Laser Blanking verbessert Umformprozess
Punkten mit Laser-geschnittenen Platinen
Erste namhafte Automobilhersteller in Europa machen es vor und profitieren von den Vorteilen der Dynamic Flow Technology. Die leistungsfähigen und effizienten Platinenschneidanlagen mit Laser von Schuler versorgen heute Pressenlinien vieler OEMs und Zulieferer. Hierdurch lassen sich bei neuen Modellen bereits komplette Schnittwerkzeugsätze einsparen – bei rund einem Dutzend Werkzeugen pro Fahrzeugkarosserie ergibt sich hierdurch eine Kostenreduzierung im Millionen-Euro-Bereich.
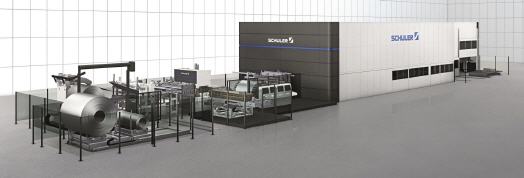
Der Anteil von Aluminium in Autos und Nutzfahrzeugen nimmt zu, weil der leichte Werkstoff die Leistung steigert und den Kraftstoffverbrauch sowie die Emissionen reduziert. Doch das oberflächensensitive Material stellt die Verarbeiter nicht nur beim Schneiden vor die Herausforderung des schonenden Handlings. Darüber hinaus neigt Aluminium zur Gratbildung an der unteren Schneidkante.
Löst sich dieser Grat und verbleibt im Umformwerkzeug, führt er zu Abdrücken auf der Materialoberfläche, die selbst nach dem Lackiervorgang noch sichtbar sind, und somit zu Ausschussbauteilen. Zur Vermeidung des Schnittgrats sind neben zusätzlichen Anlagenkomponenten wie Flitterabsauger oder Platinenreinigungsanlagen regelmäßige Anlagenstopps zur Reinigung der Umformungswerkzeuge notwendig. Je nach Bauteil kann dies eine fünf- bis zehnminütige Produktionsunterbrechung nach bereits wenigen hundert Hüben nach sich ziehen.
Aluminiumplatinen, die auf einer Laser Blanking Line von Schuler entstehen, erfüllen nicht nur die hohen Qualitätsanforderungen der Automobilindustrie, sondern bilden auch kaum abfallenden Grat. Durch die Einsparung der regelmäßigen Reinigungsaufwände erhöhen Laser-geschnittene Platinen somit die Produktivität der Pressenlinien.
Grundsätzlich ist die Flexibilität hinsichtlich der Konturenanpassung bereits von den Laser-geschnittene Platinen aus dem Tryout-Prozess bekannt. Je nach Bedarf lassen sich Platinengeometrien im Laserschneidprogramm anpassen und unkompliziert in kleinen Chargen ohne Werkzeug fertigen. Im Vergleich zu den hierzu meist eingesetzten Flachbettlasern werden die Platinen bei einer Laser Blanking Line nicht aus einem Rechteck herausgeschnitten, sondern direkt aus dem kontinuierlich durchlaufenden Bandmaterial des Coils.
Beispiel Motorhaube: Gehen wir von einer mit Robotern automatisierten Schrotttrennung und Gutteilabstapelung aus, so muss ein zusammenhängendes und umlaufendes Schrottgitter mit ca. 2-3 cm Stegbreite berücksichtigt werden. Auch ergibt sich durch die rechteckige Rohplatine ein Verschnitt von ca. 6 cm pro Seite, der beim Schneiden aus einem fortlaufenden Band für die nächste Haubenplatine verwendet werden könnte (siehe blau gestrichelter Bereich in der Grafik).
Würde man also für zwei Hauben auf einem Flachbettlaser eine Rohplatine von 2.260 mm x 2.200 mm benötigen, käme eine Laser Blanking Line mit einer Vorschublänge von 2.065 mm bei einer Coilbreite von 2.150 mm zurecht. Das würde einer Materialeinssparung von ca. 11 % entsprechen. Unabhängig ob die Teile eingekauft oder in House gefertigt werden: Materialeinsparung ist immer gleich auch Kosteneinsparung.
Neben dem Aspekt der Materialeinsparung sprechen des Weiteren die viel höheren Ausbringleistungen für das Schneiden im Dynamic Flow. Während Flachbettlaser in der Regel zwischen zwei und drei solcher Platinen pro Minute fertigen können, erreichen die Ausbringungsmengen zum Beispiel bei Hauben auf einer Laser Blanking Line bis zu 35 Teile pro Minute mit einer Anlageneffizenz von über 80%. In einer Stunde können somit ca. 1700 Teile gefertigt werden.
Je nach Einkaufsstrategie können entweder kleine Tryout-Chargen auf der eigenen Laser Blanking Line flexibel und auf Knopfdruck zwischen der Serienproduktion gefahren werden oder von einem Zulieferer mit Laser Blanking Line zeitnah eingekauft werden. Laser Blanking kombiniert die Möglichkeit der flexiblen Geometrieanpassung und dem werkzeuglosen Schneiden von Flachbettlasern mit erhöhten Reaktionszeiten, da nicht nur schneller produziert werden kann, sondern auch der vorgelagerte Cut-to-Length-Prozess eingespart wird. Damit ist der Tryout-Prozess durch die Verwendung einer Laser Blanking Line hinsichtlich zweier Aspekte optimierbar: der Kostensenkung durch Materialeinsparung und flexiblere Beschaffungsmöglichkeiten.
Sie kommen zwar nicht oft vor, aber manchmal eben doch: Änderungen während der Serienfertigung. Ein Beispiel ist die Umstellung auf ein Material mit veränderten Fließverhalten. Während die Anpassungen am Umformungs- oder Schneidwerkzeug mit Vorlauffertigungen und Werkzeugarbeiten einhergehen, können Laser-geschnittene Platinen einfach in ihrer Kontur verändert und die Umstellung auf das neue Material vereinfacht werden.
Auch lässt sich zu jeder Zeit der vorherige Status wieder herstellen. Dies bietet zudem die Möglichkeit, Optimierungen – beispielsweise zur Materialeinsparung – ohne großen Aufwand oder Risiko auszuprobieren. Schon kleine Materialeinsparungen von ein bis zwei Prozent bedeuten bei einer angenommenen Produktion pro Blanking Line von ca. 30.000 t Stahl und 10.000 t Aluminium eine Einsparung von bis zu 600 t Stahl und 200 t Aluminium pro Jahr.
So ermöglicht es eine Laser Blanking Line, die Potentiale der Materialeinsparung auch während der Serienfertigung unkompliziert auszunutzen und bei Änderungen von den reduzierten Zeitaufwänden der Werkzeugarbeiten zu profitieren.
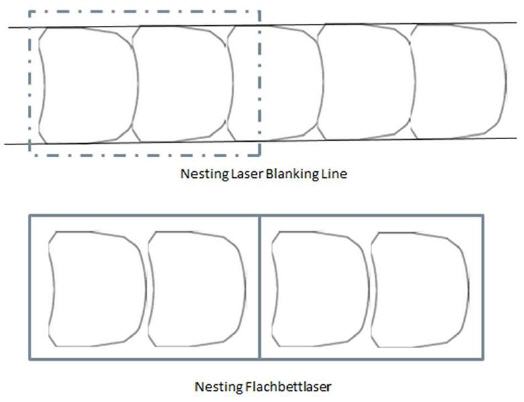
Mehr Informationen zur Schuler AG:
![]() |
Schuler AG |
![]() |
Bahnhofstr. 41 |
![]() |
73033 Göppingen |
![]() |
Tel.: +49 (71 61) 66-0 |
![]() |
Fax: +49 (71 61) 66-233 |
![]() |
www.schulergroup.com |
War dieser Artikel für Sie hilfreich?
![]() |
![]() |
![]() |
![]() |
![]() |
Bitte bewerten Sie diese Seite durch Klick auf die Symbole.
Zugriffe heute: 3 - gesamt: 5103.