Sigma: Spritzgießsimulation für Werkzeugbauer
Von der Konstruktion zur Produktion
Die aktuellsten Entwicklungen in Rechnerkapazitäten und Lösungsalgorithmen für Spritzgießsimulationssoftware ermöglichen ein neues Anwendungsspektrum der Spritzgießsimulation im Werkzeugbau. Bewertung der Energieeffizienz, Werkzeugoptimierung und Bauteilqualität stehen im Mittelpunkt.
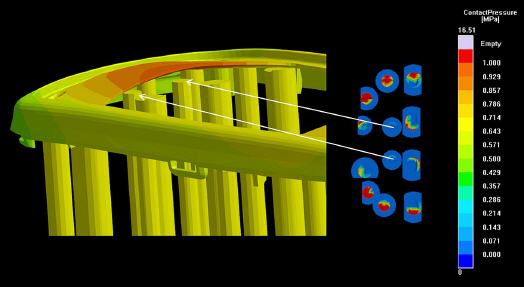
Denkt man an Software für den Werkzeugbau, kommt man wahrscheinlich nicht als erstes auf Spritzgießsimulation. Die Verwendung von Spritzgießsimulationssoftware ist in der Branche hauptsächlich auf die Konstruktionsphase (Design-Phase) des Artikels begrenzt und Werkzeugmacher betrachten dieses Tool noch immer als Hilfsmittel für einfache Fragestellungen während der Konstruktionsphase: Positionierung von Anspritzpunkten, Entstehung von Bindenähten, Angussbalancierung, Verzug. Die Möglichkeiten moderner Spritzgießsimulation gehen aber weit über die Beantwortung dieser klassischen Fragestellungen hinaus.
Die aktuellen Entwicklungen im Bereich Modellierungs- und Lösungsalgorithmen, sowie die stetig wachsenden Rechenleistung aktueller Computerhardware, eröffnen ein komplett neues Spektrum für die Anwendung von Spritzgießsimulation gerade im Werkzeugbau und an der Schnittstelle zur Produktion. Über die Beantwortung konventioneller, design-bezogenen Fragen können heutzutage detaillierte Antworten zur energetischen Leistungsfähigkeit eines Spritzgießwerkzeugs, zur Sinnhaftigkeit konturfolgender Temperierkonzepte, zum Entformungsverhalten oder zu mechanischen Verhalten von einzelnen Werkzeugkomponenten gegeben werden. Diese Aussagen begrenzen sich nicht mehr nur auf die Betrachtung einer einzelnen Sequenz aus Füllen, Nachdruck, Kühlen sondern umfassen ganze Produktionszyklen, beleuchten den Einfluss von möglichen Produktionsunterbrechungen und erlauben eine Vorhersage von Prozessfenstern.
Die Spritzgießsimulation mit SIGMASOFT® ist damit nicht mehr auf die Artikelentwicklung begrenzt, sondern wird heute schon für kundenspezifische Werkzeugoptimierungen sowie wissensbasierte, d.h. effiziente Optimierungen & Troubleshooting während der Produktion verwendet. Darüber hinaus ist die Berechnung von Entfomungskräften oder Kernverformungen als erweiterte Werkzeugauslegung heutzutage bereits per Knopfdruck möglich.
Die Spritzgießsimulation Software SIGMASOFT basiert auf der Finite Volume Methode. Mit einem vollständigen 3D-Ansatz ermöglicht sie in jeder Phase des Produktentwicklungszykluses eine schnelle und einfache Integration aller verfügbaren geometrie- und prozessrelevanten Einflussfaktoren, wobei neben der CAD-Bauteilgeometrie weitere Informationen, wie Werkzeugkomponenten, Heißkanäle oder Parameter der Prozessführung physikalisch exakt erfasst und vom Anwender einfach in die Berechnung integriert werden können. Die Vernetzung des erzeugten Simulationsmodells erfolgt voll automatisch, ohne Nacharbeit, und bietet damit einen deutlichen Produktivitätsvorteil gegenüber konventioneller Software. Zudem bildet erst die automatische Vernetzung die Grundlage komplexe Werkzeugsystem überhaupt in dem beschriebenen Detaillierungsgrad und mit der aufgezeigten Aussagefähigkeit effizient, d.h. industriell einsetzbar berechnen zu können.
Mit dem so erzeugten Simulationsmodell werden instationäre thermische Werkzeuganalysen über beliebige Produktionszyklen hinweg durchgeführt und dienen so als Grundlage zur bauteil- oder prozessbezogenen Werkzeugoptimierung mit dem Ziel einer minimalen Zykluszeit bei maximaler Bauteilqualität. Aussagen zur Effizienz des gewählten Temperierkonzeptes unter energetischen Gesichtspunkten sind so im Detail möglich. Darüber hinaus können selbst Auswerferkräfte bei der Entformung untersucht und die Auswirkungen nachgelagerter Temperierprozesse (wie etwa Lackierung oder Galvanisierung) auf die Spannungsverteilung und Maßhaltigkeit im Bauteil analysiert werden. Für Werkzeugkonstrukteure und Formenbauer bietet SIGMASOFT damit eine breite Palette Möglichkeiten, sich durch geleisteten Mehrwert gegenüber seinen Kunden zu profilieren und sich so gegenüber dem Wettbewerb zu positionieren.
Entformungsberechnung: Voraussetzung für eine zuverlässige Werkzeugkonstruktion
Ein klares Beispiel, wo der Mehrwert der Integration aller Werkzeugelemente mit dem Kunstoffbauteil bei der Spritzgießsimulation eindeutig wird, ist die Entformungssimulation. Die aktuellsten Entwicklungen von Sigmasoft ermöglichen die Berechnung des Kontaktdrucks zwischen den Auswerferstifte und dem Kunststoffbauteil. Damit ist es nun möglich, den Kontaktdruck von jedem einzelnen Auswerferstift auf das Bauteil zu berechnen und damit zu bewerten, ob bei bestimmten Entformungsbedingungen das Bauteil beschädigt werden könnte oder ob eine sichere Entformung möglich ist. Dazu ist es auch möglich zu bewerten, ob einzelne Auswerferstifte in der Auswerferkonfiguration überhaupt wirksam sind, bzw. ob deren Positionierung effizient ist. Die Reibung zwischen Bauteil und Werkzeug wird bei der Berechnung natürlich berücksichtigt.
Die Entformungsbedingungen können in der Simulation genau an die Realität angepasst werden: Die Geschwindigkeit der Stiftbewegung, der zurückgelegte Weg, die Reibung und die Entformungszeit sind einige der Parameter, die variiert werden können. Als Ergebnis der Simulation wird das Kontaktdruckprofil an jedem einzelnen Stift gezeigt. Darüber hinaus wird die von den Auswerferstiften im Bauteil verursachte Verformung dargestellt. Damit können Stellen an denen kritische Verformungen überschritten ist, identifiziert und dort die Entformungsbedingungen entsprechend angepasst werden. Auch eventuelle Markierungen an der Oberfläche werden mit der Simulation nachvollziehbar. Selbst der Verschleiß von Auswerferstiften und damit deren Haltbarkeit bzw. die Wartungszyklen können bewertet werden.
Mehr Informationen zur SIGMA Engineering GmbH:
![]() |
SIGMA Engineering GmbH |
![]() |
Kackertstr. 11 |
![]() |
52072 Aachen |
![]() |
Tel.: +49 (0) 241-89 495-0 |
![]() |
Fax: +49 (0) 241-89 495-20 |
![]() |
E-Mail: info@sigmasoft.de |
![]() |
www.sigmasoft.de |
War dieser Artikel für Sie hilfreich?
![]() |
![]() |
![]() |
![]() |
![]() |
Bitte bewerten Sie diese Seite durch Klick auf die Symbole.
Zugriffe heute: 3 - gesamt: 6046.