MMC-Werkzeuge zeigen ihr Potenzial
Einsatz bei Karl Walter Formen- und Kokillenbau
Beim Gießen von – heute meist lackierten – Autorädern sind makellose Oberflächen ein absolutes Muss. Karl Walter Formen- und Kokillenbau hat auf MMC Hitachi Tool umgestellt und fräst nun prozesssicher so gute Oberflächen, dass sich in Göppingen der Aufwand für das manuelle Einschleifen signifikant reduziert hat.
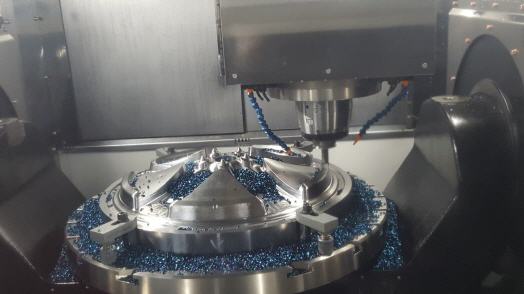
Im Gegensatz zu komplexen Druckgusswerkzeugen sind Niederdruckwerkzeuge – auch Kokillen genannt – einfacher aufgebaut. Doch ein Punkt ist beim Gießen von Autorädern ein absolutes Muss: Alle Sichtbereiche müssen eine makellose Oberfläche aufweisen. Denn Aluräder sind heute ausnahmslos lackiert, da ist schon der kleinste Kratzer ein absolutes No-Go. Ein Rad muss also so aus dem Werkzeug herauskommen, dass es geometrisch und von der Oberfläche her perfekt ist.
Denn nach der Entnahme aus dem Werkzeug wird nur noch entgratet und die Löcher für die Schrauben gebohrt. Deshalb schließt sich nach dem Fräsen noch eine zeitaufwendige Phase der Handarbeit an. „Für das manuelle Einschleifen der Oberflächen benötigte ein erfahrener Mitarbeiter pro Kokille bisher durchschnittlich 20 Arbeitsstunden. Bei 150 Komplettwerkzeugen, die wir zurzeit pro Jahr ausliefern, sind dies dreitausend Stunden“, rechnet Dr. Jens Buchert, Geschäftsführer von Karl Walter Formen- und Kokillenbau, vor. „Also zwei Mitarbeiter, die tagtäglich nur die Werkzeuge verschleifen. Gute, erfahrene Mitarbeiter sind hierfür aber äußerst schwer zu bekommen.„
Die primäre Aufgabe war deswegen, einen Prozess zu entwickeln, der beim Fräsen deutlich bessere Oberflächen erzeugt. In diesem Rahmen präsentierte MMC Hitachi Tool in Göppingen das für den Fräsbereich entwickelte Optimierungskonzept ‚Production 50‘. Dabei handelt es sich um eine neun Punkte umfassende Vorgehensweise, bei der es im Wesentlichen darum geht, nach genauer Analyse des Ist-Zustandes unter Austausch mit allen Beteiligten einen alternativen Fertigungsprozess – der auch eine Wirtschaftlichkeitsberechnung umfasst – zu erarbeiten und diesen in die Praxis umzusetzen.
Anhand eines Projektbauteils – ein Werkzeug für ein 21-Zoll-Aluminiumrad eines namhaften Radherstellers mit einem Durchmesser von 628 mm – sollte schließlich ein erster Test erfolgen. Die Herausforderung war hier der Werkstoff, ein Warmarbeitsstahl, der nicht einfach zu zerspanen ist. Dabei handelte es sich um 1.2367 (X38CrMoV5-3), der bei Karl Walter Formen- und Kokillenbau für die Kokillen fast ausschließlich zum Einsatz kommt. Mit 38 HRC ist dieser Edelstahl zwar nicht besonders hart, aber wegen seiner Zähigkeit nur sehr schwer zu zerspanen.
Dieser Werkstoff wird deshalb gerne verwendet, weil sich diese verzugsarme Legierung bei Wärme äußerst verschleißfest zeigt. Denn das Werkzeug ist bei der Räderproduktion einer hohen thermischen Belastung ausgesetzt. Vorgeheizt wird die Kokille um die 350 bis 400 °C, dann fließt 750 °C heißes Aluminium hinein. Man kühlt, und dann heizt man wieder – deshalb ist der Werkstoff sehr hoch legiert. Ein weiteres Merkmal ist, dass die Werkzeuge teilweise sehr tiefe Speichen abbilden müssen, gepaart mit kleinen Radien.
Die Aufgabe lautete nun, einen Zerspanprozess für dieses Werkzeug zu entwickeln, mit dem sich die Oberflächenqualität trotz der beschriebenen Widrigkeiten stark verbessert. Zum einen sollte sich der manuelle Polieraufwand, und zum anderen möglichst auch die Fräsbearbeitungszeit messbar reduzieren. Die Vorschläge, die MMC Hitachi Tool wenige Tage später in Göppingen präsentierte, überzeugten sowohl Jens Buchert als auch die Kollegen der CAM-Abteilung und die an den Fräsmaschinen.
Die praktische Umsetzung fand in Form von diversen Testreihen statt. So wurde zum Ende hin das gesamte Material des Werkstücks mit jeweils einem 3-schneidigen Wendeplattenfräser mit 12 und 20 mm Durchmesser geschruppt. Das Vorschlichten und Fertigschlichten übernahmen dann, wie bisher bereits, Kugelfräser, die nun aber von MMC Hitachi Tool stammten. Und zwar beim Vorschlichten zwei konische EPBPN-Kugelfräser mit den Durchmessern 4 und 8 mm, fertig geschlichtet wurde dann mit einem einzigen Kugelfräser mit Durchmesser 4 mm, ebenfalls vom Typ EPBPN.
Bisher ist beim Schruppen bei Karl Walter Formen- und Kokillenbau mit Wendeplatten und mit Vollhartmetall gearbeitet worden. Der Schruppprozess war dabei relativ langsam, wohingegen die Schlichtbearbeitungszeit durch große Tiefenzustellungen und den Einsatz mehrerer Werkzeuge kompensiert werden sollte. Der Fokus lag auf dem zentralen Kundenbedürfnis der verbesserten Oberflächengüte, darauf wurde der gesamte Bearbeitungsprozess ausgelegt.
Der Schruppprozess wurde dabei deutlich verkürzt und der Werkzeugeinsatz fast ausschließlich auf Wendeplattenwerkzeuge begrenzt. Beim finalen Test ist vom ersten bis zum letzten Span mit einem EPBPN-Kugelfräser Durchmesser 4 mm eine durchweg homogene und äußerst hochwertige Oberfläche erzeugt worden. Das Werkzeug von MMC Hitachi Tool benötigte dafür rund 20 Stunden – und zeigte danach keinerlei Verschleiß.
Durch die Umstellung auf MMC Hitachi Tool wurden in Göppingen alle vorgegebenen Ziele erreicht. Gegenüber früher hat sich die Anzahl der benötigten Fräswerkzeuge stark reduziert, was zwar nicht im Forderungskatalog stand, sich aber ebenso angenehm bei den Fertigungskosten bemerkbar machen dürfte wie die gestiegenen Standzeiten. Zwar hat sich der gesamte Fräsprozess durch die längere Zeit, die man nun zum Feinschlichten benötigt, um 2,6 Stunden auf insgesamt 37,6 Stunden verlängert.
Dem steht aber eine gut dreimal höhere Oberflächengüte gegenüber. Wurde bisher ein Mittenrauwert von Ra 3,25 μm erreicht, fräst man jetzt Ra 1,0 μm und damit eine so hervorragende Oberflächengüte, dass Riefen mit bloßem Auge nicht mehr erkennbar sind. „Die Oberflächenqualität, die nach dem anschließenden manuellen Einschleifen erzielt wird, hat im Vergleich zu früher nochmals zugelegt, obwohl wir dafür jetzt nur noch etwa 15 Stunden und damit rund 25 Prozent weniger Zeit benötigen.
So lässt sich die wertvolle Mitarbeiterkapazität für andere Aufgaben nutzen“, zieht Dr. Jens Buchert ein positives Fazit. „Bei leicht gesunkener Gesamtbearbeitungszeit erreichen wir heute eine signifikant bessere Oberfläche – und das war das Ziel. So können wir unseren Kunden sagen, sie bekommen für den gleichen Preis ein Werkzeug in noch höherer Qualität.“
Mehr Information zu Hitachi Tool:
![]() |
Hitachi Tool Engineering Europe GmbH |
![]() |
Itterpark 12 |
![]() |
40724 Hilden |
![]() |
Tel.: +49 (0) 21 03 - 24 82-0 |
![]() |
Fax: +49 (0) 21 03 - 24 82-30 |
![]() |
E-Mail: info@hitachitool-eu.com |
![]() |
www.hitachitool-eu.com |
War dieser Artikel für Sie hilfreich?
![]() |
![]() |
![]() |
![]() |
![]() |
Bitte bewerten Sie diese Seite durch Klick auf die Symbole.
Zugriffe heute: 3 - gesamt: 4964.