Bauteilerwärmung per Laser
Automatisiertes Hochleistungsauftragschweißen
Um 400 Prozent höhere Prozessgeschwindigkeiten für das Auftragen von Verschleiß- und Korrosionsschutzschichten auf große Bauteile haben sich das Laser Zentrum Hannover und drei Industriepartner zum Ziel gesetzt. In dem KMU-Projekt ›HoDopp‹ entwickeln sie dazu eine absolut neuartige Prozesskombination von nicht-übertragenem Lichtbogen und gezielter laserbasierter Bauteilerwärmung. Die hohe Reinheit des aufgeschweißten Materials soll bereits in der ersten Schicht einen ausreichenden Schutz des Bauteils gewährleisten.
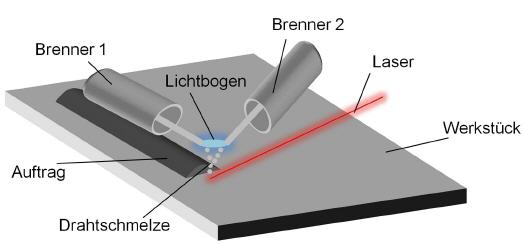
Beim derzeit eingesetzten MSG-Auftragschweißverfahren schmilzt ein Lichtbogenplasma Drahtelektrode und Werkstück gleichzeitig auf. Dabei liegt der Aufmischungsgrad der Materialien bei 30 Prozent, sodass der Beschichtungsprozess bis zu dreimal wiederholt werden muss, um eine ausreichende Qualität der Schutzschicht zu erreichen. Bei maximalen Auftragraten von nur 5 kg/h dauert das Beschichten eines Quadratmeters mit dieser Technik bis zu 24 Stunden und erzeugt hohe Energie- wie Personalkosten.
Mit dem im Juni 2012 gestarteten Projekt HoDopp wollen die Entwicklungspartner vierfach höhere Auftragraten von bis zu 20 kg/h bei gleichzeitiger Reduzierung der Einschweißtiefe sowie Aufmischungen < 5 Prozent erreichen, sodass nur eine einzige Schicht aufgetragen werden muss. Dies will man durch eine Entkopplung der Einbrandsteuerung vom Aufschmelzen des Drahtwerkstoffes erreichen und so Produktivität sowie Qualität des Schweißverfahrens erheblich steigern.
Zur Umsetzung dieser ehrgeizigen Ziele werden zwei Einzelverfahren auf vollkommen neue Weise verknüpft: Im süddeutschen Unternehmen MERKLE Schweißanlagen-Technik wird ein modifiziertes MSG-Auftragschweißverfahren optimiert, bei dem der eingesetzte Lichtbogen ohne Kontakt zum Werkstück zwischen zwei Elektroden brennt. Über eine Anpassung von Düsenform und Brennerstellung sowie durch Verminderung der Schutzgasmenge wird ein stabiler und spritzerfreier Prozess angestrebt.
In der Abteilung Werkstoff- und Prozesstechnik am LZH arbeitet man am zweiten Prozessschritt: Ein Diodenlaser der neuesten Generation mit schwacher Leistung < 0,5 kW soll für einen geringen wie homogenen Einbrand am Werkstück sorgen. Der Laser fokussiert auf das Bauteil kurz bevor die Schmelze der beiden Drähte auftrifft und führt zum Anschmelzen der Werkstückrandschicht. Eine Ablenkvorrichtung steuert dabei die Temperaturverteilung.
Für Jörg Hermsdorf, Gruppenleiter Maschinen und Steuerungen, ist die Verknüpfung der Einzelprozesse ideal: „Beide Werkzeuge können in der Kombination ihre Stärken voll ausspielen. Für das Aufschmelzen des Auftragmaterials wird viel Energie benötig, welche der Lichtbogen zur Verfügung stellt. Der Laser hingegen arbeitet mit geringer Leistung gezielt und gesteuert ausschließlich zur Erzeugung einer homogenen Anbindung des Auftragmaterials.“
Durch die Kombination aus innovativem Lichtbogenverfahren und preiswerter Diodenlasertechnik rechnen die Projektpartner damit, die Bearbeitungszeit auf nur 6 h/qm reduzieren und das Auftragschweißen besonders für große Flächen ab 1 x 2m deutlich rentabler gestalten zu können. Kostengünstig und weniger zeitintensiv bei gesteigerter Qualität – diese Faktoren machen das innovative Verfahren für viele Anwendungsbereiche interessant. Neben dem klassischen Werkzeug- und Formenbau der Automobilindustrie seien beispielhaft das Aufpanzern von Wellen, Walzen und Aufspannflächen, das Reparaturschweißen an beschädigten Flurförderzeugen oder das Auftragen abriebfester Schichten an stark beanspruchten Stellen von Ölbohrgestängen genannt.
Mehr Informationen zum Laser Zentrum Hannover e.V:
![]() |
Laser Zentrum Hannover e.V. (LZH) |
![]() |
Hollerithallee 8 |
![]() |
30419 Hannover |
![]() |
Tel.: +49 511 2788-151 |
![]() |
Fax: +49 511 2788-100 |
![]() |
E-Mail: info@lzh.de |
![]() |
www.lzh.de |
War dieser Artikel für Sie hilfreich?
![]() |
![]() |
![]() |
![]() |
![]() |
Bitte bewerten Sie diese Seite durch Klick auf die Symbole.
Zugriffe heute: 3 - gesamt: 7043.