Mit langem Werkzeug zur Serienfertigung
Die G550 und die G750 von Grob im Praxiseinsatz
Wie schaffe ich den Schritt von der Unikat-Fertigung hin zur industrialisierten Serienfertigung mit ihren automatisierten Abläufen? Fragen, die sich die oberfränkische Werkzeugbau Siegfried Hofmann GmbH bei der Fertigung von Baukammern für 3D-Drucker stellte. Eine Erfolgsgeschichte, die mit GROB-Universalmaschinen geschrieben werden sollte.
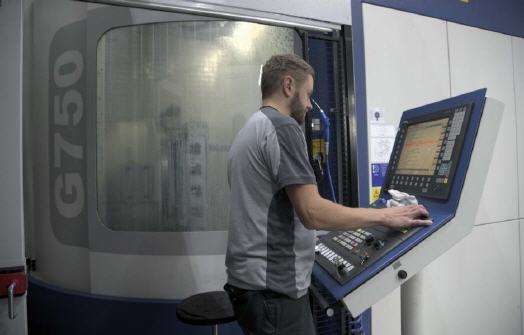
Die vor über sechs Jahrzehnten gegründete Werkzeugbau Siegfried Hofmann GmbH, mit ihrer intensiven Forschungs- und Entwicklungsarbeit, ist stets auf der Suche nach Innovationen und besten Lösungen für ihre Kunden. Und das mit großem Erfolg. Als es aber vor etwa fünf Jahren darum ging, die Fertigung des Kernstücks eines 3D-Druckers zur Industrialisierung weiter zu entwickeln, war zunächst guter Rat teuer. Bereits seit Jahren wurden bei Hofmann jährlich etwa fünf bis zehn 3D-Drucker quasi in Handarbeit gebaut. Das Kernstück dieser Drucker ist die sogenannte Baukammer, also der Raum, in dem der 3D-Druck stattfindet.
In dieser etwa 700 mm tiefen Kammer fährt ein Stempel auf und ab, vergleichbar mit einem Kolben in einem Zylinder eines Verbrenner- Motors. Dies alles muss hoch genau erfolgen und insbesondere die Oberfläche darf keine Absätze oder Unebenheiten besitzen. So wurden in der Vergangenheit exakt diese Unebenheiten in den Kammern mit sehr viel Aufwand herausgefräst und mit noch mehr Aufwand händisch nachgearbeitet.
Auf dem Weg zur Industrialisierung
Doch irgendwann war man sich bei Hofmann im Klaren, dass durch den wachsenden Markt des 3D-Drucks auch die Drucker-Herstellung industrialisiert werden wird und somit auch die Anforderungen an die Fertigungsabläufe wachsen würden – also automatisiert werden, um höhere Stückzahlen zu generieren. Das Ganze natürlich wirtschaftlich und idealerweise aufgrund der größeren Stückzahlen auch günstiger und – besonders wichtig – bei gleicher Qualität.
Mit dem Basiswissen für die Herstellung dieser Kammern, wie Preis, Dauer und Aufwand beim Finishing, hat man sich bei Hofmann auf den Weg gemacht, eine passende Maschine für die Fertigung der tiefen Baukammern zu finden. Dabei wurden unterschiedliche Szenarien durchgespielt. So haben die Hofmann-Techniker nicht ausgeschlossen, diese Kammern eventuell ganz anders herzustellen. Nicht zu fräsen, sondern zu ziehen oder zu pressen, was schon allein deswegen zum Scheitern verurteilt gewesen wäre, weil sie sich dann auf eine Geometrie festlegen hätten müssen, die nicht mehr so einfach änderbar wäre.
Aufgrund des hohen Spanvolumens, das beim Fräsen aus dem Vollen der riesigen Baukammern entstand (ca. 90 Prozent des Materials werden zerspant), hat man sich bei Hofmann nur für Horizontal-Zentren interessiert. „Die Überlegungen gingen sogar so weit, eine Sondermaschine bauen zu lassen“, erklärt Markus Gräf, Leiter der Hofmann-Prozessentwicklung, „da wir zu diesem Zeitpunkt der Meinung waren, dass es keine Maschine auf dem Markt gibt, die unseren hohen Anforderungen gerecht werden könnte.“
Eine Idee, die dann aber wieder verworfen wurde, weil dadurch die Flexibilität verloren gehen würde. Schon bei der geringsten Änderung der Kammer hätte eine neue Sondermaschine angeschafft werden müssen. „So haben wir uns entgegen unserer Auffassung, dass die Anforderung für den Universalmaschinenbereich eigentlich eine Nummer zu speziell war, entschlossen, genau in diesem Marktsegment weiter zu suchen“, beschreibt Gräf die weitere Vorgehensweise.
Von der Unikat- zur Serienfertigung
Aufgrund der Erfahrungen in der Vergangenheit, als die Baukammern mit einer Werkzeugmaschine mit Flachführungen, die im Führungsbereich bekanntlich eine sehr hohe Stabilität haben, produziert wurden, sollte die neue Maschine wiederum die gleichen baulichen Voraussetzungen erfüllen. „Schnell stellten wir allerdings fest“, so Gräf, „dass es zumindest auf dem europäischen Markt keine Maschine mit Flachführungen mehr gab. Die einzige Möglichkeit wäre die Neuanschaffung der alten Maschine gewesen, also eine Maschine mit einer zwanzig Jahre alten Technik, zu einem utopischen Preis und das mit dem bekannt hohen Nacharbeitsaufwand.“ So war guter Rat teuer, zumal zu diesem Zeitpunkt bei Hofmann die Meinung vorherrschte, dass die Rollenführung der Flachführung unterlegen sei.
GROB-Spindeltechnik ermöglicht hoch genaue Oberflächenqualität
So testete man bei Hofmann, trotz aller anfänglichen Vorurteile, eine GROB 5-Achs-Universalmaschine vom Typ G550 mit der Option für überlanges Werkzeug. Eine Maschine, die mit besseren Rollenführungen arbeitete als Maschinen vergleichbarer Wettbewerber. Da bei GROB die Z-Achse nicht aus der Führung „herausfährt“, spielt es keine Rolle, in welcher Achsposition sich die Spindel gerade befindet. Der Abstand von Spindelnase zu Führung bleibt konstant.
Der Spindelstock wird mit je drei Führungsschuhen pro Führungsschiene geführt, was ein Durchbiegen des Spindelstockes verhindert und konstante Stabilität über den kompletten Verfahrbereich in Richtung der Werkzeugachse gewährleistet. Diese Eigenschaft, gepaart mit der GROB-eigenen Spindeltechnologie, hat zur Folge, dass die hergestellten Oberflächen eine sehr hohe Güte erreichen. Ein für die Bearbeitung bei Hofmann wichtiger Aspekt, da die Stabilität in den Führungen hohe Priorität hat, weil zum einen sehr tief in die Taschen gefahren wird und zum anderen eine hoch genaue Oberflächenqualität erzeugt werden muss.
Leistungsstarkes Maschinenkonzept
Bei den Tests überzeugte die G550 von GROB in erster Linie mit ihrem schlüssigen Maschinenkonzept. Durch die horizontale Spindel und die Möglichkeit, das Werkzeug komplett aus dem Arbeitsraum zurückziehen zu können, gibt es keinerlei Kollisionsbereiche beim Schwenken des Bauteiles. Gerade bei tiefen Bauteilen hat die horizontale Spindel einen bedeutenden Vorteil: Die Späne fallen einfach vom Tisch und die Wärme der Späne hat keinen Einfluss auf die Genauigkeit durch Wärmeeintrag in den Tisch sowie das Messsystem.
Positiv ist auch, dass die Werkzeugstandzeit sich verlängert, da sich keine Späne-Nester im Bauteil bilden, die vom Werkzeug nochmals „gefräst“ werden müssen. Das Ergebnis sind makellose Oberflächen, die keiner manuellen Nacharbeit bedürfen. Weiter tragen ein sehr eigensteifes Maschinenbett und breite, groß dimensionierte Linearführungen zu einem insgesamt hochwertigen und leistungsstarken Maschinenkonzept bei, das auch höchste Anforderungen bei unterschiedlichsten Bearbeitungen erfüllt. In diesem Punkt überzeugte das GROB Maschinenkonzept mit beeindruckenden Ergebnissen.
Doch es blieb zunächst eine Gradwanderung, die G550 und ihre Parameter auf den Bedarf bei Hofmann einzustellen. Bis zu sechs Mann von GROB waren bei Hofmann vor Ort, um die doch sehr speziellen Anforderungen in die Realität umzusetzen. Um noch mehr Stabilität bei der Bearbeitung der Baukammern zu erzielen, wurde die G550 bereits mit einer leistungsstarken Motorspindel HSK-A100 ausgestattet, mit der allerdings die geforderte Oberflächenqualität zunächst nicht erfüllt werden konnte.
Diese Spindel wies leider genau in dem verwendeten Drehzahlbereich eine markante Eigenfrequenz auf, die keine zufriedenstellenden Ergebnisse brachte. Erst nachdem eine neue GROB Motorspindel mit HSK-A100 und 340 Nm Drehmoment installiert wurde, konnten die Oberflächen in der erhofften Qualität hergestellt werden.
„Wir waren sehr froh über diese Neuentwicklung bei GROB“, erinnert sich Markus Gräf noch heute gern, „da damit unsere Sorge unberechtigt war, dass die zunächst nicht zufriedenstellende Oberflächenqualität an den Lagern oder Führungen gelegen haben könnte, die wir schon durch Flachführungen ersetzen wollten.“
Als schließlich die Genauigkeit bei einer bestimmten Größe dargestellt werden konnte, forderte der Markt noch größere Kammern mit der Folge, dass noch größer und tiefer gefräst werden musste. Daher bestellte die Firma Hofmann, zwei Jahre nach der Erstinstallation einer G550 und der Lieferung von zwei weiteren G550, mit der G750 eine entsprechend größere Maschine mit noch längeren Werkzeugen.
Jetzt konnten natürlich die Erfahrungen der G550 gut umgesetzt und die noch größeren Kammern mit neu angepassten Parametern produziert werden. Ein echte 3D-Fertigung, keine 2- oder 2,5-D-Körper, mit hohen Regelgeschwindigkeiten und schnell umschaltbaren Achsen, alles das was die GROB-Maschinen in ihrer Umsetzung bieten konnten. Heute sind bei Hofmann drei G550 und drei G750 für die Produktion der Baukammern im Einsatz.
Mehr Informationen zur GROB-WERKE GmbH & Co. KG:
![]() |
GROB-WERKE GmbH & Co. KG |
![]() |
Industriestrasse 4 |
![]() |
87719 Mindelheim |
![]() |
Telefon: + 49 8261 996 0 |
![]() |
E-Mail: info@grobgroup.com |
![]() |
www.grobgroup.com |
War dieser Artikel für Sie hilfreich?
![]() |
![]() |
![]() |
![]() |
![]() |
Bitte bewerten Sie diese Seite durch Klick auf die Symbole.
Zugriffe heute: 2 - gesamt: 4623.