Entmagnetisieren von Rohrleitungen
EWM-Technik im Einsatz auf Baustellen
Hier muss jede Schweißnaht sitzen – Gashochdruckleitungen müssen höchsten Sicherheitsstandards entsprechen. Betreiberunternehmen wie die terranets bw GmbH überprüfen die Wandstärke deshalb regelmäßig mit sogenannten Rohrleitungsmolchen. Das Problem: Die Prüfsysteme magnetisieren die Leitungen. Werden Reparaturen nötig, kommt es beim Schweißen zur Ablenkung des Lichtbogens und damit zum Einschluss von Poren und Bindefehlern. Um dem entgegenzuwirken, hat EWM das Entmagnetisierungsgerät Degauss 600 entwickelt. Die EWM-Lösung ist handlich, kompakt und baustellengeeignet.
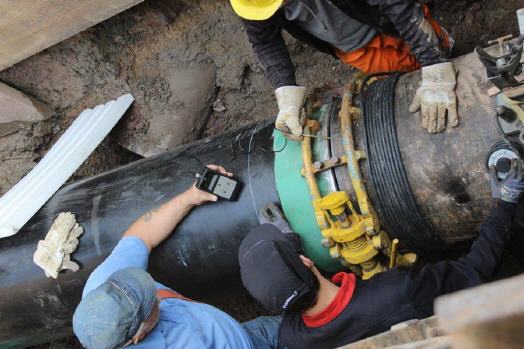
Um die Integrität zu gewährleisten, werden Gashochdruckleitungen durch eine so genannte „intelligente Rohrleitungsmolchung“ überprüft.
Ein Rohrleitungsmolch ist ein zylindrischer Körper, der aus mehreren Scheiben besteht, die mit Manschetten gegen die Rohrwand abgedichtet sind. Er wird durch den Differenzdruck innerhalb des Rohres transportiert. Die Länge eines Molches beträgt 6 bis 10 m, die Vorschubgeschwindigkeiten bewegen sich zwischen 1 und 5 m/s.
Die Wandstärke des Rohres wird mittels Magnetstreuflussverfahren (Magnetic Flux Leakage) gemessen. Dafür sind starke, ringförmig am Molch angebrachte Magnete notwendig; unmittelbar danach werden über Sensoren die eingebrachten Magnetflusslinien registriert. Diese im Zuge der Messungen aufgenommenen Signale werden mit Referenzsignalen verglichen. Aufgrund der Abweichungen können mögliche Stellen mit Materialverlust oder Ovalitäten erfasst werden. Da der intelligente Molch ein System zur Bestimmung der zurückgelegten Entfernung mitführt, kann die Position der Befunde erfasst werden. Nachteil dieser Messmethode ist, dass die überprüften Rohrleitungen dauerhaft magnetisiert sind. Deshalb sollte aufgrund der Messergebnisse eine zeitnahe Reparatur der beanstandeten Stellen erfolgen.
Für die beteiligten Unternehmen, die terranets bw GmbH als Betreiber und die Leonhard & Weiss GmbH als ausführendes Bauunternehmen, war klar, dass durch die Molchung noch ein starker Restmagnetismus im Rohr vorhanden sein wird. Um den bekannten Problemen durch Magnetismus beim Schweißen – Ablenkung des Lichtbogens und Einschluss von Poren und Bindefehlern – zu begegnen, wurde die EWM AG beauftragt, mit ihrem Entmagnetisierungsgerät Degauss 600 den Restmagnetismus im Rohr während des Schweißens zu eliminieren.
Grundprinzip ist, dass ein stromdurchflossener Leiter ein Magnetfeld erzeugt. Um ein Rohr zu entmagnetisieren, wird ein Stromkabel möglichst eng um das Rohr gewickelt. Durch einen Stromfluss kann ein Gegenmagnetfeld gleicher Stärke erzeugt und der Restmagnetismus so eliminiert werden. Je mehr Windungen aufgebracht werden, desto größer ist die maximale Feldstärke, die mit konstantem Strom erzeugt werden kann.
Die Degauss 600 bietet zwei Möglichkeiten des Entmagnetisierens:
1. Bei der Degauss-Funktion wird mit einem hohen Stromwert beginnend und mit alternierender Polarität der Stromfluss schrittförmig gesenkt. Dort wird entlang einer Hysteresekurve das Bauteil entmagnetisiert. Diese Methode funktioniert sehr gut bei kurzen Bauteilen.
2. Bei der Methode activgauss fließt kontinuierlich Strom durch die Wicklungen, wodurch ein permanentes Magnetfeld erzeugt wird. Diese Methode ist bei langen Bauteilen anzuwenden, wie im vorliegenden Fall bei Rohrleitungen.
Vor dem Einbringen des neuen Rohrabschnittes mit einem Durchmesser von 600 mm und einer Wandstärke von 10 mm wurde der Restmagnetismus an der Schweißfuge mit einem Feldstärkemessgerät gemessen. Die Werte lagen zwischen 2 und 5 mT entlang des Rohrumfangs. Nach den vorliegenden Erfahrungen der EWM AG lagen die Messwerte unterhalb des Bereiches, ab dem noch mit einer Elektrode geschweißt werden kann. Für diese Rohrseite war daher absehbar, dass höchstwahrscheinlich keine Entmagnetisierung erforderlich sein wird. Der alte, entfernte Rohrabschnitt wies Feldstärken von 18 bis 35 mT auf. Durch umfangreiche Voruntersuchung im Hause EWM konnten die erforderliche Windungszahl und der voraussichtlich benötigte Strom festgelegt werden. In diesem Fall entschieden sich die Spezialisten von EWM, neun Windungen auf das Rohr aufzulegen.
Nachdem das neue Rohrstück eingebracht war, wurde der verbliebene alte Rohrabschnitt überprüft. Dabei wurden Feldstärken von 15 bis 30 mT entlang des Umfangs gemessen. Auf dem Bild sind die an dem alten Rohrabschnitt notwendigen Windungen zu sehen.
Nach dem Vorwärmen der Schweißfuge auf ca. 100 °C wurde die Feldstärke abermals gemessen, da die Erwärmung des Rohres einen Einfluss auf das Magnetfeld hat. Mittels Fernregler wurde der passende Stromwert (175 A) zur Kompensation des magnetischen Feldes eingestellt. Nach einer Minute war das Magnetfeld an der Schweißstelle kompensiert und die Schweißung konnte beginnen.
Wie schon erwähnt, ist die Feldstärke am Umfang nicht konstant. Diese Schwankungen kann ein Spulensystem schon physikalisch nicht ausgleichen. So war es nicht verwunderlich, dass der Entmagnetisierungsstrom geändert werden musste, nachdem ca. ein Viertel der Umfangsschweißung beendet war. Die Feldstärke sinkt mit Fortschritt der Schweißungen (d. h. mit dem Verbinden der beiden Rohrabschnitte), sodass der einzustellende Stromwert ebenfalls sinkt.
Dieser Vorgang wurde bis zum Ende des Wurzelschweißvorgangs viermal wiederholt. Die Schweißer hatten Anweisung, mit dem Schweißen aufzuhören, wenn sie einen negativen Einfluss durch das Magnetfeld wahrnahmen. Die Messungen zeigten, dass dieser Grenzwert beim E-Hand-Schweißen bei 4 bis 5 mT lag. Das deckte sich mit den Erfahrungen von EWM für das E-Hand-Schweißen. Ist die Wurzellage erfolgreich geschweißt, gleichen sich die Magnetfelder aus, sodass die Zwischen- und die Decklage ohne jegliche Kompensation geschweißt werden konnten.
Bei der zweiten Stoßfuge wurde eine höhere Feldstärke zwischen 26 und 43 mT gemessen. Dies erforderte 13 Windungen und einen Entmagnetisierungsstrom von 140 A. Der Abstand des gewickelten Kabels zur Schweißfuge betrug hier 16 cm. Dank der im Labor entwickelten Grundlagen konnten die Schweißverbindungen ohne Verzögerung auf der Baustelle durchgeführt werden. Nach 4,5 Stunden war der Einsatz beendet und beide Schweißnähte waren erfolgreich gesetzt. Die nachfolgenden Röntgen- und Ultraschalluntersuchungen zeigten keine Auffälligkeiten. Der zuständige unabhängige Überwachungsingenieur vom TÜV Süd war, ebenso wie die beteiligten Firmenvertreter der terranets bw GmbH und der Leonhard & Weiss GmbH, von der einfachen Bedienung und der Baustellentauglichkeit (geringes Gewicht und kleine Baugröße) der Degauss 600 überzeugt.
Auf der zweiten Baustelle wartete eine schwierige Aufgabe. Dort sollte der alte Absperrschieber einer Hochdruckgasleitung ersetzt werden. Da die Schweißfuge in der Nähe des Schiebers lag, schied das E-Hand-Schweißverfahren aus; die Dichtflächen des Kugelventils wären durch unvermeidbare Spritzer im Inneren des Rohres beschädigt worden. Deshalb kam das WIG-Schweißverfahren zur Anwendung. Doch dieser Schweißprozess reagiert deutlich empfindlicher auf Magnetisierung, als es bei dem E-Hand-Schweißen der Fall ist. Hier müssen die Magnetfelder komplett eliminiert werden.
Die gemessenen Feldstärken lagen bei 10 bis 12 mT, deutlich unter den Werten des gemolchten Abschnittes bei der ersten Baustelle. Daher wurden nur sechs Windungen bei 70 A benötigt, um das Magnetfeld vollständig zu eliminieren (Messwerte unter 0,5 mT = 8 A/cm). Das Schweißverhalten wurde ab einer Feldstärke von ca. 1,3 mT negativ beeinflusst. Die Schweißung wurde dreimal unterbrochen, um die induzierten Magnetfelder anzupassen. Hierbei wurde der Strom schrittweise auf ca. 40 A abgesenkt.
Während bei der Schweißung der ersten Stoßfuge die Entmagnetisierung nur auf der Rohrseite erforderlich war, musste bei dem zweiten Schweißstoß – wahrscheinlich durch die Wanderung des Magnetfeldes nach Komplettierung der ersten Schweißung – sowohl die Ventilseite (–4 mT) als auch der Rohrabschnitt (–12 bis –18 mT) kompensiert werden. Hierbei wurden sechs Windungen auf der Rohrseite aufgebracht. Durch die unterschiedlichen Polaritäten der Magnetfelder konnte das Stromkabel der Rohrseite zur Ventilseite mit einer Verlängerung von drei Windungen und gleicher Wicklungsrichtung weitergeführt werden. Bei einer Stromstärke von ca. 80 A wurde der Restmagnetismus vollständig kompensiert. Bis zur Vollendung der Wurzelschweißung wurde der Schweißprozess viermal unterbrochen, um korrigierend einzugreifen. Der Endstrom betrug ca. 25 A.
Die Einsätze in der Praxis zeigten, dass mit der Degauss 600 das Problem des Magnetismus beim Reparaturschweißen im Rohrleitungsbau auch bei starken Magnetfeldern gelöst werden kann. Die dafür erforderlichen Komponenten sind handlich, kompakt und baustellengeeignet. Die Bedienung ist sehr einfach und durch den Fernsteller kann die Stromquelle auch außerhalb der Baugrube platziert werden.
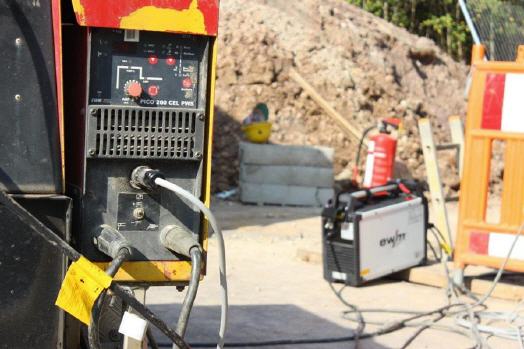
Mehr Informationen zur EWM AG:
![]() |
EWM AG |
![]() |
Dr.-Günter-Henle-Str. 8 |
![]() |
56271 Mündersbach |
![]() |
Tel.: +49 2680 181-0 |
![]() |
Fax +49 2680 181-244 |
![]() |
E-Mail: info@ewm-group.com |
![]() |
www.ewm-group.com |
War dieser Artikel für Sie hilfreich?
![]() |
![]() |
![]() |
![]() |
![]() |
Bitte bewerten Sie diese Seite durch Klick auf die Symbole.
Zugriffe heute: 3 - gesamt: 4796.