Effiziente Automatisierung von Montageaufgaben
Ringrundschalttische von Nexen
Die Vorlaufzeiten für Schalttische, Linearantriebe, Roboteranlagen und weitere Komponenten haben sich verlängert. Je nach Größe und Komplexität können Lieferzeiten für Linearführungen 20 bis 26, für Roboteranlagen 14 bis 20 und für Schalttische acht bis zwölf Wochen betragen. Nexen sorgt hier für Entlastung.
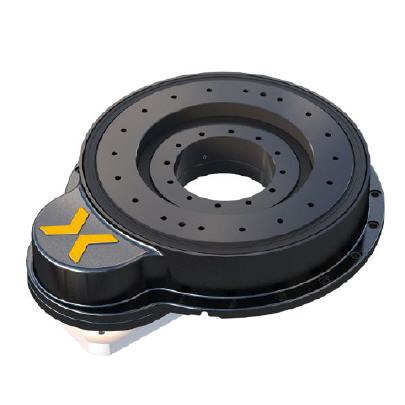
Die Frage der Vorlaufzeiten ist für Systemintegratoren wesentlich. Konstruktion und Herstellung einer automatische Montageanlage erfordern Zeit: ein einfaches Projekt ca. 12 bis 14, ein komplizierteres 48 bis 52 Wochen. Bei einem großen Projekt werden etwa 25 Prozent für die Mechanik- bzw. Elektrokonstruktion und Anschaffung von Teilen mit größeren Vorlaufzeiten verwandt. Jeweils weitere 25 Prozent für die tatsächliche Herstellung der Maschine, für die Fehlerbeseitigung an der Anlage und schließlich für Produktionstestlauf, Demontage, Versand, Vor-Ort-Montage und Schulungsmaßnahmen. Alles, was diesen Laufplan verkürzt und eine schnellere Vermarktung des Produkts ermöglicht, ist willkommen. Die Lieferzeit ist also bei der Auswahl der Automatisierungslieferanten ein wichtiges Entscheidungskriterium.
Die neue CRD MR-Reihe von Nexen baut auf der CRD-Serie präziser Ringrundschalttische auf. Neben neuen Vorzügen bietet sie auch weiterhin alle Vorteile des bewährten Rollen-Ritzel-Antriebs: Spielfreiheit, hohe Präzision und Drehmomentfähigkeiten sowie Beschleunigung, Leichtgängigkeit und kaum Wartungsbedarf.
Eines der neuen Merkmale ist Flexibilität: Bisher waren CRD Ringrundschalttische in drei Versionen erhältlich, je nach Anwendung, für hohe Drehzahlen oder für hohe Drehmomente oder für beides: der CRD PL besitzt ein präzises, spielarmes Planetengetriebe für hohe Drehmomente und Drehzahlen und eine flexible Getriebeübersetzung; der CRD HG ein spielfreies Harmonic-Getriebe für hohe Drehmomente und niedrige Drehzahlen und eine hohe Getriebeübersetzung; der CRD DD hat einen spielfreien Direktantriebsmotor für hohe Drehzahlen und mittlere Drehmomente.
Die CRD MR-Serie bietet eine vierte Option: ein eigener Motor bzw. Getriebe für den Antrieb. Einerseits werden dadurch Kosten erheblich reduziert. Andererseits ist der Ringrundschalttisch innerhalb von nur drei bis vier Wochen lieferbar, die Hälfte der Zeit, die für eine herkömmliche kurvengetriebene Version erforderlich ist. „Die kundenspezifische Antriebsseite der CRD MR-Lösung unterstützt die Montage einer Vielzahl von Motoren und Getriebe mit Abtriebswelle“, sagt Broc Grell, Anwendungsingenieur bei Nexen.
Durch die hohe Übersetzung zwischen Rollenritzel und Zahnkranz ist der Antrieb des Systems direkt über einen Servomotor oder mit einem Schrittmotor möglich. So entfallen Kosten für ein Reduktionsgetriebe. Bei Hochlastanwendungen kann für den Anlagenantrieb ein Getriebe und ein Motor verwendet werden. Zudem werden die aus dem Rollenritzel-Zahnkranz-Antrieb resultierenden Lasten vollkommen aufgenommen, wodurch die Motor- bzw. Getriebewelle keinen radialen Kräften ausgesetzt ist. Somit entfällt die Notwendigkeit, das Reduktionsgetriebe bei Hochlastanwendungen leistungsstark und kostenintensiv auszuführen. Im Ergebnis schlagen kürzere Konstruktions- und Montagezeiten zu Buche.
„Durch die höhere Übersetzung ist der Antrieb höherer Trägheitslasten auf Abtriebsseite mittels eines kleineren Motors auf Antriebseite möglich“, erklärt Isaac Klaehn, Konstruktionsleiter bei Nexen für Motion Control-Produkte. „Der Kunde erhält hierdurch ein Plus an Flexibilität“. Die Ritzel-Zahnkranz-Übersetzung beim Modell CRD PL 250 liegt beispielsweise bei 3,8:1, beim CRD MR 250 hingegen bei 12,5:1. Da zwischen dem Übersetzungsverhältnis und der abtriebsseitigen Trägheit eine umgekehrte quadratische Beziehung besteht, ist eine Steigerung von 3,8 auf 12,5 schon signifikant. Eine 50 kg-Last ist durch 156,25 besser teilbar als durch 14,44.
„Wird das Übersetzungsverhältnis von der Antriebsseite zur Abtriebsseite erhöht, muss sich die Drehzahl auf Antriebsseite ebenfalls erhöhen, um die gleiche abtriebsseitige Drehzahl zu erzielen“, erklärt Klaehn. „Durch eine entsprechende Konstruktionsleistung konnten die Höchstdrehzahlen des Schalttisches beibehalten werden. Unsere CRD MR Ringrundschaltische besitzen das Kapazitäts- und Drehzahlvermögen der ursprünglichen Modelle, trotz Steigerung des Übersetzungsverhältnisses.“
Auch die neuen CRD MR Modelle besitzen eine große Mittenöffnung, damit Kabeldurchführungen, Robotersysteme, Inspektionskameras und weitere Vorrichtungen in der Mitte des Drehtellers vorgesehen werden können. Dies führt zu einer Reduzierung des Bauraums und zu einer effizienten, übersichtlichen Maschinenkonstruktion. Alternativ kann die Mittenöffnung auch frei bleiben. „Ein aktuelles Projekt sieht mehrere, außen angeordnete Arbeitsstationen vor. Ist das Werkstück fertig bearbeitet, wird es ins Zentrum geleitet“, sagt Klaehn. „Ein darunter liegendes Transportband sorgt für den Transport zu einer Verpackungslinie.“
Drei Modelle, drei Größen
Mit Lochkreisdurchmessern von 150, 250 und 350 mm stehen für die CRD MR-Serie drei Größen zur Verfügung, die zwei letzteren als Ersatzeinheiten für die ursprünglichen Modelle CRD 250 und CRD 350. Mit den Präzisionsringantrieben deckt das Produktportfolio im Schalttisch-Bereich nun Durchmesser von 500 bis 1500 mm ab.
Die CRD MR-Serie besteht aus drei Modellen und bietet mehr Flexibilität: Das CRD MRS ist vollständig abgedichtet und wird in Schutzart IP65 geliefert. Das CRD MRG ist geschützt, aber nicht abgedichtet. Trotz reduziertem Innenlebenschutz bietet es weniger Gesamtwiderstand als bei einem komplett abgedichteten System sowie mehr Effizienz; auch der Motor muss weniger Drehmoment aufbringen. Das CRD MRO ist für Anwendungen, die keine abgedichteten oder geschützten Einheiten benötigen. „Dank der neuen Produktserie muss lediglich das gekauft werden, was auch tatsächlich benötigt wird“, sagt Klaehn.
Je nach Größe liegt die Höchstdrehzahl für alle drei Modelle zwischen 161 und 304 U/min. Hohe Schaltpräzision wird mit einer unidirektionalen Positioniergenauigkeit von 59 bis 31 arcsec (Winkelsekunden) und einer unidirektionalen Wiederholgenauigkeit von 9,8 bis 5,2 arcsec erreicht. Im Gegensatz zu anderen Antriebsystemen herrscht hier Spielfreiheit zwischen Motor und angetriebener Last.
Anwendungen im Blick
Wie auch die anderen Ringantriebsprodukte von Nexen werden die CRD MR-Systeme zur Aufnahme einer angelegten Last für gewöhnlich liegend montiert. Sie sind die perfekte Lösung für präzise Rundtaktanwendungen, z.B. Werkzeugmaschinen, Halbleiterproduktion, Robotersysteme, automatisches Schweißen, Medikamentenverpackung, Montage- und Schneidanlagen. Die Rundschalttische werden sogar in nichtindustriellen Anwendungen eingesetzt, z.B. in der Bühnentechnik.
Hier weitere Anwendungsbeispiele: Ein Pharmaunternehmen verwendet einen Ringrundschalttisch CRD MR 150, um Fläschchen schnell und unkompliziert unter einem Dosiergerät zu positionieren. Der kompakte Bauraum ist ideal für die Laborarbeit. Die große Mittenöffnung ermöglicht eine mittige und platzsparende Anordnung des Dosiergeräts in der Schaltscheibe. Eine Maschinenwerkstatt setzt ein CRD MR-Modell ein, um Teile zur externen Verarbeitung präzise zu positionieren. Bei diesem Einsatzbeispiel ist ein leichtgängiger und präziser Bewegungsablauf wichtiger als hohe Drehzahleigenschaften. In einem anderen Anwendungsfall wird der Ringrundschalttisch zur Positionierung von Metallteilen eingesetzt, die dann von einem Roboter automatisch geschweißt werden.
Im Gegensatz zu Schalttischen anderer Hersteller können die Ringantriebsprodukte von Nexen zur Aufnahme einer hängenden Last in umgekehrter Position oder vertikal montiert werden, auch bei der CRD MR-Serie, die beispielsweise in einer robotisierten Schweißanlage als Drehzapfen zur Teile-Positionierung eingesetzt wird. Auch hier kommt die Mittenöffnung zum Tragen. Die Schweißpistole durchquert diese, um im Innern der sich drehenden Montagevorrichtung eine Schweißnaht anzubringen.
Vorteil eines Ringantriebs
Der Schlüsselfaktor für die Leistungsfähigkeit der Nexen Ringrundschalttische, auch der CRD MR-Serie, ist das innovative Rollen-Ritzel-System RPS, das ursprünglich für lineare Bewegungssysteme konzipiert wurde.
Das RPS-System ist ein patentiertes Linearantriebskonzept, dass die besten Eigenschaften bestehender Technologien miteinander kombiniert und existierende Defizite größtenteils beseitigt. Das RPS wandelt Drehbewegung in Linearbewegung um. Es entwickelt das bisherige Ritzel-Zahnstangen-Konzept weiter und ersetzt die Stirnradverzahnung durch gelagerte Rollen, die mit der Zahnstange in einem einzigartigen Zahnprofil in Eingriff stehen. Statt der Gleitreibung herkömmlicher Ritzel-Zahnrad-Systeme sorgen die Rollen für eine leichtgängige Rollreibung und wandeln eine Drehbewegung mit 99-prozentiger Effizienz in eine Linearbewegung um.
Dank des Zahnprofils der Zahnstange greifen stets zwei Rollen gegenüberliegend und belastet ein und sorgen so für Spielfreiheit. Durch die ineinandergreifende Geometrie erreichen die Rollen die Stirnflächen der Zähne auf einem tangentialen Pfad und rollen diese Flächen dann gleichmäßig ab. Der Kontakt zwischen Rollen und Zähne erfolgt nicht abrupt sondern gleichmäßig. Geräuschbildung, Vibrationen und Zahnverschleiß werden hierdurch reduziert. Zudem bietet das RPS-System eine hohe Positioniergenauigkeit, vermeidet kumulative Fehler, sorgt für Geschwindigkeitsstabilität und hohe Geschwindigkeiten. Es besticht durch hohe Festigkeit, geringen Wartungsbedarf, Korrosionsbeständigkeit und eine hohe Lebensdauer. Mechanische Blockaden treten nicht auf, da die Ritzelrollen an verschiedenen Zahnflanken gleichzeitig und entgegengesetzt eingreifen.
Für einen Ringantrieb wird die lineare Zahnstange durch einen Zahnkranz ersetzt. Statt die Zahnstange von einer Seite zur anderen zu bewegen, versetzt das Ritzel nun den Zahnkranz in Drehbewegung. Die Achsen des Ritzels und des Zahnkranzes verlaufen parallel. Um ein drehendes Indexierungssystem zu erhalten, wird eine kreisförmige Platte auf den Zahnkranz geschraubt.
Anders als kurvengetriebene Ringrundschalttische können Ringantriebe an jeder inkrementellen Position starten und stoppen. Das Bewegungsprofil kann durch das Aufladen eines neuen Servoantrieb-Programms verändert werden. Der Ringantrieb ermöglicht zudem an jedem Punkt eine maximale Beschleunigung bzw. Verzögerung, ohne die Gefahr einer Systembeschädigung.
Mehr Informationen zum Nexen-Vertriebspartner:
![]() |
Nexen-Vertriebspartner in Deutschland: |
![]() |
LTK Lineartechnik Korb GmbH |
![]() |
Düsseldorfer Straße 7 |
![]() |
71332 Waiblingen |
![]() |
Tel.: 07151 93700 0 |
![]() |
Fax: 07151 93700 50 |
![]() |
E-Mail: info@ltk.de |
![]() |
www.lineartechnik-korb.com |
War dieser Artikel für Sie hilfreich?
![]() |
![]() |
![]() |
![]() |
![]() |
Bitte bewerten Sie diese Seite durch Klick auf die Symbole.
Zugriffe heute: 2 - gesamt: 4394.