Hochproduktive Großserienfertigung
Chirurgische Instrumente HSC-Fräsen
Chirurgische Instrumente sind Hochpräzisionsprodukte, die mit größter Sorgfalt in meist kleineren Stückzahlen gefertigt werden. Die Strukturen und die Ausrüstung der hierauf spezialisierten Hersteller sind daher vor allem auf hohe Umrüstflexibilität ausgelegt. Für Einmalprodukte in hohen Stückzahlen musste deshalb eine separate Prozesskette aufgebaut werden. Kernstück ist ein Doppelspindler der Schwäbische Werkzeugmaschinen GmbH (SW) mit sehr hoher Wiederholgenauigkeit.
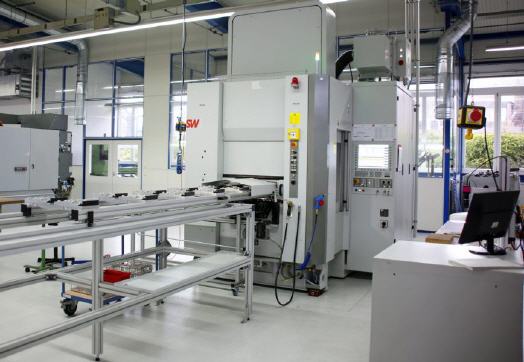
„Im Bereich der Herstellung feinmechanischer chirurgischer Instrumente sind die Anforderungen hoch und der Wettbewerb hart“, weiß Frank Pauschert, Regionaler Vertriebsleiter der SW Schwäbische Werkzeugmaschinen GmbH in Waldmössingen. Zu seinen Kunden gehört auch ein Unternehmen aus diesem Bereich, das sich seit seiner Gründung Anfang der 1980er Jahre aus bescheidenen Anfängen zu einem mittelständischen Betrieb mit rund 130 Mitarbeitern entwickelt hat.
Hergestellt werden aktuell rund 1.000 unterschiedliche Gerätschaften für eine Vielzahl von Einsatzbereichen in der Chirurgie. Alle Instrumente werden fertig und einsatzbereit ausgeliefert. Die aus hochwertigen biokompatiblen Werkstoffen wie Edelstählen bestehenden Einzelteile werden durch spanende Bearbeitung hergestellt. Ungeachtet des Einsatzes moderner NC-gesteuerter Werkzeugmaschinen ist der Anteil manueller Tätigkeiten am Fertigungsprozess recht hoch, denn solche Instrumente bestehen aus bis zu 40 unterschiedlichen Bauteilen, die veredelt, oberflächenbehandelt und mit größter Sorgfalt von Hand montiert werden.
Zudem werden sie häufig in zahlreichen Varianten hergestellt. Das bedingt kleine Serienlosgrößen, weshalb die Fertigungsanlagen vor allem sehr flexibel umrüstbar sein müssen. Wegen der außerordentlichen Vielfalt der Varianten besteht auch keine Möglichkeit, auf Lager zu arbeiten und so die Kosten durch Fertigung in größeren Losen zu senken.
Zukunftsstrategie: Ein anspruchsvolles Einmal-Produkt
Da der Hersteller bisher keine eigenen Produkte herstellte, wird er von Kunden, die häufig über große Marktmacht verfügen, ständig preislich mit dem zahlreich vorhandenen Wettbewerb verglichen. Dies begrenzt die Ertragskraft und damit auch die künftigen Wachstumsmöglichkeiten. Zur langfristigen Sicherung der Zukunft wurde vor rund zwei Jahren beschlossen, in ein äußerst anspruchsvolles Großserienprojekt einzusteigen: Die Herstellung eines Einmal-Werkzeugs für die Neurochirurgie, das so häufig eingesetzt wird, dass davon jährlich sechsstellige Stückzahlen benötigt werden.
Hierbei handelt es sich um eine Art Pinzette aus Aluminium, die es gestattet, Gewebebestandteile zu ergreifen und dabei zugleich kleinere Blutungen durch elektrische Impulse zu stillen. Zudem wurden in die beiden Arme der Pinzette winzige Schläuche integriert, durch die eine Spülflüssigkeit in den Operationsbereich geleitet werden kann. Trotz seines einfach anmutenden Aussehens ist das Werkzeug sehr aufwendig in der Herstellung und erfordert zahlreiche mechanische ebenso wie manuelle Arbeitsgänge, wobei die üblichen strengen Qualitätsvorschriften einzuhalten sind.
Viele der Arbeitsgänge müssen unter dem Mikroskop durchgeführt werden. Der Aufbau der entsprechenden Prozesskette erfordert umfassende Entwicklungsanstrengungen sowie Investitionen in Maschinen und Spezialausrüstungen. Aktuell werden hierfür zusätzliche Mitarbeiter eingestellt und qualifiziert.
Ein Bearbeitungszentrum mit der Leistung eines Sportwagens
Ausgangspunkt und Kernstück der Prozesskette ist ein automatisiertes Doppelspindel-Bearbeitungszentrum BA 321 von SW. Die Anlage verfügt über einen Arbeitsbereich von 300 x 500 x 375 mm je Spindel. Die mit HSK A63-Schnittstelle ausgerüsteten Spindeln erreichen bis zu 17.500 min-1, die Span-zu-Span-Zeiten liegen bei 2,5 s. Das Werkzeugwechselsystem hat eine Kapazität von 2 x 20 bis maximal 2 x 60 Plätzen. Mit dieser Anlage werden die Pinzettenhälften aus hochwertigem Aluminium gefräst. Sie verfügt über eine maßgeschneiderte Automatisierung für die Zuführung des Materials sowie die Abfuhr der Frästeile.
Sie ist nur für ein begrenztes Teilespektrum vorgesehen, erreicht dafür jedoch eine Produktivität, welche weit über derjenigen der anderen Fräszentren im Hause liegt. Mit seiner horizontalen, doppelspindligen Ausführung liefert das neue Bearbeitungszentrum in nur drei Minuten zwei komplett fertig gefräste Pinzettenhälften ab, und das dank der Automatisierung weitgehend mannlos rund um die Uhr. Zudem überzeugte die Maschine dank ihrer Wiederholgenauigkeit und damit der Qualität der gefertigten Teile. Auch übertrifft sie die Durchsatzleistung der sonstigen im Hause installierten Bearbeitungszentren deutlich.
Entwicklungspartnerschaft bei der Automatisierung
Die Entscheidung für SW fiel zunächst deshalb, weil die Produktivität des Doppelspindel-Konzepts überzeugte. Ein weiterer Aspekt waren die einwandfreien Referenzen sowie die relative Nachbarschaft, was kurze Reaktions- und Reisezeiten sowohl bei der anstehenden gemeinsamen Entwicklung der Automatisierung als auch bei eventuellen Serviceeinsätzen versprach.
Die ersten Kontakte im Sommer 2017 mündeten in eine partnerschaftliche Zusammenarbeit, in deren Verlauf die Möglichkeiten einer Automatisierung der Bearbeitungsprozesse abgeklärt wurden. Anschließend erfolgte die gemeinsame Konzipierung und Entwicklung einer Sondermaschine auf der Basis des Modells BA 321. Als Rohmaterial dienen spezielle Strangpressprofile in drei Abmessungsvarianten.
Die Pinzettenhälften werden aus den Profilen herausgearbeitet und erst im letzten Arbeitsgang durch Sägen abgetrennt. Auf diese Weise werden Spannprobleme mit den äußerst schlanken und filigranen Pinzettenhälften von vornherein umgangen.
Der abschließende Sägeschnitt wird so gesetzt, dass ein minimaler Restgrat erhalten bleibt, der ein Herunterfallen der Teile verhindert. Anderenfalls könnten die sehr filigranen Spitzen der Pinzette beschädigt werden. Die Entnahme erfolgt mithilfe spezieller Adapter, die aus dem Werkzeugmagazin in die Spindeln eingewechselt werden. Mit ihrer Hilfe werden die Pinzettenteile gehalten und vom verbliebenen Restgrat gebrochen. Anschließend werden sie vereinzelt auf einer Transportschublade abgelegt und per Förderband zur Entnahmestation transportiert, wo sie für die nächsten Arbeitsgänge manuell in Korbgestelle eingesetzt werden.
„Die gemeinsame Entwicklung dieser Automatisierung war dank der Professionalität beider Teams sehr effizient“, erinnert sich Frank Pauschert.
Problemlose Lieferung und Inbetriebnahme
Die gemeinsame Entwicklung und Projektierung sowie der Aufbau und die Erprobungen bis zur Abnahme dauerten bis zum Juni 2018. In diesem Zusammenhang wurden auch die benötigten Werkzeuge realisiert und ein erstes NC-Programm auf der Basis von Vorgaben den Kunden erstellt. Nach erfolgreicher Abnahme wurde die Anlage am Einsatzort in Betrieb genommen. Seitdem erfolgten Tests sowie die Programmierung der insgesamt 18 Produktvarianten. Das eigentliche Ramp-Up begann im November 2018, seit März 2019 läuft die Produktion bereits im 24/6-Betrieb, wobei die Anlage inzwischen teils bis zu einer Woche ohne jegliche Eingriffe – bis auf Zufuhr von Material und Abfuhr von fertig gefrästen Teilen – durchläuft.
Zufrieden mit Qualität, Support und Service
Dank der Produktionsbegleitung „life startUp“ in der ersten Woche nach der Inbetriebnahme konnte sich der Mitarbeiter schnell in die Bedienung einfinden und selbstständig mit der Maschine arbeiten. Mit „life data“, einem Online-Service von SW, ist die Maschine ständig online an SW angebunden, wo wesentliche Maschinenparameter nonstop überwacht werden. Bei Problemen werde sofort in Aktion getreten. Diese Hilfe sei auch bereits erfolgreich genutzt worden, indem der Maschinenbediener via Ferndiagnose unterstützt wurde. Als sehr hilfreich habe sich auch „life help“ erwiesen: Wenn es mal zu Problemen kam, habe es sofort schnelle und sehr kompetente Beratung gegeben, und erforderlichenfalls war der Servicemitarbeiter manchmal innerhalb von weniger als einer Stunde zur Stelle. Ohne diesen Service hätte vieles nicht geklappt oder viel länger gedauert.
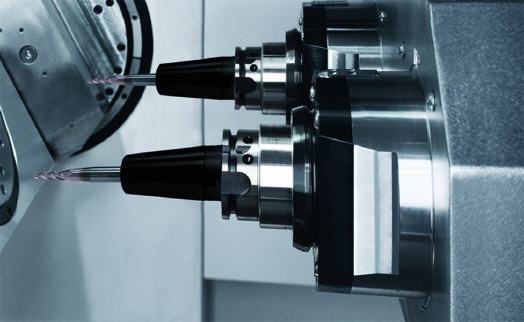
Mehr Informationen zu SW:
![]() |
Schwäbische Werkzeugmaschinen GmbH |
![]() |
Seedorfer Strasse 91 |
![]() |
78713 Schramberg-Waldmössingen |
![]() |
Tel.: +49 (0) 7402/74-0 |
![]() |
Fax: +49 (0) 7402/74-211 |
![]() |
E-Mail: info@sw-machines.de |
![]() |
www.sw-machines.de |
War dieser Artikel für Sie hilfreich?
![]() |
![]() |
![]() |
![]() |
![]() |
Bitte bewerten Sie diese Seite durch Klick auf die Symbole.
Zugriffe heute: 3 - gesamt: 4611.