Effektive Lösung zum Entgraten
ECM sorgt für perfekte Oberflächen
Die ECM-Maschine ›CI‹ von Emag garantiert extrem schnelle und perfekte elektrochemische Bearbeitungsprozesse beim Entgraten und Bearbeiten. Außerdem benötigt sie nur eine minimale Aufstellfläche.
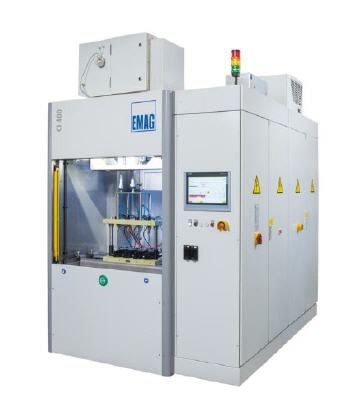
Welche Herausforderung hinter dem Entgraten steht, macht der Blick auf komplexe Komponenten wie etwa Pumpengehäuse deutlich: Diese Bauteile durchziehen häufig ein Geflecht von Bohrungen, durch die später Hydrauliköl oder Kraftstoff mit hohem Druck fließen. Insbesondere bei mehreren Bohrungsverschneidungen im Inneren eines solchen Gehäuses ist es dann nicht einfach, die vorhandenen Grate zu entfernen. Mitunter erfolgt ein langwieriger manueller Prozess, der bei großen Hydraulikkörpern für die Aviation- oder Nutzfahrzeugindustrie eine Stunde und mehr andauern kann und somit kostenintensiv ist.
»Außerdem birgt die manuelle Bearbeitung natürlich ein Fehlerrisiko«, betont Richard Keller, Mitglied der Geschäftsleitung bei Emag ECM. »Wenn Mitarbeiter einen Grat übersehen, kann sich dieser im späteren Einsatz lösen und die Strömung behindern. Das ist angesichts der hohen Sicherheitsanforderungen im Flugzeug- oder Automobilbau nicht akzeptabel.« Daher überrascht nicht, dass sich das elektrochemische Entgraten bei vielen Bauteilen durchgesetzt hat. Fehler sind hier weitgehend ausgeschlossen und das Bearbeitungstempo ist rasant: Während der Elektrochemischen Metallbearbeitung fließt zwischen dem Werkstück (der positiven Anode) und dem Werkzeug (der negativen Kathode) eine Elektrolytlösung. Dabei lösen sich Metall-Ionen vom Werkstück ab.
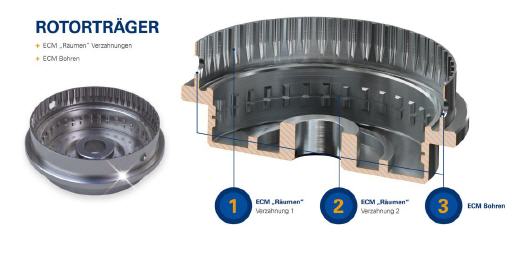
Beste Oberflächengüten
Die Form der Kathode beziehungsweise des Werkzeugs mit den aktiven, stromleitenden Bereichen ist so gewählt, dass der Materialabtrag am Werkstück zur gewünschten Bauteilkontur führt. Das führt nicht nur zu Oberflächen mit maximaler Güte – ohne thermische Schädigung des Werkstoffgefüges –, sondern auch zu völlig gleichbleibenden und repropuzierbaren Ergebnissen.
Dabei entwickeln die ECM-Spezialisten von Emag mit Sitz in Gaildorf bei Schwäbisch Hall das Verfahren mit Blick auf neue Werkstoffe, Bauteilgeometrien und Qualitätsanforderungen ständig weiter. Die wachsenden Herausforderungen bei Anwendern in aller Welt geben den Takt vor. Mit der CI-Maschinenreihe geht Emag ECM jetzt den nächsten Schritt: Um teuren Arbeitsraum in den Produktionsstätten ihrer Kunden einzusparen, haben die Ingenieure von Emag dabei unter anderem das Grundgestell der CI-Anlage überarbeitet und die Größe des Schaltschranks sowie des Elektrolytmanagementsystems optimiert.
Was steckt hinter diesen und weiteren Veränderungen? »Es ist offensichtlich, dass angesichts der technologischen Entwicklung das Entgraten und ECM-Räumen, zum Beispiel im bereits gehärteten Zustand eines Bauteiles, immer wichtiger werden. Wir wollten dafür eine Lösung entwickeln, die einerseits die herausragenden Vorteile der elektrochemischen Metallbearbeitung den Anwendern vollumfänglich garantiert und dabei prozesssichere Abläufe gewährleistet, andererseits zu einem extrem attraktiven Preis-Leistungs-Verhältnis angeboten werden kann. Genau das bietet die CI-Maschinenreihe. Unter anderem auf Basis von Early-Bird-Aktionen senken wir die Investitionskosten für den Kunden sogar noch weiter ab.«
Anschließend profitieren Anwender von einer flexiblen Technologie mit durchgängig hochwertigen Komponenten. Die Taktzeit lässt sich durch skalierbare Vorrichtungen präzise verändern, je nach Anforderung können mehrere Bauteile während eines Prozessschrittes gleichzeitig bearbeitet werden, eine Aufrüstung zur Vollautomation ist mit der CI-Maschine unproblematisch möglich. Alle Parameter während des ECM-Prozesses werden vollumfänglich und reproduzierbar überwacht sowie dokumentiert. Nicht zuletzt benötigt die CI-Maschine nur einen Stellplatz von rund 7,5 Quadratmetern inklusive Filtration – ein weiterer Kostenkiller im Einsatz.
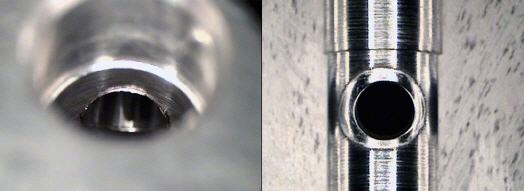
Zufriedene Nutzer
Dass diese Argumente die Anwender überzeugen, verdeutlichen aktuelle Erfolge von Emag ECM: Die neue CI-Maschine ist bereits bei einem nordamerikanischen Luftfahrt- und einem italienischen Nutzfahrzeug-Zulieferer im Einsatz. In beiden Fällen erfolgt eine Entgratung an sehr komplexen Gehäusen. Trotz einer Vielzahl von Bohrungen am Bauteil betragen die Zykluszeiten weniger als 60 Sekunden – ein Quantensprung angesichts der zuvor durchgeführten langwierigen manuellen Prozesse.
»Die Beispiele zeigen, dass wir mit unserem Entwicklungsansatz richtig liegen: Wir konnten uns gegen nationale und internationale Mitbewerber durchsetzen, weil die CI-Maschine hervorragende Leistungswerte aufweist, gleichzeitig aber kostengünstig ist. Der enorme Kostendruck bei den Anwendern verlangt nach einem effektiven Maschinenbau, wie wir ihn mit der CI-Maschine bieten«, erklärt Keller. Es spricht vieles dafür, dass dieses Kosten-Nutzen-Argument in Zukunft noch mehr Beachtung bei den Anwendern gewinnt, denn viele Bauteile in Elektro- und Hybridmotoren verlangen ebenso nach ECM-Räum-, -Bohr- und -Entgrat-Prozessen, für die Emag ECM bereits jetzt eine effektive Lösung zur Verfügung hat.
Dazu kommt ein weiteres Argument, dass angesichts der aktuellen Diskussion um den CO2-Footprint in der Automobilproduktion nicht zu unterschätzen ist: Im Vergleich zu vielen alternativen Verfahren vollzieht sich die Elektrochemische Metallverarbeitung deutlich schneller. Viele Tonnen Kohlendioxid werden so eingespart – eine Tatsache, die auch das Bundesumweltministerium überzeugt hat. So bekam ein Emag ECM-Kunde einen Umweltinnovationspreis, weil er die Elektrochemische Metallbearbeitung großtechnisch zum Einsatz bringt.
»Das bestätigt unser Engagement rund um diese effektive Technologie, die wir in den nächsten Jahren noch breiter in den Markt einbringen wollen«, so Keller abschließend.
Download:
Diesen Artikel finden Sie auch in Ausgabe 1/2019 unseres Fachmagazins ›Welt der Fertigung‹ auf Seite 22. Zum besagten Heft führt ein Klick auf den nachfolgenden Button!
Bitte beachten: Dieses Heft steht ab 1.2.2019 zum Download bereit.
Mehr Informationen zu Emag:
![]() |
Emag Gmbh & Co. KG |
![]() |
Austraße 24 |
![]() |
73084 Salach |
![]() |
Telefon 07162 17-0 |
![]() |
Fax 07162 17-199 |
![]() |
E-Mail: communications@emag.com |
![]() |
www.emag.com |
War dieser Artikel für Sie hilfreich?
![]() |
![]() |
![]() |
![]() |
![]() |
Bitte bewerten Sie diese Seite durch Klick auf die Symbole.
Zugriffe heute: 3 - gesamt: 5021.