Hightech-Werkstoff im Salzmantel
Herstellungskosten für MAX-Phasen senken
MAX-Phasen gelten als Material der Zukunft, beispielsweise für Turbinen in Kraftwerken und Flugzeugen, Raumfahrtanwendungen oder medizinische Implantate. Ein neues Verfahren von Wissenschaftlern des Forschungszentrums Jülich macht es nun erstmals möglich, die begehrte Werkstoffklasse im industriellen Maßstab herzustellen: Ein Mantel aus Salz schützt das Ausgangsmaterial bei einer Herstellungstemperatur von über 1.000 Grad vor Oxidation – und kann danach mit Wasser einfach wieder abgewaschen werden. Die Methode ist auch auf andere Hochleistungswerkstoffe anwendbar.
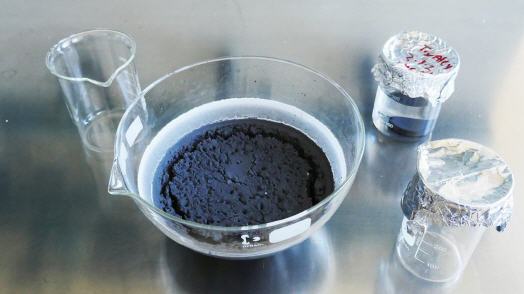
MAX-Phasen vereinen die positiven Eigenschaften von Keramiken und Metallen. Sie sind hitzestabil und leicht wie eine Keramik, gleichzeitig aber weniger spröde und plastisch verformbar wie ein Metall. Zudem sind sie die stoffliche Basis für die noch wenig erforschten MXene, die so überraschende elektronische Eigenschaften besitzen wie das Wundermaterial Graphen.
„Bisher fehlte ein geeignetes Verfahren, um MAX-Phasen in Pulverform herzustellen, so wie es für die industrielle Weiterverarbeitung wünschenswert wäre. In der industriellen Produktion spielen MAX-Phasen daher bislang praktisch keine Rolle“, erklärt Junior-Professor Jesus Gonzalez-Julian, Nachwuchsgruppenleiter am Forschungszentrum Jülich.
MAX-Phasen entstehen bei über 1.000 Grad Celsius. Damit die Materialien bei derart hohen Temperaturen nicht mit dem Luftsauerstoff reagieren und oxidieren, findet die Herstellung normalerweise im Vakuum oder in einer Schutzatmosphäre aus Argon statt. Die Jülicher Methode ist im Vergleich dazu verblüffend einfach. Die Forscher ummanteln die Ausgangsstoffe mit einem Salz, Kaliumbromid, das während des Prozesses schmilzt. Ein Vakuum oder eine Argon-Atmosphäre als zusätzlicher Schutz wird nicht mehr benötigt.
„Ein Bad aus flüssigem Salz umschließt dann das Material und verhindert, dass Sauerstoff aus der Luft damit in Berührung kommt“, erklärt Apurv Dash, Erstautor der Studie in Nature Materials und Doktorand am Forschungszentrum Jülich.
Das Salz wirkt außerdem als Trennmittel. Die Komponenten backen nicht mehr zu einem kompakten Feststoff zusammen, sodass die Herstellung feinkörniger Pulver möglich wird. Das ist wichtig, ein langer und energieaufwändiger zusätzlicher Mahlvorgang wird so nicht mehr benötigt. Als positiver Nebeneffekt senkt das Salzbad zudem die Synthesetemperatur, bei der die Ausgangsstoffe eine Verbindung miteinander eingehen, was zusätzlich dazu beitragen dürfte, Energie- und Herstellungskosten einzusparen.
Verfahren mit geschmolzenem Salz werden bereits seit längerem zur Pulverherstellung für sogenannte nichtoxidische Keramiken eingesetzt. Allerdings nicht an der Umgebungsluft, sondern in schützender Argon-Atmosphäre, was die Herstellung entsprechend aufwendig und teuer macht.
„Kaliumbromid, das wir verwenden, besitzt die Besonderheit, dass es unter Druck schon bei Raumtemperatur vollkommen dicht und undurchlässig wird. Wir konnten jetzt nachweisen, dass es ausreicht, wenn man den Werkstoff fest genug in ein Salzpellet einkapselt, um schon vor dem Schmelzen des Salzes bei 735 Grad Celsius den Sauerstoffkontakt zu unterbinden. Eine Schutzatmosphäre ist dann nicht mehr nötig“, erklärt Apurv Dash.
Bei der Erfindung der Methode war – wie bei vielen wissenschaftlichen Entdeckungen – auch ein wenig Zufall mit im Spiel. Vakuumöfen sind wegen der hohen Anschaffungskosten rar und aufwendig zu reinigen. Für die Pulverherstellung war der Jülicher Doktorand daher testweise einmal auf einen normalen Ofen ausgewichen – mit Erfolg.
Das Verfahren ist nicht auf ein bestimmtes Material beschränkt. Die Forscher konnten damit bereits eine Vielzahl unterschiedlicher MAX-Phasen und weitere Hochleistungswerkstoffe herstellen wie zum Beispiel Titanverbindungen für Bioimplantate und den Flugzeugbau. Als nächstes planen sie nun die Erprobung industrieller Prozesse, mit denen sich die Pulver weiter verarbeiten lassen.
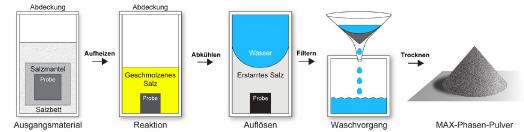
Mehr Informationen zum Forschungszentrum Jülich:
![]() |
Forschungszentrum Jülich GmbH |
![]() |
Wilhelm-Johnen-Straße |
![]() |
52428 Jülich |
![]() |
Tel.: 02461 61-0 |
![]() |
Fax: 02461 61-8100 |
![]() |
E-Mail: info@fz-juelich.de |
![]() |
www.fz-juelich.de |
War dieser Artikel für Sie hilfreich?
![]() |
![]() |
![]() |
![]() |
![]() |
Bitte bewerten Sie diese Seite durch Klick auf die Symbole.
Zugriffe heute: 3 - gesamt: 4633.