Drei Roboter und vier Kameras im Einsatz
Fertigung von Stützkonsolen
Neue Qualitätsstandards setzt MartinMechanic mit der Entwicklung einer hochwertigen Prüfanlage für Stützkonsolen aus galvanisch verzinktem Stahl. Mit ihr wird die Fertigung von Bauteilen landwirtschaftlicher Geräte aus tiefgezogenen Umformteilen überprüft. Drei Roboter teilen sich die einzelnen Arbeitsschritte bei einer Taktzeit von vier Sekunden. Die MPK01969 läuft im Drei-Schicht-Betrieb.
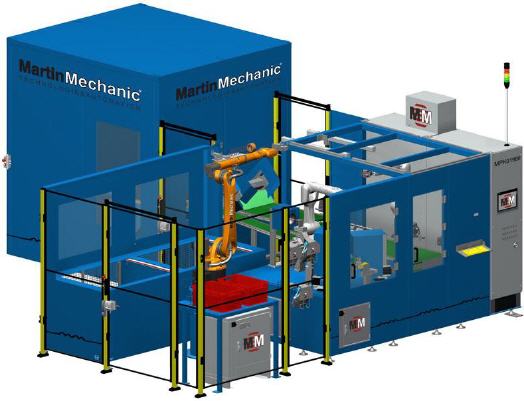
Die Anlage ist sehr hochwertig ausgestattet. So sind zum Beispiel die robusten Lichtgitter im Profil eingelassen, damit sie nicht störungsanfällig werden. Anforderungstaster und Notaus-Schalter wurden in den Axelent-Schutzzaunelementen integriert. Diese verfügen stirnseitig über einen Kartenleser. Durch das Zugangsberechtigungssystem meldet sich der Werker an der Prüfanlage an. Anhand seiner Daten erkennt die Anlage dann Funktion und Level der Bedienungsschritte.
Die Schallschutzkabine wurde mit einer hochwertigen, doppelwandigen Außenwand ummantelt. Durch den dafür verwendeten Noppenschaum erreicht MartinMechanic außerhalb der Arbeitszelle einen Schallpegel von unter 60 Dezibel. Die Schutztore sind so hoch, dass der Werker für das Materialhandling auch mit einer Ameise ins Innere der Anlage einfahren kann. Doch das gelingt ihm nur, wenn alle Roboter stehen und der Zugang über einen speziellen Schlüssel freigegeben worden ist.
Ein Sensor erkennt die abgestellte Gitterbox mit bis zu 1000 Teilen. Aber nur, wenn der Sicherheitsbereich wieder geschlossen worden ist, kann die hydraulische Kippvorrichtung in Bewegung gesetzt werden, um die zu prüfenden Rohteile in den Vorbunker zu schütten. Nockenwellenschalter überwachen den Kippwinkel der Gitterbox. Die Kippvorrichtung hat eine Traglast von 1000 Kilogramm.
Vom Vorbunker wandern die Teile über einen Stufenförderer auf ein zweigeteiltes Zuführband, von wo sie ein Sechs-Achs-Roboter vom Typ Kuka KR8 im Line-Tracking-Verfahren nacheinander entnimmt. Die Bandgeschwindigkeit wird von einem Drehgeber erfasst, eine Kamera meldet die Lage des Bauteils. Daraus berechnet sich der Roboter, der mit einem gefederten Magnetgreifer ausgestattet ist, die Abholposition. Das Bauteil legt er teileschonend mit Hilfe einer Kunststoffhülse in eine Zwischenstation ein, wo es akkurat zentriert wird.
Hier greift ein zweiter Roboter vom Typ Kuka KR8, der eine Reichweite von 2013 Millimeter hat, nach dem Bauteil, um es in die erste Station des Prüftischs einzulegen. Um diesen Rundschalttisch wurden sechs Rüststationen angelegt, von denen vier mit einer Bildverarbeitung ausgestattet sind. Mit einem Sensorantrieb kann das Bauteil jeweils um 360 gedreht werden, um die Rundum-Daten für die Bildverarbeitung, die an einem Bildschirm mitverfolgt werden können, zu liefern.
An der zweiten Rüststation wird die Stützkonsole auf einen Gewindedorn gesetzt, um ihre Kontur abzugleichen. Außerdem wird sie auf Rostablagerungen und sonstige Verunreinigungen untersucht. Dazu wird sie viermal um 90 Grad gedreht, damit sie von allen Seiten gründlich inspiziert werden kann.
An der dritten Station wird ihre Oberfläche zweieinhalbdimensional auf Risse und Kratzer überprüft. Dazu fährt die Kamera horizontal an der Vorder- und Rückseite des Bauteils entlang.
An der vierten Station senkt sich die Kamera über die Stützkonsole, um sie im Auflichtverfahren auf ihr Spaltmaß zu testen sowie einen eventuellen Versatz und verbogene Blechlaschen aufzuspüren.
An Station 5 geht es um die Maßhaltigkeit. Hierzu hält der Schwenkgreifer das Bauteil mit der Unterseite vor die vierte Kamera.
Der dritte Roboter vom Typ Kuka KR10, der eine Reichweite von 1100 Millimeter hat, übernimmt das geprüfte Bauteil an der fünften Station und legt es, soweit es für in Ordnung befunden worden ist, nach einem festgelegten Schema in einer Gitterbox ab. Die Bauteile, die nicht in Ordnung sind, werden nach Oberflächen- und Fertigungsfehlern unterschieden. Auch hierfür gibt es passende Ablageboxen.
Für weitere Prüfmöglichkeiten oder eine spätere Beschriftung wurde die Anlage noch mit einer sechsten Reservestation ausgestattet.
Die MPK01969 wurde innerhalb von zwölf Monaten entwickelt, produziert und beim Kunden aufgebaut. Eine SPS-Mastersteuerung S71500F regelt die einzelnen Abläufe.
Mehr Informationen zu MartinMechanic:
![]() |
MartinMechanic Friedrich Martin GmbH & Co KG |
![]() |
Heinrich-Hertz-Straße 2 |
![]() |
72202 Nagold |
![]() |
Tel.: +49 (0)7452-84660 |
![]() |
Fax: +49 (0)7452-8466566 |
![]() |
E-Mail: info@MartinMechanic.com |
![]() |
www.MartinMechanic.com |
War dieser Artikel für Sie hilfreich?
![]() |
![]() |
![]() |
![]() |
![]() |
Bitte bewerten Sie diese Seite durch Klick auf die Symbole.
Zugriffe heute: 2 - gesamt: 4748.