
Peter Sander: In erster Linie suchen wir nach Gewichtsreduzierung. Dieser Ansatz hilft, Flugzeuge ökonomischer zu betreiben. Das additive Layer Manufacturing, kurz 3D-Drucken, erlaubt uns, völlig neue Strukturen zu konstruieren. Diese sind um mehr als 30 Prozent leichter als konventionelle Konstruktionen. Dazu kommt, dass wir direkt aus der 3D-Konstruktion auf den Drucker, also die Laserschmelzanlage, gehen können. Normalerweise braucht man zur Herstellung von Flugzeugteilen Werkzeuge. Diese entfallen jetzt. Das beschleunigt die Zeit bis zur Bauteilverfügbarkeit um bis zu 75 Prozent.
Claus Emmelmann: Die Vorteile sind augenfällig. Die hohe geometrische Gestaltungsfreiheit ermöglicht gegenüber konventionellen Herangehensweisen effektivere Leichtbaulösungen. Dies bedeutet für die gegenwärtig im Fokus stehenden Haltelemente, auch ›Brackets‹ genannt, eine deutliche Gewichtsreduktion, die sich in niedrigeren Treibstoffverbräuchen oder einem Potenzial für erhöhte Flugzeugzuladungskapazitäten widerspiegeln.
Wie verändert das additive Verfahren die Projektabläufe?
Claus Emmelmann: Eine berechtigte Frage. Denn nicht nur das Bauteilgewicht ändert sich. Auch die Projektabläufe können von den Eigenheiten einer laseradditiven Fertigung profitieren. Es ist nun möglich, bereits früh Funktionsmuster mit seriennahem Bauteilcharakter herzustellen, ohne hohe Kosten für Werkzeuge oder andere Vorlaufkosten berücksichtigen zu müssen.
Welche Effekte ergeben sich, wenn man von einem gefrästen oder gegossenen Teil auf ein gedrucktes Bauteil umsteigt?
Peter Sander: Beim Fräsen von Flugzeugteilen entsteht bis zu 95 Prozent recyclingfähiger Abfall. Beim Laserschmelzen erhalten wir ein „endkonturnahes Bauteil“, dessen Abfall bei etwa fünf Prozent liegt. Das macht das Verfahren überaus interessant. Gegenüber dem Gießen haben wir den zusätzlichen Vorteil, dass wir kein Gusswerkzeug benötigen.
Frank Herzog: Neben der Ressourcenschonung ist die Designfreiheit sehr attraktiv. Die Bauteildichte wirtschaftlich unter Kontrolle zu halten und die Mikrostrukturqualität zu bestimmen sind weitere Aspekte. Die Anlagentechnik kann durch unsere QM-Module dem Anwender eine In-line-Qualitätskontrolle in Echtzeit bieten. Das Prozess-Mapping ist ein entscheidendes Instrument, um Qualität sicherzustellen. Damit wird Reverse-Engineering möglich.
Claus Emmelmann: In der Regel ergeben sich positive Effekte für die Herstellkosten bei kleinen bis mittleren Stückzahlen. Darüber hinaus bietet die laseradditive Fertigung eine höhere Gestaltungsfreiheit. Es können bislang unbekannte Geometrien mit Funktionalitäten verknüpft werden. Laseradditiv gefertigte Werkstoffe weisen eine höhere Festigkeit bei gleichzeitig geringerer Duktilität auf, die aber durch die richtige Wärmebehandlung auch wieder gesteigert werden kann.
Welche Potenziale bieten 3D-Drucktechniken für den Flugzeugbau und die Flugzeugstrukturelemente?
Peter Sander: Hier sind zwei Bereiche zu betrachten: Einerseits die Prozessoptimierung und anderseits die Produktauslegung. Prozessoptimierung bedeutet für uns – wir brauchen keine Werkzeuge mehr. Wir können direkt aus dem 3D-Konstruktionssystem Bauteile drucken. Dies spart uns bis zu 75 Prozent Durchlaufzeit. Losgrößenbetrachtungen sind im Flugzeugbau essenzieller als bei Volumenfertigungen. So besitzen Testflugzeuge einige Tonnen Test-Equipment. Das erfordert Tausende von Flight Test Installations-Brackets mit Kleinststückzahlen. Ein weiteres Thema sind Ersatzteile. Diese können wir zukünftig „on demand“ herstellen. Nun noch der zweite Punkt, die Bauteil- oder Produktauslegung. Da wir durch das Laserschmelzen feinste poröse Strukturen herstellen können, werden künftige Flugzeugteile „bionisch“ aussehen. Naturlösungen werden bei uns derzeit hinsichtlich ihrer Anwendbarkeit analysiert. Dies dürfte eine Art Paradigmenwechsel in Konstruktion und Fertigung auslösen.
Frank Herzog: Das Verfahren erlaubt eine signifikante Steigerung der Produktivität und zahlreiche Optionen zur Automatisierung. Auch die Bauteilgröße wurde durch die Qualifikation der 1 000 Watt-Lasertechnik deutlich gesteigert. Multipler Lasereinsatz wird zukünftig eine Rolle spielen. Mittels intelligenten Belichtungsstrategien kann der Laser ein Bauteil gezielt beaufschlagen, sodass es in Struktur, Festigkeit und Oberflächengüte maßgeschneidert werden kann.
Zu den Stichworten ›Leichtbau‹ und ›Bionik‹: Die Gewichtsreduzierung scheint ein klarer Vorteil zu sein. Wo stößt man an Grenzen der sicherheitsrelevanten Bauteile?
Peter Sander: Generell gibt es im Flugzeugbau keine Kompromisse, denn Sicherheit geht über alles. Verfahrenstechnisch reden wir bei Metallen im Flugzeugbau überwiegend vom Schweißen. Aus der Erfahrung wissen wir, wie solche Bauteile zu behandeln sind, um die hohen Sicherheitsanforderungen zu erfüllen. Was wir aber noch lernen müssen ist, die neuen Freiheiten der Geometrie in der Umsetzung als Bauteildesign maximal zu nutzen. Das Ergebnis wird ein neuartiges bionisches Flugzeugdesign sein.
Claus Emmelmann: Gegenwärtige Grenzen sind durch die Kompromisse bei der Oberflächengüte gegeben. Jene sind allerdings vergleichbar mit denen von Gussbauteilen. Diese Phänomene bringen, insbesondere bei Titan, eine erhebliche Reduktion der Dauerfestigkeit mit sich. Gerade diese Kenngröße ist jedoch für hochbelastete Strukturbauteile im Flugzeugbau essenziell. Durch nachgelagerte Oberflächenbehandlungen, wie etwa das Mikrostrahlen, sowie eine korrekte Wärmebehandlung kann die Dauerfestigkeit aber signifikant gesteigert werden. Im Ergebnis werden die Werte von gewalztem Material erreicht, wenn dies erforderlich ist.
Welchen Störgrößen oder Belastungen sind Flugzeuge ausgesetzt?
Peter Sander: Neben statischen Belastungen unterliegen Flugzeuge extremen Temperaturschwankungen zwischen Boden- und Flugbetrieb. Das wichtigste aber sind Dauerbelastungen, die den betroffenen Bauteilen das Maximum abfordern. Dazu gehören Starts und Landungen, aber auch der Flugbetrieb mit permanenten Turbulenzen, die am Flügelende schon mal zu mehreren Metern Durchbiegung führen können.
Claus Emmelmann: Flugzeuge sind in der Tat vielfältigen und äußerst komplexen Lastkollektiven ausgesetzt. Für die Auslegung der Haltestrukturen, wie Brackets, sind jedoch zunächst nur statische Lastfälle relevant. Dies erleichtert die Implementierung der noch jungen Technologie in den Flugzeugbau.
Welche Methoden oder Instrumente verwenden Sie zur Prozessüberwachung beziehungsweise Validierung beim Lasercusing?
Peter Sander: Für uns Flugzeugbauer ist die Kontrolle während der Aufbauphase des Bauteils einer der wichtigsten Industrialisierungsbausteine. In-line-Process Monitoring mit dem QM-Modul ›QMmeltpool‹ von Concept Laser bedeutet in der Praxis: Auf einer sehr kleinen Fläche von 1x1 qmm überwacht das System mittels Kamera und Foto-Diode den Prozess. Anschließend wird der Prozess dokumentiert.
Frank Herzog: Herr Sander weist hier auf einen wichtigen Aspekt hin. Die Module ›QMmeltpool‹, ›QMcoating‹, ›QMpowder‹ und ›QMlaser‹ sind Instrumente der aktiven Qualitätssicherung, während das Bauteil hergestellt wird. Sie messen die Laserleistung, das Schmelzebad, den Schichtaufbau des Metallpulvers und dokumentieren den Herstellprozess. Ein weiterer Aspekt ist das Arbeiten im geschlossenen System, um einen kontaminationsfreien Prozess zu gewährleisten. Das Entscheidende ist, alle Störeinflüsse auszuschalten. Wir können daher von einem geregelten, wiederholgenauen und prozesssicheren Herstellverfahren sprechen.
Claus Emmelmann: Wir verwenden auf unserer M2-Anlage von Concept Laser die Qualitätssicherungssoftware ›QMmeltpool‹ und ›QMatmosphere‹. Dies ermöglicht uns, wichtige Daten wie Laserparameter, Schmelzpoolverhalten, sowie die Zusammensetzung der Schutzgasatmosphäre zu überwachen und zu dokumentieren. Die Störgrößen durch Kontaminierung werden so ausgeschaltet.
Können Sie die Qualitätssicherungsansätze genauer erläutern?
Frank Herzog: Unsere Qualitäts-Management-Module, kurz ›QM-Module‹ genannt, entwickeln wir ständig weiter, um in puncto Aussagegüte, Bedienbarkeit, aber auch in der Einflussnahme auf den laufenden Bauprozess Maßstäbe zu setzen. Entwicklungsingenieure analysieren die Mikrostrukturen von Bauteilen, prüfen Festigkeiten und Dichtenverteilung. Als Pionier dieser Technik konnten wir die Qualität unserer Technologie in den vergangenen 15 Jahren entscheidend verbessern. Nur so war der Durchbruch in der Luft- und Raumfahrtbranche und der Medizintechnik möglich.
Verändert der generative Fertigungsansatz die konstruktiven Denkweisen im Flugzeugbau? Wenn ja, wie äußert sich dies?
Peter Sander: Die nächste Generation von Flugzeugingenieuren wird 3D-Druck mit seinen Möglichkeiten genauer verstehen. Ich würde auch von einem Paradigmenwechsel, wie Herr Sander es bereits ansprach, sprechen. Derzeit sind unsere Fertigungsingenieure im Gießen und Fräsen gut ausgebildet. Da braucht es neue Erkenntnisse und Erfahrungen. Generell ist die Laserschmelz-Technologie in der Lage, sicherheitsrelevante Bauteile zu entwickeln, die noch besser, leichter und langlebiger sind, als die Bauteile von heute.
Claus Emmelmann: Im Rahmen von bereits absolvierten Projekten, konnte festgestellt werden, dass die Möglichkeiten der laseradditiven Fertigung zu neuen Denkweisen und Leichtbaulösungen führen. Insbesondere für strukturoptimierte Bauteile, die in der Regel eine hohe Geometriekomplexität aufweisen, ist eine sehr direkte Umsetzung der Form zugunsten eines hohen Leichtbaugrads möglich.
Als logistische und kostenintensive Herausforderung gelten die Ersatzteile für zivile Flugzeuge aufgrund ihrer langen Lebenszyklen. Globale Verfügbarkeit, Lagerhaltung, Lebenszyklus und Zeitdruck fordern die Ersatzteilexperten. Wie kann eine generative Fertigung diese Situation verbessern?
Peter Sander: Air TrasNet fliegt bereits mit dem ersten von Airbus gedruckten Ersatzteil. Der ehemalige Hersteller des Spritzgußteiles war nicht mehr verfügbar, die Werkzeuge verschrottet. Die Fragestellung war damals, in neue Werkzeuge zu investieren oder den 3D-Druck zu nutzen. Wir konnten mit dem Laserschmelzverfahren auf Anhieb kostengünstiger anbieten. Konsequenz: Wir legen uns jetzt nicht mehr Teile aufs Lager, sondern werden künftig dezentrale Ersatzteil-Druckzellen betreiben und Kunststoff-Ersatzteile auf Anforderung herstellen.
Frank Herzog: Das Beispiel von Herrn Sander ist für das Laserschmelzen mit Metallen analog zu sehen. Eine generative Fertigung ist durch unterschiedliche Aspekte zu charakterisieren: Sie ist dezentral, zeitnah, schnell in der Umsetzung hin zum Bauteil. Sie erlaubt geringere Logistik- oder Lagerhaltungskosten. Sie ist ressourcenschonender als konventionelle Fertigungsmethoden und damit eine „Grüne Technologie“. Selbst „Production-on-demand“ wird so möglich.
Claus Emmelmann: Das Potenzial für die Ersatzteilversorgung im Flugzeugbau schätze ich auch hoch ein. Material- und Lagerhaltungskosten dürften sich enorm verbessern. Ich schätze den dezentralen Faktor, den Herr Herzog ansprach, als den eigentlichen Clou. Im Falle eines Bauteilversagens kann das Ersatzteil direkt vor Ort gefertigt werden. Dadurch werden Transportwege und Lieferzeiten minimiert.
Stichwort ›Ressourcenschonung‹ und ›Grüne Technologie‹. Wie sieht das der Flugzeugbauer?
Claus Emmelmann: Bei der herkömmlichen zerspanenden Herstellung wird der Rohling aus Plattenmaterial hergestellt. Das kann bis zu 95 Prozent recycelbarem Abfall führen. Beim Laserschmelzen sind wir quasi endkonturnah. Es gibt nur noch rund fünf Prozent Abfall. Aber selbst dieser Abfall kann nach einem Siebprozess wiederverwendet werden. Wir sprechen im Flugzeugbau von der ›buy to fly ratio‹ und da sind 90 Prozent ein fantastischer Wert. Dieser Wert spiegelt sich natürlich auch in der Energiebilanz wieder.
Welche generellen Veränderungen durch 3D-Strategien sehen Sie beim Flugzeugbau?
Peter Sander: Untersuchungen zeigen die Halbierung der Herstellungsschritte, da wir endkonturnahe Rohlinge erhalten. Interessant sind auch mehrteilige geschweißte Bauteile, die jetzt ohne Schweißvorrichtungen „aus einem Schuss“ hergestellt werden können. Das generative 3D-Drucken eröffnet neue Geschwindigkeiten bei der Bauteileentwicklung und im Bauprozess, die die bisherigen Entwicklungshorizonte massiv verkürzen. Auch bringt der neue Ansatz den Leichtbau voran.
Claus Emmelmann: Da wir bei den additiven Fertigungsverfahren keine Werkzeuge oder Halterungen benötigen, können wir das Bauteil direkt aus den 3D-CAD-Daten fertigen. Dieser Zeitfaktor sorgt dafür, dass wir häufig deutlich schneller sein können, als mit konventionellen Fertigungsverfahren. Bezüglich der Fertigungskosten: Wenn man die reinen Kosten für die Herstellung eines Fräsbauteils mit den Herstellkosten durch die laseradditive Fertigung vergleicht, schneiden die additiven Verfahren in der Regel ungünstiger ab. Aber wenn man seine Bauteile umkonstruiert und durch die neuen Designmöglichkeiten verbessert – etwa indem man sie leichter oder funktional leistungsfähiger macht – gibt es viele Beispiele, bei denen der Einsatz von additiven Fertigungsverfahren Kostenvorteile bietet.
Welche Möglichkeiten sehen Sie für Funktionsintegrationen, wie etwa Kühlfunktionen, bei Bauteilen der Zukunft?
Peter Sander: Ähnlich wie bei den Flugzeugstrukturen überdenken wir aktuell die gesamten Flugzeugsysteme. Wir stehen quasi vor einem neuen Kontinent der Möglichkeiten und Optionen. Für das vor uns liegende unbekannte Terrain brauchen wir, wenn Sie so wollen, Landkarten, also Erfahrungswerte und Fertigungsstrategien. Bei konventionellen Verfahren gibt es das alles. Hier betreten wir aber Neuland, allerdings mit faszinierenden Möglichkeiten. Erste Prototypen aus unserer Entwicklungsarbeit zeigen erhebliche Potenziale in den Bereichen Kosten- und Gewichtseinsparung. Funktionsintegration ist dabei eine der möglichen Optionen, die neu sind.
Frank Herzog: Funktionsintegration und Mehrwert stehen für das Laserschmelzen. Mehrwert zeigt sich durch bessere Qualität am Bauteil. Die konturnahe Kühlung im Werkzeugbau für Spritzgießen ist so eine Anwendung. In der Luftfahrt könnten dies gekühlte Elemente für die Elektronik oder hydraulische Komponenten sein. Bei Flugzeugkonstruktionen können zukünftige Bauteile gezielt die Kraftlinien auffangen.
Claus Emmelmann: Die Möglichkeit, ganze Baugruppen in einem Stück zu fertigen oder zusätzliche Funktionen in ein Bauteil zu integrieren, zählt zu den Vorteilen der laseradditiven Fertigung. In Bereichen, in denen wir die geometrische Gestaltungsfreiheit zur Funktionsintegration nutzen, wird die laseradditive Fertigung daher immer stärker an Bedeutung gewinnen. Allerdings sollte die Konstruktion bereits früh die Designfreiheit berücksichtigen, um sich von konventionellen Fertigungsstrategien zu unterscheiden. Hier mangelt es in Konstruktion und Entwicklung oft am fehlenden Wissen über die Möglichkeiten des Fertigungsverfahrens.
Der Flugzeugbau ist durch lange Lebenszyklen und kleine Losgrößen geprägt. Welche Auswirkungen hat dies auf generative Fertigungsstrategien?
Claus Emmelmann: Die vergleichsweise geringen Stückzahlen im Flugzeugbau spielen der laseradditiven Fertigung durchaus in die Karten. Bei den additiven Fertigungsverfahren können wir keine Skaleneffekte erzielen, wie das bei anderen Fertigungsverfahren der Fall ist. Dies bedeutet konkret: Die Stückkosten ändern sich nur sehr gering mit steigendem Produktionsvolumen. Im Umkehrschluss ergibt sich für konventionelle Fertigungsverfahren, wie etwa dem Druckguss, dass sie bei großen Stückzahlen wirtschaftlicher einzusetzen sind.
Frank Herzog: Das sehe ich auch so. In der Tat ergeben der Losgrößenansatz, aber auch Sicherheitsaspekte und die Langlebigkeit ein spezielles Anforderungsprofil für den Flugzeugbau. Hier liegen auch die Stärken des Laserschmelzens: Werkzeuglos, Production-on-demand, schnell, wirtschaftlich, qualitativ hochwertig.
Peter Sander: Wenn wir die beiden Ansätze ›Qualität‹ sowie ›Geometriefreiheit‹ betrachten, so werden Bauteile des 3D-Drucks mit Metallen für den Einsatz im Flugzeugbau besser, leichter, schneller verfügbar und vor allem sicherer sein – wohlgemerkt auch mit Vorteilen auf der Kostenseite.
Kritiker sagen, dass die Bauraumgrenzen die Möglichkeiten beschneiden. Befürworter hingegen sagen, dass dies durch klassische Montage- oder Fügetechniken an und für sich keine echte Einschränkung sei. Wie bewerten Sie diese Diskussion?
Peter Sander: Das wird die Zukunft zeigen. Eins ist jedoch schon jetzt klar für uns. Wir reden über schweißbares Material. Dies eröffnet die Möglichkeit, verschiedene Bauteile zusammenzuschweißen. Methoden der Fügetechnik werden hier zum Zuge kommen.
Frank Herzog: In der Vergangenheit wurden Bauraumsteigerungen um bis zu 700 Prozent erzielt. Die Laserleistung wurde auf 1 000 Watt gesteigert oder die Baurate bei Aluminium um den Faktor 10 bis 15 erweitert. Das sind gewaltige Fortschritte. Bei sehr großen Bauteilen vermehren sich die prozessbedingten Eigenspannungen im Teil. Diese Verzugsneigung setzt Grenzen. Letztlich setzen nicht die Bauräume die Grenzen, sondern physikalische Grenzen sind auszuloten. Mit einer intelligenten Fügetechnik wird es möglich, großvolumige Bauteile, die über die reine Bauraumgröße von Laserschmelzanlagen hinausreichen, zu entwickeln.
Claus Emmelmann: Das Fügen von einzelnen Substrukturen zu größeren Bauteilen ist zwar technisch machbar. Jedoch bedeutet dies für das Gesamtbauteil, die Notwendigkeit der Berücksichtigung zusätzlicher Fertigungsrestriktionen. Die gestalterischen Freiheiten der laseradditiven Fertigung werden dadurch eingeschränkt. Wir sollten auch beachten, dass die Fertigungskosten durch das Bauteilvolumen bestimmt werden. Daher lohnen sich unter wirtschaftlichen Gesichtspunkten derzeit eher kleiner Bauteile, die bereits durch die am Markt verfügbaren Anlagen hergestellt werden können. In der Zukunft kann sich das natürlich verändern.
Welche generativen Bauteile werden im Flugzeugbau der nächsten Dekade denkbar sein?
Peter Sander: Wenn die Entwicklung weiter so fortschreitet, sehe ich keine technischen Beschränkungen. Die Entscheidung wird dann letztendlich über die Wirtschaftlichkeit und damit über die industrielle Verfügbarkeit von Metallpulvern und Hochgeschwindigkeitsmaschinen fallen.
Claus Emmelmann: Auch in zehn Jahren werden wir noch keine kompletten Flugzeuge drucken. Doch ich bin sicher, dass sich in Zukunft immer größere und komplexere Bauteile wirtschaftlich mittels laseradditiver Fertigung herstellen lassen.
Meine Herren, vielen Dank für das Interview.
Download
Diesen Artikel können Sie hier im PDF-Format [307 KB] herunterladen.
Mehr Informationen zu Concept Laser:
![]() |
CONCEPT Laser GmbH |
![]() |
An der Zeil 8 |
![]() |
96215 Lichtenfels |
![]() |
Tel.: +49 (0) 9571 / 949-238 |
![]() |
Fax: +49 (0) 9571 / 949-239 |
![]() |
E-Mail: info@concept-laser.de |
![]() |
www.concept-laser.de |
War dieser Artikel für Sie hilfreich?
![]() |
![]() |
![]() |
![]() |
![]() |
Bitte bewerten Sie diese Seite durch Klick auf die Symbole.
Zugriffe heute: 1 - gesamt: 8670.