Ökonomie und Ökologie im Einklang
Turbinenbau mit Anspruch
Im Rahmen der ICTM Conference 2019 zeigten Wissenschaftler des Fraunhofer ILT erste Ergebnisse des Fraunhofer-Fokusprojekts futureAM: Mit einem skalierbaren LPBF-System lassen sich großvolumige Bauteile herstellen und die bisherigen Grenzen konventioneller Anlagen für den metallischen 3D-Druck überschreiten.
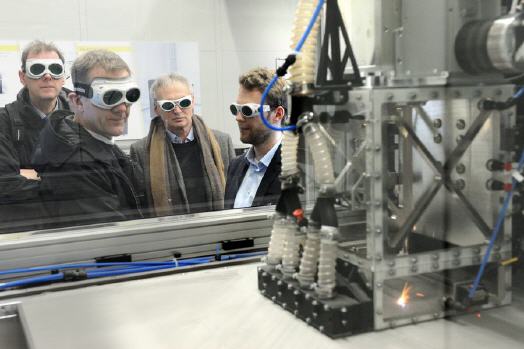
Zahlreiche Branchen, ein gemeinsamer Nenner: Seit 2011 treffen sich in Aachen auf der ICTM Conference alle zwei Jahre Turbinenhersteller, Softwareentwickler, Werkzeugproduzenten, Wissenschaftler sowie Maschinen- und Anlagenbauer, um mit Experten zum Beispiel aus der Luftfahrtindustrie und Energieerzeugung zwei Tage lang neue Trends zu diskutieren. Veranstalter sind die beiden Fraunhofer-Institute für Produktionstechnologie IPT und für Lasertechnik ILT, die sich auch als Forschungspartner an der Konferenz beteiligen.
Ecolonomical: Umwelt schonen und Geld sparen
Die Vorträge behandelten alle Themen von der Digitalisierung, Produktion, Werkstoffauswahl bis hin zur Zukunft des Turbomaschinenbaus. Hier ist jedoch nicht mehr die Rede vom Spagat zwischen Ökologie und Ökonomie: Gefragt ist der Zustand »ecolonomical«: der produktive Umweltschutz. Erheblich beeinflusst wird der Turbomaschinenbau aktuell nicht nur von der Energiewende und ihren hohen Anforderungen, sondern auch von den Umweltvorgaben der Internationalen Zivilluftfahrtorganisation (ICAO: International Civil Aviation Organization). Bis 2050 sollen die Kohlendioxid- und Stickstoff-Emissionen um 75 bzw. 90 Prozent sinken und die Lärmbelastung um 65 Prozent abnehmen. Die Erreichung dieser Ziele wird dadurch erschwert, dass aufgrund der positiven Auftragslage in der Luftfahrtbranche weltweit der Bedarf an Turbinen seit Jahren steigt.
So berichtete Lars Wagner, Vorstand Technik der MTU Aero Engines AG aus München, wie das Unternehmen unter anderem mit Hilfe einer Smart Factory den Auftragsboom und die Auslastung für die nächsten zehn Jahre bewältigen wird. Bei der Erhöhung der Produktivität spielt auch Additive Manufacturing (AM) eine wichtige Rolle. MTU zählt zu den Pionieren beim Einsatz dieser Technologie im Triebwerksbau, bereits 2000 seriengefertigte AM-Niederdruckturbinenteile werden derzeit in der Industrie eingesetzt. Geplant ist die Fertigung von weiteren AM-Bauteilen mit einem Volumen von 25 000 bis 30 000 Teilen pro Jahr ab 2020.
Additive Design erhöht Schaufel-Performance
Ein AM-Newcomer ist die MAN Energy Solutions SE aus Oberhausen, die mit dem »Laser Power Bed Fusion LPBF« in den metallischen 3D-Druck eingestiegen ist. Dieses Verfahren, auch bekannt als Selective Laser Melting SLM, ist am Fraunhofer ILT entwickelt worden und patentiert. Bewährt hat sich LPBF, resümiert Michael Kleinhenz, Head of Production bei MAN Energy Solutions, nicht nur beim Prototyping, sondern auch schon beim ersten zugelassenen Serienbauteil: Kleinhenz widerlegte in Aachen die Annahme, dass AM-Bauteile grundsätzlich teurer ausfallen. So ließen sich die Produktionskosten für das Bauteil eines Verdichterschaufelclusters senken, weil es nun nicht mehr aus 13 einzelnen Teilen entsteht, sondern als ein einziges Bauteil aus dem 3D-Drucker kommt. Für das Verfahren spreche außerdem, dass sich mit Hilfe des Additive Designs die Konstruktion optimieren und die Performance der Schaufel steigern ließe.
Noch ist die AM-Technik allerdings nicht ausgereizt. An welchen Verfahren die Wissenschaftler des Fraunhofer ILT arbeiten, um den metallischen 3D-Druck auch mit Blick auf den prozesssicheren Serieneinsatz zu optimieren, erfuhren die Teilnehmer beim Rundgang durch das Institut. Es ging unter anderem um die Integration von Sensoren in den LPBF-Prozess, den 3D-Druck von Bauteilen aus Titan und hochfesten Stählen sowie die Entwicklung von Werkstofflegierungen für Laser Additive Manufacturing.
Vielversprechende Ansätze im Bereich AM: schneller, größer, produktiver
Auf besonderes Interesse stießen drei Entwicklungen: Das hybrid-additive Laserauftragschweißen ist ein automatisiertes Auftragsverfahren, welches in einem BMBF geförderten Verbundprojekt (ProLMD) unter anderem mit Partnern aus der Luftfahrt untersucht wird. Es kombiniert das Laserauftragschweißen (Laser Material Deposition LMD) mit konventionellen Herstellungsverfahren. So können beispielsweise Verstärkungen oder andere Geometrieelemente auf Guss- oder Schmiedeteile mit Hilfe von LMD aufgetragen werden. Bereits praxiserprobt ist das Extreme Hochgeschwindigkeits-Laserauftragschweißen (EHLA), das sich als umweltfreundliche und schnelle Alternative zum Hartbeschichten mit Chrom(VI) beim Offshore-Einsatz in den Niederlanden bewährt hat.
Großvolumige Bauteile wiederum mit Ausmaßen von 1 000 mm x 800 mm x 500 mm lassen sich mit einem skalierbaren LPBF-System herstellen, das die bisherigen Grenzen konventioneller Anlagen für den metallischen 3D-Druck überschreitet. In Aachen wurde zudem ein System mit einem neuen Laserkopf vorgestellt, der im Rahmen des Fraunhofer-Fokusprojekts futureAM entwickelt wurde und die Produktivität im Vergleich zu üblichen LPBF-Anlagen um den Faktor 10 steigert.
Mehr Informationen zum Fraunhofer ILT:
![]() |
Fraunhofer-Institut für Lasertechnik ILT |
![]() |
Steinbachstr. 15 |
![]() |
52074 Aachen |
![]() |
Telefon +49 241 8906-0 |
![]() |
www.ilt.fraunhofer.de |
War dieser Artikel für Sie hilfreich?
![]() |
![]() |
![]() |
![]() |
![]() |
Bitte bewerten Sie diese Seite durch Klick auf die Symbole.
Zugriffe heute: 3 - gesamt: 4999.