»Zufriedene Kunden sind für uns das Wichtigste«
Interview mit Markus Kluge, TL von Dr. Tretter
Die vielseitig einsetzbaren Toleranzhülsen, die Dr. Tretter auf Messen als Falldämpfer präsentiert, stellen eine wirtschaftliche Alternative zu herkömmlichen Lösung dar. Was es damit auf sich hat und wie Dr. TRETTER seine Kunden umfassend unterstützt, erzählt Markus Kluge, Technischer Leiter bei dem schwäbischen Hersteller.
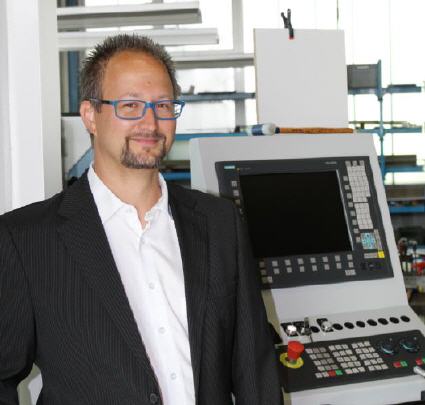
Herr Kluge, auf der Motek 2018 hat Dr. TRETTER einen Schwerpunkt unter anderem auf die vielseitig einsetzbaren Toleranzhülsen gelegt. Was macht diese Maschinenelemente so besonders?
Markus Kluge: Toleranzhülsen lassen sich als kraftschlüssige Verbindungselemente vielseitig einsetzen, und einmal erstellte Verbindungen können im Gegensatz zum Pressen oder Kleben wieder gelöst werden. Dies gilt auch für die Drehmomentübertragung – ganz anders als zum Beispiel bei der Keil- und Presspassung. Setze ich eine Passfeder ein, muss sowohl in der Welle als auch in der Nabe eine Nut eingebracht werden. Das macht die Herstellung teurer. Was die Toleranzhülsen aber ganz besonders auszeichnet: Sie können eine festgelegte Vorspannkraft in radialer Richtung aufbringen. Damit übertragen die Toleranzhülsen über eine definierte Reibung Kräfte. Das haben wir auf der Motek in einer speziellen Anwendung gezeigt.
In dieser Anwendung war die Toleranzhülse auf der Motek als Falldämpfer in Absturzsicherungssystemen zu sehen, die unter anderem Industriekletterer oder Dachdecker einsetzen. Können Sie die Funktion des Bauteils erklären, und warum eignet es sich so gut für diese Aufgabe?
Markus Kluge: In der Regel ist in einem Absturzsicherungssystem ein mehrlagig vernähtes Band als Falldämpfer verbaut. Kommt es zum Absturz, reißen die Nähte auf und bremsen den Fall ab. Weil sich das Band danach nicht wieder verwenden lässt, muss der Betreiber den kompletten Bandfalldämpfer tauschen. Das ist aufwendig und teuer. Mit diesem Problem kam ein Hersteller auf uns zu. Wir haben für diese Anwendung nun eine deutlich effizientere Lösung mit einer Toleranzhülse entwickelt. Beim Sturz gibt diese erst nach und bremst dann über die Reibung den Fall ab. Nach einmaligem Gebrauch muss die Toleranzhülse mit dem zugehörigen Einbauteil zwar auch gewechselt werden, doch das ist deutlich einfacher und preiswerter. Die Kosten für eine Toleranzhülse bewegen sich bei diesem Anwendungsfall gerade mal um die 1,20 Euro.
Können Sie andere typische Anwendungen nennen, in denen Toleranzhülsen zum Einsatz kommen?
Markus Kluge: Toleranzhülsen lösen Herausforderungen, die sich im Zusammenhang mit Mittenversatz, Zentrierung, Schwingungen, Temperaturausdehnung, zu großen Toleranzen der Anschlusskomponenten oder auch der Drehmomentbegrenzung ergeben. Einfache Einsatzfälle ohne definierte Kraftübertragung sind unter anderem Befestigungen von Bediengriffen sowie von Armlehnen- und Federrohren bei Sitzmöbeln. Spielt die definierte Kraftübertragung eine Rolle, sind Toleranzhülsen auch in der Antriebstechnik bei Riemenscheiben, Schwung- oder Zahnrädern verbaut. Auch in dem Bereich der Automobilindustrie werden sie eingesetzt. Beispielsweise zentriert die Toleranzhülse in einem Elektromotor einen Stator im Gehäuse und fixiert diesen gegenüber den Drehmomentkräften des Rotors. In der Regel werden beide Komponenten verklebt und nochmal nachbearbeitet. Mit der Toleranzhülse muss der Stator nur noch eingepresst werden. Das sorgt für eine deutlich schnellere Montage und eine einfachere Wartung.
Wie ist die Resonanz auf diese Bauteile?
Markus Kluge: Aktuell erfreuen sich Toleranzhülsen steigender Beliebtheit. Trotzdem sind sie in vielen Bereichen noch völlig unbekannt. Um das zu ändern, gehen unsere Außendienstmitarbeiter aktiv auf die Kunden zu. Dazu gehören insbesondere Hersteller von Elektromotoren. Hier sprechen wir vor allem die Konstruktionsabteilungen an und stehen beratend zur Seite. Die größte Resonanz erfahren wir über unseren Internet-Auftritt, wenn der Konstrukteur nach einer Problemlösung sucht und dann auf unser besonderes Bauteil stößt.
Welche Rolle spielt der Servicegedanke bei Dr. TRETTER? Wie schaffen Sie es, Kunden bestmöglich zu unterstützen?
Markus Kluge: Zufriedene Kunden sind für uns das Wichtigste. Um das zu erreichen, liefern wir ihnen nicht nur hochwertige Komponenten, sondern beraten die Anwender auch umfassend. Das fängt schon bei der Konstruktion an. Eine Herausforderung bei den Toleranzhülsen ist zum Beispiel immer wieder die Einbausituation. Auf unserer Internetseite stellen wir unseren Kunden zudem ein Formular bereit, das sie bei den erforderlichen Berechnungen unterstützt. Und natürlich sind wir jederzeit ein zuverlässiger Ansprechpartner und helfen unseren Kunden aus – sei es in der Testphase oder anschließend bei der Umsetzung in die Serie.
Zu Ihrem umfassenden Dienstleistungs-Programm gehört auch die Bearbeitung von Wellen, die in Lineareinheiten verbaut sind. Wie wird dieser Service angenommen?
Markus Kluge: Sehr gut. Wir bearbeiten gehärtete Wellen schon seit den 1990er Jahren. Weil es jedoch immer weniger Hersteller gibt, die diese Dienstleistung auch bei geringen Stückzahlen zu entsprechend günstigen Preisen anbieten, haben wir uns in den vergangenen vier Jahren darauf fokussiert. Die Kunden nehmen diesen Service dankbar an, die Auslastung ist hoch, und wir verzeichnen zweistellige Umsatzzuwächse.
Unser Ausgangsmaterial sind bis zu 65 Rockwell gehärtete und geschliffene Stahlwellen. Je nach Kundenwunsch bearbeiten wir die Enden entsprechend. Die Maximallänge, die wir fertigen, liegt bei sechs Metern. Mit Stoßverbindungen können die Anwender die Wellen beliebig über die sechs Meter hinaus zusammensetzen. Unsere Expertise liegt vor allem in der kostengünstigen Bearbeitung kleiner und mittlerer Stückzahlen. Besonders wissen es unsere Kunden zu schätzen, dass wir auch bei Kleinststückzahlen und Einzelteilen eine zeitnahe Bearbeitung der Wellen anbieten können. Dazu stehen uns acht hochflexible Dreh- und drei Fräsmaschinen zur Verfügung. Seit etwa zwei Jahren setzen wir für etwas größere Stückzahlen ein Dreh-Fräszentrum mit Stangenlager ein, auf dem wir Bauteile mit Längen von 600 und Durchmessern bis 40 Millimetern zu sehr wettbewerbsfähigen Stückzahlen fertigen können.
Mit welchen Lieferzeiten kann der Anwender rechnen?
Markus Kluge: Aktuell beträgt die Lieferzeit etwa vier bis sechs Wochen. Unser Ziel liegt allerdings bei zwei Wochen. Das ist natürlich immer auch abhängig von der Stückzahl. Dazu planen wir, unsere Kapazitäten um eine weitere Drehmaschine zu erweitern.
Wie wichtig ist eine Messe wie die Motek für Dr. TRETTER?
Markus Kluge: Die Motek ist unsere Hauptmesse. Und mit dem Standort Stuttgart liegt sie mitten in unserem Einzugsgebiet. Die meisten Anwender unserer Produkte, insbesondere im Bereich der Lineartechnik, sitzen rund um die Landeshauptstadt – oder zumindest in Baden-Württemberg. Dies hat natürlich auch damit zu tun, dass die mittelständischen Sondermaschinenbauer hier in der Region sehr stark sind. Auf der Motek treffen wir auf Bestandskunden, stoßen aber auch auf viele potenzielle Kunden. Begeistert bin ich von der Qualität der Gespräche, häufig zum Thema Toleranzhülsen. Daraus ergeben sich oft neue Kontakte. Das Spannende ist: Gerade bei diesen Komponenten kommen die interessierten Anfragen aus ganz unterschiedlichen Branchen. Aktuell zum Beispiel von Herstellern von Elektromotoren und Unternehmen aus der Elektromobilität, einer Branche, die sehr stark im Kommen ist.
Mehr Informationen zur Dr. Tretter GmbH+Co.:
![]() |
Dr. Erich TRETTER GmbH + Co. |
![]() |
Am Desenbach 10 + 12 |
![]() |
73098 Rechberghausen |
![]() |
Telefon: +49 7161 95334-0 |
![]() |
Telefax: +49 7161 51096 |
![]() |
E-Mail: info@tretter.de |
![]() |
www.tretter.de |
War dieser Artikel für Sie hilfreich?
![]() |
![]() |
![]() |
![]() |
![]() |
Bitte bewerten Sie diese Seite durch Klick auf die Symbole.
Zugriffe heute: 3 - gesamt: 5564.