Statt acht Stunden jetzt nur 20 Minuten
Scheibenfräser von ISCAR verbessert die Prozesse
Rohrhalterungssysteme für den Energiesektor sind die Spezialität der LISEGA SE im niedersächsischen Zeven. Das Unternehmen verwendet dabei regelmäßig hochfeste Stähle. Diese stellen große Anforderungen an die Zerspanung. Beim Einbringen von Schlitzen in Gabelköpfe erzielt LISEGA enorme Prozessvorteile mit einem Sonderscheibenfräser von ISCAR. Früher dauerte eine Bearbeitung bis zu acht Stunden. Mit dem Werkzeug aus Ettlingen schaffen es die Zerspanungsspezialisten in gerade einmal 20 Minuten.
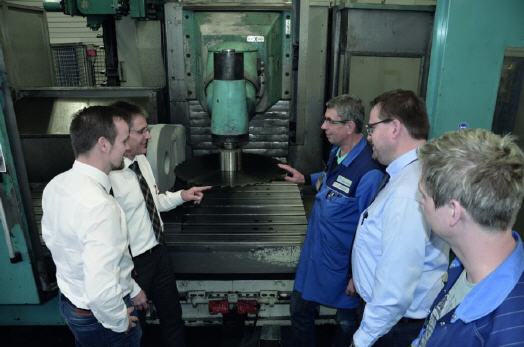
LISEGA wurde 1964 gegründet und fertigt Halterungssysteme für den Einsatz in Kohle- und Gaskraftwerken, auf Bohrinseln oder in der Petrochemie. Ein Großteil der Produkte geht in den Export, die Kunden sind weltweit verteilt. LISEGA betreibt Standorte in Frankreich, China, Großbritannien, den USA und Indien und einen weiteren in Deutschland. Am Hauptsitz in Zeven mit rund 25.000 Quadratmetern Produktionsfläche sind gut 600 Mitarbeiter beschäftigt, ca. 50 davon mit fachlicher Qualifikation in der Zerspanung. Die Ansprüche der Kunden sind hoch. Das Unternehmen muss sehr flexibel sein und mit schnellen Lieferzeiten auf kurzfristige Anfragen reagieren.
Hohe Anforderung an die Zerspanung
Waren in der Vergangenheit eher normale Baustähle üblich, müssen heute regelmäßig hochfeste Duplex-Stähle bearbeitet werden. „Diese stellen größere Anforderungen an die Zerspanung. Darauf waren wir werkzeugtechnisch nicht eingestellt“, beschreibt Friedemann Brandt, Meister in der spanenden Fertigung. Handlungsbedarf entstand beim Einbringen eines Schlitzes in Gabelköpfe für Stoßbremsen in Edelstahl 1.4312. Solche bis zu drei Tonnen schwere Komponenten wirken als eine Art Sicherheitsgurt in Rohrleitungssystemen. Sie leiten Druckstöße weiter, die aufgrund von Dynamiken in den Systemen entstehen können.
Bisherige Bearbeitung dauerte zu lange
Zum Einbringen des Schlitzes setzte LISEGA bislang eine Bandsäge ein – mit deutlichen Nachteilen. Eine Bearbeitung dauerte bis zu acht Stunden. „Mit dieser Lösung konnten wir das Auftragsaufkommen nicht mehr bewältigen. Der Vorgang dauerte zu lange und die Prozesssicherheit war nicht immer gegeben. Wir mussten nacharbeiten, etwa weil das Sägeblatt nicht präzise geschnitten hat“, schildert Dirk Giesel, stellvertretender Gruppenleiter Zerspanung. Auf der Suche nach einer Alternative wandten sich die Zevener an den Werkzeugspezialisten ISCAR, zu dem bereits langjährige Kontakte bestanden.
Damit waren Bernd Pfeuffer, Produktspezialist Fräsen, Claus Mackenstedt, Beratung und Verkauf, sowie Christian Buck, Technische Beratung und Vertrieb bei ISCAR mit im Team. „Wir haben uns die Anwendung vor Ort angesehen. Dabei kam relativ schnell die Idee auf, einen Scheibenfräser einzusetzen“, sagt Claus Mackenstedt. „Auf der Suche nach einer geeigneten technischen Lösung haben wir mehrere Varianten durchgespielt“, ergänzt Christian Buck. Aus Sicht von Bernd Pfeuffer bestand eine große Herausforderung in der Bearbeitungsstabilität. „Läuft das Werkzeug ruhig oder kann es vor lauter Schwingungen gar nicht zum Einsatz kommen?“, habe die entscheidende Frage gelautet.
Gemeinsam eine Lösung gefunden
In dieser Projektphase haben die Partner intensiv zusammengearbeitet. Maschinendaten wurden verschickt und die Machbarkeit geprüft. „Wir haben gemeinsam erarbeitet, wie eine geeignete Werkzeugaufnahme auszusehen hat. Dabei standen wir in ständigem Kontakt mit ISCAR“, schildert Friedemann Brandt. Als Ergebnis der Zusammenarbeit legten die Ettlinger einen detaillierten Entwurf vor. „Auf dieser Basis sind wir das Risiko eingegangen, eine Konstruktion ohne Praxiserfahrung in Auftrag zu geben“, sagt Friedemann Brandt.
Die ISCAR-Experten entwickelten einen Scheibenfräser samt Aufnahme als Sonderlösung. Die Wendeschneidplatten sind hingegen Standardausführungen. Der Fräser besitzt einen Durchmesser von 700 Millimetern und erzielt eine Schnittbreite von 6,8 Millimetern. Als das Werkzeug nach kurzer Entwicklungszeit zur Verfügung stand, führten die Projektpartner erste Praxistests durch – mit positiven Ergebnissen. Der Fräser arbeitete mit einer Schnittgeschwindigkeit von 99 Metern pro Minute und einer Schnitttiefe von 110 Millimetern. Der Vorschub pro Zahn betrug 0,07 Millimeter. Das Werkzeug wurde von außen mit einem Kühlmitteldruck von 20 bar gekühlt. Die erzielte Oberflächengüte überzeugte die Partner. Damit war der Weg für einen dauerhaften Einsatz frei.
Der Scheibenfräser arbeitet mit 40 Zähnen. Dabei handelt es sich um vierschneidige Platten mit tangentialer Schraubenklemmung für einen sicheren Sitz. „LISEGA kann mit kleinen Schnittgeschwindigkeiten fahren, und es entstehen keine hohen Temperaturen. Deswegen ist auch kein hochverschleißfestes Substrat erforderlich“, beschreibt Bernd Pfeuffer. Darüber hinaus besitzt der Scheibenfräser einen speziellen TN-Spanformer. „Er leitet den Span von der Wandung in der Nut weg in die Schnittmitte. Dies verhindert Schäden an der Wandungsoberfläche“, sagt Christian Buck.
Die Oberfläche passt perfekt
LISEGA erzielt mit dem Scheibenfräser eindeutige Prozessvorteile. „Der Schnitt kann jetzt exakt auf 1/10 Millimeter genau eingebracht werden. Früher hatten wir das Problem, dass der Schnitt verlaufen konnte. Eine Bearbeitung zog sich bis zu acht Stunden hin. Jetzt dauert das nicht länger als 20 Minuten“, freut sich Friedemann Brandt. Auch bei der Nacharbeit sparen die Zerspanungsspezialisten Zeit ein. „Der Schnitt ist praktisch gratfrei. Wir gehen nur noch kurz mit dem Handentgrater drüber, und die Oberfläche passt perfekt“, sagt Dirk Giesel.
Für die Zerspanungsexperten ist die Bearbeitung zuverlässiger geworden. „Wir können uns darauf verlassen, dass die Komplettbearbeitung prozesssicher läuft“, freut sich Friedemann Brandt. Lob gibt es auch für die Kooperation mit den ISCAR-Mitarbeitern. „Wir konnten uns immer auf einen starken Außendienst und kompetente Anwendungstechniker verlassen.“ Das Angebot war schnell erstellt und die Projekt-Dokumentation bezeichnet er als vorbildlich. „Das gibt uns auch für zukünftige Anwendungen viel Sicherheit.“ Sein Fazit: „Wir sparen bei dieser Bearbeitung viel Zeit, und die Produktqualität ist besser geworden. Das sind die Bringer für uns.“
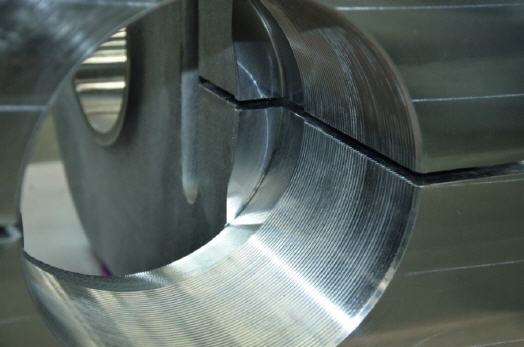
Mehr Informationen zur ISCAR Germany GmbH:
![]() |
ISCAR Germany GmbH |
![]() |
Eisenstockstraße 14 |
![]() |
76275 Ettlingen |
![]() |
Tel.: 07243 9908-0 |
![]() |
Fax: 07243 9908-93 |
![]() |
E-Mail: werkzeuge@iscar.de |
![]() |
www.iscar.de |
War dieser Artikel für Sie hilfreich?
![]() |
![]() |
![]() |
![]() |
![]() |
Bitte bewerten Sie diese Seite durch Klick auf die Symbole.
Zugriffe heute: 3 - gesamt: 4784.