Die Kraft aus dem Memorymetall
Energieumwandlung cleverer Art
Formgedächtnismetalle haben mittlerweile viele Bereiche erobert. Sie sind in der Medizintechnik ebenso anzutreffen, wie im Maschinenbau oder in der Automationstechnik. Dr.-Ing. Joachim Strittmatter erläutert das Potenzial dieser Metalle, die sich sogar für Wärmekraftmaschinen eignen.
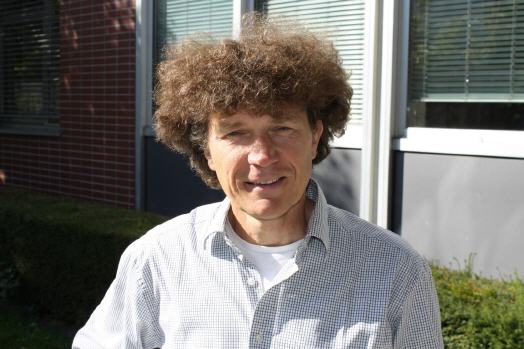
Sehr geehrter Herr Dr. Strittmatter, wie sind Sie auf die Idee gekommen, eine Wärmekraftmaschine mithilfe von Formgedächtnismetallen zu entwickeln?
Dr. Joachim Strittmatter: Die Grundidee stammt von Prof. Paul Gümpel, den ich durch mein Studium an der Hochschule Konstanz und meinen Studienarbeiten im Werkstoffprüflabor her kannte. Er selbst war genauso begeistert von Formgedächtnislegierungen und beantragte daher ein Forschungsvorhaben, das die Entwicklung einer Wärmekraftmaschine auf Basis von Formgedächtnis-Elementen beinhaltete. Da das Projekt zeitgleich mit dem Ende meines Maschinenbaustudiums bewilligt wurde, konnte ich direkt als Projektmitarbeiter in dieser Thematik starten. So entwickelte ich zusammen mit ihm über die Jahre mehrere Prototypen von Wärmekraftmaschinen mit Formgedächtnismetallen.
Welchen Nutzen versprechen Sie sich von so einer Maschine?
Dr. Strittmatter: Eine derartige Maschine bietet die Möglichkeit, Wärme in Kraft, sprich thermische Energie in mechanische Energie umzuwandeln. Das Faszinierende daran ist, dass diese Energieumwandlung direkt erfolgt, also ohne weitere Umwandlungsschritte. Da zudem bei den derzeit verwendeten Formgedächtnislegierungen die Umwandlungstemperaturen im Bereich von rund 65 Grad Celsius liegen, ist es möglich, eine derartige Maschine mit Niedertemperaturwärme im Bereich von 80 bis 90 Grad Celsius auf der Warmseite und mit Luft oder Wasser im Bereich von 5 bis 35 Grad Celsius auf der Kaltseite zu betreiben.
Die Warmseite könnte man in Ländern wie Island oder Neuseeland direkt durch oberflächennahe Geysire abdecken, in Ländern wie Afrika oder Asien müsste Oberflächenwasser erst noch durch solar betriebene Wärmetauscher erwärmt werden. Hierzulande bietet sich gerade in industriellen Betrieben und Kraftwerken durch immense Energiemengen an Prozesswässern oder auch warmer Abluft im meist nicht genutzten Niedertemperaturbereich unter 100 Grad Celsius die Möglichkeit eines sinnvollen Einsatzes von Wärmekraftmaschinen mit Formgedächtnislegierungen.
Anstelle eines energieintensiven Kühlens von Prozesswasser in Wärmetauschern und Kühlkreisläufen könnten kaskadierte Wärmekraftmaschinen dazu beitragen, durch Energieumwandlung den gewünschten Kühleffekt zu erreichen.
Welche Leistung ist mit solchen Konstruktionen erreichbar?
Dr. Strittmatter: Aufgrund meiner eigenen Erfahrungen, die sich bei der Umsetzung einer scheinbar genial einfachen Idee in eine tatsächlich gebaute Maschine in vielen zu überwindenden, technischen Details zeigen, ist es sicherlich möglich und zielführend, Wärmekraftmaschinen mit einer Leistung von 1 kW zu bauen und je nach Anwendungsfall dann mehrere Wärmekraftmaschinen parallel zu verwenden.
Wie hoch schätzen Sie das Potenzial eines Wärmekraftmotors?
Dr. Strittmatter: Sofern es gelingt, eine technisch einfache wie kostengünstige Lösung zu realisieren, die zudem wenig Bauraum benötigt und eine hohe Lebensdauer erreicht, steckt ein sehr großes Potenzial in derartigen Wärmekraftmaschinen. Dann ist es meiner Meinung nach auch zielführend, diese Maschinen nicht nur dezentral etwa als autarke Motoren einzusetzen, sondern auch überall dort, wo in großen Mengen Niedertemperaturwärme anfällt, also beispielsweise in Großkraftwerken oder Gießereien.
Ist das Projekt bereits über das Versuchsstadium hinausgekommen?
Dr. Strittmatter: Leider nein. Wir haben an der Hochschule Konstanz neben einem Demonstrations-Modell, das wir sowohl auf der Hannover-Messe als auch in der damaligen Knoff-Hoff-Show zeigen konnten, in diversen Folgeprojekten weitere Demonstratoren mit unterschiedlichen Antriebsprinzipien entwickelt, jedoch kamen wir selbst in der größten Ausbaustufe nicht über eine mechanische Abtriebsleistung von 63 Watt hinaus.
Woran liegt das?
Dr. Strittmatter: In unserem Fall liegt das wohl hauptsächlich am Schrägscheibenprinzip. Bei Erwärmung in dem Wasserbad entwickeln die Drähte eine rund dreimal so hohe Zugkraft wie auf der gegenüberliegenden Kaltseite. Diese Zugkräfte in axialer Richtung werden nur zu einem Teil über die Kräftezerlegung und den Hebelarm in ein Moment umgewandelt, das die Wärmekraftmaschine in Rotation ersetzt – ein Großteil der Zugkräfte wirkt weiterhin auf die Scheiben und belastet damit die Lager.
Wenn Sie nun von einem kleinen Modell mit wenigen dünnen Drähten auf eine deutliche größere Anlage mit vielen dickeren Drähten upscalen, vervielfachen sich die auf die Scheiben wirkenden Kräfte enorm. Hinzu kommt, dass auf der Warmseite – wie erwähnt – deutlich höhere Kräfte auftreten als auf der Kaltseite, die Scheibe also nicht symmetrisch belastet wird. In den ersten Tests mit einer Wärmekraftmaschine mit 120 Drähten mit einem Meter wirksamer Länge und 1 mm Durchmesser wurden bei arretierter Maschine Stillstandmomente von über 120 Nm ermittelt und es erfolgte der erste Lagerschaden nach wenigen Stunden Betriebszeit. Nachdem wir mit zusätzlichen, exzentrisch einstellbaren Lagern am Scheibenumfang die auf das Hauptlager wirkenden Kräfte deutlich reduzieren konnten, versagte dann nach wenigen Tagen Betriebszeit die Achse aufgrund eines Ermüdungsbruchs.
Eine weitere Herausforderung stellen dann die Erwärmung und die Abkühlung dar: wenn bei der vergrößert gebauten Anlage sehr viel mehr Drahtmaterial erwärmt und abgekühlt werden muss, stoßen Sie ganz schnell an Grenzen, die in einer Laboranlage nicht mehr zu stemmen sind. Um Ihre Frage kurz zu beantworten: beim Hochskalieren eines einfachen Prinzips erwarten Sie konstruktive und logistische Probleme, die für ein Forschungsinstitut nur schwer zu realisieren sind. Hier müsste man für eine erfolgreiche, industrietaugliche Weiterentwicklung deutlich mehr finanzielle und personelle Ressourcen einsetzen, was meiner Meinung nach nur mit einem potenten Industrieunternehmen zu schaffen ist.
Zur Technik: Wieso funktioniert eine Wärmekraftmaschine überhaupt?
Dr. Strittmatter: Die Antwort steckt in den Phasenzuständen der Formgedächtnislegierungen, die bei niederen Temperaturen deutlich andere Eigenschaften aufweisen, als bei höheren Temperaturen. In dem martensitischen Gefüge, das ist die fachmännisch Bezeichnung für den sogenannten Niedertemperaturbereich, weisen Formgedächtnislegierungen deutlich geringere Bindungskräfte zwischen den Atomen auf, als in der austenitischen Gefügeform, also dem Hochtemperaturbereich.
Beim Wechsel zwischen den beiden Zuständen findet im Material eine reversible Phasenumwandlung statt, was zu der Änderung vieler mechanischer, elektrischer und magnetischer Eigenschaften führt. Hinsichtlich der Zugspannung eines Formgedächtnisdrahtes führt das dazu, dass Sie zum Verlängern im martensitischen, kalten Zustand nur etwa ein Drittel der Kraft benötigen, die Sie bei der Rückumwandlung im austenitischen, warmen Zustand erhalten.
Wenn Sie nun ein Bauteil aus Formgedächtnismetall zyklisch im kalten Zustand verlängern und im warmen Zustand sich verkürzen lassen, können Sie diese Differenz als mechanische Energie nutzen. In unserem Fall ist dies die treibende Kraft: die Zugkräfte der sich gerade im Warmwasser befindlichen Drähte reicht aus, um nicht nur die sich gerade auf der Kaltseite befindlichen Drähte wieder vorzudehnen, sondern darüber hinaus auch die Wärmekraftmaschine in Rotation zu halten, auch wenn an der Abtriebswelle mechanische Energie abgegriffen wird.
Ist dieses Verhalten mit Verschleiß verbunden?
Dr. Strittmatter: Sofern Sie gewisse Grenzen einhalten, können Sie diese martensitische Phasenumwandlung beliebig oft wiederholen. Aber schon bei vergleichsweise dünnen Drähten ist die Erwärmung und Abkühlung nicht für alle Atome gleichzeitig, sondern zeitlich etwas versetzt. Diese führt dazu, dass einige Atome sich gegenseitig bei der Phasenumwandlung behindern und sich sogenannte Gitterfehler einstellen. Diese Gitterfehler summieren sich über die Anzahl der Zyklen, bis irgendwann die Phasenumwandlung zu stark behindert wird und ein Verkürzen des Formgedächtniselementes nicht mehr erfolgt, in unserem Fall die Wärmekraftmaschine stehen bleiben würde. Man spricht hier allerdings nicht von Verschleiß, sondern von Ermüdung des Formgedächtniseffektes.
Wird das Metall daher schleichend zu Schrott?
Dr. Strittmatter: Schrott ist das Material dadurch jedoch nicht, es wurde ja kein Atom verbraucht, lediglich die Phasenumwandlung ist behindert. Durch eine Art Erholungsglühen und erneutem Eintrainieren des Effektes, einer thermomechanischen Behandlung des Materials, könnte man nicht mehr funktionierende Drähte wieder reaktivieren.
Wird der Motor leistungsstärker, wenn dickere Drähte verwendet werden?
Dr. Strittmatter: Indem Sie dickere Drähte verwenden, erhöhen Sie die Querschnittsfläche und damit die wirkenden Zugspannungen in den Drähten. Sofern ausreichende Energiemengen zum Wärmen und Kühlen der Formgedächtniselemente vorhanden sind, kann ich Ihrer Frage zunächst zustimmen. Allerdings dauert der Wärmeübergang bei dickeren Drähten länger, was die Drehzahl einer Wärmekraftmaschine stark reduziert. Der Königsweg liegt eher in der Verwendung von vielen Drahtbündeln aus dünnen Drähten, um eine Querschnittsflächenerhöhung zu erreichen, ohne die Phasenumwandlungen zu verlangsamen und damit die Drehzahlen zu verringern.
Könnte ein Motor aus Formgedächtnismetallen einem Elektromotor das Wasser reichen?
Dr. Strittmatter: Die Werkstoffentwicklung und Herstellung von kommerziell verfügbarem Formgedächtnismaterial hat in den letzten Jahrzehnten enorme Fortschritte erzielt, was sich nicht zuletzt in einer permanent steigenden Anzahl an erreichbaren Lastzyklen widerspiegelt. Meiner Ansicht nach haben Wärmekraftmaschinen nur eine Chance auf eine kommerzielle Umsetzung im großindustriellen Maßstab, wenn die Maschinen sich selbst amortisieren, sprich die Ermüdung der Formgedächtnislegierungen erst dann eintritt, wenn sich die Anlagenkosten schon lange gerechnet haben.
Durch das steigende Interesse anderer Branchen an hochwertigen Formgedächtniselementen werden derartige Elemente bei sinkendem Preis qualitativ immer besser, sodass dieser „break-even-point“ tatsächlich erreicht werden kann. Einem Vergleich mit einem Elektromotor, der seit knapp 200 Jahren in ganz anderem Maßstab weiterentwickelt wurde, werden Permanentantriebe mit Formgedächtnislegierungen in absehbarer Zeit wohl aber nicht standhalten.
Ganz anders sieht es allerdings für Anwendungen in der Aktorik aus: dort kann ein einzelner Zugdraht aus Nitinol einen kompletten Elektromotor ersetzen, um beispielsweise einen Verschließmechanismus oder eine Klappe zu betätigen. Aufgrund der damit verbundenen Gewichtsreduzierung und Vereinfachung der technischen Lösung sind derartige Einsätze von Formgedächtnisdrähten besonders in der Automobiltechnik sehr interessant. Wenn Sie dann noch die sensorischen Eigenschaften der Formgedächtnismetalle gezielt ausnutzen können, sind sie teileweise heute schon konventionellen Elektromotoren überlegen.
Welche Arten von Wärmekraftmaschinen sind generell denkbar?
Dr. Strittmatter: Neben der Wärmekraftmaschine mit Schrägscheibenprinzip haben wir noch eine Antriebsart nach dem Exzenterprinzip entwickelt, bei dem in einer Fahrradfelge ein zweiter Satz aus Formgedächtnisdrähten auf einer exzentrisch gelagerten Achse zentriert ist und bei halbseitigem Eintauchen in warmes Wasser in Verbindung mit der kühleren Luft eine langsame Drehbewegung generiert. Es gibt aber noch viele andere Funktionsprinzipien, wie beispielsweise ein meines Wissens nur theoretisch existierendes Design, das die Temperaturunterschiede zwischen Tiefenwasser und Oberflächenwasser im Meer ausnutzt, um eine langsame Drehbewegung eines Formgedächtnisantriebs zu realisieren. Andere Designs verwenden konzentrierte und durch Linsen verstärkte Sonnenstrahlen zur Erwärmung von Formgedächtnisstreifen.
Nun sind die Eigenschaften von Formgedächtnismetallen auch in anderen Bereichen gefragt. Wo werden diese heute eingesetzt?
Dr. Strittmatter: An erster Stelle steht hier die Medizintechnik. Die Stents – per Laser zu einem Geflecht geschnittene Röhrchen – die als Gefäßstützimplantate eingesetzt werden, sind dabei die Hauptanwendung. Weitere typische Anwendungen liegen in der minimalinvasiven Chirurgie, da Formgedächtnislegierungen durch ihre große Dehnbarkeit im superelastischen Bereich die Möglichkeit bieten, kleine flexible Werkzeuge bei minimalsten Zugangsöffnungen im Körper zu bewegen, um dann etwa über ausklappende Fangkörbchen vorzertrümmerte Nieren- oder Gallensteine einzufangen.
Weitere Anwendungen sind Knochenklammern oder orthodontische Drähte für die Zahnmedizin. Es finden sich jedoch in vielen anderen Bereichen Produkte mit Formgedächtnisbauteilen, von Verbrühungsschutzsystemen in Duscharmaturen über hochgenaue, autark arbeitende Positioniersysteme in der Luftfahrt, Schrumpfringe als Verbindungssysteme für Unterwasser-Pipelines bis hin zu Ausrückmechanismen von Solarpanels bei Satelliten und Raumfahrtstationen oder auch Greifsystemen in der Mikrosystemtechnik.
Welche Kräfte können dabei genutzt werden und wie groß sind diese?
Dr. Strittmatter: Die Kräfte richten sich vor allem nach dem Querschnitt der Formgedächtniselemente und der Auslegung hinsichtlich des Hubs und der Schalthäufigkeit. Soll ein Aktor beispielsweise zwei bis drei Prozent Hub über mindestens 10 000 Zyklen erreichen, sind 350 MPa realistisch. Bezogen auf einen 2 mm dicken Runddraht werden hier Kräfte von rund 1 100 N erreicht, bezogen auf eine Hublast von einer Tonne ist ein Runddraht mit 6 mm Durchmesser erforderlich. Bei Anwendungen im Brandschutz legt man Bauteile jedoch nur auf zehn Schaltungen aus und rechnet mit Zugspannungen von bis zu 800 MPa. Ich kenne auch eine Anwendung zum Aufsprengen von Felsblöcken über das Erwärmen von Formgedächtnisbolzen, die in Bohrungen in einen Felsen positioniert werden und bei elektrischer Erwärmung einen definierten Riss erzeugen. Es wird von maximalen Kräften bis zu 900 kN berichtet. Im Übrigen eignet sich dieses beim Felsen demonstrierte Verfahren in der Bauwirtschaft um Betonteile gezielt abzutrennen.
Wo liegen die Grenzen des Hebens eines Gewichtes hinsichtlich Last und Weg?
Dr. Strittmatter: Hinsichtlich des Wegs erreichen Formgedächtniselemente aus Nickel-Titan in axialer Zugrichtung maximal sechs Prozent, hinsichtlich der Last 800 N pro eingesetzten Quadratmillimeter Querschnittsfläche – dann allerdings nur eine begrenzte Anzahl an Lastwechseln. Wenn hohe Schaltzyklen gefordert werden, erreichen Sie große Hübe nur bei geringeren Belastungen beziehungsweise die größeren Lasten nur bei reduziertem Hub. Auf der anderen Seite können Sie durch Wahl einer geeigneten Über- oder Untersetzung, eines Getriebes oder auch durch Verwendung einer als Feder ausgeführten Formgedächtnisdrahtes deutlich höhere Werte hinsichtlich Weg und Kraft erreichen.
Wie kam man überhaupt auf den Memory-Effekt?
Dr. Strittmatter: Wie so oft war dies ein Zufall: Arbeiter berichteten beim Schweißen von besonderen Titanblechen für ein U-Boot, dass die Bleche „zurückschlugen“. Der Effekt wurde anschließend am amerikanischen Naval Ordnance Laboratory erforscht und gab durch die Anfangsbuchstaben, erweitert mit den chemischen Elemente Ni und Ti, dieser am weitesten verbreiteten und am besten erforschten Formgedächtnislegierung deren geschützten Namen ›nitinol‹.
Wo liegen die Grenzen, damit Memory-Metalle noch funktionieren. Gibt es Dimensionsgrenzen nach unten beziehungsweise oben?
Dr. Strittmatter: Wenn Sie Bauteile aus Formgedächtnislegierungen immer dünner machen, funktioniert der Effekt immer besser, weil weniger Atome die Umwandlung makroskopisch behindern können. Auch die Wärmeeinbringung ist dann quasi schlagartig. In einem Forschungsprojekt wurde festgestellt, dass die Phasenumwandlung eines Bauteils bei wenigen Atomlagen mit annähender Schallgeschwindigkeit erfolgt. Derartige Teile sind jedoch kommerziell nicht erhältlich.
Bei den mir bekannten Herstellern von Formgedächtnis-Halbzeugen liegt die untere Grenze bei NiTi-Draht derzeit bei 25 µm, für Folien bei 76 µm. Nach oben gibt es hier herstellungsbedingte Grenzen, vor allem aber auch in der Anwendung, denn irgendwoher muss man ja auch die Energie zum Erwärmen oder Abkühlen beziehen und ins System einbringen können. Mir bekannt sind in diesem „oberen Bereich“ für thermische Memory-Metalle beispielsweise Zugdrähte beziehungsweise Stäbe mit 15 mm Einzeldurchmessern oder kommerziell verfügbare Einzelplatten mit 2,5 mm Stärke.
Wie und mit welchen Werkzeugen lassen sich Formgedächtnismetalle bearbeiten?
Dr. Strittmatter: Wer das erste Mal mit nitinol arbeitet und beispielsweise Gewinde oder Bohrungen einbringen möchte, merkt schnell, dass man hier mit teilweise komplett anderen Werkzeugen und Schnittgeschwindigkeiten arbeiten muss. Dies ist jedoch in der Branche mittlerweile gut bekannt und bietet kaum noch nennenswerte Probleme. Natürlich darf bei der Bearbeitung auch kein hoher Wärmeeintrag auftreten. Für eine optimale Oberflächenqualität muss jedoch nach der mechanischen Bearbeitung oft noch ein elektrochemischer Prozess nachgeschaltet werden, wie beispielsweise Elektropolieren. Schon etwas schwieriger gestaltet sich das Schweißen von Formgedächtniselementen mit anderen Bauteilen.
Was sind die Alleinstellungsmerkmale von Formgedächtnismetallen im Vergleich zu Produkten, die mit herkömmlicher Technik realisiert sind?
Dr. Strittmatter: Die martensitische Phasenumwandlung verbunden mit Bauteiländerungen im Prozentbereich, sprich der thermische Formgedächtniseffekt, macht diese Werkstoffgruppe so einzigartig, weshalb sie nicht nur Funktionswerkstoffe genannt werden, sondern teilweise auch Smart Materials oder Intelligente Materialien. Der superelastische Effekt in der Hochtemperaturphase ermöglicht diese einzigartigen Verformungsdehnungen auf nahezu konstantem Spannungsniveau, bei Nickel-Titan verbunden mit einer hervorragenden Körperverträglichkeit. Daher lassen sich auf der einen Seite mit geringem Materialeinsatz thermische Aktoren im hohen Arbeitsbereich realisieren, auf der anderen Seite ermöglichen Formgedächtnismetalle manchmal einzigartige Einsatzmöglichkeiten im menschlichen Körper.
Haben Sie ein aktuelles Forschungsvorhaben mit Formgedächtnismetallen laufen?
Dr. Strittmatter: Derzeit beschäftige ich mich mit mehreren Forschungsvorhaben auf dem Gebiet der Formgedächtnislegierungen, darf Ihnen aufgrund von Geheimhaltungsvereinbarungen mit den beteiligten Firmen jedoch nicht allzu viel davon erzählen. Am weitesten hinsichtlich einer kommerziellen Umsetzung und auch bestens abgesichert mit drei Patenten sind wir mit unserem Formgedächtnis-Marknagel zur Knochenverlängerung. Dieses klinische Implantat wird von uns in Kooperation mit einer Medizinfirma entwickelt und dient zur Knochenverlängerung beim Menschen.
Sie können sich den Marknagel als zylinderförmiges Bauteil vorstellen, dass in die Markhöhle des Oberschenkels nach zuvor erfolgtem Bruch eingesetzt wird. Dieser Marknagel ist mit den beiden Knochenfragmenten des Oberschenkels über Querverriegelungsbolzen fixiert und dient dazu, diese 1 mm pro Tag auseinander zu bewegen und den gesetzten Knochenspalt täglich zu vergrößern. Der menschliche Körper ist in der Lage, in dem entstehenden Raum neues Kallus einzubringen, das nach Beendigung der Verlängerungsphase immer mehr kalzifiziert, also knochenähnlicher wird. Dadurch kann ein um mehrere Zentimeter kürzeres Bein dem längeren angeglichen werden.
Was möchten Sie mit Formgedächtnismetallen noch erreichen?
Dr. Strittmatter: Auf der einen Seite würde ich nur allzu gerne den beiden hier vertieft vorgestellten Anwendungen von Formgedächtnismetallen in einer Wärmekraftmaschine und in einem klinischen Verlängerungs-Marknagel zum industriellen Einsatz verhelfen. Auf der anderen Seite sehe ich meine Aufgabe aber auch darin, den heutigen Studierenden diese faszinierenden Materialien näher zu bringen, auch wenn zukünftige Anwendungen dann außerhalb meines Einflussbereiches über deren Köpfe zum Einsatz kommen.
Sehr geehrter Herr Dr. Strittmatter, vielen Dank für das Interview!
Download
Diesen Artikel finden Sie auch in Heft 4/2019 auf Seite 16. Zum besagten Heft führt ein Klick auf den nachfolgenden Button!
Mehr Informationen zum WITG:
![]() |
Institut für Werkstoffsystemtechnik Thurgau an der Hochschule Konstanz |
![]() |
Konstanzerstrasse 19 |
![]() |
CH-8274 Tägerwilen |
![]() |
Tel: 0041 71 666 42 04 |
![]() |
Fax: 0041 71 666 42 01 |
![]() |
E-Mail: info@witg.ch |
![]() |
www.witg.ch |
![]() |
|
![]() |
Adresse in Deutschland: |
![]() |
Alfred-Wachtel-Str. 8 |
![]() |
78462 Konstanz |
![]() |
Tel: 0049 7531 206 447 |
![]() |
Fax: 0049 7531 206 87 447 |
War dieser Artikel für Sie hilfreich?
![]() |
![]() |
![]() |
![]() |
![]() |
Bitte bewerten Sie diese Seite durch Klick auf die Symbole.
Zugriffe heute: 1 - gesamt: 3705.