Sphärische Teile in kurzen Taktzeiten
SpheroStar von Thielenhaus Microfinish
Auf Basis der Höchstpräzisions-Werkzeugmaschine Sphero hat Thielenhaus Microfinish eine hocheffiziente Zwei-Schritt-Lösung entwickelt, die den gesamten Feinstbearbeitungsprozess von sphärischen Werkstücken in kurzen Taktzeiten ausführt.
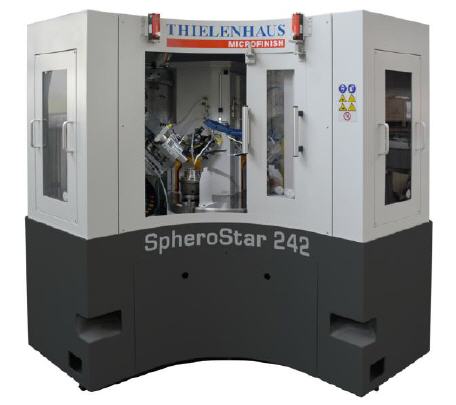
Die SpheroStar verfügt über zwei um bis zu 90 Grad automatisch schwenkbare Werkzeugspindeleinheiten, so dass stets die für den jeweiligen Prozess optimalen Bearbeitungspositionen gewählt und nicht nur sphärische, sondern – mit optionalen Querschlitten – sogar auch plane Oberflächen erzeugt werden können. Die Einheiten sind vertikal angeordnet und für schnelles Umrüsten gut zugänglich.
Auf der ersten Station wird die Maschine von einem Handling-Roboter taktzeitneutral beladen und später nach der Bearbeitung wieder entladen. Der Rundtisch taktet dann in die Station 2, auf der das Werkstück axial ausgerichtet wird. Das Vorfinishen erfolgt in-process-messgesteuert (IPM) auf Station 3, das Fertigfinishen mit flexiblem Stein auf Station 4. Auch diese Operation ist IPM-überwacht. Für beide Bearbeitungsschritte kommt eine MicroSens-Kraftsensorik mit Werkstück-Kontakterkennung und Steinverschleiß-Kompensation zum Einsatz.
Das eingespannte Werkstück rotiert bei der Bearbeitung mit einer Drehzahl von bis zu 4.500 Umdrehungen pro Minute. In Verbindung mit einer entsprechenden Kontur der Microfinish-Werkzeuge werden so die sphärischen Flächen prozesssicher erzeugt. Die Taktzeit beträgt in Abhängigkeit von der Vorbearbeitung nur 12 bis 13 Sekunden, so dass die Maschine gut in effiziente Produktionslinien eingebunden werden kann.
Da die wichtigsten Baugruppen von bewährten, bereits lange im Markt befindlichen Plattformen stammen, ist eine hohe Ausfallsicherheit gegeben. So kommt der Rundtisch von der NanoStar, die Spindeleinheiten von der Sphero und die Futter sowie die Spannsysteme von der MicroStar.
Mit der SpheroStar lassen sich die Oberflächentopografie, die Rundheit der Sphäre, der Kugeldurchmesser und die Dichtflächen bearbeiten. Darüber hinaus ermöglicht die Verbesserung der Traganteile die Erfüllung tribologischer Anforderungen. Durch wenige Einrichtmaßnahmen lässt sich die Maschine von einer Außen- auf eine Innenbearbeitung und damit z. B. von Kugel auf Dichtring oder Kalotte umstellen. Da das Werkstück bis zur kompletten Fertigstellung in der Aufnahme verbleibt, kann der Bedienereinfluss reduziert und ein Fehler durch erneutes Spannen nicht auftreten. Die Prozess-Wiederholbarkeit steigt dadurch erheblich.
Auf der ergonomisch gestalteten Maschine können Werkstücke bis zu einem Durchmesser von 75 mm bearbeitet werden. Sie kommt beispielsweise im Automotive-Bereich bei der Bearbeitung von Gelenkköpfen von Radaufhängungen und Lenkungsteilen zum Einsatz, die einen sehr hohen Freiheitsgrad und große Beweglichkeit für die damit verbundenen Baugruppen haben müssen. Auch für Ventile in der Chemieindustrie, durch die aggressive oder sehr heiße Medien gefördert werden, lassen sich metallisch dichtende Ventilkugeln und Sitzringe mit einer sehr hohen Geometrie- und Oberflächengenauigkeit bearbeiten.
Ein weiteres Beispiel stellen Axialkolbenpumpen dar, die in allen Bereichen der Hydraulik benötigt werden. Der Axialkolben hat am Ende eine kugelförmige Gleitfläche und muss für einen sicheren Betrieb unter höchsten Belastungen – wie z. B. in der Luftfahrt – eine extrem hohe Formgenauigkeit von 1 µm und kleiner aufweisen.
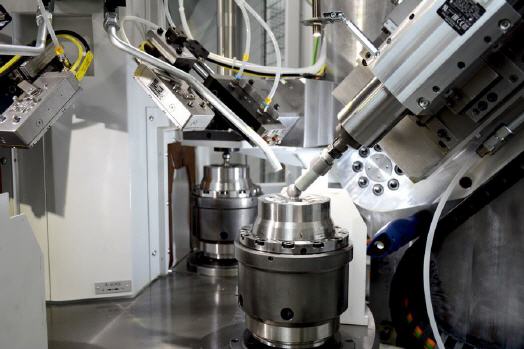
Mehr Informationen zu Thielenhaus:
![]() |
Thielenhaus Technologies GmbH |
![]() |
Schwesterstraße 50 |
![]() |
42285 Wuppertal |
![]() |
Tel.: 0202481-0 |
![]() |
Fax: 0202450445 |
![]() |
www.thielenhaus.com |
War dieser Artikel für Sie hilfreich?
![]() |
![]() |
![]() |
![]() |
![]() |
Bitte bewerten Sie diese Seite durch Klick auf die Symbole.
Zugriffe heute: 4 - gesamt: 4612.