Mühelose Kleinteilefertigung
Das Zusammenspiel ist entscheidend
In rasanter Entwicklung wird Präzision immer genauer definiert und gefordert. Hightech-Branchen wie Feinmechanik, Uhrenindustrie, Elektro- und Medizintechnik müssen Drehteile innerhalb µm- genauer Toleranzen in Durchmesser und Rundlauf mit hervorragender Oberflächengüte fertigen. Um diese Präzision erbringen zu können, muss die gesamte Prozesskette aufeinander abgestimmt sein - von der Materialführung bis hin zur Entnahme des fertigen Teils.
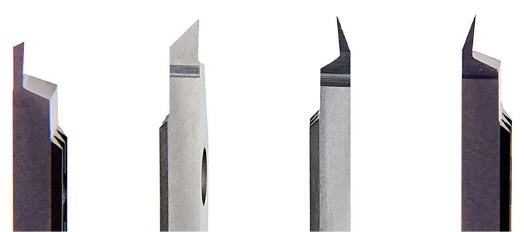
Der ungebrochene Trend zur Minaturisierung stellt hohe Anforderungen an die Präzision. Am Beispiel der Fertigung einer sehr kleinen Welle, mit einer Gesamtlänge von 1,6 mm und Durchmesser 0,8 mm sowie beidseitig mit zwei Ansatzzapfen in Durchmesser 0,25 mm und 0,14 mm und nur wenige zehntel Millimeter lang, lässt sich dies gut demonstrieren. „Um Prozesssicherheit, Reproduzierbarkeit und hohe Oberflächengüte mit extrem kleinen Toleranzen zu gewährleisten, müssen alle Fertigungskomponenten aufeinander abgestimmt sein“, so Jörg Schwartz, Geschäftsführer von Schwartz – tools + more, „da sich sonst selbst kleinste Ungenauigkeiten katastrophal auf das Endergebnis auswirken.“
Präzision beginnt schon mit der Führungsbüchse
Die Auswahl der richtigen Führungsbüchse vermeidet Beschädigungen an der Oberfläche der Materialstange. Hierbei sind verschiedene Faktoren wichtig. Je nach Beschaffenheit des Materials ist eine polierte oder geschliffene Bohrung notwendig. Entgratete Schlitze und verrundete Übergänge in der Bohrung tragen ebenfalls entscheidend zu makellosen Oberflächen bei.
Für die Fertigung der kleinen Welle ist deswegen eine Führungsbüchse mit polierter Bohrung, entgrateten Schlitzen und einer Beschichtung die passende Lösung. Damit gleitet das Material der Welle auch mit dem kleinen Durchmesser sehr gut durch die Führungsbüchse. Die spielfreie Einstellung der Materialstange in der Führungsbüchse ist ein weiterer Faktor, um der hohen Anforderung an den Rundlauf gerecht zu werden. Dabei sollte der Durchmesser der Führungsbüchsenbohrung im Verhältnis zum Materialdurchmesser geringfügig größer gewählt werden, um die gewünschte Kapillarwirkung für die Ölförderung in die Bohrung zu erhalten.
Individuell angepasste Spannzangen
Während der weiteren Bearbeitung werden auch beim Abgreifvorgang hohe Anforderungen an die Zange gestellt. „Jedes Drehteil ist individuell. Die optimale Spannlösung hängt von vielen Faktoren ab. Beim Beispiel der kleinen Welle liegt die besondere Herausforderung in einem sehr hohen Rundlauf sowie einer absolut abdruckfreien Oberfläche. Um dies zu realisieren, wird eine hartmetallbestückte Vorbauzange mit ultrapräziser Rundlaufgenauigkeit (< 5 µm) und polierter Oberfläche verwendet. Der Vorbau unterstützt hier die optimale Kühlmittelzufuhr.
Auch Faktoren wie der Durchmesser, die Beschaffenheit der Abgreifstelle, das Material und der Einsatzzweck des Drehteils haben großen Einfluss auf die Wahl der Spanzange. Oft findet sich zum Beispiel keine optimale Stelle laut Lehrbuch am Drehteil. „Mit standardisierten Sonderlösungen lässt sich das Abgreifen dennoch ohne Qualitätsverlust realisieren“, so Jörg Schwartz. „Dafür haben wir Präzisionsspannzangen mit einer Rundlaufgenauigkeit kleiner 5 µm im Programm, die sich auf die jeweilige Spannsituation individuell, im ‚Baukastensystem‘ anpassen lassen.“
Sollen keine Abdrücke auf dem Material entstehen, kann eine Spannzange mit Verzahnung oder eine hartmetallbestückte Spannzange mit sehr glatter Bohrung die Lösung sein. Eine Spannbohrung aus Kunststoff oder Phenol eignet sich besonders gut für abdruckfreies Spannen sehr empfindlicher Teile. Um ein mögliches Eindringen von Schmutzpartikeln zwischen Material und Zange zu verhindern, bietet sich die Option der extra schmalen Schlitze an.
Gerade bei der Fertigung von kleinen Drehteilen fehlt oft der Platz an der Gegenspindel für eine optimale Bearbeitung. Um Stabilität und Rundlauf zu gewährleisten, sollte das Drehteil so lange als möglich eingespannt sein. Nur so ist ein stabiler Bearbeitungsprozess möglich. Hier hat eine Spannzange mit Vorbau oft Vorteile gegenüber der Standardausführung. Sie gibt dem Werkzeug dank der verjüngten Nase den Platz die Späne gut abzuführen und unterstützt zudem eine punktgenaue Kühlschmierung. Dazu Jörg Schwartz: „Bei der Vorbauzange sollte systembedingt jedoch zu viel Spanndruck auf den Kegel vermieden werden, da sich die Zange verformt. Darunter leidet der Rundlauf enorm.“
Faktor Präzisionswerkzeuge
Ein weiterer einflussgebender Faktor bei der Fertigung kleinster Drehteile sind neben der Spanntechnik hochpräzise Werkzeuge mit sehr scharfen Schneiden. Filigrane Geometrien für feine Schnitte erfordern Schneiden, die beispielsweise nur ein zehntel Millimeter breit sind und einen flachen Spanwinkel von 0° aufweisen. Ein positiver Spanwinkel kann bewirken, dass Werkstücke mit sehr kleinen Durchmessern in die Schneide gezogen und beschädigt werden. „Wendeplattenwerkzeuge mit filigranen Geometrien, speziell für die Mikrobearbeitung, werden daher schon seit Jahren über unsere TOP-Watch Wendeplattenserie abgedeckt,“ so Jörg Schwartz.
Mit diesem umfassenden Programm an standardisierten Geometrien zum Langdrehen im Miniaturbereich bietet Schwartz – tools + more Wendeschneidplatten mit einer vielfältigen Auswahl an Geometrien, Beschichtungen und Hartmetallsorten zum Abstechen, Vorwärtsdrehen, Schlichten und Schruppen sowie zum Rückwärtsdrehen. Zudem finden Anwender auch Geometrien für Zentrums- und Planeinstiche für die Front-, sowie Rückseite. Durch die patentierte Keilverzahnung und die geschliffenen Halter der Serie sitzt die Wendeschneidplatte formschlüssig und extrem stabil sowie rechtwinklig und gerade im Halter. Das Ergebnis: Hohe Prozesssicherheit und Wiederholgenauigkeit.
Um Mikrovibrationen, die durch die hohen Drehzahlen entstehen, entgegenzuwirken, bietet das TOP-Watch-System neben weiteren Haltervarianten den Wendeplattenhalter „Novibra“. Er absorbiert Mikrovibrationen, welche die scharfen feinen Schneiden zerstören können. „Aus diesem Grund ist bei der Fertigung der kleinen Welle der Novibra-Halter erste Wahl. Zudem werden für die Drehoperationen Wendeschneidplatten aus der TOP-Watch-Serie eingesetzt, deren Freiwinkel nach der Beschichtung nochmals überschliffen sind. Das erzeugt extrem scharfe Schneiden ohne Kantenverrundung“, erklärt Jörg Schwartz. Erst diese scharfe Schneide sowie ein extrem geringer Vorschub von 0,004 mm ermöglichen das maßhaltige Drehen von Durchmesser 0,14 mm an der beispielhaften Welle bei einer Drehzahl von 8.000 U/min“, ergänzt Jörg Schwartz.
Exakte Spindelausrichtung
Die exakte Zentrierung der Spindeln und der axialen Werkzeuge zueinander ist ebenfalls ein wichtiger Aspekt für die Mikropräzisionsbearbeitung. Sind die Spindeln nicht gut aufeinander abgestimmt, kann die Oberfläche des Drehteils beim Einführen in die Gegenspindelzange beschädigt werden, und/oder das Drehteil sitzt verspannt in der Zange. Das erzeugt gegebenenfalls Rundlaufprobleme. Bei axial am Drehteil eingebrachten Bohrungen wären Werkzeugbruch oder verlaufende Bohrungen die Folge.
Mit einer Messuhr ist das Zentrieren oft sehr zeitaufwendig sowie stark vom Wissen und der Routine des Anwenders abhängig. Die Alternative von Schwartz – tools + more ist das berührungslose Zentriergerät MOWIDEC-TT mit Digitalanzeige. Dazu Jörg Schwartz: „Hiermit müssen Unternehmen keine Kompromisse in punkto Präzision eingehen. Mit dem Zentriergerät kann der Anwender Haupt-, Gegen- und Werkzeugspindeln einfach, schnell und präzise ausrichten – und dies mit einer Messgenauigkeit von 2 µm. Dank der simplen Handhabung kann jeder Anwender MOWIDEC-TT ohne lange Schulung einsetzen.“
Beratung inklusive
Jörg Schwartz: „Dies können selbstverständlich nicht alle Faktoren sein, die für eine hohe Rundlaufgenauigkeit, Präzision und Oberflächengüte maßgeblich sind. Es soll einen kleinen Einblick in die zahlreichen Einflüsse geben, die eine Rolle spielen können. In der Mikropräzisionsbearbeitung profitiert jeder Anwender von dem Wissen der Hersteller. Denn vor allem über eine enge Zusammenarbeit und eine eingehende Beratung kann der Prozess effektiv und wirtschaftlich abgebildet werden.“
Mehr Informationen zu Schwartz Tools:
![]() |
Schwartz – tools + more GmbH & Co. KG |
![]() |
Gewerbestr. 26 |
![]() |
D-76327 Pfinztal |
![]() |
Tel.: 0049 (0)721 / 915 684-0 |
![]() |
Fax: 0049 (0)721 / 915 684-22 |
![]() |
E-Mail: info@schwartz-tools.de |
![]() |
www.schwartz-tools.de |
War dieser Artikel für Sie hilfreich?
![]() |
![]() |
![]() |
![]() |
![]() |
Bitte bewerten Sie diese Seite durch Klick auf die Symbole.
Zugriffe heute: 3 - gesamt: 4713.