Ergonomisches Gesamtkonzept
Transportauslastung bei dm optimiert
Schon seit 1986 gehören Kindertextilien zum Sortiment von dm-drogerie markt. Für die pünktliche Lieferung in die einzelnen dm-Märkte sorgt unter anderem das Textil-Verteilzentrum in Karlsruhe. Der stetig wachsende Durchsatz erforderte eine Umgestaltung der Halle inklusive des Verladebereiches. Der Vakuum-Spezialist Schmalz entwickelte ein ergonomisches und effizientes Gesamtkonzept, das den gestiegenen Anforderungen von dm gerecht wird.
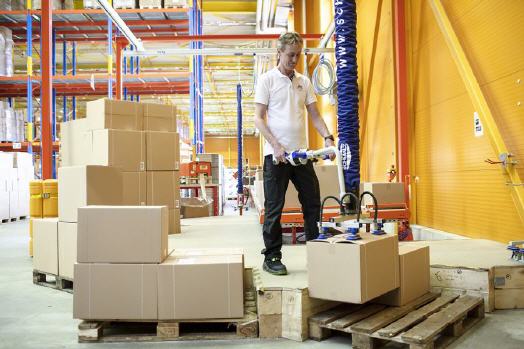
In den Regalen der dm-Märkte sind nicht nur Shampoos, Zahnbürsten und Deos zu finden. Vielmehr umfasst das umfangreiche dm-Sortiment auch Produkte aus den Bereichen Gesundheit, Ernährung, Foto sowie Baby- und Kinderkleidung. Beliefert werden die dm-Märkte – heute sind es mehr als 3.600 Filialen in 13 europäischen Ländern – aus verschiedenen Verteilzentren. Dort stellen die Mitarbeiter die eingehende Ware für die einzelnen dm-Märkte zusammen und sorgen so dafür, dass das breite Angebot von mehr als 12.500 Produkten immer für die Kunden verfügbar ist.
Im Textil-Verteilzentrum in Karlsruhe sind derzeit rund 160 Mitarbeiter beschäftigt. Auf einer Fläche von knapp 11.000 Quadratmetern erfolgt die Distribution von Kindertextilien, Bad-Accessoires und Kulturtaschen für alle deutschen Märkte sowie für ausgewählte dm-Märkte in Österreich, Kroatien und Slowenien. Pro Jahr werden hier rund 480.000 Pakete in vier Größen und mit einem Gewicht von bis zu 30 Kilogramm gepackt und ausgeliefert.
Verdreifachung der Aussendungen
„Anfangs verließen etwa 800 Pakete pro Tag unser Lager, mittlerweile sind es im Schnitt 1.850 Sendungen“, berichtet Alexander Fiedler, Leiter der Abteilung Textillogistik in Karlsruhe. Ein enormer Anstieg, dem das ursprüngliche Hallenlayout nicht mehr gerecht werden konnte. „Für das Verladen der großen Kartonagen nutzten wir von Anfang an den Vakuumheber JumboFlex 35 von Schmalz in Kombination mit einem Säulenschwenkkran“, erinnert sich der Logistiker. Doch nach dem Umbau des Verladebereichs war das vorhandene System nicht mehr optimal auf das neue Layout ausgelegt: Die Länge des Säulenschwenkkrans reichte nicht mehr für die neugestaltete Verpackungslinie und die Stapelhöhe war mit dem universellen Vakuumheber systembedingt begrenzt.
Diese Herausforderungen sollten durch ein neues System gelöst werden. Ziel war es, einerseits Prozesse zu optimieren und andererseits den Mitarbeitern das Arbeiten weiter zu erleichtern. Das Ladevolumen der LKW sollte noch besser genutzt, die Transportkosten minimiert und die CO2-Bilanz weiter verbessert werden. Zudem wies die bisherige Kombination ergonomische Schwachpunkte bei der Nutzung durch die Lageristen auf. Statt auf Paletten wurden Pakete auf Rollwagen verladen. Dies wirkte sich negativ auf den Arbeitsablauf aus, wie der Logistikleiter beschreibt: „Die Mitarbeiter mussten quasi in die Rollwägen steigen, um die Pakete in den hinteren Reihen zu erreichen.“
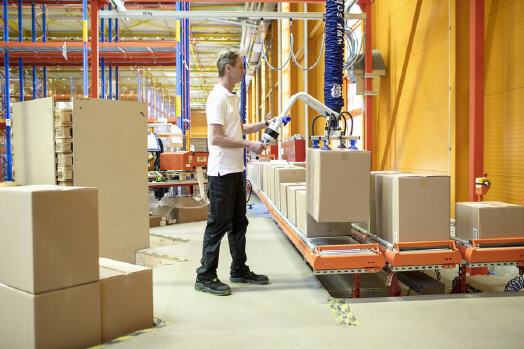
Flexibilität gewinnt
Auf der Suche nach einer ergonomischen und gleichzeitig effizienten Lösung zogen die Logistikplaner zunächst auch teil- und vollautomatisierte Lösungen in Erwägung. „Diese waren weder wirtschaftlich noch praktikabel, weil wir zum Beispiel stets verschiedene Kartontypen verladen müssen“, erklärt Fiedler und ergänzt: „Eine manuelle Handhabungslösung gibt uns hier die nötige Flexibilität und ist zudem günstiger und schneller realisierbar.“
Mit der logistischen Zielsetzung sowie dem Anspruch, dass die Lösung von den Mitarbeitern gänzlich akzeptiert werden muss, gingen die Verantwortlichen des Handelsunternehmens erneut auf die J. Schmalz GmbH zu. Der Kontakt zu dem Vakuum-Experten besteht schon seit mehreren Jahren, so dass die Karlsruher auch diesmal auf die konstruktive und lösungsorientierte Zusammenarbeit vertrauten.
Auf die Frage, wie sich der Transportraum auch nach oben hin maximal nutzen lässt, hatte Schmalz eine eindeutige Antwort: Der JumboFlex High-Stack ist speziell für Handhabungsaufgaben über Kopf entwickelt worden. Gleichzeitig können Lasten aus Bodennähe, beispielsweise die unterste Lage auf den Paletten, mit dem Schlauchheber rückenschonend aufgenommen werden. „In unserem Entwurf kombinierten wir den JumboFlex High-Stack mit einer leichtgängigen Krananlage“, erläutert Michael Schlaich, Leiter Geschäftsentwicklungsprozess Handhabung bei Schmalz.
Die notwendige Flexibilität erreicht das Konzept durch einen verstellbaren Vakuum-Greifer – so können die verschiedenen Kartongrößen problemlos gegriffen werden. Mehr Komfort und damit einen wichtigen Beitrag zur Akzeptanz der Systemlösung durch die Mitarbeiter im Verteilzentrum erreicht Schmalz durch eine Schalldämmbox, die den Schalldruckpegel des Vakuumerzeugers reduziert. Zudem ist der Vakuumheber mit einer Funkfernsteuerung ausgestattet, mit der die Nutzer den Vakuum-Erzeuger in Arbeitspausen direkt am Bedienelement aus- und wieder einschalten können.
„Das reduziert den Geräuschpegel zusätzlich und spart zudem Energie“, verdeutlicht Schlaich. Das aufeinander abgestimmte Gesamtkonzept überzeugte nicht nur die Entscheider. „Wir bezogen die Mitarbeiter vor Ort frühzeitig mit ein und konnten in einem Feldtest die Funktionalität des JumboFlex High-Stack erproben“, erklärt Alexander Fiedler.
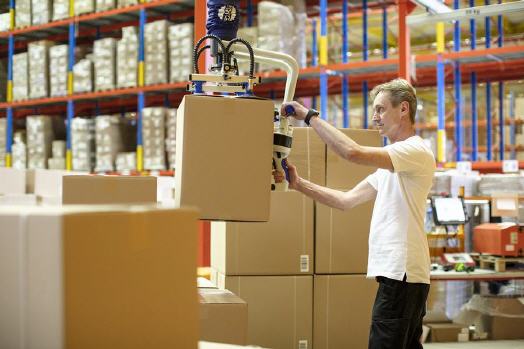
Ergonomisch und sicher
Heute kommen die Kartonagen auf drei parallelen Rollenbahnen in den Verladebereich. „Dieses Layout ist möglich, weil auch die mittlere Bahn mit der neuen Hebehilfe ohne Verrenkungen erreichbar ist“, ergänzt der Logistikleiter. Die Mitarbeiter stehen auf einem circa 40 Zentimeter hohen Podest, was die Zugänglichkeit im Vergleich zu früher verbessert. Sie stapeln die Pakete mithilfe des JumboFlex High-Stack auf Paletten bis zu einer Höhe von 215 Zentimetern.
„Dank des langen, drehgelagerten Bedienbügels ist von der unteren bis zur obersten Lage jeder Ablageplatz auf der Palette in ergonomischer Haltung erreichbar“, betont Schlaich. Die Endlos-Dreheinheit verschafft viel Bewegungsfreiheit und verhindert ein Verdrehen des Schlauches. So kann das Gerät flexibel aus allen Richtungen bedient werden.
Um ein vorzeitiges Herabfallen der Waren auszuschließen, kann der Anwender diese nur im abgesenkten Zustand ablösen. Erst wenn der Nutzer den Taster für das Absenken der Last komplett durchdrückt, lässt sich ein zweiter Hebel betätigen, der das Vakuum aufhebt. Außerdem erfolgt die Belüftung des Greifers so schnell, dass kein zusätzlicher Kraftaufwand zum Lösen des Schlauchhebers benötigt wird.
„Die neue Lösung hat unsere Erwartungen voll und ganz erfüllt“, resümiert Alexander Fiedler. Aufgrund der erhöhten Stapelhöhe kann das Ladevolumen der LKW deutlich besser genutzt und damit die Anzahl der täglichen Transportfahrten reduziert werden. Das Feedback der Mitarbeiter fällt ebenso positiv aus: „Sie nehmen die Hebehilfen sehr gut an und loben die Leichtgängigkeit des Kransystems“, gibt Fiedler seine Eindrücke aus dem Versandbereich weiter.
Mehr Informationen zur J. Schmalz GmbH:
![]() |
J. Schmalz GmbH |
![]() |
Aacher Str. 29 |
![]() |
72293 Glatten |
![]() |
Tel.: +49 (0)7443 2403-0 |
![]() |
Fax: +49 (0)7443 2403-259 |
![]() |
E-Mail: schmalz@schmalz.de |
![]() |
www.schmalz.com |
War dieser Artikel für Sie hilfreich?
![]() |
![]() |
![]() |
![]() |
![]() |
Bitte bewerten Sie diese Seite durch Klick auf die Symbole.
Zugriffe heute: 3 - gesamt: 5205.