Ein hoch produktives Präzisions-Arbeitspferd
Schnelle Fertigung mit höchster Genauigkeit
Die Anforderungen an die Hersteller von Werkzeugen für das Spritzgießen von Kunststoffteilen steigen kontinuierlich, während gleichzeitig der Preisdruck aus Billiglohnländern zunimmt. Für die Fertigung der Spritzgießwerkzeuge brauchen diese daher Werkzeugmaschinen, die sowohl hoch produktiv als auch besonders genau sind, um den Nacharbeitsaufwand senken und Kundenwünsche schnell erfüllen zu können. Zudem muss die Unterstützung durch den Maschinenhersteller „stimmen“. Ein Erfahrungsbericht.
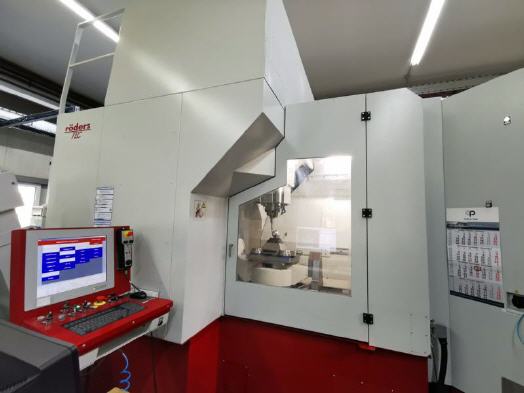
„Wir bauen Spritzgießformen zur Herstellung von Kunststoffteilen für eine ganze Reihe von Hightech-Branchen“, erläutert Marc Wiegelmann, Inhaber und Geschäftsführer der Dieter Wiegelmann GmbH in Olsberg-Bruchhausen. Er führt den 1980 von seinem Vater gegründeten Familienbetrieb mit 40 Mitarbeitern in zweiter Generation und beliefert Kunden aus der Luft- und Raumfahrt, der Elektrotechnik sowie Hersteller von Automobilen, Medizintechnik-Produkten oder Haushaltsgeräten mit anspruchsvollen Werkzeugen.
Die meisten hiervon sind für die Großserienfertigung vorgesehen und werden deshalb aus Stahl gefertigt. Für Prototypen oder Kleinserien bis zu wenigen 10.000 Stück werden jedoch auch preisgünstigere Formen aus Aluminium hergestellt. Dabei kann dank umfassender Erfahrung bei Werkstoffauswahl und Bearbeitungsverfahren sogar Spiegelglanz fast ohne manuelle Politur erzeugt werden. Dies ist u.a. bei optisch anspruchsvollen Bauteilen im Sichtbereich von Vorteil.
Entwicklungspartnerschaft
„Der Spritzgießprozess ist kompliziert und folgt sehr speziellen Gesetzen“, ergänzt Marc Wiegelmann. Geometrie und Qualität eines spritzgegossenen Bauteils entsprächen deshalb nicht immer auf Anhieb den Erwartungen des Konstrukteurs. Um negative Überraschungen zu vermeiden, stehe man den Kunden auf Wunsch mit einem Stamm erfahrener Spezialisten in den Bereichen Spritzgießen und Werkzeugbau als Entwicklungspartner zur Seite.
Die Leistungspalette reiche dabei von der Herstellbarkeitsanalyse über Füllsimulation und Verzugsanalyse bis zur Spritztechnik. Hierfür stünde den Fachleuten eine Auswahl leistungsfähiger Programme sowohl auf der Konstruktionsseite (Catia V5, Cimatron und WorkNC) als auch zur Simulation des eigentlichen Spritzgießprozesses (Simcon Cadmould) zur Verfügung.
Zu den wesentlichen Extras, die man den Kunden bieten könne, gehöre auch ein Technikum mit insgesamt sieben Spritzgießmaschinen mit Zuhaltekräften von 500 bis 16.000 kN.
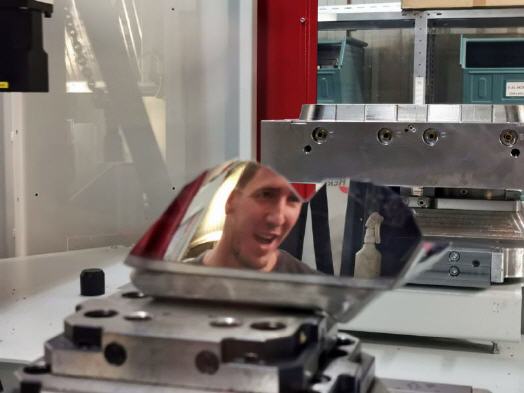
Großer Maschinenpark
„Auch im Bereich der eigentlichen Werkzeugherstellung verfügen wir über einen besonders breiten Maschinenpark“, sagt Marc Wiegelmann. Neben insgesamt sechs 3- bzw. 5Achs-Fräsbearbeitungszentren verfüge man auch über Senkerodiertechnik, eine Tieflochbohrmaschine mit Bohrtiefen bis zu 1.250 mm sowie über Polier- und Tuschiertechnik. Selbstverständlich gehöre dazu auch das erforderliche Instrumentarium an Qualitätsprüfeinrichtungen wie Koordinatenmessmaschine und optische Vermessung mithilfe von 3D-Kamerasystemen. Diese umfassende Ausstattung ermögliche auch schnelle, flexible Reaktionen bei „Feuerwehreinsätzen“. Zu solchen komme es beispielsweise bei dringenden Überarbeitungen von Spritzgießwerkzeugen, die der Anwender zuvor billig aus Fernost bezogen hatte, die aber den Produktionsanforderungen nicht entsprechen.
Entscheidung für eine Röders-Fräsmaschine
„Im Jahr 2015 fiel bei uns nach mehrjährigen Überlegungen die Entscheidung, dass wir für unser nächstes Bearbeitungszentrum einen anderen Anbieter als bisher nehmen würden“, verrät Marc Wiegelmann. Dadurch wollte man höhere Werkstückqualitäten beim Fräsen erreichen. Dies schien möglich aufgrund des Fortschritts bei den für das Fräsen eingesetzten Maschinen und auch Werkzeugen. Das neue System sollte sich einerseits zum Schruppen eignen und andererseits feinste Schlichtbearbeitungen bei hohen Anforderungen an die Oberflächengüte ausführen können, was komplette Bearbeitungen in einer Aufspannung ermöglicht.
Nach langer Suche, einem Besuch beim Hersteller sowie einer Testbearbeitung dort fiel die Entscheidung zugunsten eines automatisierten 5Achs- Fräsbearbeitungszentrums RXU 1001 DSH der Firma Röders in Soltau. Dies bedingte auch eine Abkehr vom eingesetzten Steuerungstyp bei den Fräsmaschinen. Die Lieferung erfolgte Mitte 2016.
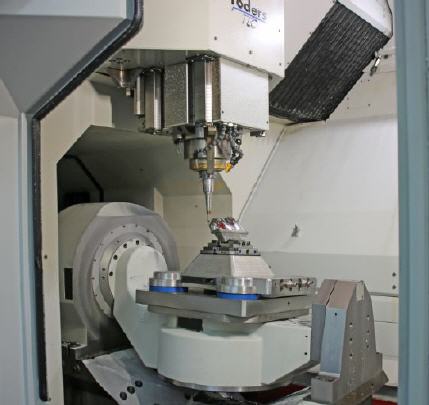
Die neue Fertigungszelle
„Die neue Fräsmaschine hat eine äußerst steif ausgelegte „Quadroguide“-Z-Achse mit insgesamt 16 Führungsschuhen auf vier an den Ecken angeordneten Schienen“, weiß Marc Wiegelmann. Diese robuste Konstruktion ermöglicht mit der gewählten HSK63F-Spindel Hochleistungs-Schruppbearbeitungen mit Messerköpfen bis zu einem Durchmesser von 25 mm bei einer Maximaldrehzahl von 30.000 1/min. Die RXU1001 erreicht dank hoch auflösender Maßstäbe und einem Regelungstakt von 32 kHz Genauigkeiten im µm-Bereich sowie höchste Oberflächengüten und kann mit Fräserdurchmessern bis herab zu 0,2 mm selbst feinste Schlichtbearbeitungen ausführen.
Somit ist die gewählte Spindel ein guter Ausgleich zwischen Steifigkeit und Drehmoment für gute Schruppleistung sowie Drehzahl und Laufruhe für optimale Schlichtergebnisse auch mit kleinsten Werkzeugen.
Das neue Bearbeitungszentrum ist mit einem vierfach-Palettenwechsler RCE2 von Röders gekoppelt, so dass mehrere Werkstücke hauptzeitparallel eingespeichert und mannlos, insbesondere nachts oder am Wochenende abgearbeitet werden können. Gesteuert wird die Zelle vom Röders Jobmanager RMSMain. Die Maschine und ihr Zusammenspiel mit der CAM-Software sind so gut, dass der Mitarbeiter nach dem Einrüsten die Maschine verlassen und anderen Aufgaben nachgehen kann – in Zeiten drängenden Personalmangels sowie nicht unerheblicher Personalkosten ein willkommener Vorteil.
Erfahrungen
„Mit der neuen Anlage und der vom Hersteller geleisteten Unterstützung sind meine Mitarbeiter und ich rundum zufrieden“, bilanziert Marc Wiegelmann. Schließlich bedingte die Umstellung vom bisher gewohnten Umfeld zur Röders eigenen, Windows-basierten RMS6-Steuerung, dass die Mitarbeiter eine weitere Steuerung erlernen und bedienen müssen. Die Unterstützung bei diesem Wechsel sei jedoch ebenso hervorragend gewesen wie bereits vorher bei der Beratung im Hause sowie bei den Testbearbeitungen. Aufgrund der einfachen Bedienbarkeit sei es kein Problem für die Bediener, neben den bisherigen Maschinen auch mit der Röders zu arbeiten, so Marc Wiegelmann.
Bei der Schulung und der späteren Beratung hätten sich die Röders-Mitarbeiter als sehr kompetent und hilfsbereit erwiesen. Zusammen mit der Maschinenlieferung waren auch Umstellungen auf der CAM-Ebene erforderlich: Um die volle Leistungsfähigkeit der Maschine und Steuerung zu nutzen wurden nicht alle bisherige NC-Programme 1:1 übernommen, sondern oft neu generiert. Hier habe Röders wertvolle Tipps gegeben, was die Umstellung der Bearbeitungsstrategien auf die Möglichkeiten der HSC-Bearbeitung und die Umgewöhnung der Mitarbeiter sehr erleichterte.
Nachdem die Programme bzw. Strategien einmal umgestellt waren, konnte die Röders-Anlage erst so richtig ihre Vorteile zur Geltung bringen. Sie sei deutlich schneller als ihre „Kollegen“, wobei dieser Vorteil von bis zu 25 % umso größer werde, je filigraner die auszuführenden Arbeiten ausfielen. Die hohe Bahngenauigkeit bedinge deutliche Verbesserungen sowohl bei der Konturgenauigkeit als auch bei der Oberflächengüte und damit weniger Nacharbeit. Auch verbrauche die Röders-Maschine dank ihrer Linear-Direktantriebe und der damit verbundenen Reibungsfreiheit deutlich weniger Strom, was einen Förderkredit zur Effizienzförderung durch die KfW-Bank ermöglichte. Ein weiterer Aspekt sei die sehr gut zu bedienende, in die Röders Steuerung integrierte Werkzeugverwaltung, der man anmerke, dass sie von Praktikern geschrieben wurde.
Zusammenfassend betont Marc Wiegelmann, dass sich seine Erwartungen beim Einstieg in das HSC-Fräsen voll erfüllt hätten. Die schnelle und präzise Zerspanung selbst harter Stähle durch Fräsen ermöglichte es, mehr und mehr Bearbeitungen vom Senkerodieren auf das schnellere und wirtschaftlichere Fräsen zu verlagern und auch den manuellen Nacharbeitsaufwand deutlich zu reduzieren. Erodiert werde inzwischen meist nur noch da, wo man nicht fräsen kann, z.B. bei sehr tiefen Taschen bzw. Rippen, oder dort, wo scharfe Innenkanten nötig sind. Auch die Entscheidung, die Maschine von Anfang an zu automatisieren, erwies sich als richtig, da hierdurch eine sehr hohe Produktivität – mit den damit verbundenen Kostenvorteilen – erreicht wurde.
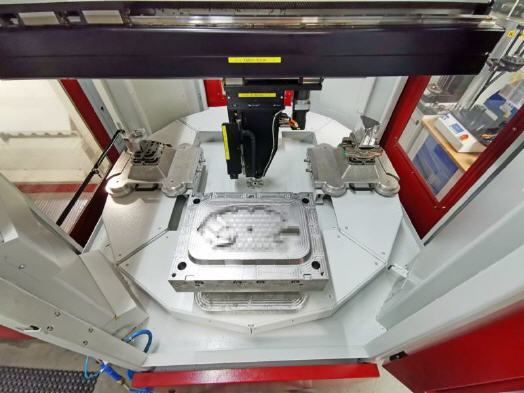
Mehr Informationen zur Röders GmbH:
![]() |
Röders GmbH |
![]() |
Gottlieb-Daimler-Str. 6 |
![]() |
29614 Soltau |
![]() |
Tel. +49 5191-603-43 |
![]() |
Fax +49 5191-603-38 |
![]() |
E-Mail info@roeders.de |
![]() |
www.roeders.de |
War dieser Artikel für Sie hilfreich?
![]() |
![]() |
![]() |
![]() |
![]() |
Bitte bewerten Sie diese Seite durch Klick auf die Symbole.
Zugriffe heute: 2 - gesamt: 4598.