Punkten bei der Motorenherstellung
Induktives Erwärmungssystem von Emag eldec
Bei der Herstellung von Elektromotoren, setzt Elektror auf die ›Uni Heat‹ von Emag eldec: Das System sorgt für die schnelle und präzise induktive Erwärmung des Statorleergehäuses vor einem Fügeprozess mit der Motorwicklung.
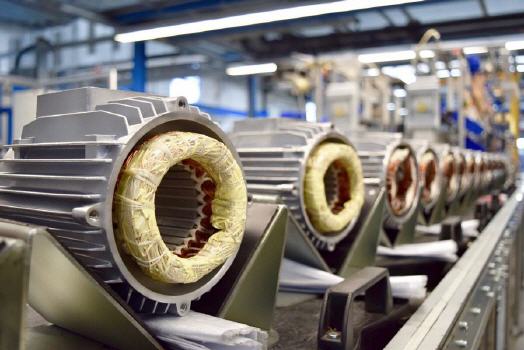
Luft ist ein unverzichtbares Arbeitsmedium in der industriellen Produktion: Mit ihrer Hilfe werden zum Beispiel überschüssige Feuchtigkeit oder Staub abgesaugt, erhitzte Werkstoffe gekühlt, auftretende Gase und Dämpfe abtransportiert oder Feststoffe per Luftstrom gefördert. Dabei bilden Ventilatoren nicht nur so etwas wie das Herzstück der dazugehörigen Lufttechnik-Anlage, sondern sie sind zudem auch extremen Belastungen ausgesetzt und müssen häufig jahrzehntelang ihren Dienst verrichten – ein Bündel von Herausforderungen, dem sich Elektror airsystems seit Jahrzehnten stellt.
Das Unternehmen mit Stammsitz in Ostfildern sowie zwei Produktionsstandorten in Waghäusel und Chorzów (Polen) stellt pro Jahr rund 60.000 Industrieventilatoren und Seitenkanalverdichter her. Es handelt sich häufig um individuelle Lösungen, die sich zum Beispiel durch ein präzises Druckniveau, widerstandsfähige Werkstoffe oder eine besonders schwingungsarme Bauweise auszeichnen. Bei der Konstruktion eines Ventilators gibt es letztlich unzählige Anpassungsmöglichkeiten – und das gilt selbstverständlich auch für die Elektroantriebe der Geräte. Deshalb entstehen bei Elektror unterschiedlich große und leistungsstarke Motoren. Ihre Komponenten werden je nach Auftrag konfiguriert und im Rahmen eines schlanken Prozesses montiert. Dabei legen die Lufttechnik-Spezialisten höchsten Wert auf Prozesssicherheit. Die Fehlertoleranz beträgt immer „null“.
Induktive Erwärmung im Zentrum
Einer der zentralen Prozesse ist in diesem Zusammenhang das thermische Fügen von Statorleergehäuse und Motorwicklung: Das Gehäuse wird per induktivem Erwärmungssystem auf eine Temperatur von 280 bis 300 Grad Celsius erhitzt. Dabei weitet es sich und die Motorwicklung lässt sich einfach per Hand einsetzen. Während des Erkaltens zieht sich das Gehäuse wieder zusammen und bildet mit der Wicklung eine formschlüssige und feste Verbindung. Im Jahr 2018 haben sich die Spezialisten dazu entschieden, das veraltete Erwärmungssystem auszutauschen. Wie kam es dazu? „Eines unserer Hauptziele bei dieser Investitionsentscheidung war es, die Prozesssicherheit rund um das induktive Erwärmen zu erhöhen.
Das alte System zeigte zum Beispiel nicht an, welche Bearbeitungstemperatur tatsächlich am Bauteil erreicht wurde. Das führte teilweise zu längeren Durchlaufzeiten beim anschließenden Fügen. Außerdem war die Ersatzteilversorgung nicht gesichert“, erklärt Roland Sand, Gruppenleiter Produktion bei Elektror. „Wir waren deshalb auf der Suche nach einem System, das für sehr präzise Temperaturen bei der Erwärmung sorgt, unkompliziert für jeden Bediener zu handhaben ist und dessen Prozesse durchgängig sicher ablaufen. Außerdem wollten wir einen Lieferanten aus der Region, der im Servicefall direkt zur Stelle ist. Diese Anforderungen erfüllt EMAG eldec mit seiner UNI-HEAT-Technologie.“
Einfacher und sicherer Prozess
Insgesamt vollzieht sich jetzt ein sehr sicherer und zugleich schneller Arbeitsablauf bei Elektror rund um das individuell entwickelte UNI-HEAT-System: Der Bediener ergreift mit Schutzhandschuhen das Leergehäuse, setzt es in einen passgenauen Werkstückträger und schiebt diesen in das Innere der Anlage. Mit dem Schließen einer Schiebetür startet er den weiteren Prozess: Das Bauteil bewegt sich nach oben in seine Grundposition, dabei „taucht“ der Stabinduktor in die leere Gehäusehülle ein. Der anschließende Erwärmprozess dauert je nach Bauteilgröße nur 30 bis 120 Sekunden. Nach Abschluss signalisiert eine Warnleuchte, dass der Bediener das Bauteil wieder entnehmen kann. Er setzt es in eine Schablone, die auf dem Abkühlplatz bereitsteht, und schiebt die Motorwicklung von oben hinein. Nach kurzem Abkühlungsprozess ist der Motor fertig „verheiratet“ und landet auf einem Förderband zur weiteren Verarbeitung.
„Wir produzieren auf diese Weise rund 250 Motoren am Tag“, sagt Steffen Müller von der Qualitätssicherung bei Elektror. „Die Bauteilgrößen wechseln dabei regelmäßig. Trotzdem erfolgt der Prozess völlig stabil. Es treten überhaupt keine Probleme oder Fehler auf.“ Dafür verantwortlich ist nicht zuletzt die einfache Umrüstung der Anlage im Fall eines Bauteilwechsels: Der Bediener schließt die Wasserversorgung, löst zwei Schrauben an der Induktorhalterung und kann anschließend das Werkzeug abziehen beziehungsweise ein neues aufstecken. Der Werkstückhalter ist sogar nur aufgesetzt, lässt sich einfach aus der Halterung entfernen und austauschen. „Inklusive des Programmwechsels über das Steuermodul dauert der ganze Umrüstprozess nur rund eine Minute. Diverse Sicherheitsmaßnahmen verhindern eine Fehlbedienung“, sagt Müller.
Individuelle Entwicklungslösung für Elektror
Eine entscheidende Rolle für die Qualität, Sicherheit und Effizienz dieses induktiven Erwärmungsprozesses spielt die Entwicklung bei EMAG eldec: Die Induktionsspezialisten verantworten Gesamtlösungen, zu denen auch der passende Generator und die benötigten Induktoren gehören. Für die Entwicklung dieser Kernelemente eines Erwärmungsprozesses ist EMAG eldec ideal aufgestellt: Zum einen entsteht am Standort in Dornstätten eine große Bandbreite von Generatoren mit hohem Wirkungsgrad und präziser Energiedosierung. Zum anderen produzieren die Spezialisten bis zu 1.000 Induktoren pro Jahr. Ihre Produktion erfolgt im Rahmen eines anspruchsvollen Manufakturprozesses, bei dem es auf viele hochgenaue Details ankommt.
Entscheidend ist dabei zum Beispiel, wie tief und an welchen Stellen die Wärme in das Bauteil eindringen soll. Das beeinflusst die Geometrie des Induktors und die Ausstattung des Generators. Darüber hinaus setzt EMAG eldec im Vorfeld unter anderem auf eine umfangreiche Simulation des Prozesses und den Einsatz von Wärmebildkameras. Abschließend wird jede fertige UNI-HEAT-Gesamtlösung am echten Bauteil getestet und dem Kunden bei einer Abnahme in Dornstetten vorgeführt. „Seit dem Produktionsstart im Mai 2018 gab es überhaupt keine Störungen“, fasst Roland Sand abschließend zusammen. „Minimale Startprobleme hat der eldec Service schnell behoben. Wir sehen unsere Erwartungen an diese Investitionsentscheidung rundum bestätigt.“
Mehr Informationen zu Emag:
![]() |
Emag Gmbh & Co. KG |
![]() |
Austraße 24 |
![]() |
73084 Salach |
![]() |
Telefon 07162 17-0 |
![]() |
Fax 07162 17-199 |
![]() |
E-Mail: communications@emag.com |
![]() |
www.emag.com |
War dieser Artikel für Sie hilfreich?
![]() |
![]() |
![]() |
![]() |
![]() |
Bitte bewerten Sie diese Seite durch Klick auf die Symbole.
Zugriffe heute: 3 - gesamt: 4790.