ANT: Produktivität und Schnittqualität vereint
Luftfrei Wasserstrahlschneiden
Als innovativen Ansatz auf dem Gebiet des Wasser Abrasiv Suspension-Wasserstrahlschneidens hat ANT die Abrasivmittelzumischeinheit ›ConSus‹ entwickelt.
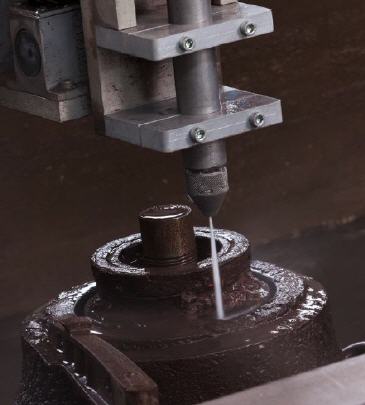
Das Wasserstrahlschneiden ist eine der wichtigsten modernen Schneidtechnologien, mit der sich nahezu alle Materialien von Gummi über Keramik bis hin zu Metall bearbeiten lassen. Hierzu trennt ein Hochdruckwasserstrahl, dem ein Abrasiv (Schleifmittel) zugesetzt wird, die Werkstücke mit Drücken von bis zu 6000 bar. Relevante Parameter sind die Härte und Stärke des Materials sowie die geforderte Qualität der Schnittkanten.
Anders als beim Laser-, Plasma- oder Thermalschneiden entsteht beim Wasserstrahlschneiden keine Hitze, die das Schneidmaterial negativ beeinflusst, sodass eine Nachbearbeitung im Regelfall entfällt. Ebenso entstehen keine Dämpfe oder Rauch, die die Gesundheit der Anwender belasten könnten. Der Wasserstrahl eignet sich auch besonders für weiche oder spröde Materialien. Als Verbrauchsmaterialien fallen lediglich Wasser und gegebenenfalls Abrasiv an. Ein Recycling des Schleifmittels ermöglicht eine weitere Senkung der Kosten und sorgt für nachhaltige Prozesse.
Verschiedene Verfahren und Weiterentwicklungen
Unternehmen, die auf der Suche nach dem für ihre Prozesse optimalen Wasserstrahlschneidverfahren sind, haben die Auswahl zwischen zwei Methoden: dem Injektionsverfahren (WAIS) und dem Suspensionsverfahren (WAS).
Wasser Abrasiv Injektion System
Bei dem bisher industriell eingesetzten Wasser Abrasiv Injektion (WAIS) System strömt Wasser unter Druck durch die Düse im Schneidkopf der Anlage. Dabei wird das Abrasivmittel durch Unterdruck („Venturi Prinzip“) eingesaugt. Hierbei wird aus der Abrasiv-Mischkammer auch eine große Menge Luft mit eingesogen. So entsteht ein turbulentes Drei-Phasen-System mit circa 95 Vol. Prozent Luft, vier Vol. Prozent Wasser und einem Vol. Prozent Abrasiv.
Wasser Abrasiv Suspension System
Als innovativen Ansatz auf dem Gebiet des Wasser Abrasiv Suspension (WAS) Wasserstrahlschneidens hat ANT die Abrasivmittelzumischeinheit ConSus entwickelt: In WAS-Systemen, die mit ConSus ausgerüstet sind, fließt ein Teil des Druckwassers über ein Bypass-Ventil in die Zumischeinheit, in der das Wasser und das Schleifmittel eine Suspension bilden. Diese wird in den Schlauch und anschließend zur Beschleunigung in die Düse gespült. Das Ergebnis ist ein zweiphasiges Strahlwerkzeug aus circa 97,5 Vol. Prozent Wasser und 2,5 Vol. Prozent Abrasiv. Durch das weltweit patentierte Schleusenverfahren wird zudem immer neues Abrasiv in die Zumischeinheit befördert, sobald ein definiertes Niveau unterschritten ist. Dies ermöglicht, ohne Unterbrechung eine kontinuierliche Suspension (Continuous Suspension) zu produzieren – ConSus.
Welche Vorteile bietet WAS?
Da die Abrasivpartikel in WAS-Systemen direkt im Wasser gebunden sind, ist der Suspensionsstrahl deutlich stabiler und präziser als der Injektionsstrahl. Damit bietet das Verfahren eine hohe Leistungsdichte bei geringer Schnittbreite. Bei WAIS hingegen kommt es durch den Luftanteil zu turbulenten Mischungsverlusten, die den Gesamtwirkungsgrad auf circa zwei Drittel reduzieren. Des Weiteren müssen Anwender bei der Wahl des Abrasivmittels bestimmte Anforderungen zum Beispiel zur Rieselfähigkeit berücksichtigen.
Versuchsreihen des Fraunhofer-Instituts für Produktionstechnologie
Das Fraunhofer-Institut für Produktionstechnologie (Fraunhofer IPT) hat die beiden Wasserstrahlschneidverfahren getestet und Versuchsreihen zu für Unternehmen relevanten Fragen durchgeführt: Die Entwicklung der Abrasivmittelgröße erlaubt Rückschlüsse auf die Schnittleistung der Partikel und die Recyclingfähigkeit. Die Versuche wurden an einem WAIS- und einem WAS-System durchgeführt. Das WAS-System setzte dabei ConSus ein.
Verringerung des Geräuschpegels
An DIN 9612 angelehnte Messungen des Fraunhofer IPT haben ergeben, dass das WAS-Verfahren mit ConSus einen deutlich geringeren Schallpegel aufweist als herkömmliche WAIS-Schneidstrahler. Selbst bei Maximaldruck von 1500 bar und 750 g Abrasiv bleibt das Suspensionsverfahren mit ConSus auf 98 dB beschränkt, während bei einem WAIS-Strahl mit einem Druck von 5000 bar und mit 500 g Abrasiv 108 dB zu verzeichnen sind. Dies entspricht einem Schallpegel Faktor 3 bei WAIS. Im realen Schneidbetrieb ergeben sich gegenüber dem Freistrahl je nach Anwendung nochmals deutlich größere Differenzen von 20 bis 25 dB.
Minimierung von Feststoffpartikeln
In einem weiteren Versuch nach DIN 33896-1 wurden die Partikelemissionen beim Zerspanen des Werkstücks gemessen, um eine etwaige Gefährdung des Anwenders durch gesundheitsschädliche Kleinstteilchen zu bewerten. Die in die Umgebung gelangende Partikelmenge wird sowohl vom Systemdruck als auch von der eingesetzten Menge des Abrasivs beeinflusst. Die Emissionsrate steigt mit zunehmender Abtragsleistung. Als Werkstoff wurde Inconel 718 verwendet, eine hitzebeständige sowie feste und zähe Nickelbasislegierung. Im relativen Vergleich zum WAS-Verfahren mit ConSus wurden beim Injektionsverfahren bis zu über 200 Prozent Feststoffpartikel emittiert (WAS mit ConSus, 1500 bar: 4 mg/cbcm; WAIS, 5000 bar: 11 mg/cbcm; jeweils 400 g Granatsand Mesh 120 pro Minute).
Schonung des Abrasivs sorgt für Wiederverwertbarkeit
Partikelemissionen sind eine Folge der Zerkleinerung des Abrasivmittels. Laut Fraunhofer IPT findet beim Injektionsverfahren mit Granatsanden Mesh 80 und Mesh 120 bereits während Durchlaufen des Strahlkopfs, vor dem Kontakt mit dem Werkstück, durch das turbulente Verfahren eine deutliche Zerkleinerung von 40 Prozent der Abrasivteilchen statt. Partikel, die durch normalen Einsatz eine Größe von weniger als 100 µm erreichen, sind im Regelfall nicht weiter verwendbar und werden entsorgt.
Dies betraf während des Tests 25 Prozent der Partikel. Im Suspensionsverfahren mit ConSus ließ sich hingegen selbst mit Mesh 120 keine nennenswerte (unter drei Prozent bei 1.000 bar) bzw. nur eine sehr geringe (unter neun Prozent bei 1.500 bar) Partikelzerkleinerung feststellen. Die Abrasivmittelgröße blieb also nahezu vollständig erhalten, was für eine gute Schneidleistung sorgt und ein nachhaltiges Abrasivstoffrecycling (bis zu 80 Prozent) ermöglicht.
WAS punktet beim Kosten-Leistungs-Verhältnis
Neben vorgenannten Vorteilen bei den Geräusch- und Partikelemissionen hat das Fraunhofer IPT in weiteren Versuchsreihen einen Vergleich der Leistung und der Kosten eines WAIS- sowie eines WAS-Systems (letzteres mit ConSus) erstellt. Neben den direkten Verbrauchskosten für Abrasivmittel, Energie, Personal, Verschleißteile, Wartung und Wasser wurden Ausgaben für die Erstanschaffung und Abschreibung berücksichtigt. Hierzu wurden beide Systeme mit nahezu gleicher hydraulischer Energie versorgt (WAIS: 20 kW; WAS: 21kW).
Höhere Schnittraten mit WAS
Im Vergleich zum Injektionsstrahl besitzen die Abrasivteilchen im Suspensionsstrahl eine höhere kinetische Energie. Gleichzeitig ist der Strahl stabiler und präziser ausgerichtet. In der Folge erzielt das WAS-Verfahren deutlich gesteigerte Schnittraten sowie größere Schnitttiefen (3-fach und mehr!).
WAS-Systeme weisen gegenüber WAIS-Systemen auf den ersten Blick zwar höhere Anschaffungs- und Betriebskosten auf, diese werden jedoch durch die deutlich höhere Schnittrate des Suspensionsstrahls mehr als ausgeglichen. So ergeben sich Einsparungen der laufenden Kosten pro Schnittmeter von bis zu 50 Prozent.
Zusätzlich zu den Versuchsreihen des Fraunhofer IPT sollten Unternehmen einen weiteren wichtigen Aspekt beachten, der Kosten und Nachhaltigkeit betrifft. Die Entsorgung von verwendetem Schleifmittel ist zeit- und kostenintensiv. Die Verbrauchskosten von WAS-Systemen lassen sich daher signifikant senken, indem die zusammen mit dem Materialabtrag im Schneidwasser enthaltenen Abrasivmittel aufbereitet werden. Die von ANT entwickelte Abrasiv Recycling Unit (ARU) beispielsweise ermöglicht eine Inline-Aufbereitung von bis zu 80 Prozent. Anschließend kann das Rezyklat automatisch mit neuem Abrasiv gemischt und ConSus direkt wieder zugeführt werden. Partikel, die aufgrund ihrer Größe zur Wiederverwendung ungeeignet sind, werden automatisch aussortiert.
Der Einsatz von Wasser Abrasiv Suspension Systemen mit ConSus bietet Anwendern viele und entscheidende Vorteile gegenüber herkömmlichen Wasser Abrasiv Injektion Systemen. Der zweiphasige Suspensionsstrahl aus Wasser und Abrasivmittel sorgt für verringerte Schall- und Partikelemissionen beim Wasserschneiden. Die deutlich höhere Abtragleistung der WAS-Systeme überwiegt bei weitem die zunächst höheren Betriebskosten (per h) von WAS-Systemen.
Vor allem bei gesteigerten Schnitttiefen sowie der Bearbeitung hochfester Werkstoffe ergeben sich technologische und wirtschaftliche Vorteile für die Unternehmen. Hinzu kommt, dass das traditionelle Injektionsverfahren auch bei Drücken von bis zu 6000 bar (Limit) keine wesentlichen Leistungssteigerungen mehr erzielen können. So steigt bei höheren Drücken der Verschleiß des WAIS-Systems und sinken die Lebensdauer und Zuverlässigkeit der Komponenten signifikant.
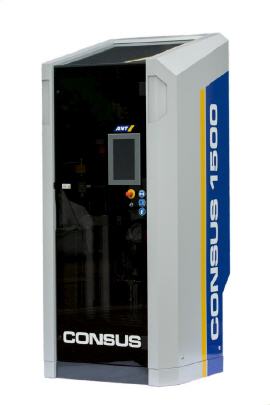
Mehr Informationen zur ANT AG:
![]() |
ANT Applied New Technologies AG |
![]() |
Hinter den Kirschkaten 32 |
![]() |
23560 Lübeck |
![]() |
Tel.: +49 (0)451 5 83 80-0 |
![]() |
Fax: +49 (0)451 5 83 80-99 |
![]() |
E-Mail: info@ant-ag.com |
![]() |
www.ant-ag.com |
War dieser Artikel für Sie hilfreich?
![]() |
![]() |
![]() |
![]() |
![]() |
Bitte bewerten Sie diese Seite durch Klick auf die Symbole.
Zugriffe heute: 2 - gesamt: 4631.