Parmaco: schnell zum MIM-Bauteil
Präzise, kostengünstig, belastbar
Das Metal Injection Molding (MIM-Verfahren) ermöglicht die Herstellung kleiner, komplex geformter Präzisionsbauteile aus hochfesten Stählen oder Edelstählen in mittleren bis hohen Stückzahlen. Dabei werden Metallpulver-Binder-Gemische im Spritzgießverfahren zu Bauteilen geformt und anschließend gesintert. Diese können komplexe Geometrien aufweisen und sind hoch belastbar. Die Herstellung der metallischen Formen erforderte bisher jedoch Vorlaufzeiten von mehreren Monaten. Dank neuer Lösungen im Bereich Prototypformen sinkt dies für Kleinstserien künftig auf wenige Tage.
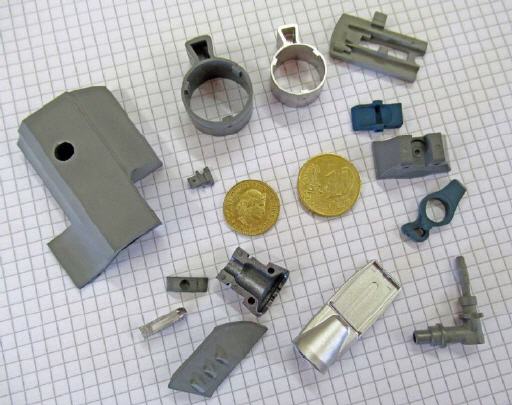
„Mit dem MIM-Verfahren stellen wir kleine, hochfeste und geometrisch anspruchsvolle Teile aus Stahl oder Edelstahl in Serie her“, erläutert Georg Breitenmoser, Geschäftsführer der Parmaco AG in Fischingen (Schweiz). Dazu wird eine fließfähige Mischung aus feinen Metallpulvern mit Zugaben von Bindemitteln und Additiven hergestellt und mithilfe einer Kunststoff-Spritzgießmaschine unter hohem Druck in eine Stahlform gespritzt. Dabei entsteht ein noch weicher „Grünling“, der anschließend entbindert und bei hoher Temperatur zu einem nahezu porenfreien Bauteil gesintert wird.
Dabei entstehen hoch belastbare, geometrisch und funktionell anspruchsvolle Bauteile mit sehr guter Oberflächenqualität. Darstellbar sind Längenabmessungen bis zu etwa 70 mm und Gewichte zwischen 1 und 100 g, beim Mikro-MIM-Verfahren sind bis zu 0,01 g möglich. Am Markt muss sich MIM gegen eine Reihe konkurrierender Verfahren wie Druckgießen, Feingießen, 3D-Druck, pulvermetallurgische Sinterpresslinge oder die Zerspanung aus dem Vollen behaupten.
Überzeugende Vorteile
„Innerhalb dieses Wettbewerbsumfelds zeichnet sich das MIM-Verfahren durch Vorteile aus, die es für bestimmte Anwendungsbereiche und Randbedingungen zur bestmöglichen Lösung machen“, ergänzt G. Breitenmoser. Dazu gehört unter anderem der hohe gestalterische Freiheitsgrad des Spritzgießverfahrens. Dies ermöglicht die Herstellung sehr komplexer und filigraner Geometrien mit Hinterschneidungen. Die Abbildungsgenauigkeit sowie die Oberflächenqualität lägen weit über derjenigen der 3D-Druckverfahren und überträfen mit Leichtigkeit selbst die von Feinguss.
Im Vergleich zu 3D-Druckverfahren erziele man beim MIM-Verfahren zudem deutlich engere Eigenschaftstoleranzen. Die mechanischen Eigenschaften entsprechen weitgehend denen von Komponenten, die aus dem Vollen gefräst wurden. Die Teile können mechanisch bearbeitet, wärmebehandelt, gehärtet, vergütet und mit allen gängigen Oberflächenbeschichtungsverfahren veredelt werden. Auch sind MIM-Teile selbst bei hohen Drücken gas- und flüssigkeitsdicht.
Die Anwendungsgebiete sind äußerst vielfältig und reichen vom Maschinenbau und der Mechatronik über die Kfz-Herstellung und die Schloss- und Beschlagindustrie bis zur Medizintechnik. Besondere Domäne sind auch Werkstoffe, die selten, schwer herstellbar oder sehr teuer sind. Zudem erfüllt der MIM-Prozess auch die höchsten heute in der Industrie geforderten Qualitätsvorschriften beispielsweise aus den Bereichen Automobil, Medizintechnik oder Luft- und Raumfahrt.
Entwicklungspartnerschaft im Vordergrund
„Bei der Entwicklung von MIM-Anwendungen ist eine möglichst frühzeitige Zusammenarbeit mit den Konstrukteuren des Kunden von besonderem Nutzen“, weiß G. Breitenmoser. Bei der Konzeption eines Bauteils berücksichtige der Konstrukteur häufig noch nicht die Besonderheiten und Restriktionen der verschiedenen möglichen Herstellprozesse. Das Ergebnis seien häufig Geometrien, die mit dem ins Auge gefassten Herstellprozess nicht harmonierten, beispielsweise bezüglich Materialanhäufungen, Wanddickenübergängen, Fließwegen bei der Formfüllung, Kantenradien etc.
Deshalb sei es sinnvoll, wenn die Prozesserfahrung des Zulieferers schon möglichst frühzeitig im Verlauf der Entwicklung mit in das Design einfließe. Die hohe Gestaltungsfreiheit des Spritzgießens ermöglicht es, belastungsoptimierte Strukturen mit Freiformflächen sowie Verrippungen oder Bohrungen zu erzeugen und so Materialverbrauch, Kosten und Gewicht zu minimieren. Zudem lassen sich oft Zusatzfunktionen gleich mit ins Bauteil integrieren, wodurch Montageaufwendungen entfallen.
Selbst Gewindebohrungen können direkt im Verlauf des Formgebungsprozesses erzeugt werden. Die optimale Nutzbarmachung dieser Möglichkeiten setzt jedoch die genaue Kenntnis der Möglichkeiten und Grenzen des Herstellprozesses voraus. Aus diesem Grund lege Parmaco großen Wert auf eine enge Zusammenarbeit bereits zu Beginn der Entwurfsphase und bringe sich hier mit seinen erfahrenen Mitarbeitern partnerschaftlich ein. In diesem Zusammenhang benötige man häufig voll funktionsfähige Prototypen für Tests.
Da man bisher jedoch MIM-Teile nur mithilfe aufwendiger Metallformen herstellen konnte, bedingte dies nicht nur hohe Kosten, sondern darüber hinaus auch lange Wartezeiten von typischerweise acht Wochen oder mehr. Entwicklungsprojekte stehen jedoch heutzutage aufgrund des Zwangs, mit neuen Produkten möglichst frühzeitig auf den Markt zu kommen, unter enormem Zeitdruck. Mit dem Spezialdienstleister Injex könne man diese Lücke jetzt schließen.
Schnelle Prototypen im Spritzgießverfahren
„Als Startup an der ETH Zürich haben wir uns auf die besonders schnelle Herstellung von kleinformatigen Spritzguss-Prototypen spezialisiert“, sagt Oliver Schlatter, Mitgründer und Geschäftsführer der Injex AG. Typische Reaktionszeiten liegen bei zwei bis drei Werktagen, fallweise kann sogar innerhalb von 24 Stunden geliefert werden. Hierfür verfüge man über selbst entwickelte kleinformatige Spritzgießmaschinen mit Formzuhaltekräften von bis zu 10 t.
Hierauf könne man Mikroteile im Gewichtsbereich von 0,01 bis ca. 20 g herstellen. Verarbeitet werden alle handelsüblichen Thermoplaste von Polypropylen bis PEEK, Elastomere und Silikone, sowie weitere kundenspezifische Materialien. Im Laufe der Zeit habe man die Bandbreite auf MIM- sowie auf Ceramic Injection-Molding-(CIM)-Mischungen erweitern können. Zu den Kunden gehörten vor allem Unternehmen der Kunststoffverarbeitung, der Mechatronik, der Uhrenherstellung sowie der Medizintechnik.
Hybridformen aus unterschiedlichen Werkstoffen
„Um die Spritzlinge schnell herstellen zu können, bestehen unsere Prototypformen nicht nur aus Metall, sondern auch aus weiteren Werkstoffen“, setzt O. Schlatter hinzu. Dazu gehören Duroplaste ebenso wie auch Komponenten aus Keramik. Für die formgebenden Konturen kommen häufig 3D-Druckverfahren zum Einsatz. Die auf diese Weise entstehenden Hybridformen bilden die Teile mit der erforderlichen Genauigkeit ab.
Zwar sind sie nicht ganz so hoch belastbar und auch nicht so haltbar wie Ganzmetall-Formen, doch reichen sie dazu aus, bis zu 100 brauchbare Bauteile aus dem Originalwerkstoff und mit dem Originalverfahren herzustellen. Trotz des geringeren Spritzdrucks unterscheiden sich die Prototypen in ihren Eigenschaften kaum noch von Originalteilen. Nicht nur die Abmessungen, sondern auch die mechanischen Eigenschaften der späteren Serienteile werden weitestgehend erreicht.
Prozessablauf
„Ausgangspunkt ist für uns die 3D-CAD-Darstellung des gewünschten Bauteils“, verrät O. Schlatter. Diese wird um produktionstechnisch erforderliche Details wie Fließkanäle, Entformungsschrägen etc. ergänzt. Anschließend wird im 3D-Druckverfahren ein Formeinsatz erzeugt und mit anderen Komponenten zur vollständigen Hybridform ergänzt. Vor dem Einsatz wird meist noch manuell nachgearbeitet, um die Oberflächenqualität zu verbessern bzw. die Abbildungsgenauigkeit zu optimieren.
Hinterschnitte und Kerngeometrien werden ggfs. durch Einlegeteile abgebildet, die nach dem Spritzgießvorgang entfernt werden.
Das Spritzgießen erfolgt mit dem vom Kunden vorgegebenen Material. Hierbei kann es sich um Kunststoffe oder um Feedstock-Mischungen für das MIM- oder das CIM-Verfahren handeln. Der Prozess läuft weitgehend manuell ab, d.h. sowohl der Zusammenbau des Werkzeugs als auch die Entformung des Spritzlings erfolgen von Hand. Nach dem Entfernen des Angusses werden die Teile noch auf Qualität geprüft, gewogen und vermessen.
Bei Parmaco durchlaufen die so erzeugten „Grünlinge“ anschließend die übliche Prozesskette aus Entbindern, Sintern sowie ggfs. zusätzlichen weiteren Fertigungsschritten. Die kurzfristige Verfügbarkeit solcher spritzgegossenen Teile ermöglicht die schnelle Lieferung von Prototypen aus dem Originalmaterial und damit eine erhebliche Verkürzung der Entwicklungszeiten. Zudem könne man dadurch MIM-Bauteile zu konkurrenzfähigen Kosten auch im Bereich von Kleinstserien bis hin zu individuellen Varianten z.B. für die Medizintechnik herstellen.
Besonders attraktiv ist hierbei die Tatsache, dass bei diesen Prototypen bereits das spätere Serien-Herstellungsverfahren zum Einsatz kommt. Somit entsprechen die Prototypen nicht nur maßlich, sondern auch in Bezug auf das Material und dessen Eigenschaften den späteren Serienteilen. Dies kann bei der Prototypenherstellung durch reine Additive-Manufacturing-Verfahren nicht erreicht werden.
Eigenschaftsvergleich
Beim Vergleich von MIM-Bauteilen, die von Parmaco wie üblich durch Spritzgießen und Sintern hergestellt wurden, und solchen, die aus Injex-Werkzeugen erzeugt wurden, zeigten sich gewisse Unterschiede. Mit dem Originalverfahren erreicht Parmaco durchschnittliche Maßabweichungen von 1-19 µm bei einer Streuung zwischen 4-26 µm. Bei MIM-Teilen, die aus Injex-Werkzeugen entstanden, ergaben sich durchschnittliche Maßabweichung von 5-100 µm und Streuungen von 16-52 µm.
Standardmäßig hergestellte MIM-Bauteile von Parmaco erreichten eine Oberflächenrauheit Ra von 1 µm, während solche aus Injex-Werkzeugen bei ca. 2 µm lagen. Die Dichte der aus Injex Komponenten erzeugten MIM-Teile war um etwa 1.3 Prozent geringer.
Auch wenn bei Verwendung von Injex-Werkzeugen die Eigenschaften von Serienteilen somit nicht zu 100 Prozent erreicht werden können, sind die Abweichungen andererseits gering genug, um in vielen Fällen den Einsatz bei Kleinstserien oder Prototypanwendungen zu rechtfertigen, vor allem mit Blick auf die Aspekte Oberflächenrauheit und Vergleichbarkeit des Herstellverfahrens. Hier erwiesen sich Injex-Prototypen solchen, die mithilfe von Additive-Manufacturing-Verfahren wie SLM (Selective Laser Melting) hergestellt wurden, als deutlich überlegen.
Mehr Informationen zu Parmaco:
![]() |
Parmaco Metal Injection Molding AG |
![]() |
Fischingerstrasse 75 |
![]() |
CH - 8376 Fischingen |
![]() |
Tel.: +41-71-978-7878 |
![]() |
E-Mail: info@parmaco.com |
![]() |
www.parmaco.com |
War dieser Artikel für Sie hilfreich?
![]() |
![]() |
![]() |
![]() |
![]() |
Bitte bewerten Sie diese Seite durch Klick auf die Symbole.
Zugriffe heute: 3 - gesamt: 5425.